Abscheidekammern, insbesondere bei PVD-Verfahren (Physical Vapor Deposition), arbeiten unter Hochvakuumbedingungen, um eine optimale Materialabscheidung zu gewährleisten.Diese Umgebung minimiert Verunreinigungen, ermöglicht eine präzise Steuerung des Abscheidungsprozesses und gewährleistet, dass das Material fest auf dem Substrat haftet.Hochvakuumbedingungen sind für Prozesse wie die Mikrochip-Herstellung unerlässlich, bei denen schon geringe Verunreinigungen zu erheblichen Mängeln führen können.Die Vakuumumgebung vergrößert auch die mittlere freie Weglänge der Atome, was einen effizienten Materialtransfer und hohe thermische Verdampfungsraten ermöglicht.
Die wichtigsten Punkte erklärt:
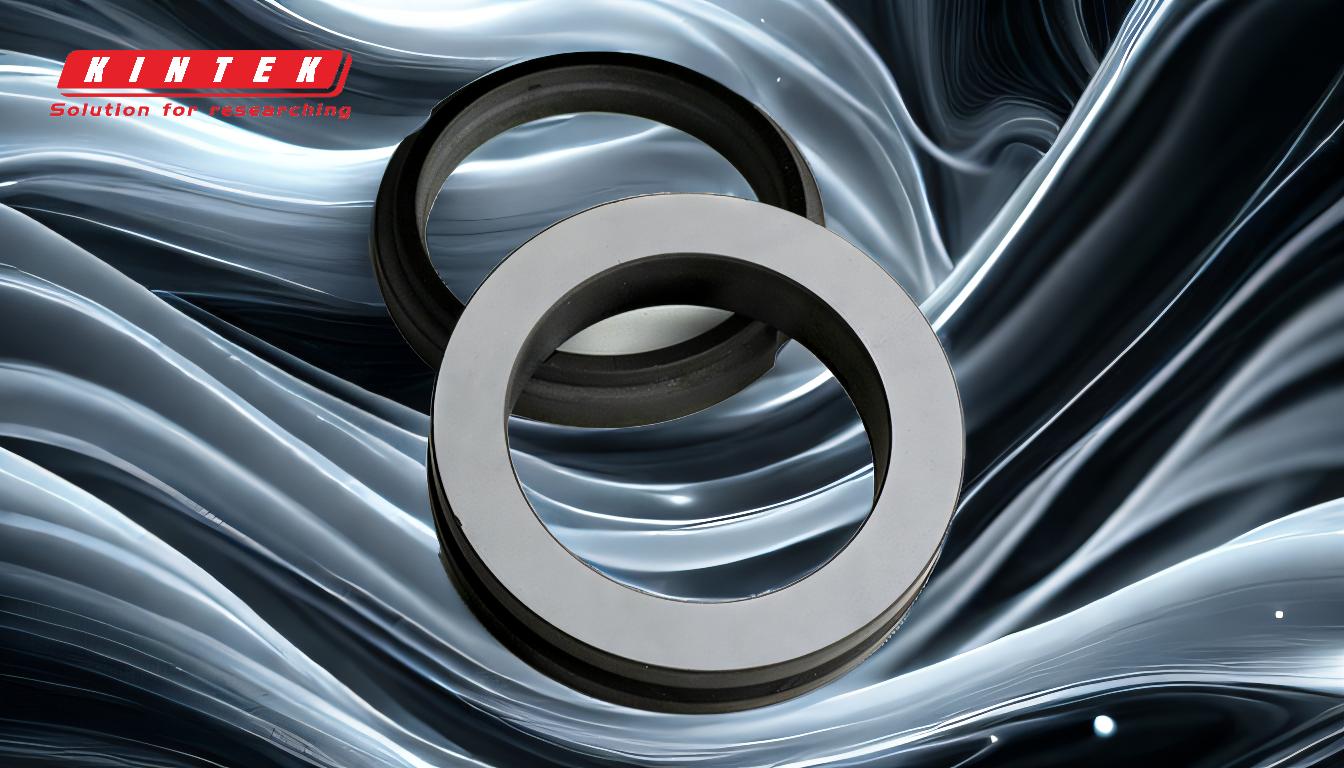
-
Minimierung der Kontamination:
- Eine Hochvakuumumgebung reduziert das Vorhandensein unerwünschter Atome und Moleküle, die sonst den Abscheidungsprozess verunreinigen könnten, erheblich.Dies ist entscheidend für Anwendungen wie die Mikrochip-Herstellung, wo selbst winzige Partikel Defekte verursachen können.Das Hochvakuum sorgt für eine saubere Umgebung, frei von Staub, Feuchtigkeit und anderen Verunreinigungen, die den Abscheidungsprozess beeinträchtigen könnten.
