Das PVD-Verfahren (Physical Vapor Deposition) ist eine vakuumbasierte Beschichtungstechnik, mit der dünne Materialschichten auf ein Substrat aufgebracht werden.Dabei wird ein festes Material durch physikalische Mittel wie Hochtemperaturvakuum oder Plasma in einen Dampfzustand überführt, der Dampf zum Substrat transportiert und kondensiert, um eine dünne, gleichmäßige Schicht zu bilden.Das PVD-Verfahren ist weit verbreitet, da es dauerhafte, hochleistungsfähige Beschichtungen erzeugt, die zur Verringerung der Reibung, zur Verbesserung der Oxidationsbeständigkeit und zur Erhöhung der Härte eingesetzt werden können.Das Verfahren wird unter Niederdruckbedingungen durchgeführt und umfasst in der Regel Schritte wie Sputtern, Verdampfen und thermische Behandlung.
Die wichtigsten Punkte werden erklärt:
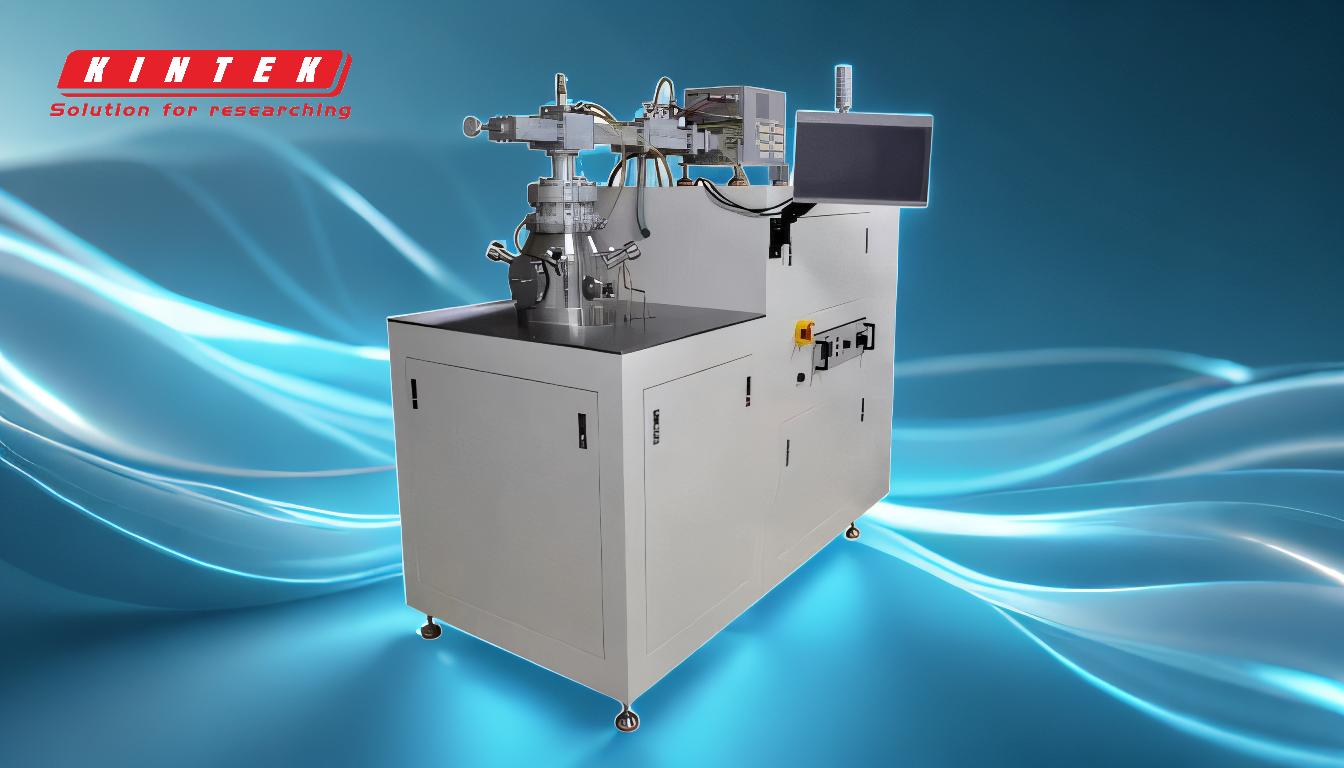
-
Verdampfung des Ausgangsmaterials:
- Das PVD-Verfahren beginnt mit der Umwandlung eines festen Vorläufermaterials in einen Dampf.Dies wird durch physikalische Methoden wie Hochtemperaturvakuum, Elektronenstrahlbeschuss oder Plasmaentladung erreicht.
- Beispielsweise wird ein festes Metalltarget mit hochenergetischen Elektronen oder Ionen beschossen, wodurch Atome aus der Oberfläche herausgeschleudert werden (Sputtern).
- Die verdampften Atome werden dann durch eine Niederdruckumgebung zum Substrat transportiert.
-
Transport des Dampfes zum Substrat:
- Das verdampfte Material wird in einer Vakuumkammer von der Quelle zum Substrat transportiert.Dieser Schritt stellt sicher, dass sich die verdampften Atome in einer geraden Linie bewegen (Line-of-Sight-Beschichtung), ohne Störungen durch Hintergrundgase.
