Die Porosität in der Pulvermetallurgie ist ein kritischer Faktor, der die mechanischen Eigenschaften und die Leistung des Endprodukts beeinflusst.Eine Verringerung der Porosität kann durch die Optimierung mehrerer Schlüsselparameter während des Herstellungsprozesses erreicht werden.Dazu gehören die Erhöhung des Verdichtungsdrucks, der Sintertemperatur und der Sinterzeit, die zusammen zur Verringerung der scheinbaren Porosität und zur Erhöhung der Schüttdichte beitragen.Darüber hinaus ist die Kontrolle der Partikelgröße von entscheidender Bedeutung, da größere Partikel tendenziell die Porosität erhöhen.Durch eine sorgfältige Steuerung dieser Faktoren können die Hersteller Komponenten mit hoher Dichte und geringer Porosität sowie verbesserten mechanischen Eigenschaften herstellen.
Die wichtigsten Punkte werden erklärt:
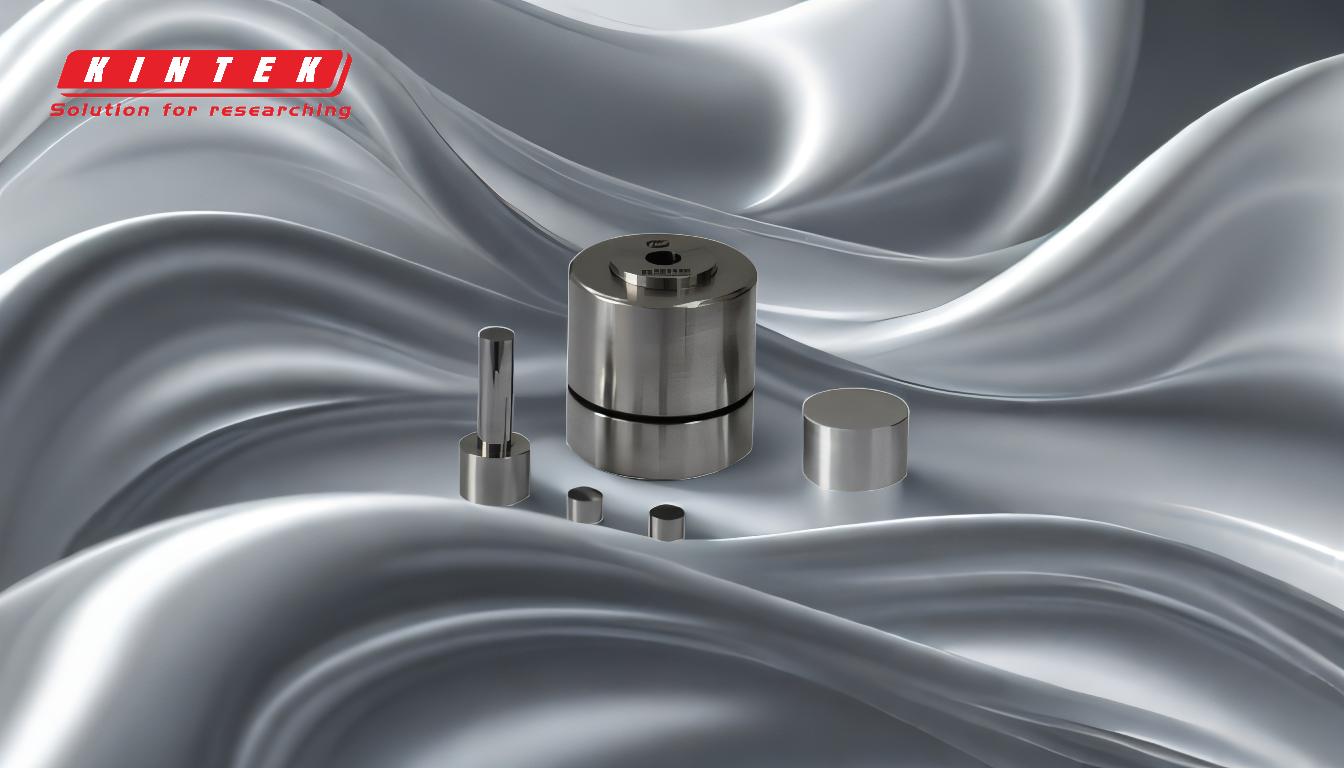
-
Erhöhung des Verdichtungsdrucks:
- Aufschlag:Ein höherer Verdichtungsdruck verringert die Lücken zwischen den Pulverteilchen und führt zu einem dichteren Pressling mit geringerer Porosität.
- Mechanismus:Wenn während der Verdichtungsphase Druck ausgeübt wird, werden die Partikel enger zusammengedrückt, wodurch die Hohlräume minimiert und die Schüttdichte des Grünlings erhöht wird.
- Praktische Überlegungen:Ein höherer Druck ist zwar vorteilhaft, muss aber gegen das Risiko abgewogen werden, die Matrize zu beschädigen oder eine ungleichmäßige Dichteverteilung im Teil zu verursachen.
