Die Vakuumbeschichtung von Aluminium ist ein spezielles Beschichtungsverfahren, bei dem Aluminium in einer Vakuumumgebung auf ein Substrat aufgebracht wird. Bei dieser Technik wird festes Aluminium unter niedrigem Druck verdampft, so dass sich die Aluminiumatome oder -moleküle frei bewegen und ohne Störung durch Luftmoleküle auf der Zieloberfläche haften können. Das Verfahren wird häufig eingesetzt, um dünne, gleichmäßige Aluminiumschichten auf verschiedenen Materialien zu erzeugen und Eigenschaften wie Reflexionsvermögen, Leitfähigkeit und Korrosionsbeständigkeit zu verbessern. Zu den Anwendungen gehören die Herstellung von Spiegeln, optischen Komponenten und Schutzschichten für Kunststoffe. Die Vakuumumgebung gewährleistet eine präzise Steuerung des Abscheidungsprozesses und ermöglicht so hochwertige, dauerhafte Beschichtungen.
Die wichtigsten Punkte werden erklärt:
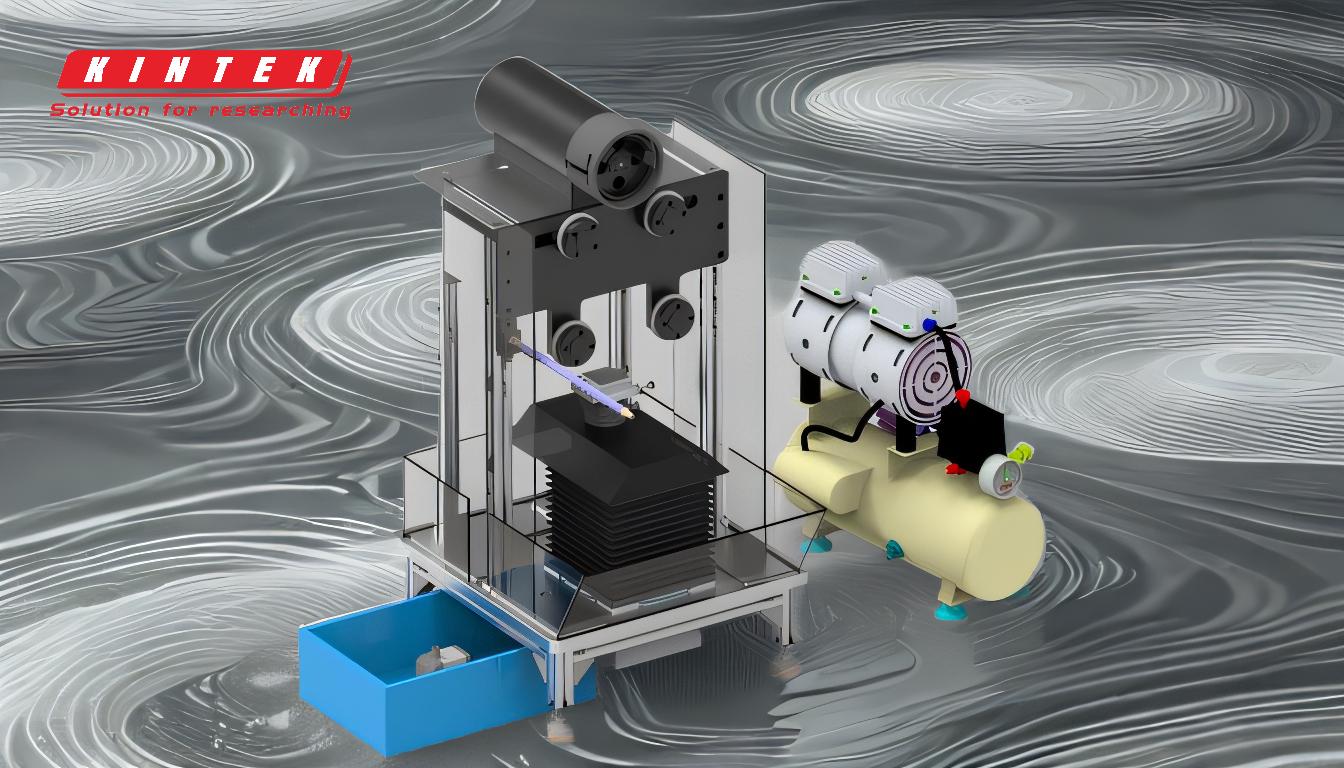
-
Definition der Vakuumabscheidung von Aluminium:
- Bei der Vakuumbeschichtung von Aluminium wird Aluminium in einer Vakuumkammer aufgedampft und auf ein Substrat aufgebracht. Die Vakuumumgebung minimiert die Anwesenheit von Gasmolekülen, so dass sich Aluminiumatome oder -moleküle ungehindert bewegen und eine dünne, gleichmäßige Schicht auf der Zieloberfläche bilden können.
-
Wie der Prozess funktioniert:
- Das Verfahren beginnt damit, dass das Substrat (z. B. Glas, Kunststoff oder Metall) und das feste Aluminium in eine Vakuumkammer gebracht werden.
