Einführung in die Bedeutung von Ofenatmosphären
Ofenatmosphären spielen bei verschiedenen Wärmebehandlungsprozessen wie Sintern und Glühen eine entscheidende Rolle. Sie sind wichtig, um Oxidation zu verhindern, das Kontaminationsrisiko zu verringern und die Eigenschaften der behandelten Materialien zu verbessern. Ein Ofen mit inerter Atmosphäre ist beispielsweise darauf ausgelegt, eine kontrollierte Umgebung aufrechtzuerhalten, die frei von Sauerstoff, Feuchtigkeit und anderen Verunreinigungen ist. Dieser Ofentyp wird in Anwendungen eingesetzt, die eine Hochtemperaturverarbeitung von Materialien wie Keramik, Metallen und Verbundwerkstoffen erfordern. Der Einsatz von Öfen mit kontrollierter Atmosphäre kann zu einer verbesserten Materialqualität, einer höheren Effizienz und geringeren Kosten führen.
Inhaltsverzeichnis
- Einführung in die Bedeutung von Ofenatmosphären
- Was ist ein Inertatmosphärenofen?
- Verwendung von Inertatmosphärenöfen zum Sintern und Glühen
- Vorteile von Öfen mit kontrollierter Atmosphäre
- Verbesserte Umweltbedingungen
- Bessere Ofensteuerung und effizienter Durchsatz
- Zwei Hauptkategorien: Chargen- und Durchlauföfen
- Atmosphärenöfen von KINTEK
- Abschluss
Was ist ein Inertatmosphärenofen?
Ein Inertatmosphärenofen ist eine Art Laborgerät, das für Sinter- und Glühprozesse verwendet wird. Es sorgt für eine kontrollierte, sauerstofffreie Umgebung, die für bestimmte Hochtemperaturanwendungen unerlässlich ist. Inert bedeutet chemisch inaktiv, weshalb für chemische Prozesse, die keine Kontamination mit reaktiven Gasen erfordern, inerte Atmosphären erforderlich sind.
Wie funktioniert ein Inertatmosphärenofen?
Inertatmosphärenöfen entfernen Sauerstoff und andere reaktive Gase aus der Umgebung. Dies wird erreicht, indem der Ofen mit einem Inertgas wie Stickstoff oder Argon gespült wird. Anschließend wird der Ofen auf die gewünschte Temperatur aufgeheizt und das zu sinternde oder zu glühende Material hineingelegt. Der Ofen ist versiegelt, um die inerte Atmosphäre aufrechtzuerhalten, sodass das Material den Heiz- und Kühlprozess ohne Oxidation oder andere chemische Reaktionen durchlaufen kann.
Warum erfordert ein Prozess einen Inertatmosphärenofen?
Viele Wärmebehandlungsprozesse erfordern eine stark kontrollierte Atmosphäre, um das gewünschte Ergebnis zu erzielen. Sintern, Blankglühen und Karbonitrieren sind beispielsweise Verfahren zur Herstellung von Teilen für verschiedene Branchen. Diese Prozesse erfordern eine Atmosphäre, die stark kontrolliert wird, um ein erfolgreiches Ergebnis zu gewährleisten. Inerte Atmosphären, wie sie beispielsweise in einem Ofen mit inerter Atmosphäre erzeugt werden, sind erforderlich, um chemische Reaktionen wie Entkohlung oder Oxidation zu vermeiden, die sich negativ auf die Qualität und Leistung des Endprodukts auswirken könnten.
Die Bedeutung inerter Atmosphärengase
Inerte Atmosphärengase sind für die Schaffung der kontrollierten Umgebung, die für Sinter- und Glühprozesse erforderlich ist, unerlässlich. Stickstoff, Helium und Argon werden üblicherweise zur Erzeugung inerter Atmosphären verwendet, da sie chemisch stabil sind und eine geringe Reaktivität aufweisen. Durch die Verwendung dieser Gase können Forscher und Hersteller eine stabile, sauerstofffreie Umgebung schaffen, die eine präzise Kontrolle über das Erhitzen und Abkühlen von Materialien ermöglicht.
Zusammenfassend lässt sich sagen, dass ein Inertatmosphärenofen ein wichtiges Gerät für Forscher und Hersteller ist, die mit Hochtemperaturmaterialien arbeiten. Durch die Bereitstellung einer stabilen, sauerstofffreien Umgebung für Sinter- und Glühprozesse können Inertatmosphärenöfen dazu beitragen, bessere Ergebnisse und konsistentere Produktionsergebnisse zu erzielen.
