Die Schichtdicke in einem Verdampfungssystem wird durch eine Kombination aus präzisen Einstellungen des Verdampfungsprozesses und Überwachungstechniken kontrolliert.Zu den Schlüsselfaktoren gehören die Temperatur des Verdampfungsmittels, die Abscheidungsrate, der Abstand zwischen dem Verdampfer und dem Substrat sowie die Verwendung von Quarzkristall-Mikrowaagen (QCMs) zur Echtzeitmessung der Schichtdicke.Darüber hinaus spielen Umgebungsbedingungen wie Vakuumdruck, Substrattemperatur und Oberflächenvorbereitung eine wichtige Rolle bei der Gewährleistung von Gleichmäßigkeit und Qualität.Durch eine sorgfältige Steuerung dieser Parameter kann das System konsistente und genaue Schichtdicken erzielen, die auf spezifische Anforderungen zugeschnitten sind.
Die wichtigsten Punkte erklärt:
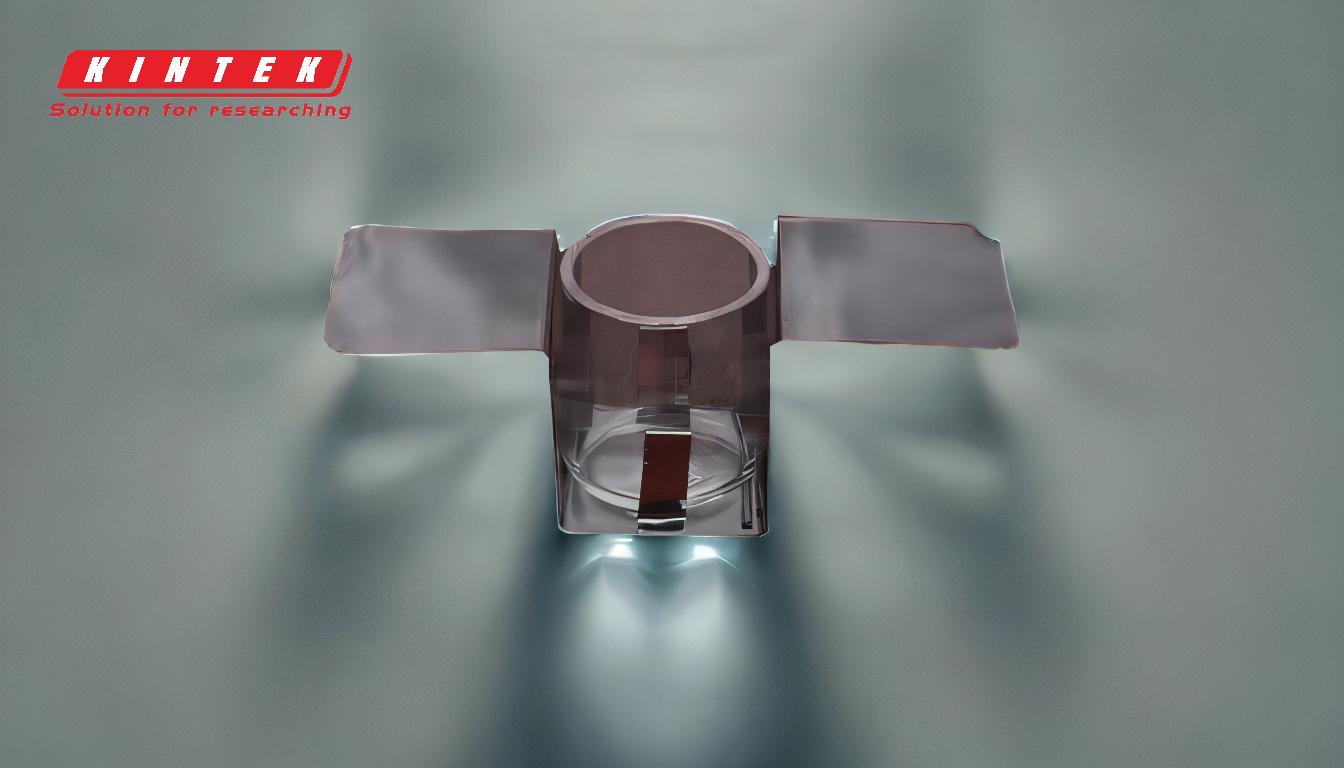
-
Kontrolle der Verdampfungstemperatur:
- Die Temperatur des Verdampfungsmittels hat einen direkten Einfluss auf die Verdampfungsgeschwindigkeit des Materials.Höhere Temperaturen erhöhen die Verdampfungsrate, während niedrigere Temperaturen sie verlangsamen.
- Eine präzise Steuerung der Verdampfungstemperatur gewährleistet eine gleichmäßige Abscheidungsrate, die für das Erreichen der gewünschten Schichtdicke entscheidend ist.
