Der Temperaturbereich für die Kalzinierung liegt normalerweise zwischen 800°C und 1300°C abhängig von der jeweiligen Anwendung und den zu verarbeitenden Materialien.Das Kalzinieren ist ein thermischer Behandlungsprozess, der in speziellen Anlagen wie Kalzinierern oder Öfen durchgeführt wird. Dabei werden die Materialien unter kontrollierten Bedingungen erhitzt, um flüchtige Bestandteile wie Kohlendioxid auszutreiben und chemische oder physikalische Veränderungen zu bewirken.Die genaue Temperatur innerhalb dieses Bereichs hängt von Faktoren wie der Zusammensetzung des Materials, dem gewünschten Ergebnis und der Art der verwendeten Ausrüstung ab.
Die wichtigsten Punkte erklärt:
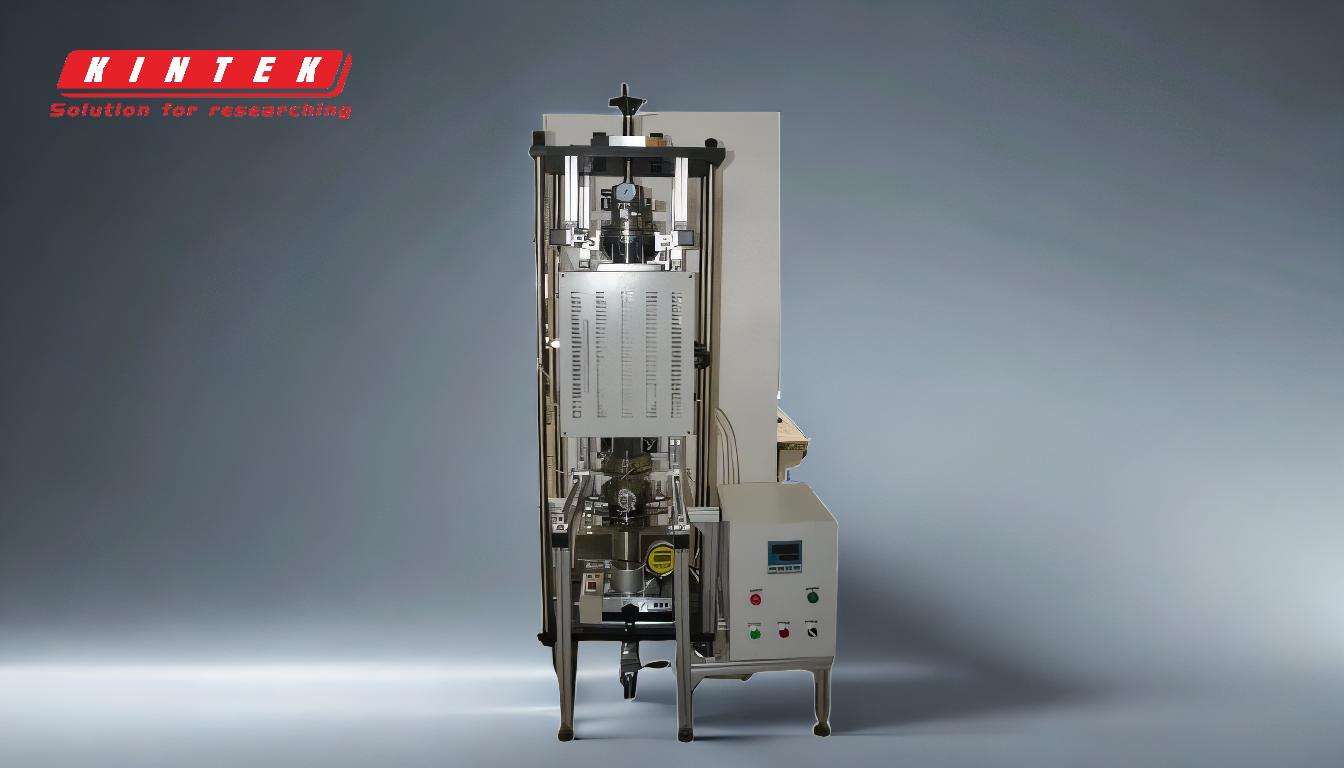
-
Temperaturbereich für die Kalzinierung:
- Der allgemeine Temperaturbereich für die Kalzinierung beträgt 800°C bis 1300°C .Dieser Bereich eignet sich für die meisten Kalzinierungsverfahren, bei denen es darum geht, Materialien thermisch zu zersetzen oder flüchtige Bestandteile zu entfernen.
-
Die spezifische Temperatur innerhalb dieses Bereichs hängt von dem zu verarbeitenden Material und dem gewünschten Ergebnis ab.Ein Beispiel:
- Niedrigere Temperaturen (etwa 800 °C) können für Materialien verwendet werden, die sich leicht zersetzen.
- Höhere Temperaturen (bis zu 1300 °C) sind für stabilere Verbindungen oder zum Erreichen bestimmter Phasenumwandlungen erforderlich.
