Der VAR-Prozess (Vacuum Arc Remelting) ist eine entscheidende Methode in der Stahl- und Legierungsproduktion, insbesondere zur Erzielung hoher Reinheit und hervorragender Materialeigenschaften. Dabei werden vorgeformte Legierungselektroden unter Vakuumatmosphäre umgeschmolzen und so eine kontrollierte Erstarrung in einem wassergekühlten Kupfertiegel gewährleistet. Dieses Verfahren wird häufig für Edelstahl sowie Legierungen auf Nickel- und Titanbasis eingesetzt und erzeugt Materialien mit außergewöhnlicher Homogenität, Festigkeit und metallurgischen Eigenschaften. Der VAR-Prozess ist energieeffizient, reproduzierbar und in der Lage, Barren mit einheitlicher chemischer Zusammensetzung und kristalliner Struktur zu liefern, was ihn für Hochleistungsanwendungen unverzichtbar macht.
Wichtige Punkte erklärt:
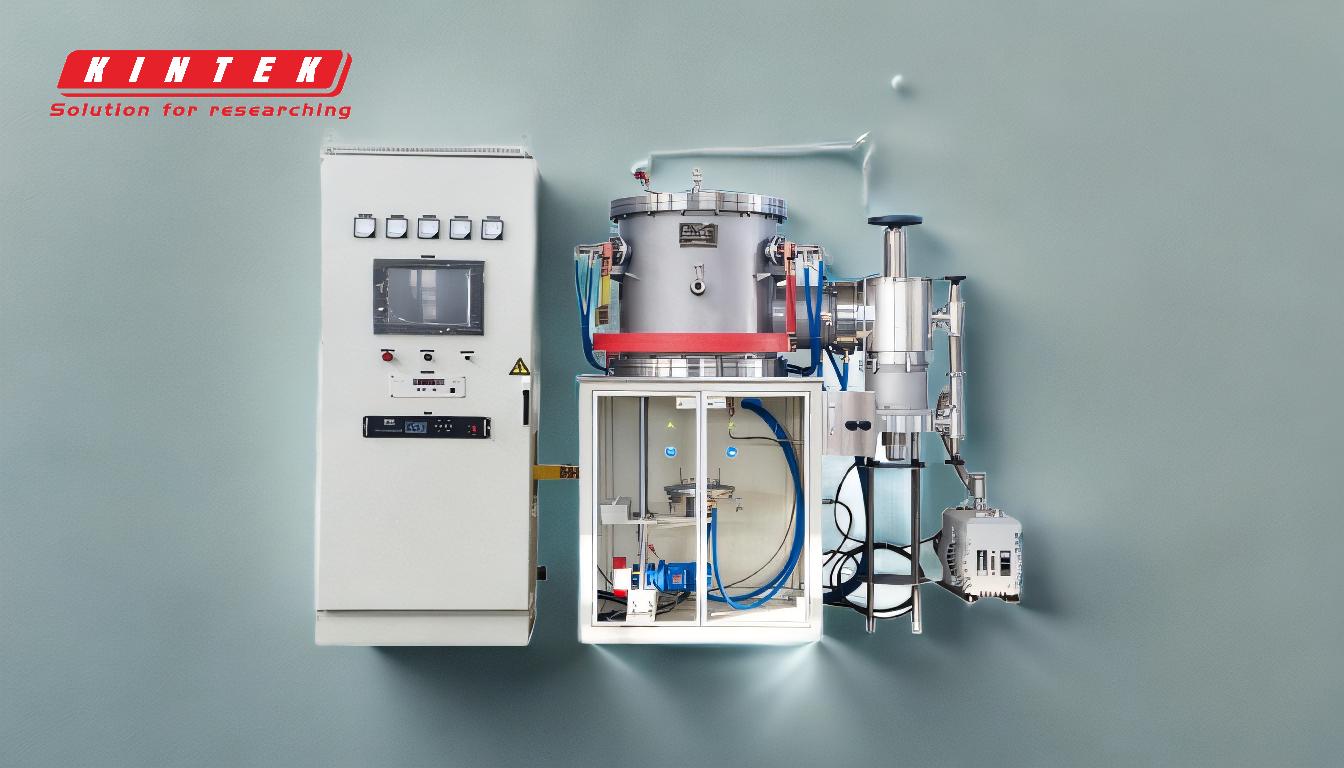
-
Definition und Zweck von VAR:
- VAR steht für Vacuum Arc Remelting, ein spezielles Produktionsverfahren zur Veredelung und Reinigung von Legierungen.
- Das Hauptziel besteht darin, hochreine Materialien mit überlegenen metallurgischen Eigenschaften wie Homogenität, Festigkeit und kontrollierter chemischer Zusammensetzung zu erhalten.
- Es ist besonders effektiv für Edelstahl sowie Legierungen auf Nickel- und Titanbasis, die häufig in anspruchsvollen Anwendungen wie der Luft- und Raumfahrt, medizinischen Geräten und Energiesystemen eingesetzt werden.
-
Prozessübersicht:
- Der VAR-Prozess beginnt mit einer vorgeformten Legierungselektrode, die typischerweise durch Vakuuminduktionsschmelzen (VIM) oder Pfannenschmelzen (Airmelt) hergestellt wird.
- Die Elektrode wird in einem wassergekühlten Kupfertiegel in einer Vakuumkammer platziert.
- Zwischen der Elektrode und dem Tiegel entsteht ein starker Lichtbogen, der die Elektrode zum Schmelzen bringt.
