Die Substrattemperatur beim Sputtern spielt eine entscheidende Rolle bei der Bestimmung der Qualität und der Eigenschaften der abgeschiedenen Dünnschichten.Sie beeinflusst Faktoren wie Schichtdichte, Haftung, Kristallinität, Spannung und Defektdichte.Höhere Substrattemperaturen führen im Allgemeinen zu dichteren Schichten mit verbesserten Oberflächenreaktionen und geringerer Defektdichte, während für bestimmte Materialien oder Anwendungen niedrigere Temperaturen erforderlich sein können, um Spannungen und Haftung zu kontrollieren.Die Temperatur kann optimiert werden, um die gewünschten Schichteigenschaften zu erreichen, und in einigen Fällen können Kühlschritte erforderlich sein, um thermische Effekte zu steuern.Das Verständnis des Zusammenhangs zwischen Substrattemperatur und Schichteigenschaften ist für die Optimierung von Sputterprozessen unerlässlich.
Die wichtigsten Punkte werden erklärt:
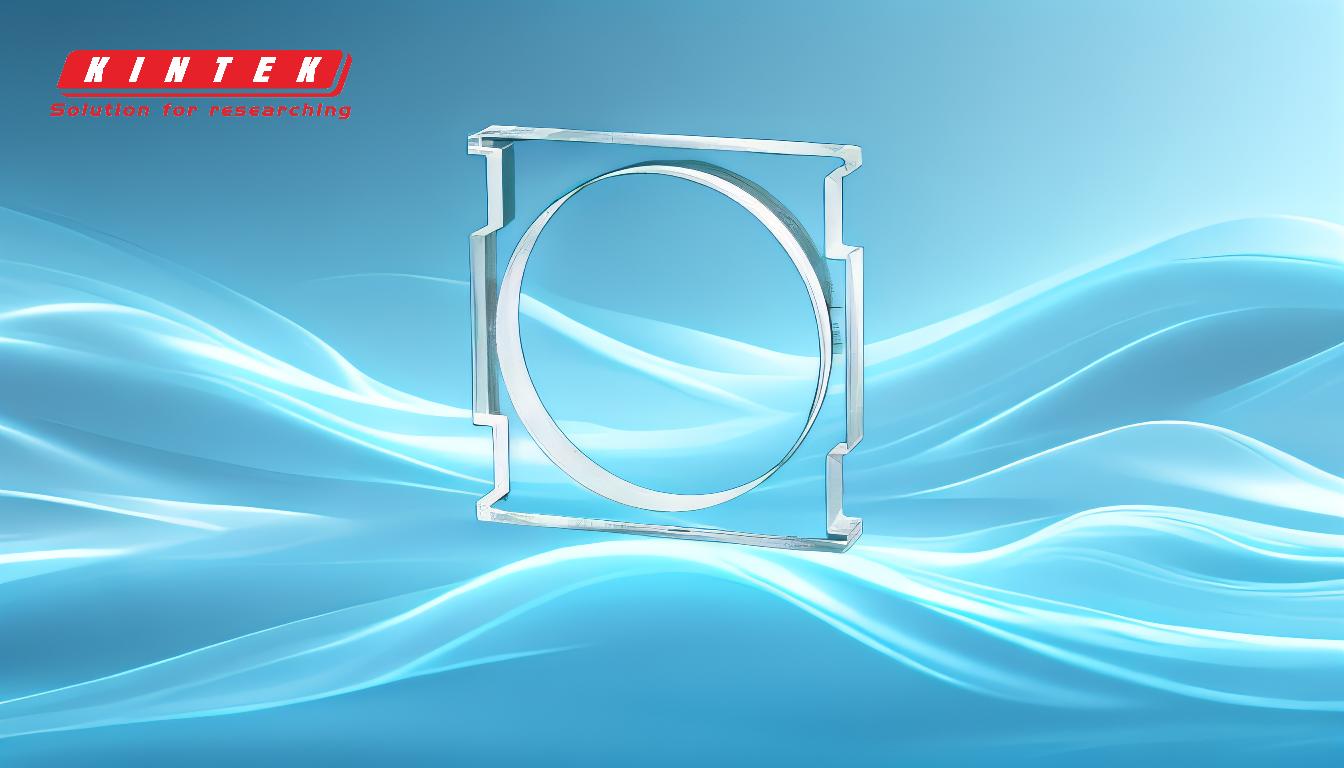
-
Auswirkungen auf die Filmqualität:
- Die Temperatur des Substrats hat einen erheblichen Einfluss auf die Qualität der beim Sputtern abgeschiedenen dünnen Schichten.