- Die Vakuumumgebung minimiert die Verunreinigung und gewährleistet einen sauberen Abscheidungsprozess.
- In einigen Fällen können reaktive Gase in die Kammer eingeleitet werden, um zusammengesetzte Beschichtungen (z. B. Nitride oder Oxide) zu erzeugen.
-
Kondensation und Filmbildung:
- Sobald die verdampften Atome das Substrat erreichen, kondensieren sie und bilden einen dünnen, gleichmäßigen Film.Die Dicke des Films kann je nach Anwendung von Nanometern bis zu Mikrometern reichen.
- Der Kondensationsprozess wird von Faktoren wie der Substrattemperatur, der Abscheidungsrate und dem Vorhandensein von reaktiven Gasen beeinflusst.
- Der entstehende Film haftet fest auf dem Substrat und bietet verbesserte Eigenschaften wie Härte, Verschleißfestigkeit und Korrosionsbeständigkeit.
-
Arten von PVD-Techniken:
- Sputtern:Ein Zielmaterial wird mit hochenergetischen Ionen beschossen, wodurch Atome herausgeschleudert werden und sich auf dem Substrat ablagern.Diese Technik wird häufig für die Abscheidung von Metallen, Legierungen und Verbindungen verwendet.
- Verdampfung:Das Ausgangsmaterial wird bis zu seinem Verdampfungspunkt erhitzt, und die verdampften Atome werden auf dem Substrat abgeschieden.Dieses Verfahren wird üblicherweise für die Abscheidung dünner Schichten aus Metallen und Halbleitern verwendet.
- Lichtbogen-Dampfabscheidung:Mit einem Lichtbogen wird das Ausgangsmaterial verdampft und anschließend auf das Substrat aufgebracht.Diese Technik wird häufig für harte Beschichtungen wie Titannitrid (TiN) verwendet.
-
Vorteile von PVD:
- Hochwertige Beschichtungen:PVD erzeugt dichte, gleichmäßige Beschichtungen mit hervorragender Haftung und Haltbarkeit.
- Vielseitigkeit:Es kann eine breite Palette von Materialien abscheiden, darunter Metalle, Keramik und einige organische Verbindungen.
- Umweltfreundlich:PVD ist ein sauberes Verfahren, bei dem keine gefährlichen Chemikalien eingesetzt werden und keine schädlichen Nebenprodukte entstehen.
- Präzision:Das Verfahren ermöglicht eine präzise Kontrolle der Schichtdicke und -zusammensetzung und eignet sich daher für Anwendungen in der Mikroelektronik, Optik und Werkzeugbeschichtung.
-
Anwendungen von PVD:
- Werkzeug- und Gesenkbeschichtungen:PVD wird verwendet, um Schneidwerkzeuge, Formen und Matrizen mit harten, verschleißfesten Materialien wie Titannitrid (TiN) und diamantähnlichem Kohlenstoff (DLC) zu beschichten.
- Dekorative Beschichtungen:PVD wird verwendet, um haltbare, kratzfeste Beschichtungen für Uhren, Schmuck und Unterhaltungselektronik herzustellen.
- Halbleiterherstellung:PVD wird zur Abscheidung dünner Schichten aus Metallen und Dielektrika bei der Herstellung von integrierten Schaltkreisen und mikroelektronischen Geräten eingesetzt.
- Optische Beschichtungen:PVD wird zur Herstellung von Antireflexions-, Reflexions- und Schutzschichten auf Linsen, Spiegeln und anderen optischen Komponenten verwendet.
-
Prozesssteuerung und -überwachung:
- Der PVD-Prozess wird sorgfältig kontrolliert, um eine gleichbleibende Schichtqualität zu gewährleisten.Parameter wie Kammerdruck, Substrattemperatur und Abscheiderate werden überwacht und bei Bedarf angepasst.
- Häufig wird ein Quarzkristall-Monitor verwendet, um die Dicke der abgeschiedenen Schicht in Echtzeit zu messen und so eine präzise Kontrolle des Beschichtungsprozesses zu gewährleisten.
Zusammenfassend lässt sich sagen, dass das PVD-Verfahren ein vielseitiges und präzises Verfahren für die Abscheidung dünner Schichten mit einem breiten Anwendungsspektrum ist.Durch die Umwandlung eines festen Materials in einen Dampf und dessen Kondensation auf einem Substrat entstehen durch PVD Beschichtungen, die die Leistung und Haltbarkeit verschiedener Produkte verbessern.
Zusammenfassende Tabelle:
Aspekt | Einzelheiten |
---|---|
Prozess-Übersicht | Wandelt Feststoffe in Dampf um, transportiert ihn und kondensiert ihn zu einem dünnen Film. |
Schlüsseltechniken | Sputtern, Verdampfen, Arc Vapor Deposition |
Vorteile | Hochwertig, langlebig, vielseitig, umweltfreundlich, präzise Steuerung |
Anwendungen | Werkzeugbeschichtungen, dekorative Beschichtungen, Halbleiter, optische Beschichtungen |
Prozesskontrolle | Überwachte Parameter: Druck, Temperatur, Abscheidungsrate |
Entdecken Sie, wie PVD-Beschichtungen Ihre Produkte verbessern können. Kontaktieren Sie noch heute unsere Experten für maßgeschneiderte Lösungen!