Kernlose Induktionsöfen bieten zwar Vorteile wie präzise Temperaturregelung, gleichmäßige Wärmeverteilung und Flexibilität beim Legierungswechsel, haben aber auch erhebliche Nachteile.Zu den wichtigsten Nachteilen gehört der geringere Wirkungsgrad (ca. 75 %) im Vergleich zu Kernöfen, die einen Wirkungsgrad von bis zu 98 % erreichen können.Außerdem kann der häufige Legierungswechsel den Verschleiß der feuerfesten Auskleidung beschleunigen, was deren Lebensdauer verkürzt.Das Fehlen eines flussmittelkonzentrierenden Kerns in kernlosen Öfen trägt ebenfalls zu deren geringerer Effizienz bei.Aufgrund dieser Faktoren sind Induktionstiegelöfen weniger geeignet für Betriebe mit hohem Durchsatz oder für Umgebungen, die eine kontinuierliche Produktion mit minimalen Ausfallzeiten erfordern.
Die wichtigsten Punkte werden erklärt:
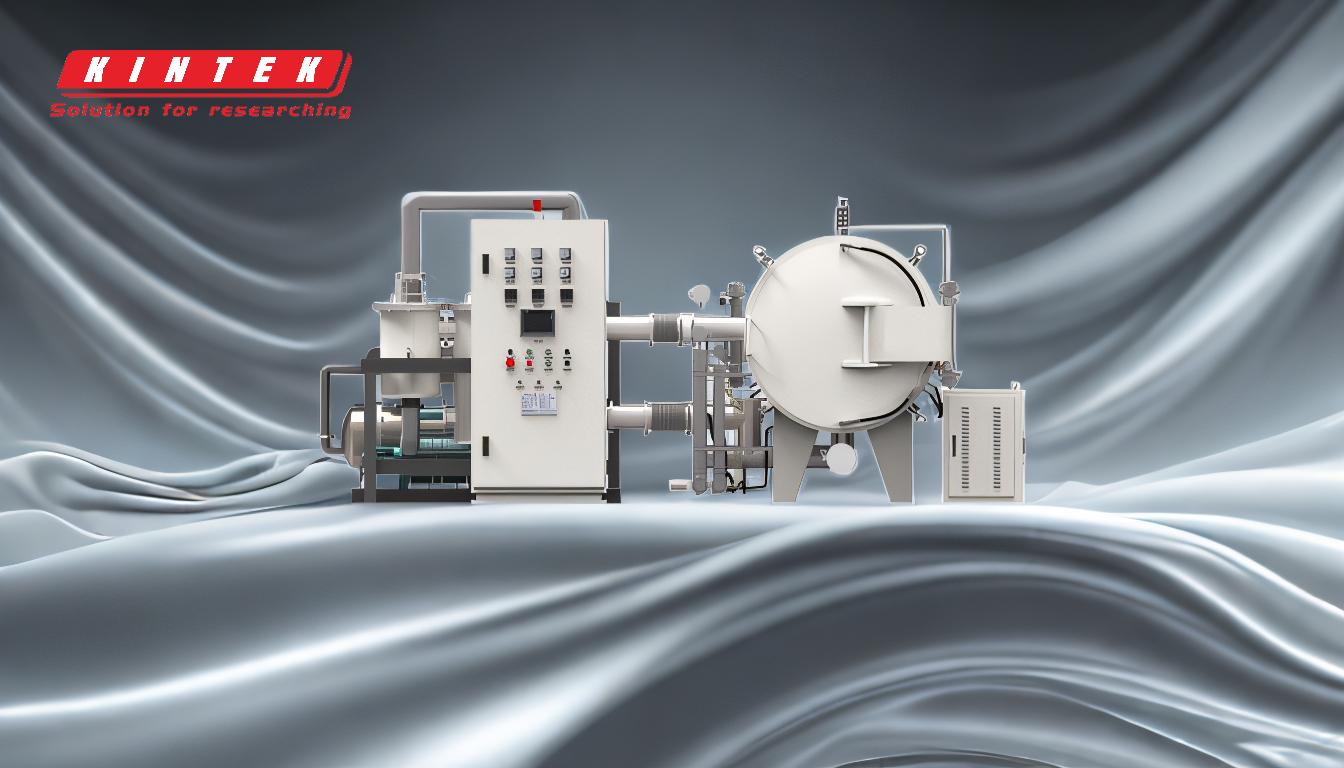
-
Reduzierter Leistungswirkungsgrad
- Kernlose Induktionsöfen arbeiten mit einem Wirkungsgrad von ca. 75 % und damit deutlich niedriger als Öfen mit Kern, die einen Wirkungsgrad von bis zu 98 % erreichen können.
- Das Fehlen eines flusskonzentrierenden Kerns in kernlosen Öfen führt zu Energieverlusten, da das Magnetfeld weniger effektiv auf die Metallcharge konzentriert ist.
