Die Vakuumbeschichtung ist ein hochentwickeltes Verfahren zur Abscheidung dünner Materialschichten auf ein Substrat in einer kontrollierten Vakuumumgebung.Diese Technik ist in Branchen wie der Halbleiterindustrie, der Optik und der Luft- und Raumfahrt zur Herstellung präziser, hochwertiger Beschichtungen weit verbreitet.Das Verfahren umfasst die Erzeugung eines Vakuums zur Eliminierung störender Gase, die Vorbereitung des Substrats, das Aufdampfen oder Sputtern des Beschichtungsmaterials, das Aufbringen auf das Substrat und schließlich das Abkühlen und Entlüften der Kammer.Das Ergebnis ist eine gleichmäßige, hochreine Beschichtung, die je nach Anwendung von atomarer Dicke bis zu mehreren Millimetern reichen kann.
Die wichtigsten Punkte erklärt:
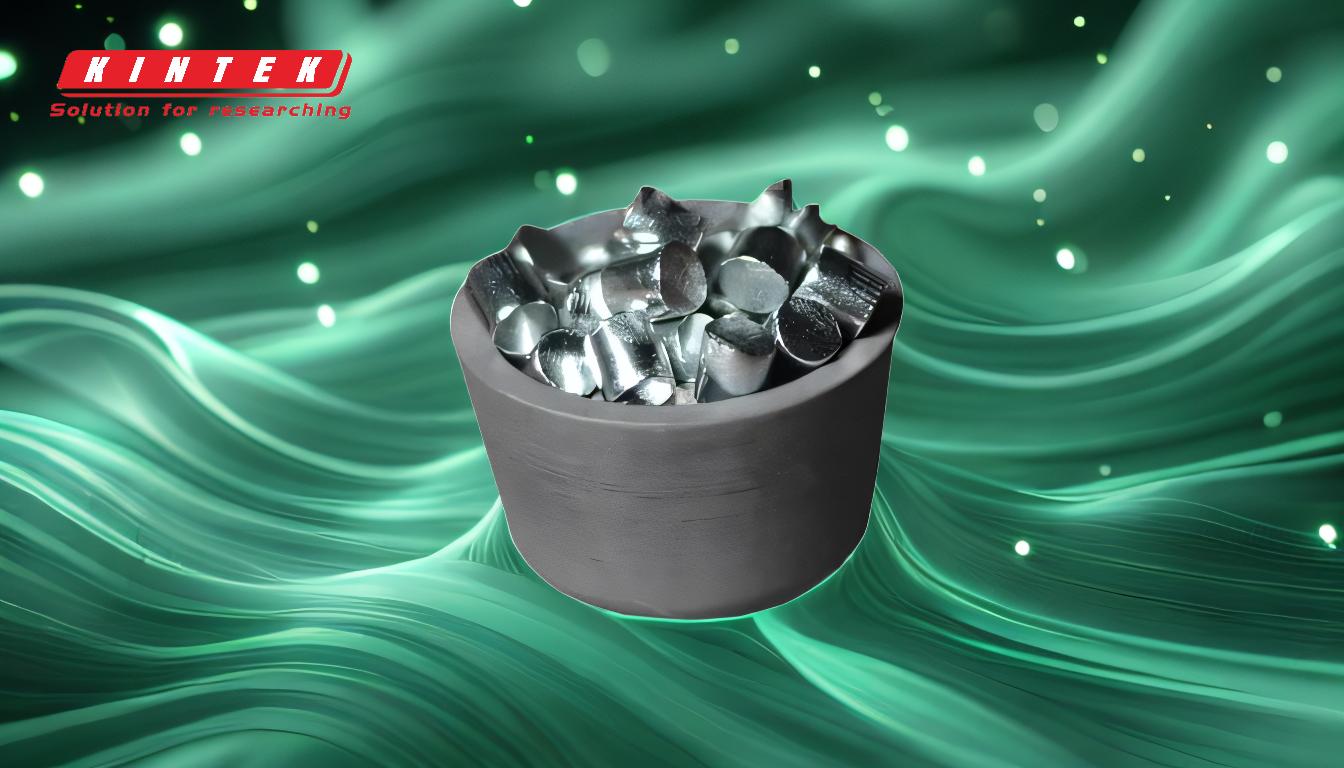
-
Schaffung einer Vakuumumgebung:
- Der erste Schritt bei der Vakuumbeschichtung ist die Erzeugung eines Vakuums in der Beschichtungskammer.Dazu müssen Luft und andere Gase entfernt werden, um Verunreinigungen und Störungen während des Beschichtungsprozesses zu minimieren.Eine Vakuumumgebung sorgt dafür, dass das Beschichtungsmaterial ungehindert auf das Substrat gelangen kann, was zu einer saubereren und gleichmäßigeren Beschichtung führt.
