Einsatzhärten ist ein spezielles Wärmebehandlungsverfahren, mit dem die Härte der Außenfläche eines Metallteils erhöht und gleichzeitig ein weicherer, duktilerer Kern erhalten bleibt. Dieses Verfahren ist besonders nützlich für Komponenten, die eine hohe Verschleißfestigkeit an der Oberfläche erfordern, aber im Kern ihre Zähigkeit und Flexibilität beibehalten müssen, wie z. B. Zahnräder, Wellen und Lager. Der schrittweise Prozess des Einsatzhärtens umfasst mehrere Schritte, von denen jeder entscheidend für die Erzielung der gewünschten Eigenschaften des Metalls ist.
Wichtige Punkte erklärt:
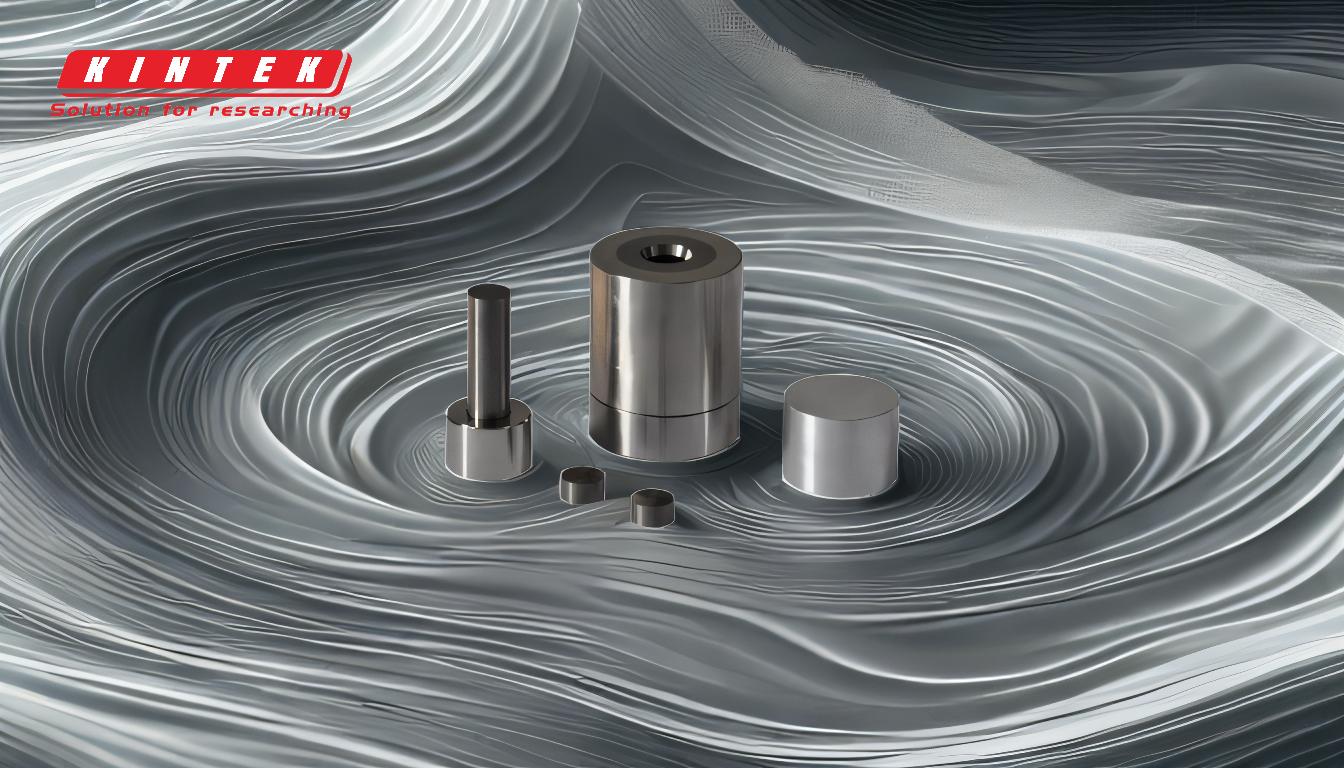
-
Materialauswahl:
- Der erste Schritt beim Einsatzhärten ist die Auswahl des geeigneten Materials. Typischerweise werden kohlenstoffarme Stähle oder Eisenlegierungen gewählt, da diese während des Härteprozesses effektiv Kohlenstoff oder Stickstoff absorbieren können. Diese Materialien ermöglichen einen erheblichen Härteunterschied zwischen der Oberfläche und dem Kern.
-
Reinigen und Vorbereiten der Oberfläche:
- Bevor der eigentliche Härteprozess beginnt, muss das Metallteil gründlich gereinigt werden, um Schmutz, Öl oder Oxide zu entfernen. Dadurch wird sichergestellt, dass die Härter (Kohlenstoff oder Stickstoff) gleichmäßig in die Oberfläche eindringen können. Die Oberflächenvorbereitung kann eine mechanische Reinigung (z. B. Sandstrahlen) oder eine chemische Reinigung (z. B. mit Lösungsmitteln oder Säuren) umfassen.
-
Erhitzen des Metalls:
- Das Metall wird auf eine bestimmte Temperatur erhitzt, typischerweise zwischen 850 °C und 950 °C (1562 °F und 1742 °F), abhängig vom Material und der gewünschten Härte. Dieser Schritt ist entscheidend, da er es dem Metall ermöglicht, einen Zustand zu erreichen, in dem es Kohlenstoff oder Stickstoff effektiv absorbieren kann. Der Erhitzungsprozess wird normalerweise in einer kontrollierten Umgebung, beispielsweise einem Ofen, durchgeführt, um eine gleichmäßige Temperaturverteilung sicherzustellen.
