Inhaltsübersicht
Einführung: Vakuum-Induktions-Schmelzofen
Vakuum-Induktions-Schmelzöfen (VIM-Öfen) sind Spezialanlagen, die Vakuum und Induktionserwärmung nutzen, um Metalle und Legierungen mit außergewöhnlicher Präzision und Reinheit zu veredeln. Die VIM-Technologie bietet im Vergleich zu herkömmlichen Schmelzverfahren erhebliche Vorteile, u. a. die Möglichkeit, Oxidation und Verunreinigungen zu verhindern und so die Herstellung hochwertiger Materialien zu gewährleisten. Dieser umfassende Leitfaden befasst sich mit dem Prinzip, den Vorteilen, den Komponenten und den verschiedenen Anwendungen von VIM-Öfen und hebt ihre entscheidende Rolle in Branchen hervor, die Hochleistungswerkstoffe und eine präzise Kontrolle der Legierungszusammensetzung benötigen.
Prinzip der Funktionsweise
Mittelfrequenz-Induktionserwärmung
Die Mittelfrequenz-Induktionserwärmung ist ein Verfahren, bei dem ein elektromagnetisches Wechselfeld verwendet wird, um Wärme in einem leitfähigen Material zu erzeugen. Bei Vakuum-Induktionsschmelzöfen umgibt eine Induktionsspule den Tiegel, der das zu schmelzende Metall oder die Legierung enthält. Wenn ein Wechselstrom durch die Spule fließt, erzeugt er ein Magnetfeld, das im Metall Wirbelströme induziert. Diese Wirbelströme bewirken, dass sich das Metall schnell erhitzt und schmilzt.
Die Frequenz des in Mittelfrequenz-Induktionsöfen verwendeten Wechselstroms liegt in der Regel zwischen 1 kHz und 10 kHz. Dieser Frequenzbereich ist hoch genug, um genügend Wirbelströme für eine effiziente Erwärmung zu erzeugen, aber niedrig genug, um Energieverluste durch den Skin-Effekt zu minimieren.
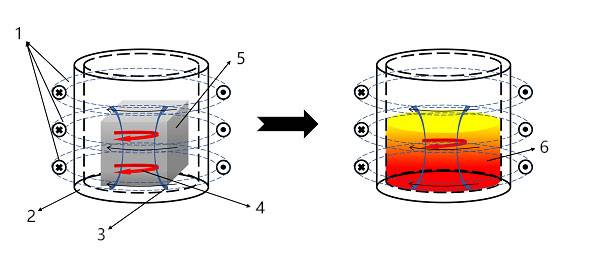
Die Rolle der Vakuumumgebung
Die Vakuumumgebung in einem Vakuum-Induktionsschmelzofen ist wichtig, um Oxidation und Verunreinigung des geschmolzenen Metalls zu verhindern. Oxidation tritt auf, wenn das geschmolzene Metall mit dem Sauerstoff der Atmosphäre reagiert und Metalloxide bildet, die die Eigenschaften des Materials beeinträchtigen können. Ebenso kann eine Verunreinigung auftreten, wenn das geschmolzene Metall mit Verunreinigungen in der Atmosphäre in Kontakt kommt.
Durch die Schaffung einer Vakuumumgebung verhindert der Ofen diese Reaktionen. Durch das Vakuum können außerdem gelöste Gase aus dem geschmolzenen Metall entfernt werden, was dessen Eigenschaften weiter verbessern kann.
Insgesamt bietet die Kombination aus Mittelfrequenz-Induktionserwärmung und einer Vakuumumgebung eine kontrollierte und effiziente Methode zum Schmelzen von Metallen und Legierungen, die zu hochreinen und hochwertigen Materialien führt.
Vorteile des Vakuum-Induktionsschmelzens
Hohe Reinheit und Qualität
Das Vakuum-Induktionsschmelzen (VIM) bietet höchste Reinheit und Qualität der geschmolzenen Materialien. Die Vakuumumgebung verhindert die Verunreinigung durch Sauerstoff, Stickstoff und andere atmosphärische Gase. Das Ergebnis ist eine sauberere, homogenere Schmelze ohne schädliche Einschlüsse und Verunreinigungen, die die mechanischen Eigenschaften beeinträchtigen könnten.
Präzise Temperaturkontrolle
Das VIM ermöglicht eine präzise Temperaturregelung während des Schmelzprozesses. Das Induktionserwärmungssystem gewährleistet konsistente und wiederholbare Ergebnisse, die für die Herstellung von Materialien mit spezifischen Eigenschaften und Zusammensetzungen entscheidend sind.
