Die Wärmebehandlung hat einen erheblichen Einfluss auf die Oberflächenrauheit metallischer Werkstoffe, indem sie deren Mikrostruktur und mechanischen Eigenschaften verändert. Bei diesem Prozess werden Metalle unter kontrollierten Bedingungen erhitzt und abgekühlt, was zu Veränderungen der Härte, Korngröße und Eigenspannungen führen kann. Diese Veränderungen wirken sich wiederum auf die Oberflächenrauheit aus. Beispielsweise können Prozesse wie Glühen die Oberflächenrauheit verringern, indem sie das Material erweichen und innere Spannungen reduzieren, während Härtebehandlungen die Rauheit aufgrund der Bildung härterer, spröderer Phasen erhöhen können. Die Abkühlgeschwindigkeit, die Temperatur und die spezifische Wärmebehandlungsmethode spielen alle eine entscheidende Rolle bei der Bestimmung der endgültigen Oberflächenrauheit.
Wichtige Punkte erklärt:
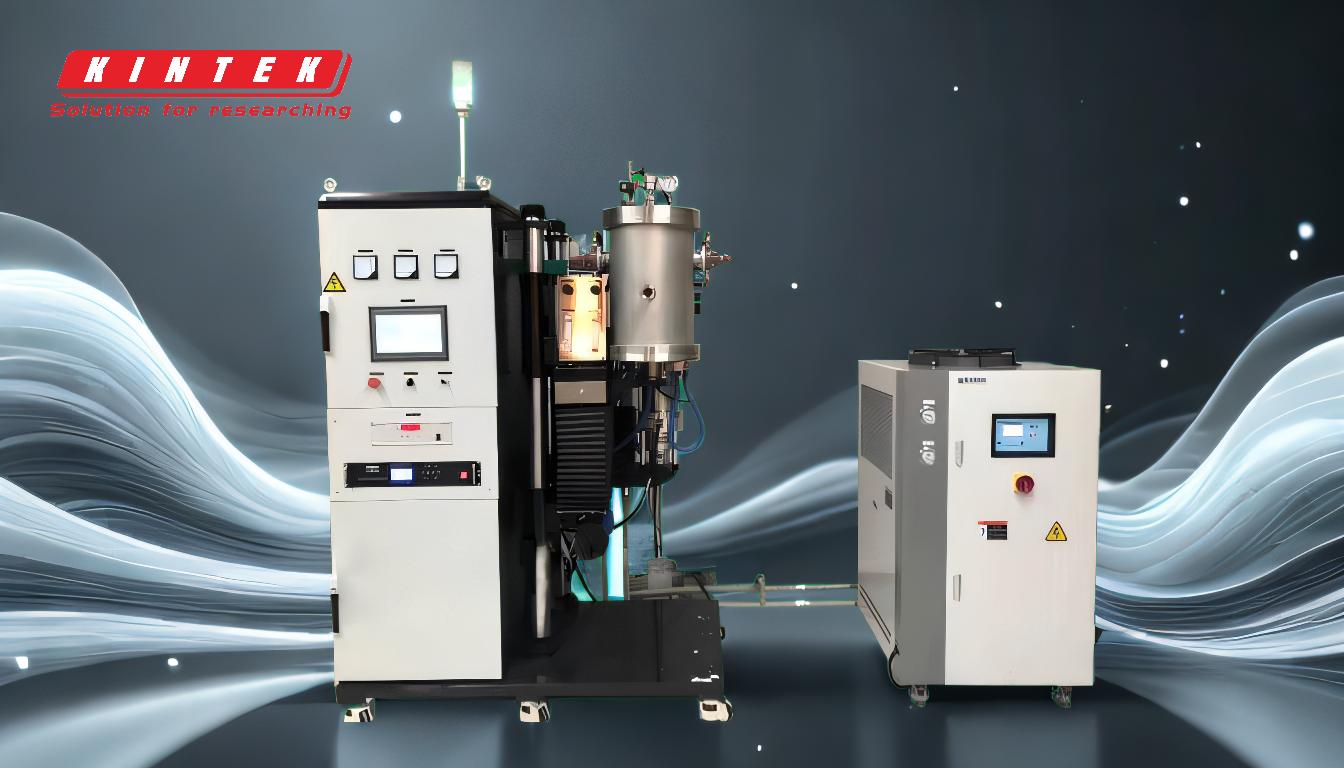
-
Mikrostrukturelle Veränderungen während der Wärmebehandlung
- Die Wärmebehandlung verändert die Mikrostruktur von Metallen, einschließlich Korngröße, Phasenzusammensetzung und Phasenverteilung.
- Durch das Glühen wird beispielsweise die Kornstruktur verfeinert, wodurch sie gleichmäßiger wird, was zu einer glatteren Oberfläche führen kann.
