Die Kalzinierung ist ein thermischer Behandlungsprozess, der dazu dient, eine thermische Zersetzung, einen Phasenübergang oder die Entfernung flüchtiger Bestandteile bei hohen Temperaturen zu bewirken. Die für die Kalzinierung verwendeten Öfen sind speziell für hohe Temperaturen und eine gleichmäßige Erwärmung ausgelegt, was für das Erreichen der gewünschten chemischen oder physikalischen Veränderungen entscheidend ist. Auf der Grundlage der angegebenen Referenzen werden folgende Öfen am häufigsten für die Kalzinierung verwendet muffelöfen , flammofenanlagen , schachtöfen und brennöfen . Die Auswahl dieser Öfen richtet sich nach dem zu verarbeitenden Material, dem Umfang des Betriebs (Labor oder Industrie) und den spezifischen Temperaturanforderungen. Im Folgenden werden die wichtigsten Punkte im Zusammenhang mit Kalzinierungsöfen ausführlich erläutert.
Die wichtigsten Punkte werden erklärt:
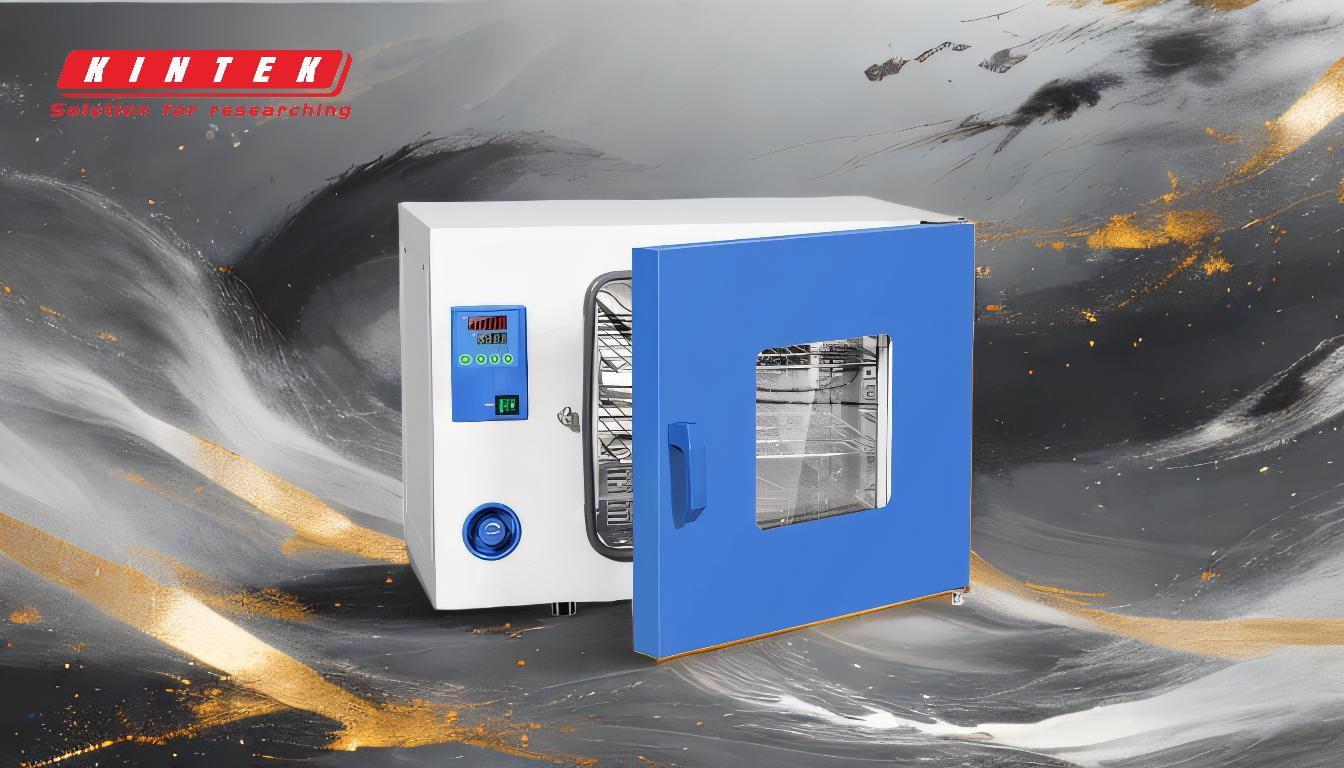
-
Arten von Öfen für die Kalzinierung:
- Muffelöfen: Diese Geräte sind sowohl im Labor als auch in der Industrie weit verbreitet. Sie verfügen über eine von Heizelementen umgebene Kammer, die eine gleichmäßige Temperaturverteilung gewährleistet. Muffelöfen sind ideal für die Kalzinierung, da sie eine Kontamination des zu verarbeitenden Materials verhindern, indem sie es von den Verbrennungsgasen isolieren.
- Hallraumöfen: Diese Öfen sind für großtechnische Anwendungen konzipiert. Sie verwenden eine Flamme, um das Material indirekt zu erhitzen, wobei die Hitze von den Ofenwänden reflektiert wird. Diese Konstruktion eignet sich für das Kalzinieren von Materialien wie Erzen und Mineralien.
- Schachtöfen: Schachtöfen werden in der Regel für kontinuierliche Kalzinierungsprozesse verwendet und sind vertikale Bauwerke, in denen sich das Material während der Erhitzung nach unten bewegt. Sie sind effizient für die Verarbeitung großer Mengen von Materialien, wie Kalkstein oder Zementklinker.
- Brennöfen: Brennöfen sind vielseitig einsetzbar und können für die Kalzinierung in Branchen wie der Keramik- und Zementherstellung verwendet werden. Sie arbeiten bei hohen Temperaturen und können je nach Anwendung als rotierende oder stationäre Einheiten konzipiert werden.
