Einführung in die Dünnschichtabscheidung
Zweck und Verfahren
Die Dünnschichtabscheidung ist ein entscheidender Prozess in der Halbleiterherstellung, bei dem eine dünne Schicht im Nanomaßstab auf ein Substrat aufgebracht wird. Auf diesen ersten Schritt folgt eine Reihe sorgfältiger Prozesse, darunter wiederholtes Ätzen und Polieren, um mehrere übereinanderliegende Schichten zu erzeugen. Diese Schichten können entweder leitend oder isolierend sein und werden jeweils sorgfältig gemustert, um komplizierte Schaltkreisdesigns zu bilden.
Das Verfahren der Dünnschichtabscheidung ist für die Integration von Halbleiterkomponenten und Schaltkreisen in komplexe Chips unerlässlich. Jede abgeschiedene und strukturierte Schicht hat eine bestimmte Funktion innerhalb der gesamten Chiparchitektur und trägt zur Leistung, Zuverlässigkeit und Funktionalität des Chips bei. Die Präzision und Kontrolle von Dünnschichtabscheidungsprozessen sind unerlässlich, um sicherzustellen, dass diese Schichten die anspruchsvollen Standards erfüllen, die in modernen Halbleitergeräten erforderlich sind.
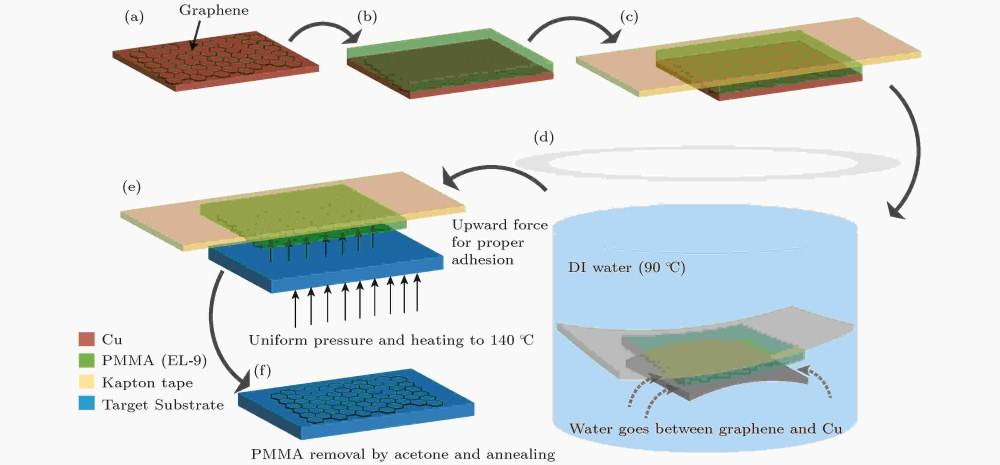
Im Wesentlichen geht es bei der Dünnschichtabscheidung nicht nur darum, Schichten zu erzeugen, sondern Schicht für Schicht die grundlegenden Elemente der Halbleitertechnologie aufzubauen, um die hochentwickelten und leistungsstarken Chips zu erhalten, die die heutigen elektronischen Geräte antreiben.
Chemische Gasphasenabscheidung (CVD)
Überblick und Merkmale
Die chemische Gasphasenabscheidung (Chemical Vapor Deposition, CVD) ist eine hochentwickelte Technik, bei der dünne Schichten durch die thermische Zersetzung und/oder Reaktion von Gasverbindungen gebildet werden. Diese Methode bietet eine Vielzahl von Vorteilen, die sie zu einem Eckpfeiler in der Halbleiterherstellung machen. Eine der Hauptstärken ist die Vielseitigkeit der Abscheidungsarten, die die Herstellung einer breiten Palette von Materialien mit spezifischen Eigenschaften ermöglicht. Diese Vielseitigkeit wird durch die Fähigkeit ergänzt, gleichmäßige Beschichtungen auf verschiedenen Substraten zu erzielen, was eine gleichbleibende Leistung und Zuverlässigkeit des Endprodukts gewährleistet.
