Vakuumlaminierung ist ein spezielles Herstellungsverfahren, bei dem mehrere Materialschichten unter Vakuumdruck miteinander verbunden werden, um Eigenschaften wie Festigkeit, Stabilität und Aussehen zu verbessern.Diese Technik ist in verschiedenen Branchen weit verbreitet, unter anderem in der Elektronik-, Automobil-, Bau- und Kunstgewerbebranche.Durch die Anwendung von Vakuumdruck gewährleistet das Verfahren eine gleichmäßige Haftung und eliminiert Luftblasen, was zu qualitativ hochwertigen, langlebigen laminierten Produkten führt.Das Vakuumlaminieren eignet sich besonders gut für die Herstellung komplexer Formen, gekrümmter Oberflächen und komplizierter Designs und ist damit eine vielseitige Lösung für Anwendungen, die von Leiterplatten und Kohlefaserarbeiten bis hin zur Möbelproduktion und dem Musikinstrumentenbau reichen.
Die wichtigsten Punkte erklärt:
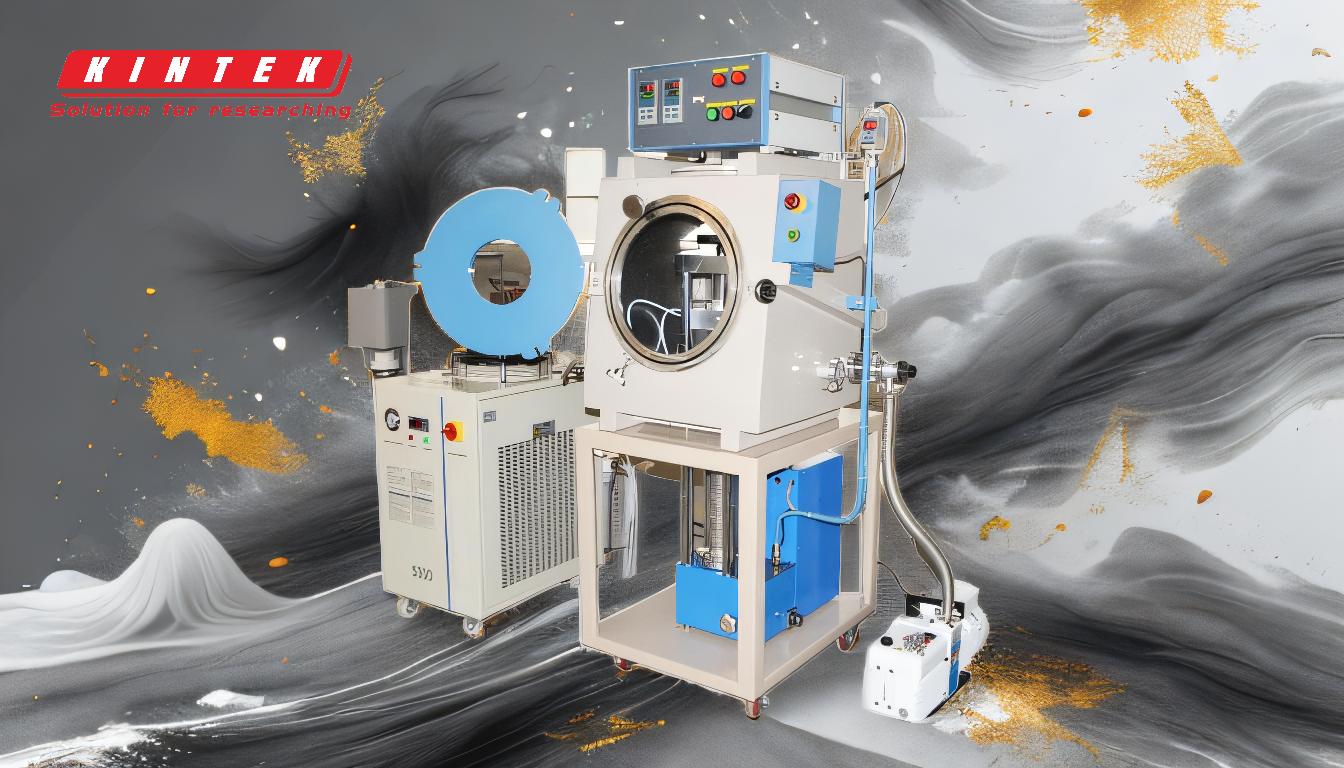
-
Definition und Zweck der Vakuumkaschierung:
- Vakuumlaminierung ist ein Verfahren, bei dem mehrere Materialschichten unter Vakuumdruck miteinander verbunden werden, um ein Verbundmaterial mit verbesserten Eigenschaften zu schaffen.
- Der Hauptzweck besteht darin, die Festigkeit, Stabilität und Ästhetik zu verbessern und gleichzeitig eine gleichmäßige Haftung zu gewährleisten und Mängel wie Luftblasen zu beseitigen.
-
Branchenübergreifende Anwendungen:
- Elektronik:Wird bei der Herstellung von Leiterplatten (PCBs), keramischen Vielschichtkondensatoren (MLCCs) und Hybridchips verwendet.