- Höhere Temperaturen verbessern die Oberflächenreaktionen, was zu dichteren Schichten mit besserer Zusammensetzung führt.
- Eine höhere Temperatur trägt dazu bei, die baumelnden Bindungen auf der Filmoberfläche zu kompensieren, wodurch die Defektdichte verringert und die lokale Zustandsdichte, die Elektronenbeweglichkeit und die optischen Eigenschaften verbessert werden.
-
Einfluss auf die Abscheiderate:
- Die Substrattemperatur hat nur minimale Auswirkungen auf die Abscheiderate.
- Die Temperatur wirkt sich in erster Linie auf die Qualität und die Eigenschaften der Schicht aus und weniger auf die Geschwindigkeit der Abscheidung.
-
Adhäsion, Kristallinität und Spannung:
- Die Temperatur beeinflusst die Haftung der Folie auf dem Substrat, wobei optimale Temperaturen die Haftung verbessern.
- Die Kristallinität der Folie kann durch Anpassung der Substrattemperatur gesteuert werden, da höhere Temperaturen bessere kristalline Strukturen fördern.
-
Die Spannung im Film wird durch die Temperatur beeinflusst, wie in der Formel beschrieben:
[
\sigma = E \times \alpha \times (T - T_0)
-
] wobei (\sigma) die Spannung, (E) der Elastizitätsmodul, (\alpha) der Wärmeausdehnungskoeffizient, (T) die Substrattemperatur und (T_0) die Referenztemperatur ist.
- Optimierung der Temperatur
- :
- Die Temperatur des Substrats kann optimiert werden, um bestimmte Filmeigenschaften zu erreichen, wie z. B. die gewünschte Dichte, Haftung und Spannungswerte.
-
In einigen Fällen ist es notwendig, das Substrat auf eine bestimmte Temperatur zu erhitzen, um die Qualität der Folie zu verbessern. Es können auch Kühlschritte erforderlich sein, um thermische Effekte zu steuern und Schäden an empfindlichen Materialien zu vermeiden.
- Materialspezifische Überlegungen
- :
-
Verschiedene Materialien können unterschiedliche Substrattemperaturen erfordern, um optimale Filmeigenschaften zu erzielen. Materialien mit einem hohen Wärmeausdehnungskoeffizienten erfordern beispielsweise eine sorgfältige Temperaturkontrolle, um Spannungen zu minimieren und Delaminationen zu vermeiden.
- Praktische Auswirkungen auf Geräte und Verbrauchsmaterialien
- :
- Für die Käufer von Anlagen ist das Verständnis der Beziehung zwischen Substrattemperatur und Schichteigenschaften entscheidend für die Auswahl des richtigen Sputtersystems.
Für fortgeschrittene Anwendungen können Systeme mit präziser Temperaturregelung und Kühlung erforderlich sein.
Verbrauchsmaterialien wie Substrate und Targetmaterialien sollten unter Berücksichtigung ihrer thermischen Eigenschaften und ihrer Kompatibilität mit dem gewünschten Temperaturbereich ausgewählt werden.
Durch sorgfältige Kontrolle und Optimierung der Substrattemperatur können Sputterprozesse so angepasst werden, dass sie hochwertige Dünnschichten mit den gewünschten Eigenschaften für verschiedene Anwendungen erzeugen. | Zusammenfassende Tabelle: |
---|---|
Faktor | Einfluss der Substrattemperatur |
Dichte des Films | Höhere Temperaturen führen zu dichteren Schichten mit verbesserten Oberflächenreaktionen und geringerer Defektdichte. |
Haftung | Optimale Temperaturen verbessern die Haftung zwischen Folie und Substrat. |
Kristallinität | Höhere Temperaturen fördern bessere kristalline Strukturen im Film. |
Spannung | Die Spannung wird durch die Temperatur beeinflusst, wie in der Formel für die thermische Ausdehnung beschrieben. |
Abscheidungsgeschwindigkeit | Minimale Auswirkung; die Temperatur beeinflusst in erster Linie die Filmqualität, nicht die Abscheidegeschwindigkeit. |
Materialkompatibilität Verschiedene Materialien erfordern bestimmte Temperaturen für optimale Filmeigenschaften. Optimieren Sie Ihren Sputterprozess mit präziser Temperatursteuerung.