Verwendung von Inertatmosphärenöfen zum Sintern und Glühen
Inertatmosphärenöfen werden häufig in Sinter- und Glühprozessen eingesetzt, um eine Umgebung zu schaffen, die frei von reaktiven Gasen ist. Durch die Verwendung von Inertgasen wie Argon oder Stickstoff entsteht eine stabile und gleichmäßige Atmosphäre, die die Wahrscheinlichkeit unerwünschter Reaktionen während des Sinter- oder Glühprozesses verringert.
Vorteile der Verwendung von Öfen mit Inertatmosphäre
Die Verwendung von Öfen mit Schutzgasatmosphäre bietet mehrere Vorteile. Einer der bedeutendsten Vorteile ist die verbesserte Produktqualität. Durch die Schaffung einer stabilen und gleichmäßigen Atmosphäre können Öfen mit inerter Atmosphäre dazu beitragen, qualitativ hochwertige Endprodukte mit weniger Fehlern herzustellen.
Ein weiterer Vorteil ist die erhöhte Produktionseffizienz. Inertatmosphärenöfen können dazu beitragen, die Verarbeitungszeit zu verkürzen und den Fertigungsdurchsatz zu verbessern. Dies wird durch die Minimierung des Nacharbeitsbedarfs und die Steigerung der Ausbeute an qualitativ hochwertigen Produkten erreicht.
Reduzierung von Verunreinigungen und Oxidation
Öfen mit inerter Atmosphäre können außerdem Kontamination und Oxidation minimieren, was einen erheblichen Einfluss auf die Endeigenschaften des Produkts haben kann. Die Verwendung einer kontrollierten Atmosphäre trägt dazu bei, die Wahrscheinlichkeit einer Kontamination durch externe Quellen zu verringern und verhindert außerdem die Oxidation des Produkts während des Sinter- oder Glühprozesses.
Vielseitigkeit der Materialien
Inertatmosphärenöfen können für eine Vielzahl von Materialien verwendet werden, darunter Metalle, Keramik und Verbundwerkstoffe, was sie zu einem unverzichtbaren Werkzeug für viele Branchen macht. Die Möglichkeit, diese Öfen für unterschiedliche Materialien zu verwenden, bietet Herstellern mehr Flexibilität bei der Produktgestaltung und -produktion.
Vorteile von Öfen mit kontrollierter Atmosphäre
Öfen mit kontrollierter Atmosphäre bieten Labortechnikern mehrere Vorteile und machen sie zu einem unverzichtbaren Werkzeug bei Sinter- und Glühprozessen.
Maßgeschneiderte Umgebung für spezifische Anwendungen
Einer der größten Vorteile von Öfen mit kontrollierter Atmosphäre ist die Möglichkeit, eine spezifische Umgebung zu schaffen, die auf eine bestimmte Anwendung zugeschnitten werden kann. Durch die Steuerung der Gaszusammensetzung, der Temperatur und des Drucks im Ofen können Labortechniker die chemischen Reaktionen beeinflussen, die beim Sintern und Glühen ablaufen, und so die Qualität und Konsistenz des Endprodukts verbessern.
Verhinderung von Oxidation
Öfen mit kontrollierter Atmosphäre können verwendet werden, um die Oxidation empfindlicher Materialien zu verhindern, indem Sauerstoff aus der Umgebung entfernt wird. Dies verringert das Kontaminationsrisiko und verbessert die Produktreinheit.
Hochtemperaturverarbeitung
Ein weiterer Vorteil von Öfen mit kontrollierter Atmosphäre ist ihre Fähigkeit, bei hohen Temperaturen zu arbeiten, was eine größere Flexibilität bei den zu verarbeitenden Materialien bietet. Diese Öfen werden häufig bei der Herstellung von Keramik, Metallen und Halbleitern eingesetzt, wo hohe Temperaturen erforderlich sind, um die gewünschten Eigenschaften zu erreichen.
Präzise Kontrolle für genaue und reproduzierbare Ergebnisse
Die präzise Steuerung, die Öfen mit kontrollierter Atmosphäre bieten, bedeutet, dass Labortechniker genauere und reproduzierbarere Ergebnisse erzielen können. Dies verringert das Fehlerrisiko und verbessert die Gesamtqualität ihrer Forschung.
