Das Sintern ist ein wichtiger Prozess in der Werkstoffkunde, bei dem pulverförmige Materialien verdichtet und erhitzt werden, um eine feste Struktur zu bilden.Die Qualität und die Eigenschaften des gesinterten Produkts werden von mehreren Schlüsselfaktoren beeinflusst, darunter Temperatur, Sinterzeit, Druck, Atmosphäre, Partikelgröße und Zusammensetzung.Jeder dieser Faktoren spielt eine wichtige Rolle bei der Bestimmung der Sinterkinetik, der Verdichtung und der endgültigen Materialeigenschaften.So können beispielsweise höhere Temperaturen die Zugfestigkeit und die Kerbschlagarbeit verbessern, während kleinere Partikelgrößen und homogene Zusammensetzungen eine bessere Verdichtung begünstigen.Auch die Sinteratmosphäre, ob Luft, Vakuum oder Inertgase, kann das Ergebnis erheblich beeinflussen.Das Verständnis dieser Faktoren ist entscheidend für die Optimierung des Sinterprozesses, um die gewünschten Materialeigenschaften zu erzielen.
Die wichtigsten Punkte werden erklärt:
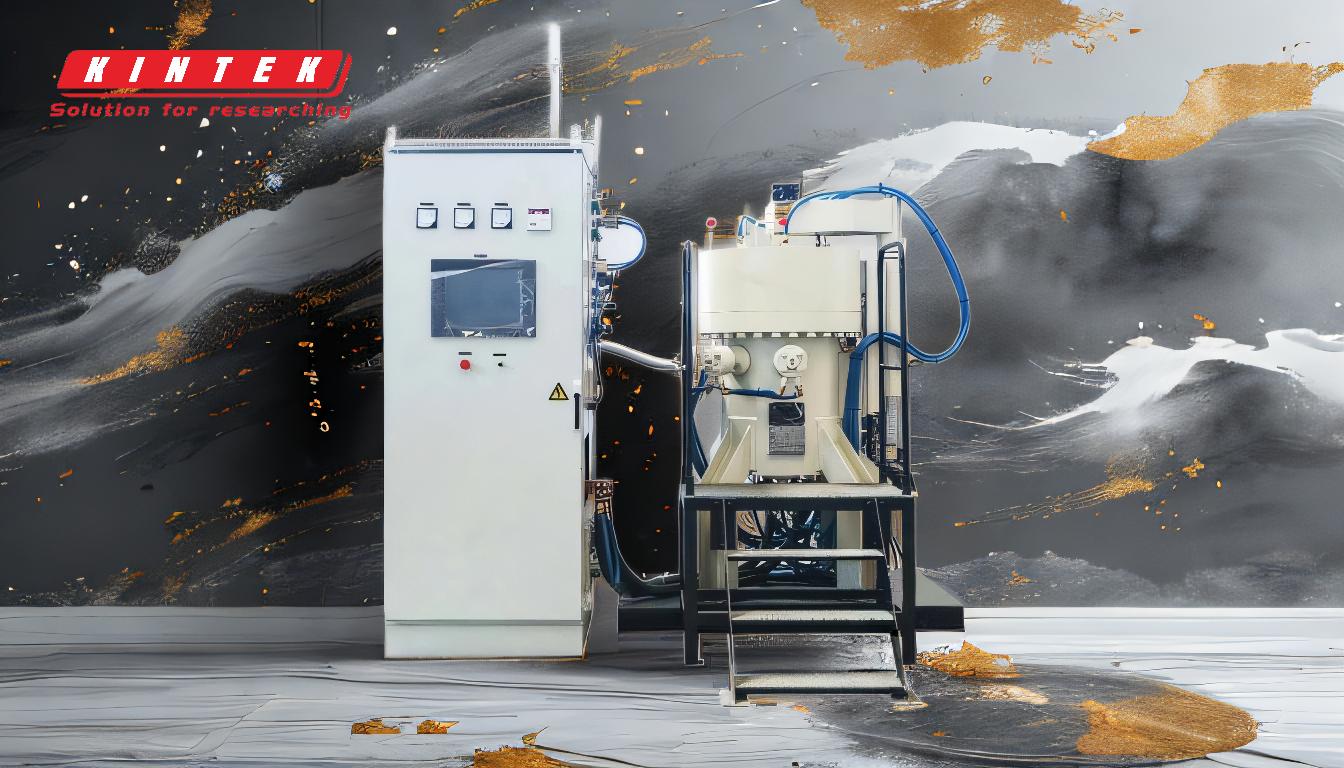
-
Temperatur:
- Rolle bei der Sinterung:Die Temperatur ist einer der wichtigsten Faktoren bei der Sinterung.Sie beeinflusst direkt die Sinterkinetik, die die Geschwindigkeit bestimmt, mit der sich die Partikel verbinden und verdichten.Höhere Temperaturen erhöhen im Allgemeinen die Mobilität der Atome, was zu einer schnelleren Diffusion und einer besseren Partikelbindung führt.