Hohe Reinheit ist ein weiteres entscheidendes Merkmal von CVD-abgeschiedenen Schichten. Durch die kontrollierte Umgebung im CVD-Reaktor wird die Verunreinigung minimiert, was zu Schichten mit minimalen Verunreinigungen führt. Diese hohe Reinheit ist für die Leistung und Langlebigkeit von Halbleiterbauelementen von entscheidender Bedeutung, bei denen selbst Spuren von Verunreinigungen die Funktionalität erheblich beeinträchtigen können.
Darüber hinaus bietet CVD eine präzise Kontrolle über die Zusammensetzung der abgeschiedenen Schichten. Durch die sorgfältige Auswahl und Regulierung der Gasverbindungen und Reaktionsbedingungen können die Hersteller die Eigenschaften der Schichten auf die jeweiligen Anforderungen abstimmen. Dieses Maß an Kontrolle ist von unschätzbarem Wert für die Herstellung moderner Halbleiterbauelemente, bei denen präzise Materialeigenschaften für eine optimale Leistung entscheidend sind.
Eine bemerkenswerte Einschränkung der CVD-Technik ist jedoch, dass während des Abscheidungsprozesses hohe Temperaturen erforderlich sind. Diese hohen Temperaturen können die Art der verwendbaren Substrate einschränken und zusätzliche Kühl- und Wärmemanagementlösungen erforderlich machen. Trotz dieser Herausforderung machen die Vorteile der CVD in Bezug auf Vielseitigkeit, Gleichmäßigkeit, Reinheit und Kontrolle der Zusammensetzung das Verfahren zu einer unverzichtbaren Technik in der Halbleiterindustrie.
Stufen des CVD-Verfahrens
Das CVD-Verfahren (Chemical Vapor Deposition) ist ein mehrstufiges Verfahren, bei dem gasförmige Ausgangsstoffe in eine feste Schicht auf einem Substrat umgewandelt werden. Dieser Prozess ist entscheidend für die Herstellung dünner Schichten mit präziser Kontrolle über Zusammensetzung und Dicke, die für die Halbleiterherstellung unerlässlich sind.
-
Gasdiffusion auf dem Substrat: In der ersten Phase diffundieren die reaktiven Gase zum Substrat. Diese Diffusion erfolgt aufgrund von Konzentrationsgradienten, bei denen sich die Gase von Bereichen mit höherer Konzentration zu Bereichen mit niedrigerer Konzentration bewegen. Die Effizienz dieses Schritts wird durch Faktoren wie Temperatur, Druck und die Konstruktion der Reaktorkammer beeinflusst.
-
Adsorption an der Substratoberfläche: Sobald die reaktiven Gase das Substrat erreichen, werden sie adsorbiert, d. h. sie haften an der Oberfläche des Substrats. Die Adsorption kann physikalisch sein, wenn schwache Van-der-Waals-Kräfte im Spiel sind, oder chemisch, wenn sich kovalente Bindungen bilden. Die Art der Adsorption hat erhebliche Auswirkungen auf die nachfolgenden chemischen Reaktionen und die Qualität des fertigen Films.
-
Chemische Reaktion zur Bildung einer festen Ablagerung: Die dritte Stufe ist die kritischste und umfasst eine Reihe von chemischen Reaktionen, die die adsorbierten Gase in einen festen Film umwandeln. Bei diesen Reaktionen kann es sich um thermische Zersetzung handeln, bei der das Gas in feste und gasförmige Produkte zerfällt, oder um chemische Synthese, bei der zwei oder mehr Gase zu einem festen Produkt reagieren. Die gebildeten festen Ablagerungen sind in der Regel dünn, gleichmäßig und von hoher Reinheit und erfüllen die strengen Anforderungen der Halbleiterherstellung.