Überlegen gegenüber Kasten- und Salzbadöfen
Öfen mit kontrollierter Atmosphäre haben inzwischen Kastenöfen (Packungsaufkohlung) und Salzbadöfen weitgehend verdrängt, da sie eine bessere Ofensteuerung, einen effizienteren Durchsatz und einen geringeren Arbeitsaufwand bieten. Sie bieten außerdem deutlich verbesserte Umweltbedingungen für den Betrieb, ohne dass es zu den ernsthaften Problemen einer Bodenverunreinigung mit giftigen Salzen (Cyaniden) und den Schwierigkeiten bei der Entsorgung von Abfallsalzen, kontaminierten Vorrichtungen und Vorrichtungen sowie Verpackungsaufkohlungsabfällen kommt.
Insgesamt machen die Vorteile von Öfen mit kontrollierter Atmosphäre sie zu einem unverzichtbaren Werkzeug für Labore, die in den Bereichen Materialwissenschaft, Chemie und Ingenieurwesen tätig sind.
Verbesserte Umweltbedingungen
Öfen mit kontrollierter Atmosphäre sollen eine Umgebung schaffen, in der Materialien präzise und ohne unerwünschte Kontamination erhitzt werden können. Einer der Hauptvorteile der Verwendung eines Ofens mit kontrollierter Atmosphäre sind die verbesserten Umgebungsbedingungen. Durch die Kontrolle der Atmosphäre im Ofen ist es möglich, die Menge an vorhandenem Sauerstoff und Feuchtigkeit zu reduzieren, was einen erheblichen Einfluss auf die Qualität des Endprodukts haben kann.
Reduzierter Sauerstoffgehalt
Durch die Reduzierung der während des Sinter- oder Glühprozesses vorhandenen Sauerstoffmenge kann eine Oxidation verhindert werden, die zu einem schwächeren und weniger haltbaren Endprodukt führen kann. Wenn der Sauerstoffgehalt hoch ist, kann er bei unterschiedlichen Temperaturen mit vielen chemischen Elementen reagieren und Oxidation verursachen. Mit einem Ofen mit kontrollierter Atmosphäre kann der Sauerstoffgehalt gesenkt werden, um dies zu verhindern. Stickstoff gilt als chemisch inertes Trägergas der Luft und wird häufig als Reduktionsgas verwendet, um die Oxidation von Materialien in Hochtemperaturöfen zu verhindern. Dieser Überlagerungsprozess wird mithilfe von Gaseinlässen wie Stickstoffdurchflussmessern und einer Auslassöffnung erreicht, um verbrauchtes Gas über einen Abzug oder eine externe Verteilerleitung aus der Kammer auszustoßen.
Reduzierter Feuchtigkeitsgehalt
Ebenso kann durch die Kontrolle der vorhandenen Feuchtigkeitsmenge die Bildung unerwünschter chemischer Verbindungen verhindert werden, die sich ebenfalls auf die Qualität des Endprodukts auswirken können. Feuchtigkeit kann während des Glühprozesses unerwünschte chemische Reaktionen hervorrufen, die die Qualität des Endprodukts beeinträchtigen können. Durch die Verwendung eines Ofens mit kontrollierter Atmosphäre kann der Feuchtigkeitsgehalt reduziert werden, wodurch sichergestellt wird, dass das Endprodukt von hoher Qualität ist.
Erhöhte Effizienz und Produktivität
Zusätzlich zu diesen Umweltvorteilen bieten Öfen mit kontrollierter Atmosphäre auch eine höhere Effizienz und Produktivität sowie eine größere Flexibilität und Kontrolle über den gesamten Sinter- oder Glühprozess. Durch die Verwendung eines Ofens mit kontrollierter Atmosphäre ist es möglich, eine Umgebung zu schaffen, die den Heizprozess begünstigt, was zu einer schnelleren und effizienteren Erwärmung führen kann. Dies wiederum kann dazu beitragen, die Produktivität zu steigern und die Kosten zu senken.
Bessere Ofensteuerung und effizienter Durchsatz
Öfen mit kontrollierter Atmosphäre (CAFs) bieten gegenüber herkömmlichen Öfen mehrere Vorteile, darunter eine bessere Kontrolle über die Ofenumgebung und einen effizienteren Durchsatz. CAFs sind für den Betrieb in Umgebungen mit kontrollierten Mengen an Sauerstoff, Stickstoff oder anderen Gasen konzipiert, die je nach den spezifischen Anforderungen des Prozesses angepasst werden können.