- Auswirkungen auf die Materialeigenschaften:Erhöhte Temperaturen können die mechanischen Eigenschaften des Sinterprodukts verbessern, z. B. die Zugfestigkeit, die Biegewechselfestigkeit und die Kerbschlagarbeit.Zu hohe Temperaturen können jedoch zu unerwünschtem Kornwachstum oder Phasenumwandlungen führen, die die Materialeigenschaften beeinträchtigen können.
-
Sinterzeit:
- Wirkung auf die Verdichtung:Die Dauer des Sinterprozesses wirkt sich auf den Grad der Verdichtung aus.Längere Sinterzeiten ermöglichen eine vollständigere Partikelbindung und Porenbeseitigung, was zu einer höheren Dichte und besseren mechanischen Eigenschaften führt.
- Kompromisse:Längere Sinterzeiten können zwar die Verdichtung verbessern, sie erhöhen aber auch das Risiko des Kornwachstums und können zu Energieineffizienz führen.Daher muss die Sinterzeit optimiert werden, um ein Gleichgewicht zwischen Verdichtung und Energieverbrauch herzustellen.
-
Druck:
- Rolle bei der Umlagerung von Teilchen:Der während des Sinterns ausgeübte Druck trägt zur Umstrukturierung der Partikel, zur Verringerung der Porosität und zur Verbesserung der Verdichtung bei.Druck kann auch die Beseitigung von Hohlräumen erleichtern und die Gleichmäßigkeit des gesinterten Produkts verbessern.
- Auswirkungen auf die endgültigen Eigenschaften:Höhere Drücke führen im Allgemeinen zu einer besseren Verdichtung und besseren mechanischen Eigenschaften.Die Anwendung von Druck muss jedoch sorgfältig kontrolliert werden, um Verformungen oder Risse im Material zu vermeiden.
-
Atmosphäre:
- Arten von Atmosphären:Die Sinteratmosphäre kann aus Luft, Vakuum oder Inertgasen wie Argon oder Stickstoff bestehen.Jede Atmosphäre hat unterschiedliche Auswirkungen auf den Sinterprozess.
- Einfluss auf die Sinterung:Die Wahl der Atmosphäre kann die Oxidation, Reduktion oder Verunreinigung des Materials beeinflussen.So kann beispielsweise eine Vakuum- oder Inertatmosphäre die Oxidation verhindern, was für sauerstoffempfindliche Materialien entscheidend ist.Die Atmosphäre beeinflusst auch die Wärmeleitfähigkeit und den Wärmeübergang während des Sinterns.
-
Partikelgröße:
- Einfluss auf das Sinterverhalten:Kleinere Partikel haben ein größeres Verhältnis von Oberfläche zu Volumen, was eine schnellere Diffusion und bessere Verdichtung begünstigt.Kleinere Partikel neigen auch dazu, bei niedrigeren Temperaturen zu sintern als größere Partikel.
- Auswirkungen auf die endgültigen Eigenschaften:Feinere Pulver führen im Allgemeinen zu einem homogeneren Gefüge und besseren mechanischen Eigenschaften.Sehr feine Partikel können jedoch schwierig zu handhaben sein und erfordern möglicherweise spezielle Verarbeitungstechniken.
-
Zusammensetzung:
- Rolle bei der Sinterung:Die chemische Zusammensetzung der Pulvermischung wirkt sich auf das Sinterverhalten aus.Homogene Zusammensetzungen neigen dazu, gleichmäßiger zu sintern, was zu einer besseren Verdichtung und weniger Defekten führt.
- Auswirkungen auf die Materialeigenschaften:Die Zusammensetzung bestimmt die Endphase und das Mikrogefüge des Sinterprodukts.Legierungselemente oder Zusatzstoffe können verwendet werden, um die Eigenschaften des gesinterten Materials, wie Härte, Zähigkeit oder Wärmeleitfähigkeit, zu beeinflussen.
-
Aufheizrate:
- Wirkung auf die Verdichtung:Die Geschwindigkeit, mit der das Material erhitzt wird, kann den Sinterprozess beeinflussen.Eine langsamere Aufheizgeschwindigkeit ermöglicht eine gleichmäßigere Wärmeverteilung und kann thermische Spannungen reduzieren, was zu einer besseren Verdichtung führt.
- Auswirkungen auf die Mikrostruktur:Schnelle Erhitzungsgeschwindigkeiten können zu ungleichmäßiger Sinterung führen und Defekte wie Risse oder Hohlräume verursachen.Daher muss die Aufheizgeschwindigkeit sorgfältig kontrolliert werden, um die gewünschte Mikrostruktur und die gewünschten Eigenschaften zu erreichen.
-
Abkühlgeschwindigkeit:
- Auswirkung auf die endgültigen Eigenschaften:Die Geschwindigkeit, mit der das gesinterte Produkt abgekühlt wird, kann sich auf das endgültige Mikrogefüge und die Eigenschaften auswirken.Langsame Abkühlungsraten können zu Kornwachstum und Phasenumwandlungen führen, während eine schnelle Abkühlung zu einem feineren Gefüge und besseren mechanischen Eigenschaften führen kann.