-
Für die Kalzinierung verwendete Ausrüstung:
- Die Kalzinierung wird in der Regel in speziellen Reaktoren durchgeführt, die Kalzinatoren zylindrische Konstruktionen, die für hohe Temperaturen und kontrollierte Atmosphären ausgelegt sind.
- In einigen Fällen, Öfen werden für die Kalzinierung verwendet, da sie in der Lage sind, die für den Prozess erforderlichen hohen Temperaturen zu erreichen und zu halten.
-
Prozessbedingungen:
- Die Kalzinierung erfolgt unter kontrollierten Bedingungen um gleichbleibende Ergebnisse zu gewährleisten.Dazu gehören eine präzise Temperaturkontrolle, die Regulierung der Atmosphäre und manchmal auch Druckanpassungen.
- Während der Kalzinierung werden flüchtige Bestandteile wie Kohlendioxid (CO₂) werden als Gase freigesetzt, die kontrolliert werden müssen, um die Effizienz und Sicherheit des Prozesses zu gewährleisten.
-
Faktoren, die die Temperaturauswahl beeinflussen:
- Materialzusammensetzung:Verschiedene Materialien haben unterschiedliche thermische Zersetzungstemperaturen.So zersetzt sich beispielsweise Kalziumkarbonat (CaCO₃) bei etwa 825 °C, während für andere Verbindungen höhere Temperaturen erforderlich sein können.
- Gewünschtes Ergebnis:Die Temperatur wird auf der Grundlage der spezifischen chemischen oder physikalischen Veränderungen gewählt, die erforderlich sind, z. B. Phasenübergänge, Entfernung von Verunreinigungen oder Bildung neuer Verbindungen.
- Fähigkeiten der Ausrüstung:Die Art des verwendeten Kalzinators oder Ofens kann den erreichbaren Temperaturbereich einschränken oder beeinflussen.
-
Anwendungen der Kalzinierung:
-
Die Kalzinierung wird in vielen Industriezweigen eingesetzt, wie z. B.:
- Zementherstellung:Kalkstein wird gebrannt, um Kalk (CaO) zu gewinnen, einen wichtigen Bestandteil von Zement.
- Metallurgie:Erze werden gebrannt, um flüchtige Verunreinigungen zu entfernen oder sie in Oxide umzuwandeln.
- Chemische Herstellung:Durch Kalzinierung werden Materialien wie Tonerde (Al₂O₃) aus Bauxit hergestellt.
- Keramik und feuerfeste Materialien:Rohmaterialien werden kalziniert, um ihre Eigenschaften für Hochtemperaturanwendungen zu verbessern.
-
Die Kalzinierung wird in vielen Industriezweigen eingesetzt, wie z. B.:
-
Die Bedeutung der Temperaturkontrolle:
- Die Aufrechterhaltung der richtigen Temperatur ist entscheidend für das Erreichen der gewünschten Ergebnisse bei der Kalzinierung.Eine Überhitzung kann zu unerwünschten Reaktionen oder zum Materialabbau führen, während eine unzureichende Erhitzung zu einer unvollständigen Zersetzung oder Umwandlung führen kann.
- Moderne Kalzinierungsanlagen umfassen häufig Temperaturüberwachungs- und -steuerungssysteme um Präzision und Konsistenz zu gewährleisten.
-
Sicherheitsaspekte:
- Der Betrieb bei hohen Temperaturen erfordert eine sorgfältige Handhabung, um Schäden an der Ausrüstung zu vermeiden und die Sicherheit des Bedieners zu gewährleisten.
- Die Freisetzung von Gasen wie CO₂ während der Kalzinierung muss kontrolliert werden, um Umwelt- oder Gesundheitsrisiken zu vermeiden.
Durch das Verständnis des Temperaturbereichs und der Faktoren, die die Kalzinierung beeinflussen, können die Käufer von Geräten und Verbrauchsmaterialien fundierte Entscheidungen über die Art des Kalzinierers oder Ofens treffen, der für ihre spezifischen Anwendungen benötigt wird.
Zusammenfassende Tabelle:
Aspekt | Einzelheiten |
---|---|
Temperaturbereich | 800°C bis 1300°C, je nach Material und Anwendung. |
Ausrüstung | Kalzinieranlagen oder Öfen, die für hohe Temperaturen und kontrollierte Bedingungen ausgelegt sind. |
Schlüsselfaktoren | Materialzusammensetzung, gewünschtes Ergebnis und Möglichkeiten der Ausrüstung. |
Anwendungen | Zementherstellung, Metallurgie, chemische Produktion, Keramik, feuerfeste Materialien. |
Sicherheitsaspekte | Beherrschen Sie hohe Temperaturen und Gasemissionen (z. B. CO₂) für Sicherheit und Effizienz. |
Sie benötigen die richtige Kalzinieranlage für Ihre Anwendung? Kontaktieren Sie noch heute unsere Experten für maßgeschneiderte Lösungen!