-
Erhöhung der mittleren freien Weglänge:
- Im Hochvakuum ist die Dichte der Atome und Moleküle drastisch reduziert, wodurch sich die mittlere freie Weglänge der am Abscheidungsprozess beteiligten Teilchen erhöht.Das bedeutet, dass die Atome oder Moleküle längere Strecken zurücklegen können, ohne mit anderen Teilchen zusammenzustoßen, so dass sie das Substrat mit genügend Energie erreichen, um fest zu haften.Dies ist besonders wichtig, um gleichmäßige und hochwertige Beschichtungen zu erzielen.
-
Ermöglichung hoher thermischer Verdampfungsraten:
- Hochvakuumbedingungen ermöglichen höhere thermische Verdampfungsraten, die für einen effizienten Materialtransfer unerlässlich sind.Im Vakuum können Materialien auf hohe Temperaturen erhitzt werden, ohne dass die Gefahr einer Oxidation oder anderer unerwünschter chemischer Reaktionen besteht.Dadurch wird sichergestellt, dass das Material gleichmäßig verdampft und sich gleichmäßig auf dem Substrat ablagert.
-
Erleichtert kontrollierte und wiederholbare Prozesse:
- Eine Hochvakuumumgebung bietet einen kontrollierten und wiederholbaren Rahmen für Abscheidungsprozesse.Durch die Eliminierung von Variablen wie Luftdruck und Verunreinigung können Hersteller über mehrere Chargen hinweg gleichbleibende Ergebnisse erzielen.Dies ist besonders wichtig in Branchen wie der Halbleiterherstellung, wo Präzision und Beständigkeit entscheidend sind.
-
Verhindern chemischer Reaktionen (sofern nicht erwünscht):
- Bei PVD-Verfahren verhindert die Hochvakuumumgebung unerwünschte chemische Reaktionen und gewährleistet, dass das abgeschiedene Material rein bleibt.Ist jedoch eine chemische Reaktion erwünscht - wie etwa die Zufuhr von Sauerstoff zur Erzeugung von Oxidschichten -, kann die Vakuumumgebung so eingestellt werden, dass kontrollierte Reaktionen möglich sind.Diese Flexibilität ist ein entscheidender Vorteil von Hochvakuum-Beschichtungskammern.
-
Unterstützt fortschrittliche Fertigungsanwendungen:
- Hochvakuumbedingungen sind für fortschrittliche Fertigungsanwendungen, wie die Herstellung von Mikrochips, CDs und DVDs, unerlässlich.Diese Prozesse erfordern eine extrem saubere Umgebung, um sicherzustellen, dass die Endprodukte frei von Mängeln sind.Die Hochvakuumumgebung in Abscheidekammern ist entscheidend für die Einhaltung der strengen Qualitätsstandards, die in diesen Branchen gefordert werden.
Zusammenfassend lässt sich sagen, dass die Hochvakuumumgebung in Beschichtungskammern für die Minimierung von Verunreinigungen, die Erhöhung der mittleren freien Weglänge von Partikeln, die Ermöglichung hoher thermischer Verdampfungsraten und die Erleichterung kontrollierter und wiederholbarer Prozesse von wesentlicher Bedeutung ist.Diese Faktoren zusammen gewährleisten eine qualitativ hochwertige Materialabscheidung und machen Hochvakuumbedingungen in modernen Fertigungs- und PVD-Prozessen unverzichtbar.
Zusammenfassende Tabelle:
Hauptnutzen | Erläuterung |
---|---|
Minimierung der Kontamination | Reduziert unerwünschte Atome und Moleküle und gewährleistet eine saubere Umgebung für die Abscheidung. |
Vergrößerung der mittleren freien Weglänge | Ermöglicht es den Partikeln, längere Strecken ohne Kollisionen zurückzulegen, was eine feste Haftung gewährleistet. |
Ermöglicht hohe thermische Verdampfungsraten | Gewährleistet einen effizienten Materialtransfer und eine gleichmäßige Abscheidung. |
Erleichterung von kontrollierten Prozessen | Bietet eine wiederholbare Umgebung für konsistente Ergebnisse über alle Chargen hinweg. |
Verhinderung unerwünschter Reaktionen | Bewahrt die Materialreinheit und ermöglicht bei Bedarf kontrollierte Reaktionen. |
Unterstützt fortschrittliche Anwendungen | Unverzichtbar für die Mikrochip-Herstellung und andere Hochpräzisionsindustrien. |
Erfahren Sie, wie Hochvakuum-Beschichtungskammern Ihren Fertigungsprozess verbessern können. Kontaktieren Sie uns noch heute !