Jeder dieser Schritte wird genauestens kontrolliert, um die Abscheidung eines hochwertigen Dünnfilms zu gewährleisten. Das Zusammenspiel von Gasdiffusion, Adsorption und chemischen Reaktionen bestimmt die endgültigen Eigenschaften der abgeschiedenen Schicht, einschließlich ihrer Dicke, Gleichmäßigkeit und Zusammensetzung.
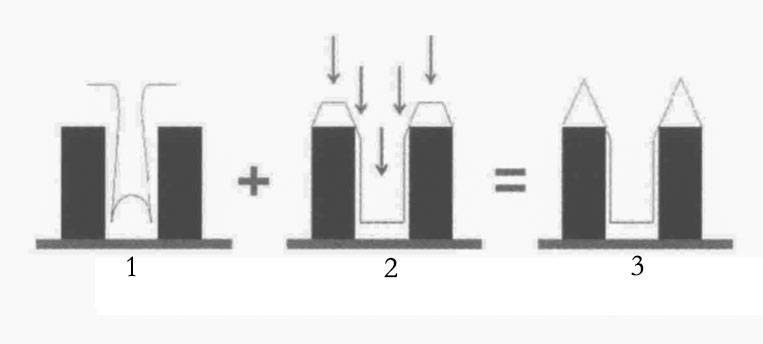
Gängige CVD-Reaktionen
Im Bereich der chemischen Gasphasenabscheidung (CVD) sind mehrere grundlegende Reaktionen für die Bildung verschiedener dünner Schichten von zentraler Bedeutung. Diese Reaktionen können grob in drei Haupttypen eingeteilt werden: thermische Zersetzung, chemische Synthese und chemische Übertragung. Jede dieser Reaktionen spielt eine entscheidende Rolle im Abscheidungsprozess und ermöglicht die Herstellung verschiedener Materialien mit spezifischen Eigenschaften.
Thermische Zersetzung Bei der thermischen Zersetzung wird eine Verbindung durch Wärmeeinwirkung zersetzt, wobei sich ein fester Film bildet. Die Abscheidung von Polysilizium beispielsweise beruht häufig auf der thermischen Zersetzung von Silan (SiH₄) bei erhöhten Temperaturen. Dieser Prozess kann wie folgt dargestellt werden:
[ \text{SiH}_4 \xrightarrow{\Delta} \text{Si} + 2\text{H}_2 ]
Chemische Synthese liegt vor, wenn sich zwei oder mehr Reaktionspartner zu einer neuen Verbindung verbinden, die sich dann als fester Film ablagert. Ein Beispiel hierfür ist die Bildung von Siliziumdioxid (SiO₂) durch die Reaktion von Silan mit Sauerstoff:
[ \text{SiH}_4 + 2\text{O}_2 \rightarrow \text{SiO}_2 + 2\text{H}_2\text{O} ]
Chemischer Transfer beinhaltet die Übertragung einer chemischen Spezies von einer Phase in eine andere, typischerweise von einem gasförmigen Vorläufer zu einem festen Film. Ein bemerkenswertes Beispiel ist die Abscheidung von Siliziumnitrid (Si₃N₄), die durch die Reaktion von Silan mit Ammoniak erreicht werden kann:
[ 3\text{SiH}_4 + 4\text{NH}_3 \rightarrow \text{Si}_3\text{N}_4 + 12\text{H}_2 ]
Diese Reaktionen verdeutlichen nicht nur die Vielseitigkeit der CVD, sondern auch ihre Fähigkeit, hochreine, gleichmäßige Schichten mit kontrollierter Zusammensetzung herzustellen. Die Wahl des Reaktionstyps und der Vorläufermaterialien ist ausschlaggebend für die Eigenschaften der abgeschiedenen Schichten, was die CVD zu einer äußerst anpassungsfähigen Technik für die Halbleiterherstellung macht.