-
Einstellung der Abscheiderate:
- Die Abscheiderate, d. h. die Geschwindigkeit, mit der das Material auf das Substrat aufgebracht wird, ist ein Schlüsselfaktor für die Steuerung der Schichtdicke.
- Durch die Anpassung der Abscheiderate können die Bediener steuern, wie schnell oder langsam die Schicht wächst, und so die endgültige Dicke fein abstimmen.
-
Abstand zwischen Verdampfer und Substrat:
- Der Abstand zwischen der Verdampfungsquelle und dem Substrat beeinflusst die Gleichmäßigkeit und Dicke der abgeschiedenen Schicht.
- Ein geringerer Abstand führt in der Regel zu einer höheren Abscheiderate und dickeren Schichten, während ein größerer Abstand zu gleichmäßigeren, aber dünneren Schichten führen kann.
-
Verwendung von Quarzkristall-Mikrowaagen (QCMs):
- QCMs werden häufig in Aufdampfsystemen eingesetzt, um die Schichtdicke in Echtzeit zu messen und zu regulieren.
- Diese Geräte liefern eine genaue Rückmeldung über die Abscheidungsrate und -dicke und ermöglichen sofortige Anpassungen, um den Prozess präzise zu steuern.
-
Einfluss des Vakuumdrucks:
- Der Druck in der Vakuumkammer spielt eine entscheidende Rolle für die Qualität und Gleichmäßigkeit der Folie.
- Höhere Vakuumniveaus verringern das Vorhandensein von Restgasen und minimieren Kollisionen, die zu ungleichmäßiger Dicke und Verunreinigungen in der Schicht führen können.
-
Substrattemperatur und Oberflächenvorbereitung:
- Die Erwärmung des Substrats verbessert die Beweglichkeit der abgeschiedenen Atome und fördert eine bessere Haftung und Gleichmäßigkeit.
- Eine ordnungsgemäße Oberflächenvorbereitung, wie z. B. das Reinigen und Glätten, stellt sicher, dass das Substrat frei von Verunreinigungen und Unregelmäßigkeiten ist, die die Filmqualität beeinträchtigen könnten.
-
Drehung des Substrathalters:
- Durch Drehen des Substrathalters während der Abscheidung kann die Gleichmäßigkeit der Schichtdicke verbessert werden, indem eine gleichmäßige Einwirkung des Verdampfungsmittels gewährleistet wird.
- Dies ist besonders wichtig bei Substraten mit komplexen Geometrien oder bei der Abscheidung auf großen Flächen.
-
Reinheit und Eigenschaften des Ausgangsmaterials:
- Die Reinheit und das Molekulargewicht des Ausgangsmaterials beeinflussen die Verdampfungsrate und die Qualität der abgeschiedenen Schicht.
- Hochreine Materialien sind für die Herstellung von Schichten mit gleichbleibenden Eigenschaften und minimalen Fehlern unerlässlich.
Durch die Integration dieser Faktoren und den Einsatz fortschrittlicher Überwachungs- und Steuerungstechnologien können Verdampfungssysteme eine präzise und wiederholbare Kontrolle der Schichtdicke erreichen und so hochwertige Ergebnisse für eine Vielzahl von Anwendungen gewährleisten.
Zusammenfassende Tabelle:
Faktor | Rolle bei der Kontrolle der Filmdicke |
---|---|
Temperatur des Verdampfungsmittels | Steuert die Verdampfungsrate; höhere Temperaturen erhöhen die Rate, niedrigere Temperaturen verlangsamen sie. |
Abscheidungsrate | Stellt ein, wie schnell oder langsam der Film wächst, und ermöglicht eine Feinabstimmung der Dicke. |
Abstand Verdampfer-Substrat | Beeinflusst Gleichmäßigkeit und Dicke; kürzerer Abstand = dickere Schichten, länger = gleichmäßigere Schichten. |
Quarzkristall-Mikrowaagen | Ermöglicht Dickenmessung in Echtzeit und Rückmeldung für präzise Kontrolle. |
Vakuumdruck | Ein höheres Vakuum reduziert die Restgase und verbessert die Gleichmäßigkeit und Qualität des Films. |
Substrattemperatur | Verbessert die Beweglichkeit der Atome und fördert eine bessere Haftung und Gleichmäßigkeit. |
Vorbereitung der Oberfläche | Sorgt für ein sauberes, glattes Substrat für eine hochwertige Schichtabscheidung. |
Drehung des Substrathalters | Verbessert die Gleichmäßigkeit durch gleichmäßige Einwirkung des Verdampfungsmittels. |
Reinheit des Ausgangsmaterials | Hochreine Materialien gewährleisten konstante Filmeigenschaften und minimale Defekte. |
Benötigen Sie eine präzise Kontrolle der Schichtdicke in Ihrem Verdampfungssystem? Kontaktieren Sie noch heute unsere Experten für maßgeschneiderte Lösungen!