Präzise Kontrolle der Ofenumgebung
Einer der Hauptvorteile von CAFs ist ihre Fähigkeit, die Ofenumgebung präzise zu steuern. Dieses Maß an Kontrolle kann zu einer besseren Produktqualität führen, da es eine präzisere Kontrolle des Sinter- oder Glühprozesses ermöglicht. CAFs können in Umgebungen mit kontrollierten Mengen an Sauerstoff, Stickstoff oder anderen Gasen betrieben werden. Dieses Maß an Kontrolle kann zu einer besseren Produktqualität führen, da es eine präzisere Kontrolle des Sinter- oder Glühprozesses ermöglicht.
Verbesserte Effizienz
Ein weiterer Vorteil von CAFs ist ihre Fähigkeit, Materialien bei höheren Temperaturen als herkömmliche Öfen zu verarbeiten, was zu schnelleren Verarbeitungszeiten und einer höheren Effizienz führen kann. CAFs können Materialien häufig bei höheren Temperaturen verarbeiten als herkömmliche Öfen, was zu schnelleren Verarbeitungszeiten und einer höheren Effizienz führen kann. Dies ist besonders wichtig für Prozesse, die eine Hochtemperaturverarbeitung erfordern, wie zum Beispiel Sintern und Glühen.
Reduzierte Oxidation
CAFs haben auch die Fähigkeit, das Ausmaß der Oxidation zu reduzieren, die während des Sinter- oder Glühprozesses auftritt, was dazu beitragen kann, die Integrität des verarbeiteten Materials zu bewahren. Dies kann besonders wichtig für Materialien sein, die gegenüber Oxidation empfindlich sind, wie zum Beispiel bestimmte Metalle oder Keramiken.
Konsistente Qualität der Ausgabe
Die präzise Steuerung der Ofenumgebung in CAFs führt zu einer gleichbleibenden Qualität der Ergebnisse, die für Anwendungen in Forschung und Entwicklung sowie in der industriellen Fertigung von entscheidender Bedeutung ist. Die Möglichkeit, den Gehalt an Sauerstoff, Stickstoff oder anderen Gasen während des Sinter- oder Glühprozesses zu kontrollieren, stellt sicher, dass das Endprodukt den gewünschten Qualitätsstandards entspricht.
Abschluss
Zusammenfassend lässt sich sagen, dass CAFs gegenüber herkömmlichen Öfen für Sinter- und Glühprozesse eine Reihe von Vorteilen bieten. Sie sorgen für eine bessere Kontrolle der Ofenumgebung, eine verbesserte Effizienz, eine geringere Oxidation und eine gleichbleibende Qualität der Produktion. Diese Vorteile machen CAFs zur idealen Wahl für ein breites Anwendungsspektrum, von Forschung und Entwicklung bis hin zur industriellen Fertigung.
Zwei Hauptkategorien: Chargen- und Durchlauföfen
Öfen mit kontrollierter Atmosphäre sind unverzichtbare Laborgeräte für Sinter- und Glühprozesse in vielen Branchen. Es gibt zwei Hauptkategorien von Öfen mit kontrollierter Atmosphäre: Chargen- und Durchlauföfen.
Chargenöfen
Für kleine Produktmengen eignen sich Chargenöfen, bei denen das Material in Chargen in den Ofen geladen und für einen bestimmten Zeitraum auf die gewünschte Temperatur erhitzt wird. Der Chargenofen ist ein Einkammerofen, der als Charge beschickt, erhitzt und entladen wird. Temperatur, Gaszusammensetzung und Druck werden für den gesamten Batch-Prozess eingestellt. Der Chargenofen ist ideal für die Produktion und Forschung im kleinen Maßstab und eignet sich auch für Materialien, die für einen bestimmten Zeitraum eine bestimmte Temperatur und Atmosphäre benötigen.
Durchlauföfen
Andererseits eignen sich Durchlauföfen für große Produktmengen, die einen kontinuierlichen Materialfluss durch den Ofen erfordern. Bei Durchlauföfen wird das Material an einem Ende eingefüllt und über ein Fördersystem durch den Ofen transportiert. Das Fördersystem ist so konzipiert, dass ein kontinuierlicher Materialfluss durch den Ofen gewährleistet ist. Temperatur, Gaszusammensetzung und Druck werden während des gesamten Prozesses kontrolliert. Durchlauföfen sind ideal für die Massenproduktion und werden häufig in der Automobil-, Luft- und Raumfahrt- und Elektronikindustrie eingesetzt.