Arten von CVD-Anlagen
Für die Abscheidung von Dünnschichten werden verschiedene CVD-Reaktoren eingesetzt, die jeweils für die Optimierung bestimmter Prozessparameter und Materialeigenschaften ausgelegt sind. Die Reaktoren lassen sich anhand ihrer Betriebsbedingungen und der von ihnen verwendeten Mechanismen in verschiedene Kategorien einteilen.
-
CVD bei Atmosphärendruck (APCVD): Dieser CVD-Typ arbeitet bei Atmosphärendruck und eignet sich aufgrund seiner Einfachheit und Effizienz für die Produktion in großem Maßstab. Der hohe Druck kann jedoch zu einer ungleichmäßigen Schichtdicke und Qualität führen.
-
Niederdruck-CVD (LPCVD): Durch die Reduzierung des Drucks verbessert die LPCVD die Gleichmäßigkeit und Qualität der abgeschiedenen Schichten. Diese Methode wird häufig für die Abscheidung von Siliziumdioxid- und Siliziumnitridschichten in der Halbleiterherstellung verwendet.
-
Ultrahochvakuum-CVD (UHVCVD): Das UHVCVD-Verfahren arbeitet unter extrem niedrigem Druck und gewährleistet höchste Reinheit und Gleichmäßigkeit der abgeschiedenen Schichten. Dieses Verfahren eignet sich besonders für Forschungs- und Entwicklungsanwendungen, bei denen es auf Präzision ankommt.
-
Laser-CVD: Bei dieser Technik wird das Substrat mit einem Laser lokal erhitzt, was eine genaue Kontrolle des Abscheidungsprozesses ermöglicht. Laser-CVD ist vorteilhaft für die Herstellung qualitativ hochwertiger Schichten auf empfindlichen Substraten, ohne dabei thermische Schäden zu verursachen.
-
Metall-organische CVD (MOCVD): Bei der MOCVD werden metallorganische Grundstoffe verwendet, um komplexe Schichten abzuscheiden, wie sie beispielsweise in optoelektronischen Geräten verwendet werden. Diese Methode ist sehr vielseitig und ermöglicht die Herstellung von Schichten mit komplizierten Zusammensetzungen.
-
Plasmaunterstützte CVD (PECVD): Durch die Einbeziehung von Plasma in den Prozess reduziert PECVD die erforderliche Abscheidungstemperatur und eignet sich daher für temperaturempfindliche Materialien. Diese Methode wird häufig für die Abscheidung dielektrischer Schichten in Halbleiterbauelementen verwendet.
Jeder CVD-Reaktortyp bietet einzigartige Vorteile und wird je nach den spezifischen Anforderungen des Materials und der Anwendung ausgewählt.
Physikalische Gasphasenabscheidung (PVD)
Überblick und Grundsätze
Die physikalische Gasphasenabscheidung (PVD) ist ein hochentwickeltes Verfahren, bei dem Materialien unter sorgfältig kontrollierten Vakuumbedingungen verdampft werden. Mit dieser Technik lassen sich dünne Schichten mit spezifischen Funktionalitäten abscheiden, was sie zu einem Eckpfeiler in verschiedenen High-Tech-Industrien macht. Das PVD-Verfahren nutzt die Vakuumumgebung, um Verunreinigungen zu beseitigen, und stellt sicher, dass die entstehenden Schichten von außergewöhnlicher Qualität sind.
Die Vielseitigkeit des PVD-Verfahrens liegt in seiner Fähigkeit, eine breite Palette von Materialien und Filmtypen zu verarbeiten. Ganz gleich, ob es sich um Metalle, Keramik oder Verbundwerkstoffe handelt, PVD kann sie mit Präzision abscheiden. Diese Anpassungsfähigkeit ist in der Halbleiterfertigung von entscheidender Bedeutung, wo die Nachfrage nach leistungsstarken, zuverlässigen und gleichmäßigen Dünnschichten von größter Bedeutung ist. Das Verfahren gewährleistet nicht nur eine hervorragende Schichtqualität, sondern ermöglicht auch die Herstellung von Schichten mit maßgeschneiderten Eigenschaften, wie Leitfähigkeit, Reflexionsvermögen und Härte.
