Der Sputterprozess ist eine weit verbreitete Technik bei der Dünnschichtabscheidung, bei der Atome aus einem Targetmaterial ausgestoßen und anschließend auf einem Substrat abgeschieden werden. Dieser Prozess wird in einer Vakuumkammer durchgeführt, in der mit einem Inertgas wie Argon ein Plasma erzeugt wird. Das Zielmaterial wird mit ionisierten Gaspartikeln bombardiert, wodurch Atome ausgestoßen und auf dem Substrat abgelagert werden, wodurch ein dünner Film entsteht. Der Prozess ist gut kontrollierbar und wird für Anwendungen bevorzugt, die eine präzise Kontrolle der Filmeigenschaften wie Korngröße, Rauheit und Stöchiometrie erfordern.
Wichtige Punkte erklärt:
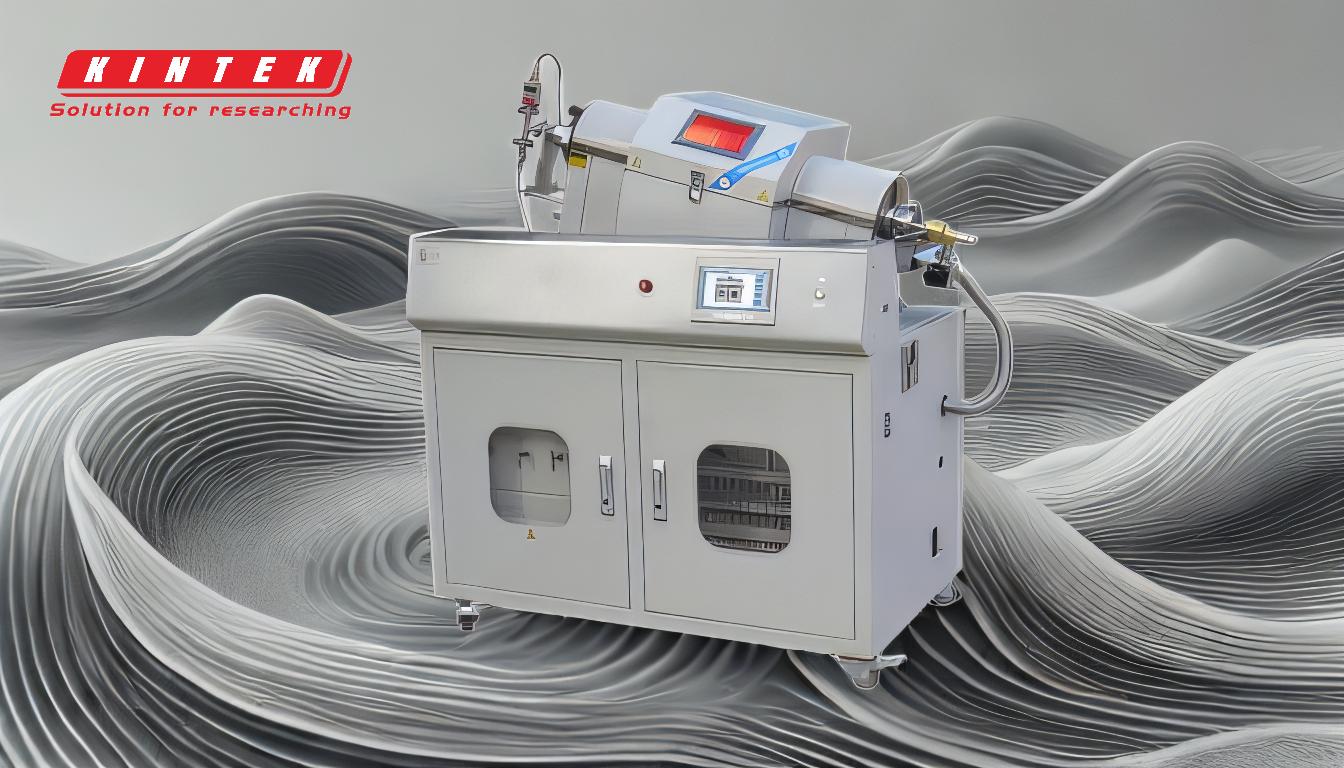
-
Aufbau der Vakuumkammer:
- Der Sputterprozess beginnt mit der Platzierung des Targetmaterials und des Substrats in einer Vakuumkammer. Anschließend wird die Kammer evakuiert, um jegliche Feuchtigkeit und Verunreinigungen zu entfernen, wodurch eine Niederdruckumgebung von typischerweise etwa 1 Pa entsteht. Dieser Schritt ist entscheidend, um sicherzustellen, dass der Sputterprozess nicht durch externe Partikel verunreinigt wird.
-
Einführung von Inertgas:
- Sobald das Vakuum aufgebaut ist, wird ein Inertgas, beispielsweise Argon, in die Kammer eingeleitet. Das Inertgas wird gewählt, weil es nicht chemisch mit dem Zielmaterial oder dem Substrat reagiert und so gewährleistet, dass der abgeschiedene Film rein bleibt.