- Die Kammer wird evakuiert, um Luft und andere Gase zu entfernen, so dass eine Umgebung mit niedrigem Druck entsteht.
- Aluminium wird erhitzt, bis es verdampft und ein Dampf aus Aluminiumatomen oder -molekülen entsteht.
- Der Aluminiumdampf wandert durch das Vakuum und kondensiert auf dem Substrat, wo er eine dünne, gleichmäßige Schicht bildet.
-
Die wichtigsten Vorteile der Vakuumbeschichtung:
- Präzision und Kontrolle: Die Vakuumumgebung ermöglicht eine präzise Steuerung des Abscheidungsprozesses und damit die Herstellung ultradünner Schichten, selbst im Nanometerbereich.
- Einheitlichkeit: Die Abwesenheit von Luftmolekülen sorgt dafür, dass die Aluminiumbeschichtung gleichmäßig und frei von Fehlern ist.
- Vielseitigkeit: Dieses Verfahren kann auf einer Vielzahl von Substraten eingesetzt werden, darunter Kunststoffe, Metalle und Glas.
- Verbesserte Materialeigenschaften: Aluminiumbeschichtungen verbessern Eigenschaften wie das Reflexionsvermögen (z. B. bei Spiegeln), die elektrische Leitfähigkeit und die Korrosionsbeständigkeit.
-
Anwendungen von vakuumabgeschiedenem Aluminium:
- Optische Komponenten: Wird verwendet, um reflektierende Oberflächen in Spiegeln, Teleskopen und anderen optischen Geräten zu erzeugen.
- Verpackung: Aluminiumbeschichtungen werden auf Kunststofffolien für Lebensmittelverpackungen aufgebracht, um eine Barriere gegen Feuchtigkeit und Sauerstoff zu schaffen.
- Elektronik: Wird bei der Herstellung von leitfähigen Schichten für elektronische Bauteile und Displays verwendet.
- Schützende Beschichtungen: Wird auf Kunststoffe und Metalle aufgetragen, um die Haltbarkeit und Beständigkeit gegen Umwelteinflüsse zu erhöhen.
-
Vergleich mit anderen Beschichtungsmethoden:
- Im Gegensatz zur Galvanik, bei der chemische Reaktionen ablaufen und leitende Substrate erforderlich sind, ist die Vakuumbeschichtung ein physikalisches Verfahren, das auch auf nichtleitenden Materialien wie Kunststoffen angewendet werden kann.
- Im Vergleich zur chemischen Gasphasenabscheidung (CVD) arbeitet die Vakuumabscheidung bei niedrigeren Temperaturen und ist daher für wärmeempfindliche Materialien geeignet.
-
Ökologische und betriebliche Erwägungen:
- Die Vakuumumgebung macht den Einsatz von chemischen Lösungsmitteln überflüssig und verringert so die Umweltbelastung.
- Das Verfahren erfordert spezielle Ausrüstungen, wie z. B. Vakuumkammern und Verdampfungsquellen, die zwar kostspielig sind, aber langfristige Vorteile in Bezug auf die Qualität und Haltbarkeit der Beschichtung bieten.
-
Herausforderungen und Beschränkungen:
- Kosten der Ausrüstung: Der Bedarf an Vakuumkammern und hochpräzisen Geräten kann das Verfahren teuer machen.
- Kompatibilität der Substrate: Obwohl sie vielseitig einsetzbar sind, haften manche Materialien ohne zusätzliche Oberflächenbehandlung nicht gut auf Aluminiumbeschichtungen.
- Komplexität der Prozesse: Um konsistente Ergebnisse zu erzielen, ist eine sorgfältige Kontrolle von Parametern wie Vakuumdruck, Temperatur und Abscheidungsrate erforderlich.
Durch das Verständnis dieser Schlüsselpunkte können Käufer von Anlagen und Verbrauchsmaterialien beurteilen, ob die Vakuumbeschichtung von Aluminium die richtige Lösung für ihre spezifischen Anforderungen ist, wobei Faktoren wie Kosten, Anwendungsanforderungen und gewünschte Materialeigenschaften zu berücksichtigen sind.
Zusammenfassende Tabelle:
Hauptaspekt | Einzelheiten |
---|---|
Prozess | Aluminium wird in einer Vakuumkammer aufgedampft und auf ein Substrat aufgebracht. |
Vorteile | Präzision, Gleichmäßigkeit, Vielseitigkeit, verbesserte Materialeigenschaften. |
Anwendungen | Optische Komponenten, Verpackungen, Elektronik, Schutzbeschichtungen. |
**Vergleich mit anderen Methoden | Keine chemischen Reaktionen, niedrigere Temperaturen, geeignet für nicht leitende Materialien. |
Herausforderungen | Hohe Gerätekosten, Substratkompatibilität, Prozesskomplexität. |
Entdecken Sie, wie Ihre Projekte von der Vakuumbeschichtung von Aluminium profitieren können kontaktieren Sie uns noch heute für fachkundige Beratung!