Ein Vakuum ist bei der Abscheidung dünner Schichten unerlässlich, um hochwertige, reine und haftende Schichten zu gewährleisten.Die Vakuumumgebung reduziert den Gasdruck, so dass die verdampften Atome längere Strecken zurücklegen können, ohne mit anderen Partikeln zusammenzustoßen, was die Keimbildung und Rußbildung minimiert.Außerdem wird die Verunreinigung erheblich gesenkt, da unerwünschte Stoffe wie Sauerstoff, Stickstoff und Kohlendioxid entfernt werden, die die Filmbildung beeinträchtigen, die Haftung schwächen oder Verunreinigungen einbringen können.Darüber hinaus ermöglicht das Vakuum eine präzise Steuerung der Gas- und Dampfzusammensetzung, erleichtert eine Niederdruck-Plasmaumgebung und gewährleistet eine effiziente Steuerung des Massenstroms - alles entscheidende Faktoren für die Herstellung konsistenter und leistungsstarker Dünnschichten.
Die wichtigsten Punkte werden erklärt:
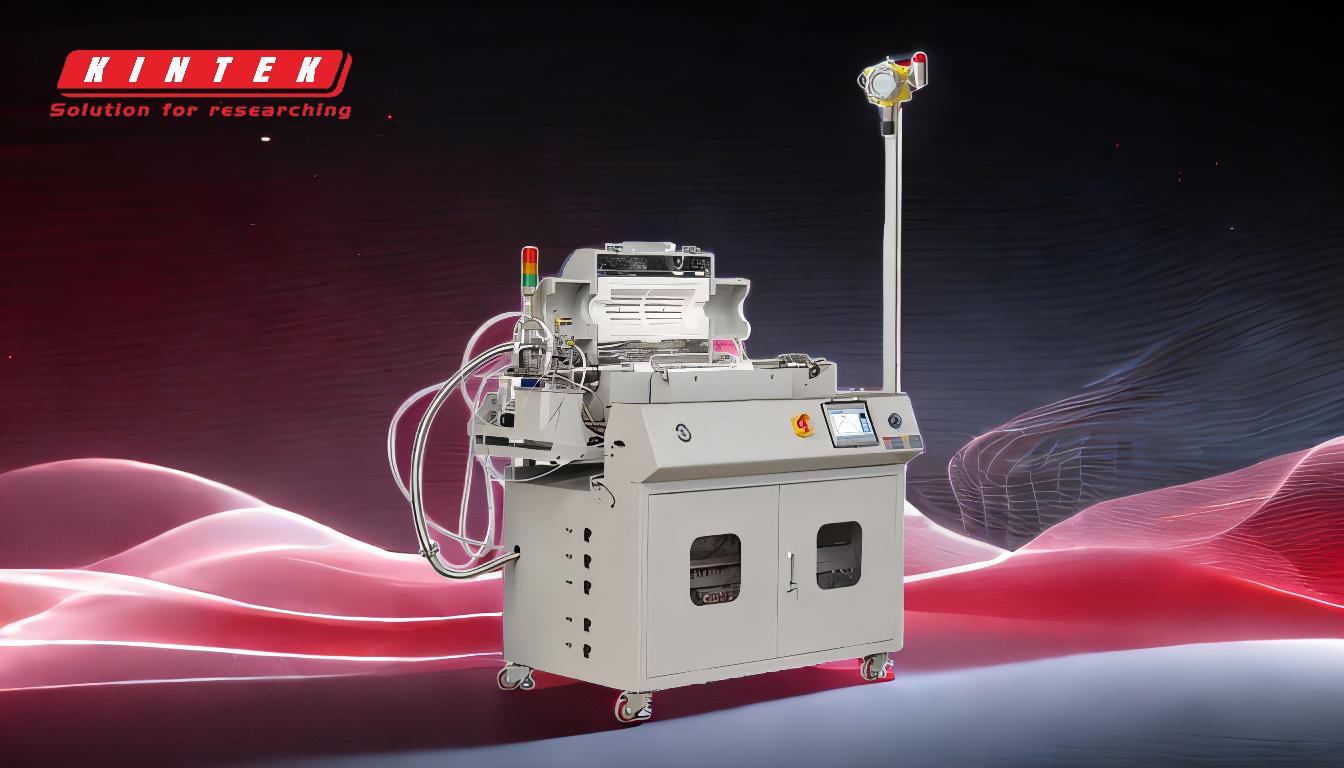
-
Verringerung des Gasdrucks für einen längeren mittleren freien Weg:
- Im Vakuum ist der Gasdruck erheblich reduziert, so dass die verdampften Atome oder Moleküle längere Strecken zurücklegen können, ohne mit anderen Partikeln zusammenzustoßen.Dieser längere mittelfreie Weg sorgt dafür, dass die Partikel das Substrat erreichen können, ohne unerwünschte Cluster oder Ruß zu bilden, die die Qualität der dünnen Schicht beeinträchtigen würden.
- Ohne Vakuum würde die hohe Dichte der Gasmoleküle zu häufigen Zusammenstößen führen, die Keimbildung und die Bildung von Partikeln zur Folge hätten, welche die Schicht verunreinigen könnten.
-
Minimierung von Verunreinigungen:
- In einer Vakuumumgebung wird die Anwesenheit von Verunreinigungen wie Sauerstoff, Stickstoff, Kohlendioxid und Wasserdampf drastisch reduziert.Diese Verunreinigungen können mit dem Filmmaterial reagieren und zu Verunreinigungen, Oxidation oder anderen chemischen Reaktionen führen, die die Eigenschaften des Films beeinträchtigen.
