Feststoffsintern und Flüssigphasensintern sind zwei verschiedene Verfahren zur Verdichtung von Keramik und anderen Werkstoffen, die sich in erster Linie durch die Mechanismen der Partikelbindung und die erforderlichen Temperaturen unterscheiden.Das Festphasensintern beruht auf Diffusionsmechanismen, um Material zu transportieren und eine Verdichtung zu erreichen, in der Regel bei höheren Temperaturen, und eignet sich für Materialien wie Zirkoniumdioxid und Aluminiumoxid.Im Gegensatz dazu wird beim Flüssigphasensintern eine flüssige Phase mit niedrigem Schmelzpunkt eingebracht, die die Umlagerung und Bindung der Partikel bei niedrigeren Temperaturen erleichtert und sich daher ideal für schwerer zu verdichtende Materialien wie Siliziumnitrid und Siliziumkarbid eignet.Das Vorhandensein der flüssigen Phase beschleunigt die Verdichtung und beeinflusst den Porenschluss, die Korngröße und die mechanischen Eigenschaften.
Die wichtigsten Punkte werden erklärt:
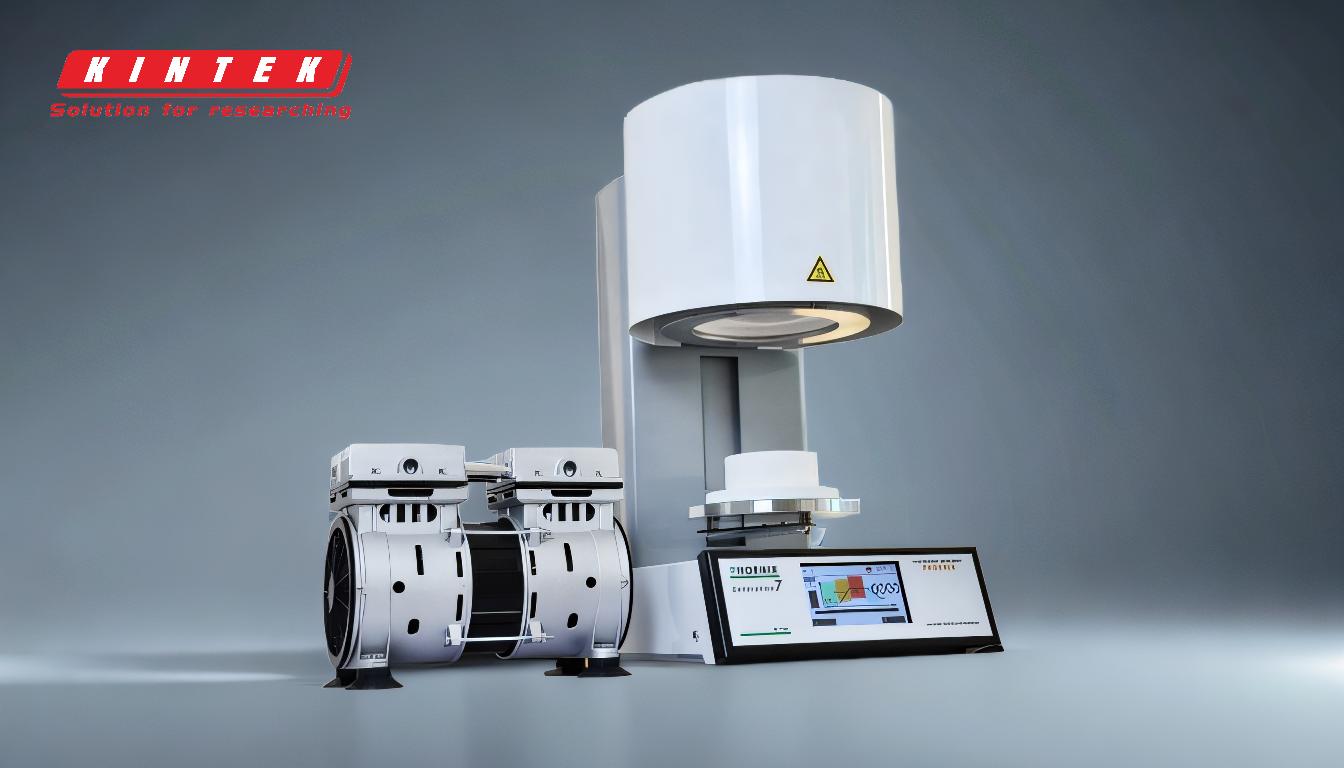
-
Sintertemperatur:
- Festkörpersintern:Dieser Prozess findet bei relativ hohen Temperaturen statt, oft nahe dem Schmelzpunkt des Ausgangsmaterials.So werden beispielsweise Zirkoniumdioxid und Aluminiumoxid bei Temperaturen um 1600 °C gesintert.Die hohen Temperaturen sind notwendig, um die Diffusionsmechanismen zu aktivieren, die das Hauptmittel für den Materialtransport und die Bindung sind.