-
Optimierung der Sintertemperatur und -zeit:
- Aufschlag:Höhere Sintertemperaturen und längere Sinterzeiten fördern eine bessere Partikelbindung und -diffusion, wodurch die Porosität verringert und die Dichte erhöht wird.
- Mechanismus:Beim Sintern wird das verdichtete Pulver unter seinen Schmelzpunkt erhitzt, so dass die Atome über die Partikelgrenzen diffundieren können, wodurch sich die Poren schließen und das Material fester wird.
- Praktische Überlegungen:Eine zu hohe Temperatur oder Zeit kann zu Kornwachstum oder Verformung führen, weshalb eine sorgfältige Optimierung erforderlich ist.
-
Kontrolle der Partikelgröße:
- Aufschlag:Kleinere Partikelgrößen führen im Allgemeinen zu einer geringeren Porosität, da sie sich effizienter zusammenfügen und weniger Hohlräume hinterlassen.
- Mechanismus:Feine Partikel haben ein größeres Verhältnis von Oberfläche zu Volumen, was die Sinterung und Bindung verbessert.Größere Partikel hingegen schaffen mehr Lücken und erhöhen die Porosität.
- Praktische Überlegungen:Kleinere Partikel sind zwar vorzuziehen, können aber auch das Risiko der Agglomeration erhöhen, was bei der Verarbeitung beachtet werden muss.
-
Methoden der Pulverherstellung:
- Aufschlag:Das Verfahren zur Herstellung von Metallpulvern beeinflusst deren Größe, Form und Verteilung, was sich wiederum auf die Porosität auswirkt.
- Mechanismus:Techniken wie die Zerstäubung erzeugen Pulver mit kontrollierten Größenbereichen, die so zugeschnitten werden können, dass die Porosität minimiert wird.Durch Zerkleinern und Mahlen können unregelmäßig geformte Partikel entstehen, die sich weniger effizient verpacken lassen.
- Praktische Überlegungen:Die Wahl des geeigneten Verfahrens zur Pulverherstellung ist entscheidend, um die gewünschten Partikeleigenschaften zu erzielen und die Porosität zu minimieren.
-
Auswahl des Materials:
- Aufschlag:Die Wahl des Basismaterials (z. B. Kupfer- oder Eisenbasis) kann die Porosität aufgrund von Unterschieden in der Partikelform und -größe sowie im Sinterverhalten beeinflussen.
- Mechanismus:Einige Materialien sintern leichter als andere, was zu einer besseren Verdichtung und geringeren Porosität führt.
- Praktische Überlegungen:Die Materialauswahl sollte auf die beabsichtigte Anwendung und die gewünschten mechanischen Eigenschaften abgestimmt sein.
Durch Berücksichtigung dieser Schlüsselfaktoren können Hersteller die Porosität in der Pulvermetallurgie effektiv reduzieren, was zu Komponenten mit verbesserter Festigkeit, Haltbarkeit und Leistung führt.
Zusammenfassende Tabelle:
Schlüsselfaktor | Auswirkung | Mechanismus | Praktische Überlegungen |
---|---|---|---|
Erhöhung des Verdichtungsdrucks | Verringert die Lücken zwischen den Partikeln, was zu dichteren Verdichtungen mit geringerer Porosität führt. | Der Druck presst die Partikel enger zusammen, wodurch Hohlräume minimiert und die Schüttdichte erhöht wird. | Gleichen Sie den Druck aus, um eine Beschädigung der Form oder eine ungleichmäßige Dichteverteilung zu vermeiden. |
Optimierung von Sintertemperatur und -zeit | Fördert die Partikelbindung, verringert die Porosität und erhöht die Dichte. | Das Erhitzen unter den Schmelzpunkt ermöglicht die Diffusion von Atomen, wodurch Poren geschlossen und das Material gestärkt wird. | Vermeiden Sie übermäßige Temperaturen oder Zeiten, um Kornwachstum oder Verformung zu verhindern. |
Kontrolle der Partikelgröße | Kleinere Partikel packen effizient und reduzieren die Porosität. | Feine Partikel haben ein besseres Verhältnis von Oberfläche zu Volumen, was die Sinterung und Bindung verbessert. | Mit kleineren Partikeln lassen sich Agglomerationsrisiken vermeiden. |
Methoden der Pulverherstellung | Beeinflusst Partikelgröße, -form und -verteilung und wirkt sich auf die Porosität aus. | Zerstäubung erzeugt kontrollierte Größenbereiche; Zerkleinern/Mahlen kann unregelmäßige Partikel erzeugen. | Wählen Sie die richtige Methode, um die gewünschten Partikeleigenschaften zu erzielen. |
Auswahl des Materials | Das Grundmaterial beeinflusst die Porosität aufgrund von Unterschieden im Sinterverhalten. | Einige Materialien sintern leichter, was zu einer besseren Verdichtung und geringeren Porosität führt. | Stimmen Sie die Materialauswahl auf die Anwendung und die gewünschten mechanischen Eigenschaften ab. |
Sind Sie bereit, Ihren pulvermetallurgischen Prozess zu optimieren? Kontaktieren Sie noch heute unsere Experten für maßgeschneiderte Lösungen!