- Umgekehrt kann durch das Abschrecken eine martensitische Struktur entstehen, die härter ist, aber aufgrund erhöhter Sprödigkeit und Eigenspannungen zu einer raueren Oberfläche führen kann.
-
Einfluss der Härte auf die Oberflächenrauheit
- Die Härte ist ein entscheidender Einflussfaktor auf die Oberflächenrauheit.
- Weichere Materialien (z. B. nach dem Glühen) lassen sich leichter bearbeiten oder polieren, was zu einer glatteren Oberfläche führt.
- Härtere Materialien (z. B. nach dem Abschrecken oder Anlassen) sind schwieriger zu bearbeiten und können aufgrund von Werkzeugverschleiß oder Mikrorissen während der Endbearbeitung eine höhere Oberflächenrauheit aufweisen.
-
Eigenspannungen und Oberflächenrauheit
- Durch Wärmebehandlung können Eigenspannungen im Material entstehen.
- Schnelles Abkühlen (Abschrecken) führt häufig zu hohen Eigenspannungen, die zu Verformungen oder Mikrorissen führen und die Oberflächenrauheit erhöhen können.
- Durch spannungsmindernde Behandlungen (z. B. Anlassen) können diese Spannungen reduziert und die Oberflächenbeschaffenheit verbessert werden.
-
Abkühlgeschwindigkeit und ihre Auswirkungen
- Die Abkühlgeschwindigkeit während der Wärmebehandlung ist entscheidend.
- Langsames Abkühlen (z. B. beim Glühen) ermöglicht eine gleichmäßigere Mikrostruktur und verringert die Oberflächenrauheit.
- Schnelles Abkühlen (z. B. beim Abschrecken) kann zu ungleichmäßigen Veränderungen der Mikrostruktur und einer erhöhten Oberflächenrauheit führen.
-
Spezifische Wärmebehandlungsmethoden und Oberflächenrauheit
- Glühen: Reduziert typischerweise die Oberflächenrauheit, indem das Material weicher gemacht und innere Spannungen reduziert werden.
- Abschrecken: Erhöht häufig die Oberflächenrauheit aufgrund der Bildung harter, spröder Phasen und Eigenspannungen.
- Temperieren: Kann die Oberflächenrauheit verbessern, indem es Spannungen abbaut und die Mikrostruktur stabilisiert.
- Normalisieren: Erzeugt eine gleichmäßigere Kornstruktur, die im Vergleich zum Guss- oder Schmiedezustand zu einer glatteren Oberfläche führen kann.
-
Praktische Überlegungen für Käufer von Geräten und Verbrauchsmaterialien
- Berücksichtigen Sie bei der Auswahl von Wärmebehandlungsverfahren die gewünschte Oberflächenbeschaffenheit und die endgültige Anwendung des Materials.
- Für Anwendungen, die eine glatte Oberfläche erfordern, kann Glühen oder Anlassen bevorzugt werden.
- Für Anwendungen, die eine hohe Härte und Verschleißfestigkeit erfordern, kann ein Abschrecken und anschließendes Anlassen erforderlich sein, es können jedoch zusätzliche Nachbearbeitungsprozesse (z. B. Schleifen oder Polieren) erforderlich sein, um die gewünschte Oberflächenrauheit zu erreichen.
- Stellen Sie sicher, dass Wärmebehandlungsgeräte (z. B. Öfen, Abschrecksysteme) in der Lage sind, die Temperatur und Abkühlgeschwindigkeit präzise zu steuern, um konsistente Ergebnisse zu erzielen.
Durch das Verständnis dieser Faktoren können Käufer fundierte Entscheidungen über Wärmebehandlungsprozesse und -geräte treffen, um die gewünschte Oberflächenrauheit für ihre spezifischen Anwendungen zu erreichen.
Übersichtstabelle:
Faktor | Einfluss auf die Oberflächenrauheit |
---|---|
Mikrostrukturelle Veränderungen | Durch das Glühen wird die Kornstruktur verfeinert und die Rauheit verringert. Durch Abschrecken wird die Rauheit erhöht. |
Härte | Weichere Materialien (z. B. nach dem Glühen) ergeben glattere Oberflächen; Härtere Materialien erhöhen die Rauheit. |
Eigenspannungen | Schnelles Abkühlen (Abschrecken) erhöht Spannungen und Rauheit; Durch Anlassen wird die Rauheit verringert. |
Kühlrate | Langsames Abkühlen (z. B. Glühen) verringert die Rauheit; schnelles Abkühlen (z. B. Abschrecken) erhöht ihn. |
Wärmebehandlungsmethoden | Durch Glühen wird die Rauheit verringert; Abschrecken erhöht es; Tempern und Normalisieren verbessern das Finish. |
Erreichen Sie die perfekte Oberflächenrauheit für Ihre Materialien – Kontaktieren Sie noch heute unsere Experten für maßgeschneiderte Wärmebehandlungslösungen!