-
Einführung von Härtemitteln (Aufkohlen oder Nitrieren):
-
Sobald das Metall die gewünschte Temperatur erreicht hat, wird es einer kohlenstoffreichen oder stickstoffreichen Umgebung ausgesetzt. Dieser Schritt wird als Aufkohlen bzw. Nitrieren bezeichnet.
- Aufkohlen: Bei diesem Verfahren wird das Metall in eine kohlenstoffreiche Atmosphäre gebracht, beispielsweise ein Gas oder eine Flüssigkeit, die Kohlenstoffverbindungen enthält. Der Kohlenstoff diffundiert in die Oberfläche des Metalls, wodurch dessen Kohlenstoffgehalt und damit seine Härte erhöht werden.
- Nitrieren: Bei diesem Verfahren wird das Metall einer stickstoffreichen Umgebung ausgesetzt, häufig in Form von Ammoniakgas. Stickstoffatome diffundieren in die Oberfläche und bilden harte Nitride, die die Oberflächenhärte erhöhen.
-
Sobald das Metall die gewünschte Temperatur erreicht hat, wird es einer kohlenstoffreichen oder stickstoffreichen Umgebung ausgesetzt. Dieser Schritt wird als Aufkohlen bzw. Nitrieren bezeichnet.
-
Einweichen:
- Nach dem Einbringen von Härtemitteln wird das Metall für einen bestimmten Zeitraum, die sogenannte Einweichzeit, auf der hohen Temperatur gehalten. Dadurch kann der Kohlenstoff oder Stickstoff tiefer in das Metall diffundieren und eine gehärtete Schicht mit der gewünschten Dicke erzeugen. Die Einweichzeit kann je nach Material und erforderlicher Härtetiefe zwischen einigen Minuten und mehreren Stunden variieren.
-
Abschrecken:
- Sobald die Einweichphase abgeschlossen ist, wird das Metall schnell abgekühlt oder abgeschreckt, um die gehärtete Oberfläche zu fixieren. Das Abschrecken erfolgt typischerweise durch Eintauchen des Metalls in ein Kühlmedium wie Wasser, Öl oder Luft. Durch die schnelle Abkühlung härtet die Oberfläche deutlich aus, während der Kern relativ weich und duktil bleibt.
-
Temperieren:
- Nach dem Abschrecken kann das Metall einem Anlassen unterzogen werden, um die Sprödigkeit zu verringern und die Zähigkeit zu verbessern. Beim Anlassen wird das Metall erneut auf eine niedrigere Temperatur erhitzt (normalerweise zwischen 150 °C und 650 °C oder 302 °F und 1202 °F) und dann langsam abkühlen gelassen. Dieser Schritt trägt dazu bei, innere Spannungen abzubauen und ein Gleichgewicht zwischen Härte und Zähigkeit zu erreichen.
-
Endgültige Fertigstellung:
- Der letzte Schritt im Einsatzhärtungsprozess ist die Endbearbeitung des Metallteils. Dies kann Schleifen, Polieren oder Beschichten umfassen, um die gewünschte Oberflächenbeschaffenheit und Maßgenauigkeit zu erreichen. Durch die Endbearbeitung wird außerdem sichergestellt, dass das Teil die erforderlichen Spezifikationen für die beabsichtigte Anwendung erfüllt.
Durch die Befolgung dieser Schritte kann das Einsatzhärten die Haltbarkeit und Verschleißfestigkeit von Metallkomponenten erheblich verbessern und gleichzeitig ihre strukturelle Integrität bewahren. Dies macht es zu einem unverzichtbaren Prozess in Branchen, in denen Hochleistungsmaterialien benötigt werden.
Übersichtstabelle:
Schritt | Beschreibung |
---|---|
1. Materialauswahl | Wählen Sie kohlenstoffarme Stähle oder Eisenlegierungen für eine effektive Kohlenstoff-/Stickstoffabsorption. |
2. Reinigen und Vorbereiten | Entfernen Sie Schmutz, Öl oder Oxide, um ein gleichmäßiges Eindringen der Härter zu gewährleisten. |
3. Erhitzen des Metalls | Für eine optimale Kohlenstoff-/Stickstoffabsorption auf 850 °C–950 °C (1562 °F–1742 °F) erhitzen. |
4. Härter | Zur Erhöhung der Oberflächenhärte wird Kohlenstoff (Aufkohlen) oder Stickstoff (Nitririeren) eingebracht. |
5. Einweichen | Bei hoher Temperatur halten, damit die Härter in das Metall diffundieren können. |
6. Abschrecken | Schnell abkühlen, um die gehärtete Oberfläche zu fixieren und gleichzeitig den Kern duktil zu halten. |
7. Temperieren | Erneut erhitzen, um die Sprödigkeit zu verringern und die Zähigkeit zu verbessern. |
8. Endbearbeitung | Schleifen, polieren oder beschichten, um die gewünschte Oberflächenbeschaffenheit und Genauigkeit zu erreichen. |
Benötigen Sie Hilfe beim Einsatzhärten Ihrer Metallkomponenten? Kontaktieren Sie noch heute unsere Experten für maßgeschneiderte Lösungen!