- Flüssig-Phasen-Sintern:Dieses Verfahren arbeitet bei niedrigeren Temperaturen als das Festkörpersintern.Durch die Zugabe einer flüssigen Phase mit niedrigem Schmelzpunkt wird die für die Verdichtung erforderliche Sintertemperatur insgesamt gesenkt.Die flüssige Phase bildet sich bei der Sintertemperatur und ermöglicht es den Kapillarkräften, die Partikel effizienter umzuordnen.
-
Mechanismen der Verdichtung:
- Festkörpersintern:Die Verdichtung wird durch Diffusion im festen Zustand erreicht.Atome bewegen sich von Bereichen mit hohem chemischem Potenzial (z. B. Partikeloberflächen) zu Bereichen mit niedrigem chemischem Potenzial (z. B. Nacken zwischen Partikeln).Dieser Prozess ist langsamer und erfordert höhere Temperaturen, um die Aktivierungsenergiebarrieren für die Diffusion zu überwinden.
- Flüssig-Phasen-Sintern:Die flüssige Phase verbessert die Verdichtung, indem sie den Atomen einen Weg mit hoher Diffusionsfähigkeit bietet.Die Kapillarkräfte treiben die Umlagerung der Partikel voran, und die flüssige Phase füllt die Lücken zwischen den Partikeln, was eine schnellere Bindung und Verdichtung fördert.Dieser Prozess ist besonders effektiv bei Materialien, die sich nur schwer durch Festkörpermechanismen verdichten lassen.
-
Porenverschluß:
- Festkörpersintern:Das Schließen der Poren beim Sintern im festen Zustand ist ein allmählicher Prozess, der auf der langsamen Diffusion von Atomen beruht.Mit fortschreitender Sinterung schrumpfen die Poren und schließen sich schließlich, doch kann dies insbesondere bei niedrigeren Temperaturen sehr lange dauern.Das endgültige Gefüge kann je nach den Sinterbedingungen noch eine gewisse Restporosität aufweisen.
- Flüssig-Phasen-Sintern:Das Vorhandensein der flüssigen Phase beschleunigt den Porenschluss.Die Flüssigkeit füllt die Poren und Lücken zwischen den Partikeln, was zu einer schnelleren Verdichtung führt.Die flüssige Phase trägt auch zur Umverteilung des Materials bei und verringert die Gesamtporosität wirksamer als beim Sintern im festen Zustand.Das Ergebnis ist ein dichteres Endprodukt mit weniger Restporen.
-
Korngröße und Gefüge:
- Festkörpersintern:Dieser Prozess kann zu einem erheblichen Kornwachstum führen, insbesondere bei hohen Temperaturen.Größere Körner können sich negativ auf die mechanischen Eigenschaften, wie Festigkeit und Zähigkeit, auswirken.Das Mikrogefüge ist in der Regel durch größere, gleichmäßigere Körner gekennzeichnet.
- Flüssig-Phasen-Sintern:Beim Flüssigphasensintern entstehen aufgrund der niedrigeren Sintertemperaturen und des Vorhandenseins der flüssigen Phase, die das Kornwachstum hemmen kann, tendenziell kleinere Korngrößen.Die resultierende Mikrostruktur ist feiner, was die mechanischen Eigenschaften wie Biegefestigkeit und Bruchzähigkeit verbessern kann.Außerdem kann sich der Bruchmodus von transgranular (durch die Körner hindurch) zu intergranular (entlang der Korngrenzen) verlagern, was die Zähigkeit weiter erhöht.