- Das geschmolzene Metall erstarrt auf kontrollierte Weise, wodurch eine gleichmäßige Abkühlung gewährleistet und Defekte minimiert werden.
-
Schlüsselkomponenten und ihre Rollen:
- Vakuumatmosphäre: Die Vakuumumgebung (0,001–0,1 mmHg oder 0,1–13,3 Pa) verhindert eine Kontamination durch atmosphärische Gase und gewährleistet so eine hohe Reinheit.
- Wassergekühlter Kupfertiegel: Erleichtert die kontrollierte Erstarrung und führt zu einem homogenen und fehlerfreien Barren.
- Elektrischer Lichtbogen: Bietet die zum Schmelzen der Elektrode erforderliche Wärme mit präziser Steuerung der Schmelzgeschwindigkeit und des Erstarrungsprozesses.
-
Vorteile von VAR:
- Hohe Reinheit: Die Vakuumumgebung beseitigt Verunreinigungen und Gase und führt zu saubereren Materialien.
- Kontrollierte Erstarrung: Sorgt für eine gleichmäßige Mikrostruktur und minimiert Defekte wie Porosität und Entmischung.
- Reproduzierbarkeit: Der Prozess ist sehr konsistent und eignet sich daher ideal für die Herstellung hochwertiger Barren in großen Mengen.
- Energieeffizienz: VAR ist für seinen geringen Stromverbrauch und seine hohe Schmelzgeschwindigkeit bekannt und daher kostengünstig.
-
Anwendungen von VAR:
- Luft- und Raumfahrt: VAR-verarbeitete Materialien werden aufgrund ihrer hohen Festigkeit und Zuverlässigkeit in kritischen Komponenten wie Turbinenschaufeln und Strukturteilen verwendet.
- Medizinische Geräte: Über VAR hergestellte Titanlegierungen werden aufgrund ihrer Biokompatibilität und mechanischen Eigenschaften in Implantaten und chirurgischen Instrumenten verwendet.
- Energiesektor: Mit VAR hergestellte Superlegierungen auf Nickelbasis sind für Hochtemperaturanwendungen in der Stromerzeugung und Ölraffinierung unverzichtbar.
-
Vergleich mit anderen Schmelzmethoden:
- Vakuuminduktionsschmelzen (VIM): Während VIM zur Herstellung der Anfangselektrode verwendet wird, bietet es nicht das gleiche Maß an Kontrolle über die Erstarrung wie VAR.
- Elektroschlacke-Umschmelzen (ESU): ESR ist eine weitere Raffinierungsmethode, die jedoch unter einer Schlackeschicht statt unter Vakuum arbeitet, wodurch sie bei der Entfernung bestimmter Verunreinigungen weniger effektiv ist.
- Luftschmelze: Herkömmliche Luftschmelzverfahren sind anfällig für Verunreinigungen und verfügen nicht über die Präzision von VAR, was sie für Hochleistungsanwendungen ungeeignet macht.
-
Technische Überlegungen für Gerätekäufer:
- Vakuumsystem: Stellen Sie sicher, dass das System die erforderlichen Vakuumwerte (0,001–0,1 mmHg) erreichen und aufrechterhalten kann.
- Kühlsystem: Der wassergekühlte Tiegel muss über eine effiziente Wärmeableitung verfügen, um eine kontrollierte Erstarrung zu gewährleisten.
- Stromversorgung: Eine stabile und stromstarke Stromversorgung ist für die Aufrechterhaltung des Lichtbogens unerlässlich.
- Automatisierung und Steuerung: Zur Überwachung und Anpassung von Parametern wie Schmelzrate, Temperatur und Vakuumniveau sind fortschrittliche Steuerungssysteme erforderlich.
-
Zukünftige Trends und Innovationen:
- Verbesserte Automatisierung: Verbesserte Kontrollsysteme und KI-gesteuerte Überwachung könnten den VAR-Prozess weiter optimieren.
- Materielle Fortschritte: Die Erforschung neuer Legierungszusammensetzungen kann die Palette der für die VAR-Verarbeitung geeigneten Materialien erweitern.
- Nachhaltigkeit: Bemühungen zur Reduzierung des Energieverbrauchs und der Verschwendung im VAR-Prozess dürften an Bedeutung gewinnen.
Durch das Verständnis des VAR-Prozesses und seiner Vorteile können Käufer von Geräten und Verbrauchsmaterialien fundierte Entscheidungen treffen, um ihre spezifischen Anforderungen zu erfüllen und die Produktion hochwertiger Materialien für kritische Anwendungen sicherzustellen.
Übersichtstabelle:
Aspekt | Einzelheiten |
---|---|
Zweck | Verfeinert und reinigt Legierungen für hochreine Materialien mit hervorragenden Eigenschaften. |
Schlüsselkomponenten | Vakuumatmosphäre, wassergekühlter Kupfertiegel, Lichtbogen. |
Vorteile | Hohe Reinheit, kontrollierte Erstarrung, Reproduzierbarkeit, Energieeffizienz. |
Anwendungen | Luft- und Raumfahrt, medizinische Geräte, Energiesysteme. |
Vergleich mit anderen | Übertrifft VIM, ESR und Luftschmelzen in Bezug auf Reinheit und Kontrolle. |
Zukünftige Trends | Verbesserte Automatisierung, neue Legierungsforschung, Nachhaltigkeitsbemühungen. |
Entdecken Sie, wie der VAR-Prozess Ihre Materialproduktion verbessern kann – Kontaktieren Sie noch heute unsere Experten für maßgeschneiderte Lösungen!