- Dieser geringere Wirkungsgrad führt zu einem höheren Energieverbrauch und zu höheren Betriebskosten, so dass kernlose Öfen für Anwendungen mit hohem Durchsatz oder hohem Energiebedarf weniger wirtschaftlich sind.
-
Abnutzung der feuerfesten Auskleidung
- Häufige Legierungswechsel, wie sie bei kernlosen Öfen üblich sind, können den Abbau der feuerfesten Auskleidung beschleunigen.
- Die feuerfeste Auskleidung ist thermischen Zyklen und chemischen Reaktionen mit verschiedenen Legierungen ausgesetzt, was zu Rissen, Erosion und verkürzter Lebensdauer führt.
- Der Austausch der feuerfesten Auskleidung ist kostspielig und zeitaufwändig und erhöht die Wartungskosten und Ausfallzeiten.
-
Begrenzte Eignung für kontinuierlichen Betrieb
- Induktionstiegelöfen sind auf Flexibilität ausgelegt, so dass sie abgestellt und kalt angefahren werden können, was bei Legierungswechseln von Vorteil ist.
- Aufgrund dieser Konstruktion eignen sie sich jedoch weniger für kontinuierliche Hochproduktionsverfahren, bei denen die Aufrechterhaltung eines konstanten Schmelzbades unerlässlich ist.
- Kernöfen hingegen sind aufgrund ihres höheren Wirkungsgrads und ihrer Fähigkeit, kontinuierlich zu arbeiten, für solche Anwendungen besser geeignet.
-
Höherer Energieverbrauch
- Der geringere Wirkungsgrad von kernlosen Öfen bedeutet, dass mehr Energie benötigt wird, um die gleichen Schmelzergebnisse zu erzielen wie mit Kernöfen.
- Dieser höhere Energiebedarf kann zu höheren Betriebskosten führen, insbesondere in Regionen mit teurem Strom.
- Für Unternehmen, die ihre Energiekosten minimieren wollen, sind kernlose Öfen möglicherweise nicht die kostengünstigste Option.
-
Abhängigkeit vom Kühlsystem
- Kernlose Induktionsöfen sind auf wassergekühlte Kupferspulen angewiesen, um eine Überhitzung während des Betriebs zu verhindern.
- Das Kühlsystem macht die Konstruktion des Ofens komplexer und erfordert eine regelmäßige Wartung, um die ordnungsgemäße Funktion sicherzustellen.
- Jede Störung im Kühlsystem kann zu Schäden an der Spule oder zur Abschaltung des Ofens führen und die Produktion unterbrechen.
-
Betriebliche Beschränkungen
- Kernlose Öfen bieten zwar Flexibilität in Bezug auf Legierungswechsel und Frequenzbereich (50 Hz bis 10 kHz), sind aber bei niedrigeren Frequenzen weniger effizient.
- Kernöfen sind mit ihrem höheren Wirkungsgrad besser für Anwendungen geeignet, die eine gleichbleibende Leistung über einen breiten Frequenzbereich erfordern.
Zusammenfassend lässt sich sagen, dass kernlose Induktionsöfen zwar eine hervorragende Kontrolle über die Temperatur und die Metallchemie bieten, aber aufgrund ihres geringeren Wirkungsgrads, ihrer Anfälligkeit für den Verschleiß der feuerfesten Auskleidung und ihres höheren Energieverbrauchs weniger geeignet sind für Anwendungen mit hohem Durchsatz oder Dauerbetrieb.Diese Nachteile sollten bei der Auswahl eines Ofens für bestimmte industrielle Anwendungen sorgfältig bedacht werden.
Zusammenfassende Tabelle:
Benachteiligung | Beschreibung |
---|---|
Reduzierter Wirkungsgrad | Arbeitet mit einem Wirkungsgrad von ca. 75 % im Vergleich zu 98 % bei Kernöfen, was zu einem höheren Energieverbrauch führt. |
Abnutzung der feuerfesten Auskleidung | Häufige Legierungswechsel beschleunigen die Abnutzung der Auskleidung und erhöhen die Wartungskosten und Ausfallzeiten. |
Begrenzt für kontinuierlichen Einsatz | Aufgrund konstruktiver Einschränkungen weniger geeignet für hohen Durchsatz oder Dauerbetrieb. |
Höherer Energieverbrauch | Eine geringere Effizienz erhöht die Betriebskosten, insbesondere in Regionen mit teurem Strom. |
Abhängigkeit vom Kühlsystem | Ist auf wassergekühlte Spulen angewiesen, was die Komplexität und den Wartungsbedarf erhöht. |
Betriebliche Beschränkungen | Geringerer Wirkungsgrad bei niedrigeren Frequenzen, daher sind Kernöfen besser für eine konstante Leistung geeignet. |
Benötigen Sie Hilfe bei der Auswahl des richtigen Ofens für Ihre Bedürfnisse? Kontaktieren Sie noch heute unsere Experten !