Im Wesentlichen zeichnet sich PVD durch seine Fähigkeit aus, dünne Schichten herzustellen, die nicht nur vielseitig, sondern auch von hervorragender Qualität sind, was es zu einem unverzichtbaren Werkzeug im Arsenal der modernen Halbleiterherstellung macht.
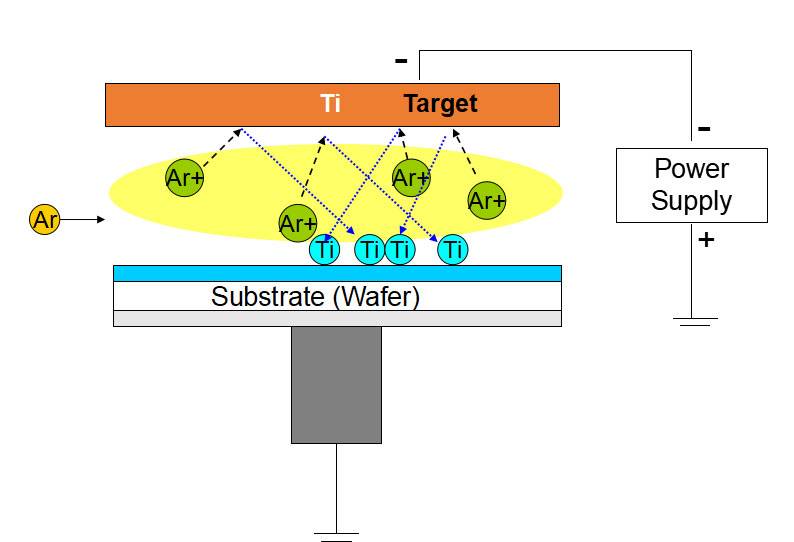
Prozess-Schritte
Das PVD-Verfahren (Physical Vapor Deposition) ist eine sorgfältige Abfolge von Schritten, die eine präzise Abscheidung von Dünnschichten auf Substraten gewährleisten. Dieser Prozess beginnt mit der Verdampfung des Beschichtungsmaterials, einem kritischen Schritt, bei dem das Material unter Vakuumbedingungen bis zu seinem Siedepunkt erhitzt wird. Durch diese Erhitzung geht das Material von einem festen oder flüssigen in einen gasförmigen Zustand über und zerfällt in seine einzelnen Atome, Moleküle oder Ionen.
Sobald sie verdampft sind, durchlaufen diese Atome, Moleküle oder Ionen eine kontrollierte Migrationsphase. Diese Migration wird durch die Vakuumumgebung erleichtert, die Kollisionen minimiert und es den Teilchen ermöglicht, sich auf einem geraden Weg zum Substrat zu bewegen. Die Vakuumbedingungen sorgen auch dafür, dass die Teilchen ihre hohen Energieniveaus beibehalten, was für eine effektive Abscheidung unerlässlich ist.
Schließlich erreichen die Partikel das Substrat und beginnen sich abzuscheiden, wobei sich ein dünner Film bildet. Dieser Abscheidungsprozess wird von mehreren Faktoren beeinflusst, unter anderem von der Energie und dem Einfallswinkel der Partikel, den Oberflächeneigenschaften des Substrats und dem Vakuumdruck. Das Ergebnis ist ein gleichmäßiger und dichter Film, der fest auf dem Substrat haftet und die gewünschten Funktionalitäten und Eigenschaften aufweist.