-
Erzeugung von Plasma:
- Zwischen dem Target (Kathode) und dem Substrat (Anode) wird eine Hochspannung angelegt, wodurch in der Kammer ein Plasma entsteht. Das Plasma besteht aus ionisierten Gasatomen, die für den Sputterprozess unerlässlich sind. Die freien Elektronen im Plasma kollidieren mit den neutralen Gasatomen, ionisieren diese und erzeugen eine Glimmentladung.
-
Ionenbeschuss:
- Die positiv geladenen Ionen aus dem Plasma werden in Richtung des negativ geladenen Ziels beschleunigt. Wenn diese Ionen mit dem Ziel kollidieren, übertragen sie ihre Energie, wodurch Atome oder Moleküle aus der Zieloberfläche herausgeschleudert werden. Dieser Vorgang wird als Sputtern bezeichnet.
-
Abscheidung dünner Filme:
- Die ausgestoßenen Zielatome wandern durch die Vakuumkammer und lagern sich auf dem Substrat ab, wodurch ein dünner Film entsteht. Der Abscheidungsprozess ist streng kontrolliert und ermöglicht die Herstellung von Filmen mit spezifischen Eigenschaften wie Dicke, Gleichmäßigkeit und Haftung.
-
Magnetronsputtern:
- In einigen Fällen wird ein Magnetfeld angelegt, um den Sputterprozess zu verstärken. Dies wird als Magnetronsputtern bezeichnet. Das Magnetfeld begrenzt das Plasma in der Nähe der Targetoberfläche und erhöht so die Ionisierungseffizienz und die Sputterrate. Diese Methode führt im Vergleich zu herkömmlichen Sputtertechniken zu dichteren und konformeren Filmen.
-
HF-Sputtern:
- Zur Isolierung von Targetmaterialien wird RF-Sputtern (Radiofrequenz) eingesetzt. Bei dieser Methode wird eine HF-Stromquelle verwendet, um die Gasatome zu ionisieren. Das HF-Feld ändert die Polarität des Targets und verhindert so den Ladungsaufbau auf der Targetoberfläche, der beim DC-Sputtern auftreten kann. Dies ermöglicht das Sputtern nichtleitender Materialien.
-
Temperaturkontrolle:
- Die Kammer wird häufig auf Temperaturen zwischen 150 °C und 750 °C erhitzt, um die Qualität des abgeschiedenen Films zu verbessern. Durch Erhitzen kann die Haftung des Films am Substrat verbessert und Restspannungen innerhalb des Films verringert werden.
-
Endgültige Filmeigenschaften:
- Der Sputterprozess ermöglicht eine präzise Kontrolle der Eigenschaften des abgeschiedenen Films, einschließlich Korngröße, Rauheit und Stöchiometrie. Dies macht das Sputtern zu einer idealen Wahl für Anwendungen, bei denen hochwertige Dünnfilme erforderlich sind, beispielsweise in der Halbleiterfertigung, bei optischen Beschichtungen und Schutzbeschichtungen.
Durch die Befolgung dieser Schritte ermöglicht der Sputterprozess die Herstellung hochwertiger dünner Filme mit kontrollierten Eigenschaften, was ihn zu einer vielseitigen und weit verbreiteten Technik in verschiedenen industriellen Anwendungen macht.
Übersichtstabelle:
Schritt | Beschreibung |
---|---|
Aufbau der Vakuumkammer | Legen Sie Ziel und Substrat in eine Vakuumkammer und evakuieren Sie sie, um Verunreinigungen zu entfernen (ca. 1 Pa). |
Einführung von Inertgasen | Führen Sie Inertgas (z. B. Argon) ein, um eine Kontamination zu verhindern. |
Plasmaerzeugung | Legen Sie Hochspannung an, um ein Plasma zu erzeugen und Gasatome zum Sputtern zu ionisieren. |
Ionenbeschuss | Positiv geladene Ionen kollidieren mit dem Ziel und schleudern Atome aus. |
Dünnschichtabscheidung | Ausgeschleuderte Atome lagern sich auf dem Substrat ab und bilden einen kontrollierten dünnen Film. |
Magnetronsputtern | Verwenden Sie ein Magnetfeld, um den Plasmaeinschluss und die Sputtereffizienz zu verbessern. |
HF-Sputtern | Legen Sie HF-Energie für Isoliermaterialien an, um einen Ladungsaufbau zu verhindern. |
Temperaturkontrolle | Wärmekammer (150 °C–750 °C), um die Folienhaftung zu verbessern und Stress zu reduzieren. |
Endgültige Filmeigenschaften | Erzielen Sie eine präzise Kontrolle über Korngröße, Rauheit und Stöchiometrie für hochwertige Filme. |
Benötigen Sie Hilfe bei Sputtergeräten oder -prozessen? Kontaktieren Sie noch heute unsere Experten für maßgeschneiderte Lösungen!