Sowohl Chargen- als auch Durchlauföfen bieten mehrere Vorteile. Die Öfen mit kontrollierter Atmosphäre können die Qualität des Endprodukts erheblich verbessern. Zu den Vorteilen der Verwendung dieser Öfen gehören eine geringere Oxidation, verbesserte Materialeigenschaften und eine höhere Produktausbeute. Öfen mit kontrollierter Atmosphäre können außerdem die Gleichmäßigkeit des Produkts verbessern, den Energieverbrauch senken und Verunreinigungen und Abfall minimieren.
Zusammenfassend lässt sich sagen, dass Öfen mit kontrollierter Atmosphäre in verschiedenen Branchen eine entscheidende Rolle spielen und eine Reihe von Vorteilen für Sinter- und Glühprozesse bieten. Die Wahl zwischen Chargen- und Durchlauföfen hängt von den spezifischen Anforderungen der Industrie oder des Labors ab. Der Chargenofen eignet sich für die Produktion und Forschung im kleinen Maßstab, während der Durchlaufofen ideal für die Produktion großer Stückzahlen ist. Beide Ofentypen sind darauf ausgelegt, eine kontrollierte Umgebung zu schaffen, die die Materialeigenschaften verbessert und die Oxidation minimiert.
Atmosphärenöfen von KINTEK
Atmosphärenöfen sind für Sinter- und Glühprozesse im Labor unerlässlich. KINTEK, ein führender Hersteller von Laborgeräten, bietet Atmosphärenöfen an, die eine präzise kontrollierte Umgebung für Sinter- und Glühprozesse bieten, um Ergebnisse höchster Qualität zu gewährleisten.
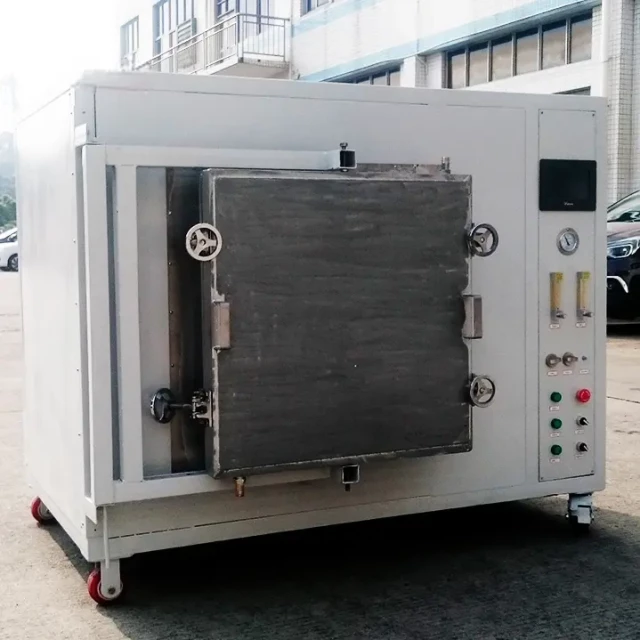
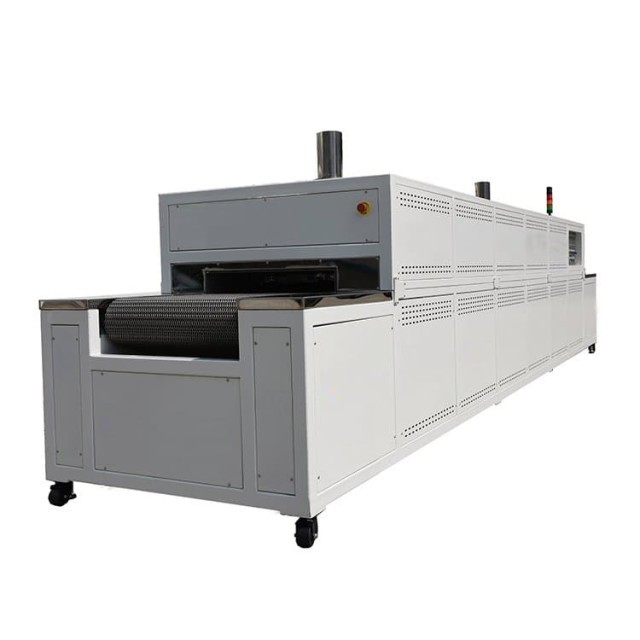
Merkmale der KINTEK-Atmosphärenöfen
Die Atmosphärenöfen von KINTEK sind so konzipiert, dass sie den individuellen Spezifikationen des Kunden entsprechen. Diese Öfen verfügen über eine Reihe von Heizzonengrößen und Arbeitstemperaturbereichen (1100 °C, 1300 °C und 1600 °C), was sie ideal für den Einsatz in einer Vielzahl von Anwendungen macht, von Metallurgie und Materialwissenschaften bis hin zu Halbleiterverarbeitung und Elektronik Herstellung.