Schritt | Beschreibung |
---|---|
Verdampfung | Erhitzen des Beschichtungsmaterials bis zu seinem Siedepunkt unter Vakuum, um es in ein Gas umzuwandeln. |
Wanderung | Kontrollierte Bewegung von Atomen/Molekülen/Ionen durch das Vakuum zum Substrat. |
Abscheidung | Bildung eines dünnen Films auf dem Substrat durch Anhaften der hochenergetischen Teilchen an der Oberfläche. |
Jeder dieser Schritte ist entscheidend für die erfolgreiche Anwendung von PVD in der Halbleiterherstellung und bietet eine vielseitige und hochwertige Methode für die Abscheidung dünner Schichten.
Anwendungen und Vorteile
Die physikalische Gasphasenabscheidung (Physical Vapor Deposition, PVD) wird in einer Vielzahl von Branchen eingesetzt, vor allem wegen ihrer Umweltfreundlichkeit und der hohen Qualität der erzeugten Schichten. Im Gegensatz zu anderen Abscheidetechniken, bei denen schädliche Chemikalien oder energiereiche Prozesse zum Einsatz kommen können, arbeitet PVD unter Vakuumbedingungen, wodurch sichergestellt wird, dass der Abscheidungsprozess frei von Schadstoffen ist. Dies macht es zu einer idealen Wahl für Branchen, in denen die Einhaltung von Umweltvorschriften ein entscheidender Faktor ist.
Eines der herausragenden Merkmale des PVD-Verfahrens ist die Gleichmäßigkeit und Dichte der erzeugten Schichten. Das Verfahren führt zu Schichten, die in ihrer Dicke und Struktur sehr gleichmäßig sind, was für Anwendungen, die eine genaue Kontrolle der Materialeigenschaften erfordern, von entscheidender Bedeutung ist. Diese Gleichmäßigkeit wird durch die kontrollierte Verdampfung und Abscheidung des Materials erreicht, wodurch sichergestellt wird, dass die Folie genau den gewünschten Spezifikationen entspricht.
Darüber hinaus weisen PVD-Folien eine starke Bindung mit den Substraten auf, auf die sie aufgebracht werden. Diese starke Haftung ist das Ergebnis des direkten Abscheidungsprozesses, bei dem das verdampfte Material kondensiert und sich chemisch mit der Substratoberfläche verbindet. Diese starke Bindung erhöht nicht nur die Haltbarkeit der Folien, sondern sorgt auch dafür, dass sie unter verschiedenen Betriebsbedingungen intakt bleiben. Dadurch eignen sich PVD-Folien für Anwendungen, bei denen langfristige Stabilität und Zuverlässigkeit gefragt sind.
Vorteil | Beschreibung |
---|---|
Verschmutzungsfreie Natur | Arbeitet unter Vakuumbedingungen, so dass während des Prozesses keine schädlichen Emissionen entstehen. |
Gleichmäßige und dichte Schichten | Produziert hochgradig gleichmäßige Filme mit präziser Dicke und Struktur. |
Starke Bindung mit Substraten | Sorgt für eine robuste Haftung, die die Haltbarkeit und Langzeitstabilität verbessert. |
Zusammenfassend lässt sich sagen, dass die Kombination dieser Vorteile PVD zu einer bevorzugten Wahl für Branchen macht, die von Elektronik und Optik bis hin zu Luft- und Raumfahrt und Automobilbau reichen und in denen die Qualität und Zuverlässigkeit dünner Schichten von größter Bedeutung sind.
