Das Kalzinieren ist ein thermisches Verfahren zur Behandlung fester chemischer Verbindungen, wie z. B. gemischter Karbonaterze, bei dem das Material auf hohe Temperaturen unterhalb seines Schmelzpunktes erhitzt wird, in der Regel unter Abwesenheit oder begrenzter Zufuhr von Sauerstoff.Dieses Verfahren wird in erster Linie eingesetzt, um Verunreinigungen und flüchtige Stoffe zu entfernen oder eine thermische Zersetzung herbeizuführen, häufig um Metalle aus Erzen zu gewinnen oder bestimmte Materialeigenschaften zu erzielen.Durch die Kalzinierung werden chemisch gebundene Bestandteile wie Wasser oder Kohlendioxid ausgetrieben, was zu einem Phasenübergang oder zur Bildung einer stabileren Verbindung führt.Sie wird in vielen Industriezweigen wie der Metallurgie, der Keramik und der Zementherstellung eingesetzt.
Die wichtigsten Punkte werden erklärt:
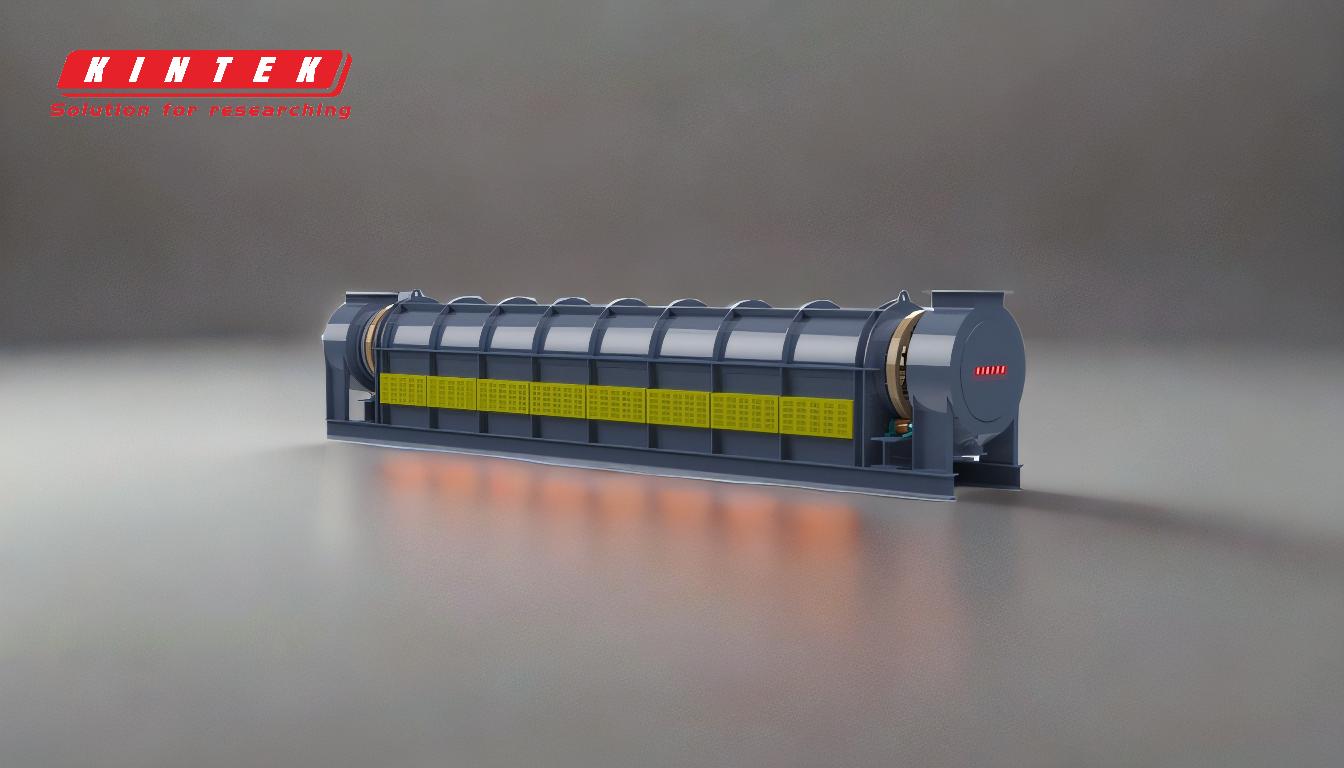
-
Definition der Kalzination:
- Das Kalzinieren ist ein Wärmebehandlungsverfahren, bei dem feste Materialien wie Erze oder chemische Verbindungen auf hohe Temperaturen unterhalb ihres Schmelzpunkts erhitzt werden.
- Dabei wird kein oder nur wenig Sauerstoff zugeführt, um eine Verbrennung oder unerwünschte Oxidation zu verhindern.
-
Zweck der Kalzinierung:
- Entfernung von flüchtigen Stoffen:Durch die Kalzinierung werden flüchtige Bestandteile wie Wasser, Kohlendioxid oder organische Verunreinigungen entfernt, die dann als Gase abgeführt werden.
- Thermische Zersetzung:Sie bewirkt den Zerfall von Verbindungen in einfachere Stoffe, z. B. die Umwandlung von Karbonaten in Oxide.