-
Hauptmerkmale von Kalzinierungsöfen:
- Hochtemperaturtauglichkeit: Die Kalzinierung erfordert in der Regel Temperaturen von 500°C bis über 1000°C. Die für diesen Prozess verwendeten Öfen müssen in der Lage sein, diese Temperaturen konstant zu halten.
- Einheitliche Heizung: Um eine vollständige und gleichmäßige Kalzinierung zu gewährleisten, ist eine gleichmäßige Temperaturverteilung entscheidend. Öfen wie Muffel- und Flammöfen sind darauf ausgelegt, dies zu erreichen.
- Kontrollierte Atmosphäre: Einige Kalzinierungsverfahren erfordern eine bestimmte Atmosphäre (z. B. inert oder oxidierend). Muffelöfen zum Beispiel können versiegelt werden, um die interne Umgebung zu kontrollieren.
- Langlebigkeit und Isolierung: Kalzinieröfen müssen über längere Zeit hohen Temperaturen und korrosiven Stoffen standhalten. Hochwertige Isoliermaterialien wie Keramikfasern werden häufig verwendet, um die Energieeffizienz und Haltbarkeit zu verbessern.
-
Industrielle Verwendung vs. Labor:
- Industrieöfen: Industrielle Kalzinieröfen, wie z. B. die Trommel- und Schachtöfen, sind für die Produktion in großen Mengen ausgelegt. Sie sind robust, energieeffizient und für einen hohen Durchsatz geeignet.
- Laboröfen: Muffelöfen werden häufig in Labors für Kalzinierungsversuche in kleinem Maßstab verwendet. Sie bieten eine präzise Temperaturregelung und sind kompakt, wodurch sie sich für Forschung und Entwicklung eignen.
-
Anwendungen von Kalzinieröfen:
- Zementherstellung: Die Kalzinierung von Kalkstein zur Herstellung von Kalk ist ein wichtiger Schritt bei der Zementherstellung. Zu diesem Zweck werden in der Regel Schacht- und Drehrohröfen verwendet.
- Metallverarbeitung: Die Kalzinierung dient der Entfernung von Verunreinigungen aus Metallerzen. In diesem Industriezweig werden häufig Flammöfen eingesetzt.
- Keramik und Glas: Brennöfen werden zum Kalzinieren von Rohstoffen wie Ton und Kieselerde verwendet, die für die Keramik- und Glasherstellung unerlässlich sind.
- Chemische Industrie: Die Kalzinierung wird zur Herstellung von Chemikalien wie Tonerde und Titandioxid verwendet. Muffelöfen werden häufig in Laboratorien eingesetzt, um diese Verfahren zu entwickeln und zu testen.
-
Vorteile der verschiedenen Ofentypen:
- Muffelöfen: Durch die geschlossene Bauweise ideal für kleine und kontaminationsanfällige Prozesse.
- Hallraumöfen: Geeignet für Großbetriebe und Materialien, die eine indirekte Beheizung erfordern.
- Schachtöfen: Effizient für kontinuierliche Verarbeitung und Großserienproduktion.
- Brennöfen: Vielseitig und anpassungsfähig an verschiedene Materialien und Branchen.
-
Überlegungen zur Auswahl eines Kalzinierofens:
- Materialeigenschaften: Die Art des zu kalzinierenden Materials (z. B. thermische Stabilität, Partikelgröße) beeinflusst die Wahl des Ofens.
- Temperaturanforderungen: Der Ofen muss in der Lage sein, die erforderliche Kalzinierungstemperatur zu erreichen und zu halten.
- Umfang der Tätigkeit: Prozesse im industriellen Maßstab erfordern robuste Öfen mit hoher Kapazität, während Prozesse im Labormaßstab von präzisen und kompakten Designs profitieren.
- Energie-Effizienz: Die Konstruktion und die Isolierung des Ofens sollten den Energieverbrauch minimieren, vor allem bei großen Anlagen.
- Auswirkungen auf die Umwelt: Elektroöfen werden dort bevorzugt, wo die Reduzierung von Emissionen eine Priorität ist.
Zusammenfassend lässt sich sagen, dass die Wahl des Ofens für die Kalzinierung von der spezifischen Anwendung, den Materialeigenschaften und der Betriebsgröße abhängt. Muffel-, Flamm- und Schachtöfen sowie Brennöfen sind die am häufigsten verwendeten Typen, die jeweils einzigartige Vorteile für verschiedene Kalzinierungsverfahren bieten. Das Verständnis der wichtigsten Merkmale und Anwendungen dieser Öfen ist für die Auswahl der richtigen Anlage für Ihre Bedürfnisse von entscheidender Bedeutung.
Zusammenfassende Tabelle:
Typ des Ofens | Wesentliche Merkmale | Anwendungen |
---|---|---|
Muffelofen | Gleichmäßige Erwärmung, kontaminationsfrei, präzise Temperaturregelung | Laborforschung, Kalzinierung im kleinen Maßstab, chemische Verarbeitung |
Hallraumofen | Indirekte Heizung, großflächige, robuste Bauweise | Verarbeitung von Metallerzen, industrielle Kalzinierung |
Schachtofen | Kontinuierliche Verarbeitung, hoher Durchsatz, vertikale Bauweise | Zementherstellung, Kalzinierung von Kalkstein |
Brennofen | Vielseitig, Hochtemperatur, rotierende oder stationäre Ausführung | Keramik, Glasherstellung, Zementherstellung |
Benötigen Sie Hilfe bei der Auswahl des richtigen Kalzinierungsofens für Ihre Anwendung? Kontaktieren Sie unsere Experten noch heute für eine persönliche Beratung!