- Das erforderliche Vakuumniveau hängt von dem jeweiligen Verfahren und den verwendeten Materialien ab.Hohe Vakuumniveaus (10^-6 bis 10^-9 Torr) sind typisch für Verfahren wie die physikalische Gasphasenabscheidung (PVD), um minimale Störungen durch Gasmoleküle zu gewährleisten.
-
Vorbereitung des Substrats:
- Vor der Abscheidung muss das Substrat (die zu beschichtende Oberfläche) gründlich gereinigt und vorbereitet werden.Dazu gehören häufig die Reinigung mit Lösungsmitteln, das Plasmaätzen oder andere Oberflächenbehandlungen, um Verunreinigungen zu entfernen und die Haftung zu verbessern.
- Die ordnungsgemäße Vorbereitung des Substrats ist entscheidend dafür, dass die Beschichtung gut haftet und die gewünschten Eigenschaften wie Gleichmäßigkeit und Haltbarkeit erreicht.
-
Aufdampfen oder Sputtern von Beschichtungsmaterial:
-
Das Beschichtungsmaterial wird in die Vakuumkammer eingeführt und in einen Dampf- oder Plasmazustand versetzt.Dies kann erreicht werden durch:
- Verdampfung:Das Material wird erhitzt, bis es verdampft, in der Regel mit Hilfe von Widerstandsheizung, Elektronenstrahlen oder Lasern.
- Sputtern:Hochenergetische Ionen beschießen ein Zielmaterial und schlagen Atome aus dem Ziel heraus, die sich dann auf dem Substrat ablagern.
- Diese Verfahren ermöglichen eine genaue Kontrolle der Abscheidungsrate und der Dicke der Beschichtung.
-
Das Beschichtungsmaterial wird in die Vakuumkammer eingeführt und in einen Dampf- oder Plasmazustand versetzt.Dies kann erreicht werden durch:
-
Abscheidung von Material auf dem Substrat:
- Das verdampfte oder gesputterte Material wandert durch das Vakuum und lagert sich auf dem Substrat ab.Das Fehlen von Gasmolekülen im Vakuum sorgt dafür, dass das Material einen gleichmäßigen, hochreinen Film bildet.
- Der Abscheidungsprozess kann gesteuert werden, um bestimmte Filmeigenschaften wie Dicke, Zusammensetzung und Mikrostruktur zu erreichen.Dies ist besonders wichtig für Anwendungen, die Präzision im Nanometerbereich erfordern.
-
Kühlung und Belüftung der Kammer:
- Nach Abschluss der Abscheidung wird die Kammer allmählich auf Raumtemperatur abgekühlt, um eine thermische Belastung des beschichteten Substrats zu vermeiden.Anschließend wird die Kammer auf Atmosphärendruck entlüftet, so dass das beschichtete Substrat entfernt werden kann.
- Eine ordnungsgemäße Kühlung und Entlüftung sind wichtig, um die Integrität der Beschichtung zu erhalten und sicherzustellen, dass das Substrat nicht beschädigt wird.
