Die Vakuumabscheidung ist eine hochentwickelte Technik zur Erzeugung dünner Schichten oder Beschichtungen auf festen Oberflächen durch Abscheidung von Material Atom für Atom oder Molekül für Molekül in einer Hochvakuumumgebung.Dieses Verfahren ist unverzichtbar für Anwendungen, die eine präzise Kontrolle der Schichtdicke erfordern, die von Nanometern bis zu Millimetern reichen kann, und ist in Branchen wie der Elektronik, Optik und Fertigung weit verbreitet.Techniken wie die physikalische Abscheidung aus der Gasphase (PVD), die chemische Abscheidung aus der Gasphase (CVD), die thermische Verdampfung und das Sputtern werden in der Regel bei der Vakuumabscheidung eingesetzt.Die Methode gewährleistet eine saubere, kontrollierte Umgebung, die Verunreinigungen minimiert und die Herstellung hochwertiger Beschichtungen mit verbesserten Eigenschaften wie Leitfähigkeit, Korrosionsbeständigkeit und optischer Leistung ermöglicht.
Die wichtigsten Punkte werden erklärt:
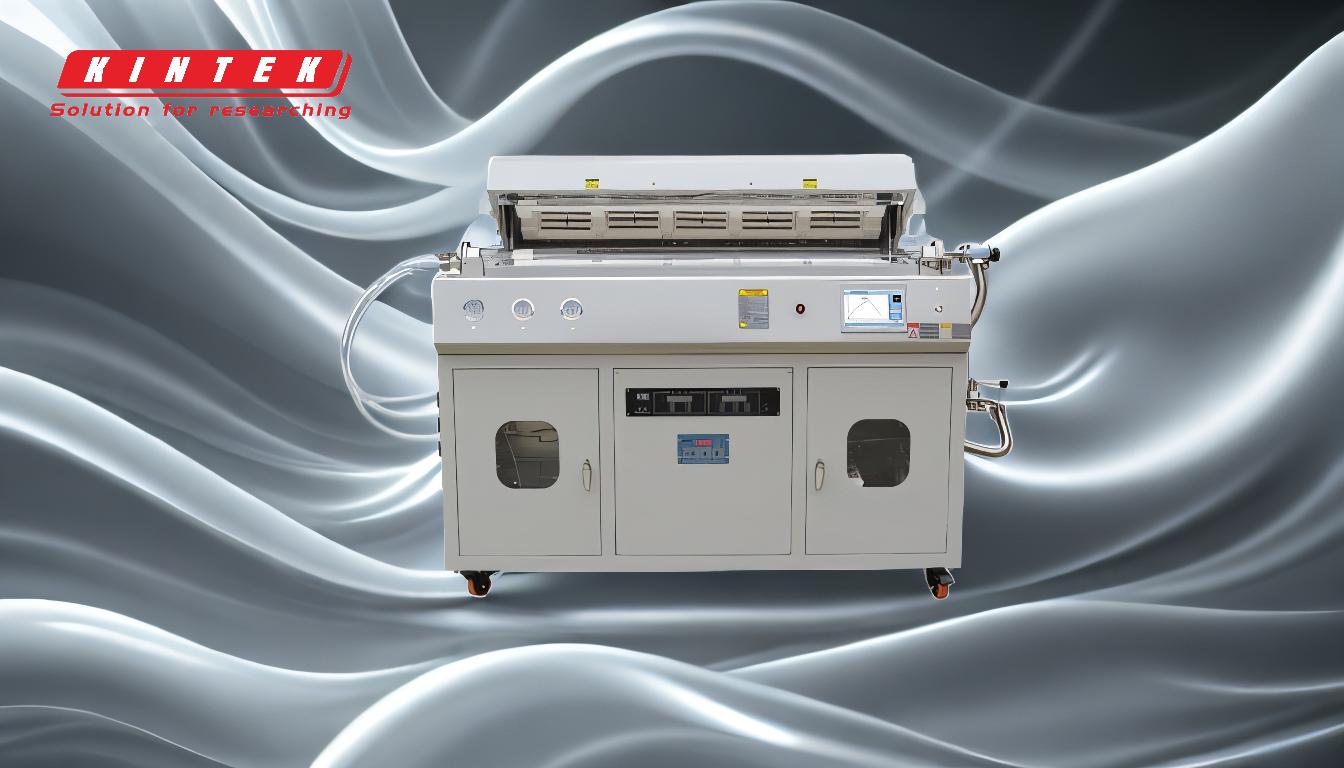
-
Definition und Zweck der Vakuumbeschichtung:
- Unter Vakuumbeschichtung versteht man eine Reihe von Verfahren, bei denen dünne Materialschichten in einer Hochvakuumumgebung auf ein Substrat aufgebracht werden.