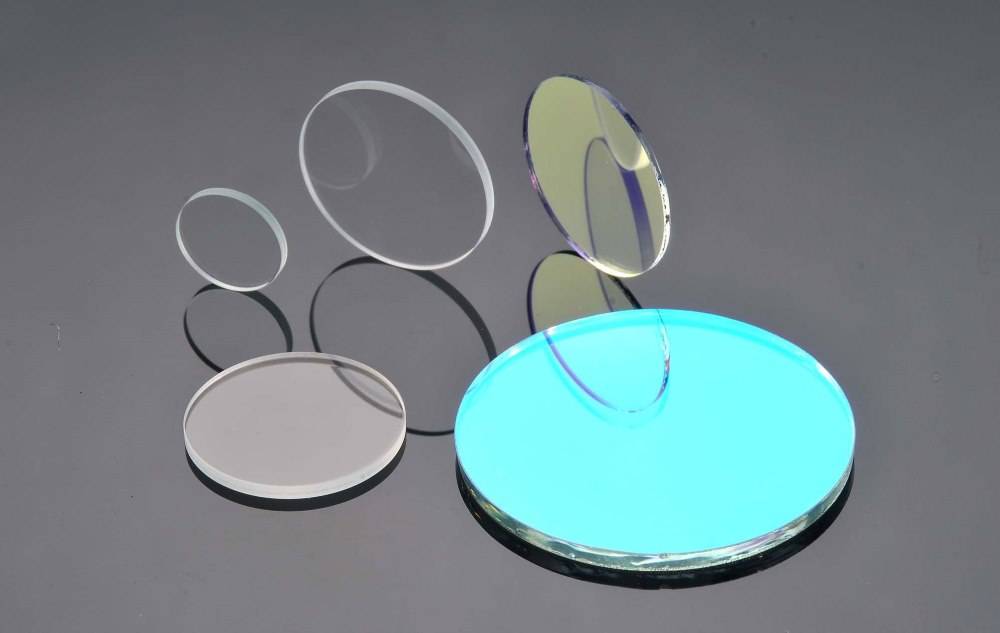
Methoden der PVD
Die physikalische Gasphasenabscheidung (Physical Vapor Deposition, PVD) umfasst mehrere hochentwickelte Verfahren zur Abscheidung dünner Schichten mit präzisen Funktionalitäten unter Vakuumbedingungen. Diese Verfahren sind für verschiedene industrielle Anwendungen von zentraler Bedeutung, da sie qualitativ hochwertige, gleichmäßige und dicht gebundene Schichten erzeugen können.
Zu den wichtigsten PVD-Verfahren gehören:
-
Vakuum-Dünnfilmbeschichtung: Bei diesem Verfahren wird ein Material in einer Vakuumkammer verdampft und der Dampf kondensiert auf einem Substrat. Das Verfahren gewährleistet eine minimale Verunreinigung und eine hervorragende Kontrolle über die Schichtdicke und Gleichmäßigkeit.
-
Sputtering PVD: Beim Sputtern wird ein Zielmaterial mit hochenergetischen Teilchen (Ionen) beschossen, um Atome abzulösen, die sich dann auf einem Substrat ablagern. Diese Methode eignet sich besonders gut für die Abscheidung einer breiten Palette von Materialien, darunter Metalle, Legierungen und Verbindungen.
-
Ionen-Beschichtung: Bei dieser Technik werden Ionen auf ein Substrat geschleudert, um die Haftung und die Dichte des abgeschiedenen Films zu erhöhen. Die Ionenbeschichtung ist für ihre Fähigkeit bekannt, stark haftende und dauerhafte Beschichtungen zu erzeugen, was sie ideal für Anwendungen macht, die einen robusten Schutz erfordern.
Jedes dieser Verfahren bietet einzigartige Vorteile und eignet sich daher für unterschiedliche Anwendungen in der Halbleiterfertigung und darüber hinaus.
Kontaktieren Sie uns für eine kostenlose Beratung
Die Produkte und Dienstleistungen von KINTEK LAB SOLUTION werden von Kunden auf der ganzen Welt anerkannt. Unsere Mitarbeiter helfen Ihnen gerne bei allen Fragen weiter. Kontaktieren Sie uns für eine kostenlose Beratung und sprechen Sie mit einem Produktspezialisten, um die am besten geeignete Lösung für Ihre Anwendungsanforderungen zu finden!