- Automobilindustrie:Angewandt bei der Verarbeitung von Karbonfasern, Autoarmaturenbrettern und der Herstellung von Bremsleitungen.
- Konstruktion und Möbel:Wird für die Laminierung von dekorativen Oberflächen, feuerfesten Türen und gebogenen Treppenwangen verwendet.
- Dekorative Kunst und Kunsthandwerk:Beschäftigt in der Foto- und Kunstmontage, im Musikinstrumentenbau und in der Töpferwarenherstellung.
- Spezialisierte Fertigung:Dazu gehören der Bau von Surfbrettern, die Herstellung von funkgesteuerten Flugzeugen/Gleitern und die Herstellung von Bodenmedaillons.
-
Materialien und Techniken:
- Die bei der Vakuumlaminierung verwendeten Materialien reichen von Holzfurnieren und Kohlefasern bis hin zu Keramik und Leder.
- Bei diesem Verfahren werden die Materialien in einen Vakuumsack oder eine Vakuumkammer gelegt, Hitze und Druck angewendet und der Klebstoff gleichmäßig ausgehärtet.
-
Vorteile der Vakuumkaschierung:
- Gleichmäßige Druckverteilung:Sorgt für eine gleichmäßige Verklebung auf der gesamten Oberfläche.
- Komplexe Formen und Kurven:Ermöglicht die Gestaltung komplizierter Designs und gebogener Oberflächen.
- Hochwertiges Finish:Erzeugt glatte, blasenfreie Laminate mit verbesserter Haltbarkeit und Ästhetik.
-
Ausrüstung und Werkzeuge:
- Spezialisierte Vakuumpressen und Laminiermaschinen werden eingesetzt, um Druck, Temperatur und Vakuum präzise zu steuern.
- Diese Maschinen sind sowohl für flache als auch für gewölbte Oberflächen geeignet und daher für verschiedene Anwendungen einsetzbar.
-
Prozess-Schritte:
- Vorbereitung:Schichten von Materialien mit Klebstoff dazwischen anordnen.
- Vakuumversiegelung:Legen Sie die Baugruppe in einen Vakuumbeutel oder eine Vakuumkammer.
- Anwendung von Hitze und Druck:Aktivieren Sie die Vakuumpresse, um die Luft zu entfernen und einen gleichmäßigen Druck auszuüben.
- Aushärtung:Lassen Sie den Klebstoff unter kontrollierten Bedingungen aushärten.
- Fertigstellung:Entnehmen Sie das laminierte Produkt und führen Sie alle erforderlichen Nachbearbeitungen durch.
-
Branchen, die von der Vakuumkaschierung profitieren:
- Elektronik:Verbessert die Leistung und Zuverlässigkeit von Komponenten.
- Automobilindustrie:Verbessert die Festigkeit und Ästhetik der Teile.
- Konstruktion:Bietet dauerhafte und visuell ansprechende Oberflächen.
- Kunst und Kunsthandwerk:Ermöglicht die Erstellung hochwertiger, komplizierter Designs.
-
Zukünftige Trends und Innovationen:
- Die Fortschritte in der Vakuumlaminiertechnik konzentrieren sich auf Automatisierung, Energieeffizienz und die Verwendung umweltfreundlicher Materialien.
- Neue Anwendungen entstehen in Bereichen wie erneuerbare Energien (z. B. Herstellung von Solarzellen) und Luft- und Raumfahrt (z. B. leichte Verbundwerkstoffe).
Durch das Verständnis der Prinzipien und Anwendungen der Vakuumlaminierung können Hersteller und Einkäufer fundierte Entscheidungen über ihren Einsatz in verschiedenen Branchen treffen und so hochwertige, kostengünstige und innovative Lösungen sicherstellen.
Zusammenfassende Tabelle:
Aspekt | Einzelheiten |
---|---|
Zweck | Verklebt Materialien unter Vakuumdruck, um Festigkeit, Stabilität und Ästhetik zu verbessern. |
Anwendungen | Elektronik, Automobilindustrie, Bauwesen, Kunstgewerbe und spezialisierte Fertigung. |
Werkstoffe | Holzfurniere, Kohlefaser, Keramik, Leder und mehr. |
Vorteile | Gleichmäßiger Druck, komplexe Formen, hochwertige Verarbeitung und blasenfreie Ergebnisse. |
Ausrüstung | Vakuumpressen und Laminiermaschinen für eine präzise Kontrolle. |
Prozess-Schritte | Vorbereitung, Vakuumversiegelung, Wärme-/Druckanwendung, Aushärtung, Endbearbeitung. |
Zukünftige Trends | Automatisierung, Energieeffizienz, umweltfreundliche Materialien und neue Anwendungen in den Bereichen erneuerbare Energien und Luft- und Raumfahrt. |
Erschließen Sie das Potenzial der Vakuumlaminierung für Ihre Projekte. Kontaktieren Sie uns noch heute für fachkundige Beratung!