Vielseitige Materialkompatibilität
VIM-Öfen können eine breite Palette von Materialien verarbeiten, darunter Metalle, Legierungen und sogar Keramik. Dank dieser Vielseitigkeit eignen sie sich für verschiedene Anwendungen, von Komponenten für die Luft- und Raumfahrt bis hin zu Hochtemperaturlegierungen und Magnetwerkstoffen.
Energie-Effizienz
Das Induktionserwärmungssystem in VIM-Öfen ist äußerst energieeffizient. Dadurch werden die Betriebskosten gesenkt und die Auswirkungen auf die Umwelt minimiert.
Kompakte Bauweise
VIM-Öfen sind im Vergleich zu anderen Schmelzverfahren relativ kompakt. Dadurch eignen sie sich für Umgebungen mit begrenztem Platzangebot oder für mobile Anwendungen.
Einfacher Betrieb
VIM-Öfen sind auf einfache Bedienung ausgelegt und verfügen über intuitive Steuerungen und automatische Funktionen, die den Betrieb vereinfachen.
Sicherheitsmerkmale
VIM-Öfen sind mit Sicherheitsfunktionen wie Übertemperaturschutz und Notabschaltmechanismen ausgestattet, um einen sicheren Betrieb zu gewährleisten.
Weitere Vorteile
- Vakuum-Umgebung: Verhindert Oxidation und Entgasung.
- Hochtemperaturfähigkeit: Geeignet zum Schmelzen von Legierungen mit hohem Schmelzpunkt.
- Elektromagnetisches Rühren: Minimiert die Elemententmischung während des Schmelzens.
- Entfernung von flüchtigen Spurenelementen: Schädliche Elemente wie Antimon und Wismut können durch Kontrolle der Vakuumumgebung entfernt werden.
Komponenten eines Vakuum-Induktionsschmelzofens
Ofenkörper
- Wassergekühlte Zwischenschicht zur Aufrechterhaltung niedriger Oberflächentemperaturen
- Seitentür für leichten Zugang (optional)
- Legierungszuführung und Beobachtungsfenster an der Ofenabdeckung
Induktor
- Spiralförmige Spule aus dickwandigen Kupferrohren
- Keramische Beschichtung für Isolierung und längere Lebensdauer
Mechanismus zum Kippen des Ofens
- Manuelle, elektrische oder hydraulische Optionen
- 105-Grad-Kippwinkel nach vorne und 10-Grad-Kippwinkel nach hinten
- Einstellbare Kippgeschwindigkeit
Vakuum-System
- Besteht aus mechanischer Pumpe, Roots-Pumpe, Diffusionspumpe (oder Booster-Diffusionspumpe), Vakuumventil, elastischer Dämpfungsmanschette und Vakuumrohrleitung
- Wird entsprechend den Eigenschaften und dem Verfahren der zu schmelzenden Materialien konfiguriert
Mittelfrequenz-Stromversorgung
- IGBT-Mittelfrequenz-Netzteil
- Maximale Temperatur: 2000°C
Elektrische Steuerung
- Touchscreen-Steuerung mit PLC
- Vakuummessgerät, Temperaturmessgerät, Bedientasten, Kontrollleuchten
- Steuerungen für Pneumatiksystem, Vakuumsystem, Anheben des Ofendeckels und Kippen des Ofens
Sicherheitsmerkmale
- Präzise Temperaturregelung
- Vakuumumgebung verhindert Oxidation und Entgasung
- Elektromagnetisches Rühren verhindert die Entmischung von Elementen
- Entfernung von schädlichen Spurenelementen
Anwendungen von Vakuum-Induktionsschmelzöfen
Vakuum-Induktionsschmelzöfen sind in verschiedenen Forschungs- und Produktionsbereichen weit verbreitet, darunter
Guss von Luft- und Raumfahrtkomponenten Vakuum-Induktionsschmelzöfen werden zum Gießen von Bauteilen für die Luft- und Raumfahrt verwendet, da sie in der Lage sind, hochreine, homogene Metallblöcke herzustellen. Diese Blöcke werden dann zur Herstellung wichtiger Komponenten für Flugzeuge, Raketen und Satelliten verwendet.
Komplexe Ventile für extreme Bedingungen In diesen Öfen werden komplexe Ventile hergestellt, die extremen Bedingungen in Branchen wie der Öl- und Gasindustrie, der Luft- und Raumfahrt und der chemischen Verarbeitung standhalten müssen. Die Vakuumumgebung gewährleistet die Herstellung von hochwertigen Ventilen mit präzisen Abmessungen und Korrosionsbeständigkeit.
Veredelung hochreiner Metalle und Legierungen Vakuum-Induktionsschmelzöfen spielen eine entscheidende Rolle beim Raffinieren von Metallen und Legierungen, um Verunreinigungen zu entfernen und einen hohen Reinheitsgrad zu erreichen. Dieser Prozess ist für Anwendungen in Branchen wie der Elektronik, der Medizintechnik und der Luft- und Raumfahrt unerlässlich.