-
Materialeignung:
- Festkörpersintern:Diese Methode eignet sich für Materialien, die durch Diffusionsmechanismen verdichtet werden können, wie z. B. Zirkoniumdioxid und Tonerde.Diese Werkstoffe haben in der Regel einen hohen Schmelzpunkt und erfordern keine Zugabe einer flüssigen Phase zur Verdichtung.
- Flüssigphasensintern:Diese Methode ist ideal für Materialien, die sich nur schwer durch Festkörpermechanismen verdichten lassen, wie z. B. Siliziumnitrid und Siliziumkarbid.Die Zugabe einer flüssigen Phase erleichtert die Verdichtung bei niedrigeren Temperaturen und verbessert die gesamte Sinterkinetik.
-
Mechanische Eigenschaften:
- Festkörpersintern:Die mechanischen Eigenschaften von im Festkörpersinterverfahren hergestellten Werkstoffen sind im Allgemeinen gut, sie weisen eine hohe Dichte und eine ausgezeichnete Hochtemperaturleistung auf.Allerdings kann das Potenzial für Kornwachstum bei hohen Temperaturen zu einer geringeren Festigkeit und Zähigkeit führen.
- Flüssig-Phasen-Sintern:Materialien, die mit Hilfe von Flüssigphasenverfahren gesintert werden, weisen häufig bessere mechanische Eigenschaften auf, darunter eine höhere Biegefestigkeit und Bruchzähigkeit.Die feinere Korngröße und der intergranulare Bruchmodus tragen zu diesen Verbesserungen bei.Außerdem können die niedrigeren Sintertemperaturen dazu beitragen, die intrinsischen Eigenschaften des Materials zu erhalten.
Zusammenfassend lässt sich sagen, dass die Wahl zwischen Festphasen- und Flüssigphasensintern von den Materialeigenschaften, der gewünschten Mikrostruktur und der mechanischen Leistung abhängt.Das Festphasensintern eignet sich für Werkstoffe, die durch Diffusion verdichtet werden können, während das Flüssigphasensintern für schwieriger zu verdichtende Werkstoffe von Vorteil ist, da es niedrigere Sintertemperaturen, eine schnellere Verdichtung und bessere mechanische Eigenschaften bietet.
Zusammenfassende Tabelle:
Aspekt | Festphasen-Sintern | Flüssig-Phasen-Sintern |
---|---|---|
Temperatur | Hohe Temperaturen (z. B. 1600 °C für Zirkoniumdioxid/Aluminiumoxid) | Niedrigere Temperaturen aufgrund des Vorhandenseins einer flüssigen Phase mit niedrigem Schmelzpunkt |
Mechanismus der Verdichtung | Beruht auf Diffusion im festen Zustand, langsamerer Prozess | Flüssige Phase verbessert die Diffusion, schnellere Umlagerung und Bindung von Partikeln |
Porenverschluß | Allmählich, beruht auf langsamer Diffusion; Restporosität möglich | Beschleunigt durch flüssige Phase, weniger Restporen |
Größe der Körner | Größere Körner aufgrund der hohen Temperaturen | Kleinere Körner, feineres Gefüge |
Material-Eignung | Geeignet für Zirkoniumdioxid, Aluminiumoxid und andere diffusionsfreundliche Materialien | Ideal für Siliziumnitrid, Siliziumkarbid und schwerer zu verdichtende Materialien |
Mechanische Eigenschaften | Gute Dichte und Hochtemperatureigenschaften; potenzielles Kornwachstum verringert die Zähigkeit | Verbesserte Biegefestigkeit, Bruchzähigkeit und feineres Gefüge |
Benötigen Sie Hilfe bei der Auswahl des richtigen Sinterverfahrens für Ihre Werkstoffe? Kontaktieren Sie noch heute unsere Experten !