- Phasenübergang:Das Verfahren kann eine Veränderung der physikalischen oder chemischen Struktur des Materials bewirken, die zu einer stabileren oder gewünschten Phase führt.
- Extraktion von Metallen:In der Metallurgie wird die Kalzinierung zur Gewinnung von Metallen aus Erzen verwendet, indem Metallkarbonate oder -hydroxide in Metalloxide zersetzt werden.
-
Prozess Bedingungen:
- Temperatur:Das Material wird auf hohe Temperaturen erhitzt, in der Regel unter seinen Schmelzpunkt, um ein Schmelzen zu vermeiden und gleichzeitig die gewünschten chemischen Veränderungen zu erzielen.
- Atmosphäre:Die Kalzinierung erfolgt in einer kontrollierten Umgebung, oft mit begrenztem Sauerstoffgehalt, um eine Oxidation oder Verbrennung des Materials zu verhindern.
- Dauer:Die Erhitzungsdauer hängt vom Material und dem gewünschten Ergebnis ab, wobei die vollständige Zersetzung oder die Entfernung flüchtiger Bestandteile gewährleistet sein muss.
-
Anwendungen der Kalzinierung:
- Metallurgie:Zur Gewinnung von Metallen wie Eisen, Zink und Aluminium aus ihren Erzen durch Umwandlung von Metallkarbonaten oder Hydroxiden in Oxide.
- Zementherstellung:Bei der Kalzinierung von Kalkstein (Kalziumkarbonat) entsteht Kalk (Kalziumoxid), ein Hauptbestandteil von Zement.
- Keramik und feuerfeste Materialien:Die Kalzinierung wird zur Herstellung von keramischen Werkstoffen und feuerfesten Produkten verwendet, um Verunreinigungen zu entfernen und die gewünschten Materialeigenschaften zu erzielen.
- Chemische Industrie:Es wird bei der Herstellung verschiedener Chemikalien eingesetzt, z. B. bei der Herstellung von Titandioxid aus Titanerzen.
-
Beispiele für Kalzinierungsreaktionen:
-
Zersetzung von Calciumcarbonat:
[ -
\text{CaCO}_3 \rightarrow \text{CaO}+ \text{CO}_2 \uparrow
]
Diese Reaktion ist für die Zementherstellung von grundlegender Bedeutung.
-
Zersetzung von Calciumcarbonat:
-
Umwandlung von Zinkkarbonat in Zinkoxid:
- [ \text{ZnCO}_3 \rightarrow \text{ZnO}+ \text{CO}_2 \uparrow
- ] Wird bei der Gewinnung von Zink aus seinen Erzen verwendet.
- Vorteile der Kalzinierung:
-
Klärung:Entfernt wirksam Verunreinigungen und flüchtige Stoffe und verbessert die Qualität des Endprodukts.
- Kontrollierte Zersetzung:Ermöglicht eine präzise Kontrolle der thermischen Zersetzung von Verbindungen, was zu konsistenten Ergebnissen führt.
- Energie-Effizienz:Da der Prozess unterhalb des Schmelzpunkts stattfindet, wird im Vergleich zum Schmelzen oder Schmelzen oft weniger Energie benötigt.
- Grenzen der Kalzinierung:
-
Anforderungen bei hohen Temperaturen:Die Kalzinierung erfordert häufig einen erheblichen Energieaufwand, um die erforderlichen Temperaturen zu erreichen.
- Emission von Gasen:Die Freisetzung flüchtiger Stoffe wie Kohlendioxid kann zu Umweltproblemen führen, wenn sie nicht ordnungsgemäß gehandhabt wird.
- Werkstoffspezifisch:Die Wirksamkeit der Kalzinierung hängt von den spezifischen Eigenschaften des zu behandelnden Materials ab, und nicht alle Verbindungen sind für dieses Verfahren geeignet.
Vergleich mit anderen thermischen Prozessen
:
Kalzinierung vs. Röstung | :Bei beiden Verfahren wird zwar erhitzt, aber das Rösten erfolgt in der Regel in Gegenwart von überschüssigem Sauerstoff und dient der Umwandlung von Sulfiden in Oxide, während das Kalzinieren in einer sauerstoffarmen Umgebung erfolgt. |
---|---|
Kalzinierung vs. Sintern | :Beim Sintern werden Materialien erhitzt, um Partikel miteinander zu verbinden, ohne zu schmelzen, was häufig in der Pulvermetallurgie verwendet wird, während sich die Kalzinierung auf die Zersetzung oder Phasenumwandlung konzentriert. |
Wenn man die Theorie der Kalzinierung versteht, kann die Industrie diesen Prozess zur Materialreinigung, Zersetzung und Phasenumwandlung optimieren, was ihn zu einem entscheidenden Schritt in verschiedenen Herstellungs- und Extraktionsprozessen macht. | Zusammenfassende Tabelle: |
Aspekt | Einzelheiten |
Definition | Erhitzen fester Stoffe unter den Schmelzpunkt in sauerstoffarmer Umgebung. |
Zweck | Beseitigung von Verunreinigungen, Einleitung der Zersetzung und Extraktion von Metallen. |
Anwendungen | Metallurgie, Zementherstellung, Keramik und chemische Industrie. |
Vorteile Reinigung, kontrollierte Zersetzung, Energieeffizienz. Beschränkungen