Herstellung von Elektroden für das Umschmelzen Vakuum-Induktionsschmelzöfen werden zur Herstellung von Elektroden für Umschmelzprozesse verwendet, insbesondere für die Produktion von hochwertigem Stahl und Superlegierungen. Die Elektroden werden in einer Vakuumumgebung geschmolzen, wodurch hochreines Material mit minimaler Verunreinigung entsteht.
Herstellung von Nickel und Spezialstahl Diese Öfen werden häufig bei der Herstellung von Nickel und Spezialstahl eingesetzt, da sich die Zusammensetzung und die Eigenschaften des geschmolzenen Metalls genau steuern lassen. Die Vakuumumgebung verhindert Oxidation und Verunreinigung und gewährleistet die Herstellung hochwertiger Legierungen.
Herstellung von Präzisionslegierungen Vakuum-Induktionsschmelzöfen sind unverzichtbar für die Herstellung von Präzisionslegierungen, die in verschiedenen Branchen wie der Luft- und Raumfahrt, der Elektronik und der Medizintechnik verwendet werden. Diese Legierungen erfordern eine präzise Kontrolle der Zusammensetzung und der Eigenschaften, was durch das Vakuuminduktionsschmelzen erreicht werden kann.
Verarbeitung von Aktivmetallen Aktivmetalle wie Titan und Zirkonium sind hochreaktiv und erfordern spezielle Schmelztechniken. Vakuum-Induktionsschmelzöfen bieten eine kontrollierte Umgebung, die Oxidation und Verunreinigung verhindert und so eine sichere und effiziente Verarbeitung dieser Metalle ermöglicht.
Entwicklung von Hochtemperaturlegierungen Vakuum-Induktionsschmelzöfen werden für die Entwicklung und Herstellung von Hochtemperaturlegierungen für Anwendungen in der Luft- und Raumfahrt, der Energieerzeugung und anderen Branchen eingesetzt. Diese Legierungen erfordern eine präzise Kontrolle der Zusammensetzung und der Eigenschaften, um extremen Temperaturen und rauen Umgebungen standzuhalten.
Herstellung von Magnetmaterial Vakuum-Induktionsschmelzöfen werden zur Herstellung von Magnetwerkstoffen wie Neodym-Magneten und Samarium-Kobalt-Magneten eingesetzt. Die Vakuumumgebung gewährleistet die Herstellung von hochreinen Materialien mit den gewünschten magnetischen Eigenschaften.
Sicherheitsvorteile des Vakuum-Induktionsschmelzens
Vakuum-Induktionsschmelzöfen bieten zahlreiche Sicherheitsvorteile gegenüber herkömmlichen Schmelzverfahren und sind daher die bevorzugte Wahl für verschiedene industrielle Anwendungen. Zu diesen Vorteilen gehören:
-
Präzise Kontrolle der Legierungszusammensetzung: Die Möglichkeit, die Atmosphäre in der Vakuumkammer präzise zu steuern, ermöglicht eine genaue und gleichmäßige Legierung. Dies ist entscheidend für die Herstellung von Hochleistungswerkstoffen mit spezifischen Eigenschaften.
-
Hemmung von nichtmetallischen Oxideinschlüssen: Die Vakuumumgebung hemmt die Bildung von nichtmetallischen Oxideinschlüssen, die die Qualität der Gussteile erheblich beeinträchtigen können. Das Ergebnis sind hochwertige Gussteile mit verbesserter Festigkeit und Haltbarkeit.
-
Elektromagnetisches Rühren: Elektromagnetisches Rühren ist ein einzigartiges Merkmal von Vakuum-Induktionsschmelzöfen, das die Entmischung von Elementen beim Schmelzen von Legierungen verhindert. Dies gewährleistet eine homogene Schmelze und verbessert die Gesamtqualität des Materials.
-
Beseitigung schädlicher flüchtiger Spurenelemente: Beim Vakuuminduktionsschmelzen können schädliche flüchtige Spurenelemente, wie Antimon, Tellur und Selen, durch kontrollierte Verdampfung selektiv entfernt werden. Dieser Prozess reinigt das geschmolzene Metall und verbessert die Eigenschaften des Materials.
Kontaktieren Sie uns für eine kostenlose Beratung
Die Produkte und Dienstleistungen von KINTEK LAB SOLUTION werden von Kunden auf der ganzen Welt anerkannt. Unsere Mitarbeiter helfen Ihnen gerne bei allen Fragen weiter. Kontaktieren Sie uns für eine kostenlose Beratung und sprechen Sie mit einem Produktspezialisten, um die am besten geeignete Lösung für Ihre Anwendungsanforderungen zu finden!