- Der Hauptzweck besteht darin, Beschichtungen oder Filme mit präziser Dicke und verbesserten Eigenschaften zu erzeugen, wie z. B. verbesserte Leitfähigkeit, optische Leistung oder Korrosionsbeständigkeit.
-
So funktioniert die Vakuumbeschichtung:
- Das Verfahren findet in einer Vakuumkammer statt, in der der Druck erheblich reduziert ist, wodurch die Anwesenheit von Gasmolekülen minimiert wird.
- Das Material wird Atom für Atom oder Molekül für Molekül auf die Substratoberfläche aufgebracht, wodurch Gleichmäßigkeit und Präzision gewährleistet sind.
- Üblich sind Techniken wie thermisches Verdampfen, Sputtern, Ionenstrahlabscheidung und chemische Gasphasenabscheidung (CVD).
-
Schlüsseltechniken der Vakuumabscheidung:
- Physikalische Gasphasenabscheidung (PVD):Physikalische Übertragung von Material von einer Quelle auf das Substrat, oft unter Verwendung von Methoden wie Sputtern oder thermischer Verdampfung.
- Chemische Gasphasenabscheidung (CVD):Durch chemische Reaktionen wird das Material auf dem Substrat abgeschieden, oft bei erhöhten Temperaturen.
- Thermische Verdampfung:Das Material wird erhitzt, bis es verdampft und dann auf dem Substrat kondensiert.
- Sputtern:Atome werden aus einem Zielmaterial herausgeschleudert und mit Hilfe eines Plasma- oder Ionenstrahls auf dem Substrat abgeschieden.
-
Vorteile der Vakuumbeschichtung:
- Präzision:Ermöglicht die Abscheidung extrem dünner Schichten, sogar im Nanometerbereich.
- Saubere Umwelt:Das Vakuum minimiert Verunreinigungen und sorgt für hochwertige Beschichtungen.
- Vielseitigkeit:Kann für eine Vielzahl von Materialien verwendet werden, darunter Metalle, Keramiken und Polymere.
- Verbesserte Eigenschaften:Verbessert Eigenschaften wie Leitfähigkeit, optische Leistung und Korrosionsbeständigkeit.
-
Anwendungen der Vakuumbeschichtung:
- Elektronik:Wird bei der Herstellung von Halbleitern, Dünnschichttransistoren und Solarzellen verwendet.
- Optik:Herstellung von Antireflexionsbeschichtungen, Spiegeln und Linsen.
- Herstellung:Verbessert die Haltbarkeit und Leistung von Werkzeugen und Komponenten durch Schutzbeschichtungen.
- Medizinische Geräte:Bietet biokompatible Beschichtungen für Implantate und chirurgische Instrumente.
-
Herausforderungen und Überlegungen:
- Kosten:Vakuumbeschichtungsanlagen und -verfahren können teuer sein.
- Komplexität:Erfordert spezielle Kenntnisse und eine genaue Kontrolle der Prozessparameter.
- Skalierbarkeit:Während sie für Anwendungen in kleinem Maßstab effektiv sind, kann die Vergrößerung für die Massenproduktion eine Herausforderung darstellen.
-
Zukünftige Trends in der Vakuumbeschichtung:
- Nanotechnologie:Zunehmender Einsatz der Vakuumabscheidung in der Nanotechnologie zur Herstellung von Geräten und Materialien im Nanomaßstab.
- Nachhaltigkeit:Entwicklung energieeffizienter und umweltfreundlicher Abscheidungstechniken.
- Fortgeschrittene Materialien:Erforschung neuer Materialien, wie 2D-Materialien (z. B. Graphen) und hybride organisch-anorganische Verbindungen, für innovative Anwendungen.
Zusammenfassend lässt sich sagen, dass die Vakuumabscheidung eine entscheidende Technologie für die Herstellung hochwertiger dünner Schichten und Beschichtungen mit präziser Kontrolle über Dicke und Eigenschaften ist.Die Anwendungen erstrecken sich über verschiedene Industriezweige, und die ständigen Weiterentwicklungen erweitern die Fähigkeiten und Einsatzmöglichkeiten.
Zusammenfassende Tabelle:
Aspekt | Einzelheiten |
---|---|
Definition | Abscheidung von Material Atom für Atom im Vakuum zur Herstellung dünner Schichten. |
Schlüsseltechniken | PVD, CVD, thermische Verdampfung, Sputtering. |
Vorteile | Präzision, saubere Umgebung, Vielseitigkeit, verbesserte Materialeigenschaften. |
Anwendungen | Elektronik, Optik, Fertigung, medizinische Geräte. |
Herausforderungen | Hohe Kosten, Komplexität, Probleme mit der Skalierbarkeit. |
Zukünftige Trends | Nanotechnologie, Nachhaltigkeit, fortschrittliche Materialien. |
Entdecken Sie, wie die Vakuumbeschichtung Ihre Projekte aufwerten kann. Kontaktieren Sie unsere Experten noch heute !