Die thermische Verdampfung ist ein Verfahren, bei dem ein festes Material in einer Hochvakuumkammer erhitzt wird, um einen Dampfdruck zu erzeugen, der zur Bildung eines dünnen Films auf einem Substrat führt. Die für diesen Prozess erforderliche Temperatur ist je nach dem zu verdampfenden Material unterschiedlich, da jedes Material eine eigene Dampfdruckkurve aufweist. Im Allgemeinen muss die Temperatur hoch genug sein, um einen ausreichenden Dampfdruck für die Abscheidung zu erzeugen, aber auch die thermische Stabilität und die Eigenschaften sowohl des Ausgangsmaterials als auch des Substrats berücksichtigen. Die Prozesstemperatur ist ein entscheidender Parameter, der die Abscheiderate, die Schichtqualität und die endgültigen Eigenschaften der abgeschiedenen Schicht beeinflusst.
Die wichtigsten Punkte werden erklärt:
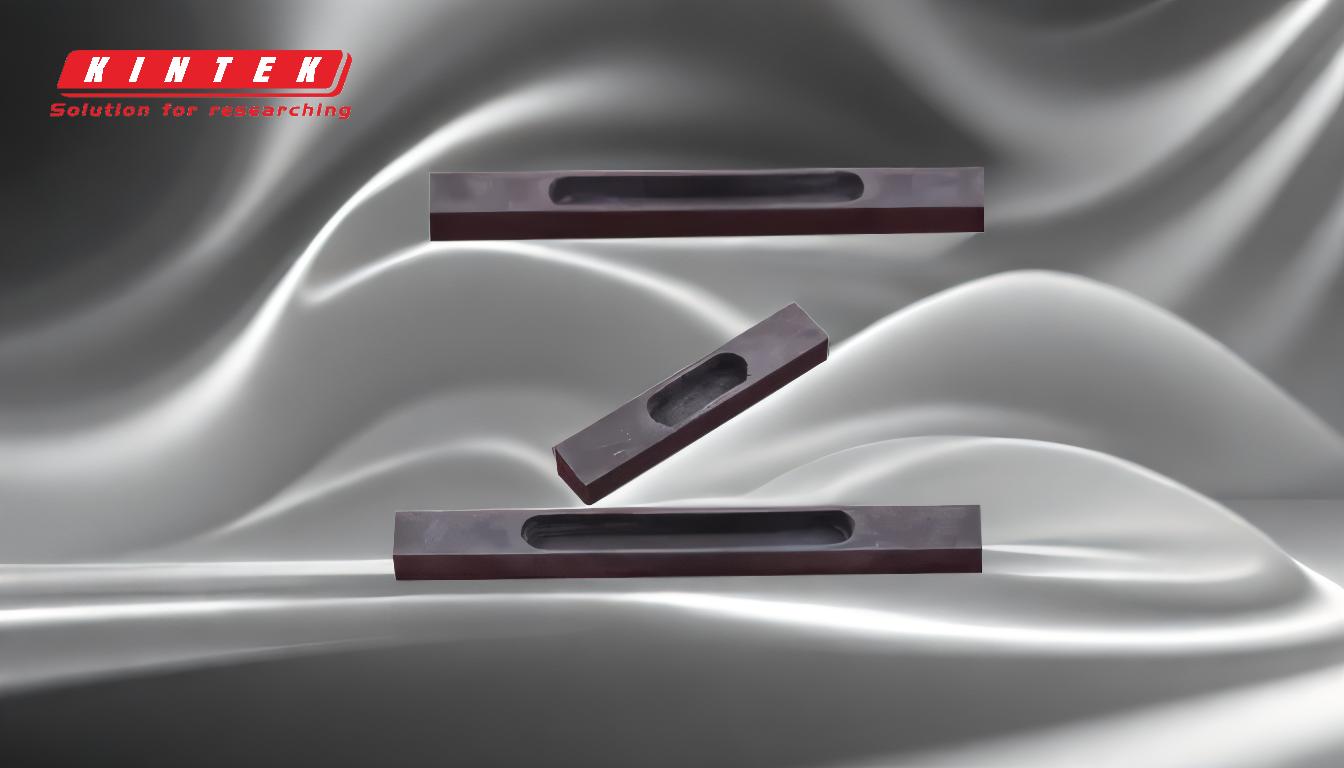
-
Beziehung zwischen Temperatur und Dampfdruck:
- Die Temperatur der thermischen Verdampfungsbeschichtung steht in direktem Zusammenhang mit dem Dampfdruck des zu verdampfenden Materials. Höhere Temperaturen erhöhen den Dampfdruck, was zu einer effizienteren Verdampfung und Abscheidung führt.
- Jedes Material hat einen bestimmten Temperaturbereich, bei dem es von der festen in die dampfförmige Phase übergeht, die so genannte Verdampfungstemperatur. Diese Temperatur wird durch die Dampfdruckkurve des Materials bestimmt.