Kontrollierte Atmosphäre
Atmosphärenöfen steuern die Umgebung, in der die Proben erhitzt werden, und schaffen so eine spezifische Atmosphäre, die die Endeigenschaften des zu verarbeitenden Materials erheblich beeinflussen kann. Die Atmosphärenöfen von KINTEK verfügen über mehrere patentierte Funktionen, die eine bessere Durchmischung ermöglichen, was zu einer verbesserten Wärme- und Stoffübertragung führt. Das Fehlen beweglicher Teile im Rohrhalterungssystem sorgt für ein einfaches, zuverlässiges und robustes Design, das die Skalierbarkeit verbessert. Darüber hinaus führt die Taumelwirkung des Produkts im Rohr zu einem hohen Grad an Temperaturgleichmäßigkeit und Gas-Feststoff-Kontakt, wodurch ein homogeneres Produkt entsteht, die Verarbeitungszeiten verkürzt und die Produktionsraten erhöht werden.
Prozessatmosphären
Die Atmosphärenöfen von KINTEK können eine Vielzahl von Prozessatmosphären aufnehmen. Zu den hervorragenden Dichtungsdesigns und dem Fokus des Unternehmens auf Atmosphärenkontrolle gehört die Systemintegration von Atmosphärenrückführungssystemen, Abgasreinigungssystemen und kontrollierter Atmosphärenmischung für eine maßgeschneiderte Prozesskontrolle. Zu diesen Atmosphären gehören brennbare und giftige Gase wie Wasserstoff, Stickstoff, Argon, Luft, Sauerstoff, Ethylen, Methan, CO2, CO und Chlorgas.
Anpassung
KINTEK betrachtet die Konstruktion eines Atmosphärenofens als komplettes System mit der Möglichkeit, Prozesssteuerungssysteme, Gasaufbereitung und -handhabung, schlüsselfertige Installation und vollständige Inbetriebnahme vor Ort zu integrieren. Das Unternehmen bietet auch maßgeschneiderte Hochtemperatur-Laboröfen an, die eine hervorragende Temperaturkontrolle und -gleichmäßigkeit sowie Energieeffizienz bieten. Diese Öfen können von einem Standardmodell abgeändert oder nach genauen Kundenspezifikationen gebaut werden.
Zusammenfassend lässt sich sagen, dass die Atmosphärenöfen von KINTEK eine ausgezeichnete Wahl für jedes Labor sind, das die Qualität und Konsistenz seiner Arbeit verbessern möchte. Diese Öfen bieten eine präzise kontrollierte Umgebung für Sinter- und Glühprozesse, reduzieren die Oxidation, kontrollieren die Phasenbildung und verbessern die Gesamtqualität und Konsistenz des Endprodukts.
Abschluss
Zusammenfassend lässt sich sagen, dass Öfen mit kontrollierter Atmosphäre aufgrund ihrer Fähigkeit, eine inerte Umgebung zu schaffen, die Oxidation verhindert, Verunreinigungen reduziert und die Qualität des Endprodukts verbessert, zu einem integralen Bestandteil von Sinter- und Glühprozessen geworden sind. Im Vergleich zu herkömmlichen Öfen bieten sie verbesserte Umgebungsbedingungen, eine bessere Ofensteuerung, einen effizienten Durchsatz und ein höheres Maß an Sicherheit. KINTEK bietet eine breite Palette von Atmosphärenöfen an, die auf die Anforderungen verschiedener Branchen zugeschnitten sind. Die Investition in einen Ofen mit kontrollierter Atmosphäre kann Unternehmen dabei helfen, Zeit zu sparen, Kosten zu senken und qualitativ hochwertige Produkte herzustellen, die den Industriestandards entsprechen.
Kontaktieren Sie uns für eine kostenlose Beratung
Die Produkte und Dienstleistungen von KINTEK LAB SOLUTION werden von Kunden auf der ganzen Welt anerkannt. Unsere Mitarbeiter helfen Ihnen gerne bei allen Fragen weiter. Kontaktieren Sie uns für eine kostenlose Beratung und sprechen Sie mit einem Produktspezialisten, um die am besten geeignete Lösung für Ihre Anwendungsanforderungen zu finden!