- Abwägungen:Die Abkühlungsgeschwindigkeit muss optimiert werden, um ein Gleichgewicht zwischen der gewünschten Mikrostruktur und den Eigenschaften herzustellen.Eine schnelle Abkühlung kann für bestimmte Werkstoffe von Vorteil sein, kann aber auch zu Eigenspannungen führen.
-
Schichtdicke und Maschinengeschwindigkeit:
- Die Rolle des industriellen Sinterns:Bei industriellen Sinterprozessen werden Faktoren wie die Schichtdicke und die Maschinengeschwindigkeit kontrolliert, um eine gleichbleibende Qualität zu gewährleisten.Die Schichtdicke beeinflusst die Wärmeverteilung und die Sinterkinetik, während die Maschinengeschwindigkeit die Sinterzeit und den Endpunkt bestimmt.
- Einfluss auf die Sinterqualität:Die richtige Steuerung dieser Parameter ist entscheidend für eine gleichmäßige Sinterung und die Vermeidung von Fehlern.So sind beispielsweise eine Schichtdicke von 250-500 mm und eine Maschinengeschwindigkeit von 1,5-4 m/min typische Werte für industrielle Sinterprozesse.
-
Gasatmosphäre und Vakuum:
- Einfluss auf die Sinterung:Die Gasatmosphäre und der Vakuumgrad können den Sinterprozess erheblich beeinflussen.Ein Vakuum oder eine inerte Atmosphäre kann Oxidation und Verunreinigung verhindern, während eine kontrollierte Gasatmosphäre verwendet werden kann, um bestimmte Reaktionen oder Phasenumwandlungen zu erreichen.
- Auswirkungen auf die Materialeigenschaften:Die Wahl der Atmosphäre kann die endgültigen Eigenschaften des Sinterprodukts, wie Dichte, Porosität und mechanische Festigkeit, beeinflussen.Daher muss die Atmosphäre je nach Material und gewünschten Eigenschaften sorgfältig ausgewählt werden.
Zusammenfassend lässt sich sagen, dass der Sinterprozess durch ein komplexes Zusammenspiel von Faktoren beeinflusst wird, von denen jeder einzelne sorgfältig gesteuert werden muss, um die gewünschten Materialeigenschaften zu erzielen.Das Verständnis dieser Faktoren und ihrer Wechselwirkungen ist entscheidend für die Optimierung des Sinterprozesses und die Herstellung hochwertiger Sinterprodukte.
Zusammenfassende Tabelle:
Faktor | Rolle bei der Sinterung | Auswirkungen auf die Materialeigenschaften |
---|---|---|
Temperatur | Bestimmt die Sinterkinetik; höhere Temperaturen verbessern die Diffusion und Bindung. | Verbessert die Zugfestigkeit, die Biegewechselfestigkeit und die Schlagenergie. |
Sinterzeit | Längere Zeiten verbessern die Verdichtung, riskieren aber Kornwachstum. | Verbessert die Dichte und die mechanischen Eigenschaften; Kompromiss mit der Energieeffizienz. |
Druck | Erleichtert die Umlagerung von Partikeln und die Verringerung der Porosität. | Höhere Drücke führen zu einer besseren Verdichtung und Gleichmäßigkeit. |
Atmosphäre | Luft, Vakuum oder Inertgase beeinflussen Oxidation, Reduktion und Verunreinigung. | Verhindert Oxidation; beeinflusst Wärmeleitfähigkeit und Materialintegrität. |
Partikelgröße | Kleinere Partikel sintern schneller und bei niedrigeren Temperaturen; die größere Oberfläche verbessert die Bindung. | Feinere Pulver führen zu homogenen Mikrostrukturen und besseren mechanischen Eigenschaften. |
Zusammensetzung | Homogene Mischungen sintern gleichmäßig; Zusatzstoffe beeinflussen die Eigenschaften. | Bestimmt die Endphase, das Gefüge und Eigenschaften wie Härte und Zähigkeit. |
Erwärmungsrate | Langsame Geschwindigkeiten gewährleisten eine gleichmäßige Wärmeverteilung und verringern die thermische Belastung. | Schnelles Erhitzen kann Defekte verursachen; kontrollierte Geschwindigkeiten verbessern die Verdichtung. |
Abkühlungsrate | Beeinflusst das Mikrogefüge; langsames Abkühlen kann zu Kornwachstum führen, während schnelles Abkühlen es verfeinert. | Schnelles Abkühlen verbessert die mechanischen Eigenschaften, kann aber Eigenspannungen verursachen. |
Schichtdicke | Beeinflusst die Wärmeverteilung und die Sinterkinetik in industriellen Prozessen. | Eine ordnungsgemäße Kontrolle gewährleistet eine gleichmäßige Sinterung und vermeidet Defekte. |
Gashaltige Atmosphäre | Vakuum oder Inertgase verhindern Oxidation; kontrollierte Atmosphären ermöglichen spezifische Reaktionen. | Beeinflusst Dichte, Porosität und mechanische Festigkeit des gesinterten Produkts. |
Sind Sie bereit, Ihren Sinterprozess zu optimieren? Kontaktieren Sie noch heute unsere Experten für maßgeschneiderte Lösungen!