-
Materialspezifische Verdampfungstemperaturen:
- Verschiedene Materialien erfordern unterschiedliche Verdampfungstemperaturen. Beispielsweise verdampfen Metalle wie Aluminium bei etwa 1200 °C, während organische Stoffe bei viel niedrigeren Temperaturen, oft unter 300 °C, verdampfen können.
- Die Wahl des Materials für die thermische Aufdampfung hängt von seinen Reaktionseigenschaften und seiner thermischen Stabilität ab. Materialien mit hohem Schmelzpunkt erfordern höhere Verdampfungstemperaturen.
-
Einfluss der Temperatur auf Abscheiderate und Filmqualität:
- Höhere Temperaturen führen im Allgemeinen zu höheren Abscheideraten aufgrund des erhöhten Dampfdrucks. Übermäßig hohe Temperaturen können jedoch zu Problemen wie Materialzersetzung oder unerwünschten Reaktionen führen.
- Die Temperatur muss sorgfältig kontrolliert werden, um eine gleichmäßige Schichtdicke, Haftfestigkeit und die gewünschten optischen oder elektrischen Eigenschaften zu gewährleisten.
-
Vakuumumgebung und Temperaturkontrolle:
- Die thermische Verdampfung erfolgt in einer Hochvakuumkammer, um Verunreinigungen zu minimieren und einen langen mittleren freien Weg für die verdampften Materialmoleküle zu gewährleisten.
- Die Vakuumumgebung ermöglicht relativ niedrige Dampfdrücke, so dass auch bei moderaten Temperaturen eine ausreichende Verdampfung erreicht werden kann.
-
Überlegungen zum Substrat:
- Bei der Wahl der Verdampfungstemperatur müssen die thermische Stabilität und die Oberflächeneigenschaften des Substrats berücksichtigt werden. Hohe Temperaturen können empfindliche Substrate beschädigen oder ihre Eigenschaften verändern.
- Auch die Substratrotation und die Oberflächenrauhigkeit spielen eine Rolle bei der Gewährleistung einer gleichmäßigen Abscheidung und Schichtqualität.
-
Praktische Temperaturbereiche:
- Bei den meisten Metallen liegen die Verdampfungstemperaturen je nach Material zwischen 1000°C und 2000°C.
- Organische Materialien und Polymere benötigen in der Regel viel niedrigere Temperaturen, oft unter 500 °C, um eine Zersetzung zu vermeiden.
-
Mechanismen zur Temperaturkontrolle:
- Das Verdampferschiffchen oder der Glühfaden wird mit elektrischem Strom beheizt, und die Temperatur wird durch die Einstellung der Stromversorgung geregelt.
- Fortgeschrittene Systeme können Rückkopplungsmechanismen enthalten, um eine präzise Temperaturkontrolle zu gewährleisten, die konstante Abscheidungsraten und Schichteigenschaften sicherstellt.
Zusammenfassend lässt sich sagen, dass die Temperatur beim thermischen Aufdampfen ein kritischer Parameter ist, der je nach dem zu verdampfenden Material und den gewünschten Schichteigenschaften variiert. Sie muss sorgfältig gesteuert werden, um ein Gleichgewicht zwischen Abscheidungsrate, Schichtqualität und Substratintegrität herzustellen. Das Verständnis der Beziehung zwischen Temperatur, Dampfdruck und Materialeigenschaften ist für die Optimierung des thermischen Verdampfungsprozesses unerlässlich.
Zusammenfassende Tabelle:
Schlüsselfaktor | Beschreibung |
---|---|
Temperatur und Dampfdruck | Höhere Temperaturen erhöhen den Dampfdruck und verbessern die Verdampfungseffizienz. |
Materialspezifische Temperaturen | Metalle (z. B. Aluminium) benötigen ~1200°C; organische Stoffe benötigen <300°C. |
Abscheiderate & Filmqualität | Die kontrollierte Temperatur gewährleistet eine gleichmäßige Dicke und die gewünschten Eigenschaften. |
Vakuum Umgebung | Das Hochvakuum minimiert Verunreinigungen und ermöglicht eine effektive Verdampfung. |
Überlegungen zum Substrat | Thermische Stabilität und Oberflächeneigenschaften müssen mit der Verdampfungstemperatur übereinstimmen. |
Praktische Temperaturbereiche | Metalle: 1000°C-2000°C; organische Stoffe: <500°C. |
Mechanismen zur Temperaturkontrolle | Elektrischer Strom beheizt das Verdampferschiffchen, mit Rückkopplung für Präzision. |
Benötigen Sie Hilfe bei der Optimierung Ihres Verfahrens zur thermischen Verdampfung? Kontaktieren Sie unsere Experten noch heute !