- So kann beispielsweise Sauerstoff Metallfilme oxidieren, während Wasserdampf Wasserstoff- oder Hydroxylgruppen einbringen kann, die die elektrischen oder optischen Eigenschaften des Films verändern.
-
Kontrolle der Zusammensetzung von Gasen und Dämpfen:
- Ein Vakuum ermöglicht eine präzise Kontrolle der Zusammensetzung der Gase und Dämpfe in der Beschichtungskammer.Dies ist entscheidend für Verfahren wie die chemische Gasphasenabscheidung (CVD) oder die plasmaunterstützte CVD, bei denen bestimmte Gasmischungen erforderlich sind, um die gewünschten Schichteigenschaften zu erzielen.
- Durch die Aufrechterhaltung einer kontrollierten Umgebung kann der Abscheidungsprozess fein abgestimmt werden, um Schichten mit bestimmten Eigenschaften wie Leitfähigkeit, Transparenz oder Härte zu erzeugen.
-
Erleichterung der Niederdruck-Plasmaumgebung:
- Viele Verfahren zur Dünnschichtabscheidung, wie z. B. das Sputtern oder die plasmagestützte Abscheidung, beruhen auf einem Niederdruckplasma, um Gase zu ionisieren und reaktive Spezies zu erzeugen.Zur Aufrechterhaltung dieses Plasmas ist ein Vakuum erforderlich, da es eine niedrige Teilchendichte benötigt, um effektiv zu funktionieren.
- Das Plasma erhöht die Energie der Partikel und verbessert die Haftung und Gleichmäßigkeit des Films.
-
Ermöglicht hohe thermische Verdampfungsraten:
- Bei physikalischen Aufdampfverfahren (PVD) wie der thermischen Verdampfung sorgt ein Vakuum dafür, dass das zu verdampfende Material das Substrat erreichen kann, ohne von Gasmolekülen behindert zu werden.Dies führt zu einer hohen Abscheiderate und einem dichten, gleichmäßigen Film.
- Da keine Gasmoleküle vorhanden sind, wird auch die Streuung des verdampften Materials verhindert, so dass es sich direkt auf dem Substrat ablagert.
-
Verbesserte Reinheit und Haftung des Films:
- Ein Hochvakuum sorgt dafür, dass sich das Folienmaterial direkt mit dem Substrat verbindet, ohne dass Verunreinigungen eindringen.Dies führt zu einer Folie mit hoher Reinheit und starker Haftung, was für Anwendungen, die Haltbarkeit und Leistung erfordern, entscheidend ist.
- Verunreinigungen oder schwache Adhäsion können zu Delamination, verminderter Leitfähigkeit oder anderen Fehlern im Endprodukt führen.
-
Massenflusskontrolle und Prozesskonsistenz:
- Eine Vakuumumgebung ermöglicht eine präzise Steuerung des Massenstroms von Gasen und Dämpfen in die Beschichtungskammer.Dies gewährleistet gleichbleibende Prozessbedingungen, die für die Herstellung einheitlicher dünner Schichten mit reproduzierbaren Eigenschaften unerlässlich sind.
- Schwankungen des Drucks oder der Gaszusammensetzung können zu Defekten oder Unregelmäßigkeiten in der Schicht führen, so dass die Vakuumkontrolle ein Schlüsselfaktor für die Erzielung hochwertiger Ergebnisse ist.
Zusammenfassend lässt sich sagen, dass die Verwendung eines Vakuums bei der Abscheidung von Dünnschichten entscheidend ist, um die Reinheit, Gleichmäßigkeit und Leistung der abgeschiedenen Schichten zu gewährleisten.Es minimiert Verunreinigungen, steuert die Abscheidungsumgebung und ermöglicht eine präzise Prozesssteuerung, was alles für die Herstellung hochwertiger Dünnschichten für eine Vielzahl von Anwendungen unerlässlich ist.
Zusammenfassende Tabelle:
Hauptnutzen | Erläuterung |
---|---|
Verringerung des Gasdrucks | Ermöglicht es den verdampften Atomen, längere Strecken zurückzulegen, wodurch Keimbildung und Rußbildung minimiert werden. |
Minimierung von Verunreinigungen | Entfernt unerwünschte Stoffe wie Sauerstoff, Stickstoff und Kohlendioxid. |
Kontrolle der Gas- und Dampfzusammensetzung | Ermöglicht eine präzise Steuerung von Verfahren wie CVD und plasmagestützter Abscheidung. |
Niederdruck-Plasmaumgebung | Erleichtert die plasmagestützte Abscheidung für bessere Schichthaftung und Gleichmäßigkeit. |
Hohe thermische Verdampfungsraten | Sorgt für dichte, gleichmäßige Schichten bei PVD-Verfahren wie der thermischen Verdampfung. |
Verbesserte Filmreinheit und Haftung | Verbindet das Filmmaterial direkt mit dem Substrat und gewährleistet hohe Reinheit und Festigkeit. |
Massenflusskontrolle und Prozesskonsistenz | Sorgt für gleichbleibende Prozessbedingungen und damit für reproduzierbare Eigenschaften der Dünnschicht. |
Benötigen Sie hochwertige Dünnschichten für Ihre Anwendungen? Kontaktieren Sie noch heute unsere Experten um mehr zu erfahren!