-
Arten von Vakuum-Beschichtungsprozessen:
- Physikalische Gasphasenabscheidung (PVD):Physikalische Verfahren wie Verdampfen oder Sputtern zur Abscheidung dünner Schichten.PVD wird häufig für die Herstellung harter, verschleißfester Beschichtungen verwendet.
- Chemische Niederdruck-Gasphasenabscheidung (LPCVD):Abscheidung dünner Schichten durch chemische Reaktionen bei niedrigem Druck.Diese Methode ist in der Halbleiterherstellung üblich.
- Niederdruck-Plasmaspritzen (LPPS):Kombiniert Plasmaspritzen mit einer Vakuumumgebung zur Abscheidung hochwertiger Beschichtungen, die häufig in der Luft- und Raumfahrt eingesetzt werden.
-
Anwendungen der Vakuumbeschichtung:
-
Die Vakuumbeschichtung wird in einer Vielzahl von Industriezweigen eingesetzt, darunter:
- Halbleiter:Für die Herstellung dünner Schichten in integrierten Schaltkreisen und in der Mikroelektronik.
- Optik:Zur Herstellung von Antireflexions-, Reflexions- oder Schutzschichten auf Linsen und Spiegeln.
- Luft- und Raumfahrt:Zum Aufbringen von Wärmedämmschichten und Korrosionsschutzschichten auf Bauteile.
- Dekorative Beschichtungen:Für dauerhafte, ästhetisch ansprechende Beschichtungen von Konsumgütern.
-
Die Vakuumbeschichtung wird in einer Vielzahl von Industriezweigen eingesetzt, darunter:
-
Vorteile der Vakuumbeschichtung:
- Hohe Präzision:Ermöglicht die Abscheidung ultradünner Schichten mit einer Genauigkeit im Nanometerbereich.
- Saubere Umwelt:Das Vakuum minimiert die Verunreinigung, was zu hochreinen Beschichtungen führt.
- Vielseitigkeit:Kann eine breite Palette von Materialien abscheiden, darunter Metalle, Keramik und Polymere.
- Verbesserte Eigenschaften:Beschichtungen können Härte, Verschleißfestigkeit, Korrosionsbeständigkeit und andere Materialeigenschaften verbessern.
Wenn Sie diese Schritte befolgen und die wichtigsten Prozesse verstehen, ermöglicht die Vakuumbeschichtung die Herstellung von fortschrittlichen Materialien und Beschichtungen mit außergewöhnlicher Präzision und Leistung.
Zusammenfassende Tabelle:
Wichtigster Schritt | Beschreibung |
---|---|
Schaffung einer Vakuumumgebung | Entfernen Sie Luft und Gase, um Verunreinigungen zu minimieren und eine gleichmäßige Abscheidung zu gewährleisten. |
Vorbereitung des Substrats | Reinigen und behandeln Sie das Substrat für optimale Haftung und Beschichtungsqualität. |
Verdampfen oder Sputtern | Umwandlung von Beschichtungsmaterial in Dampf oder Plasma durch Hitze (Verdampfung) oder Ionenbeschuss (Sputtern). |
Abscheidung auf dem Substrat | Gleichmäßiges Aufbringen des Materials auf das Substrat in einer Vakuumumgebung. |
Kühlen und Entlüften | Kühlen Sie die Kammer allmählich ab und entlüften Sie sie, um Beschichtungsschäden zu vermeiden. |
Arten von Prozessen | Dazu gehören PVD, LPCVD und LPPS, die jeweils für bestimmte Anwendungen geeignet sind. |
Anwendungen | Einsatz in der Halbleiterindustrie, Optik, Luft- und Raumfahrt und in dekorativen Beschichtungen. |
Vorteile | Hohe Präzision, saubere Umgebung, Vielseitigkeit und verbesserte Materialeigenschaften. |
Entdecken Sie, wie die Vakuumbeschichtung Ihre Projekte aufwerten kann. Kontaktieren Sie unsere Experten noch heute !