Sintern ist ein kritischer thermischer Prozess, der dazu dient, pulverförmige Materialien in feste, zusammenhängende Strukturen umzuwandeln, ohne das Primärmaterial zu schmelzen. Es umfasst drei Hauptschritte: Formen des Pulvers zu einem „grünen“ Teil, Erhitzen, um Bindemittel zu entfernen und Partikel zu verschmelzen, und Abkühlen, um das Endprodukt zu erhalten. Der Prozess erfolgt in speziellen Geräten wie a Sinterofen , wo die Temperaturkontrolle entscheidend ist, um die Partikelbindung durch Diffusion sicherzustellen. Durch Sintern werden die Materialeigenschaften verbessert, die Porosität verringert und die gewünschte mechanische Festigkeit und Maßhaltigkeit erreicht. Das Verfahren wird in Branchen wie Metallurgie, Keramik und Fertigung häufig zur Herstellung komplexer Hochleistungskomponenten eingesetzt.
Wichtige Punkte erklärt:
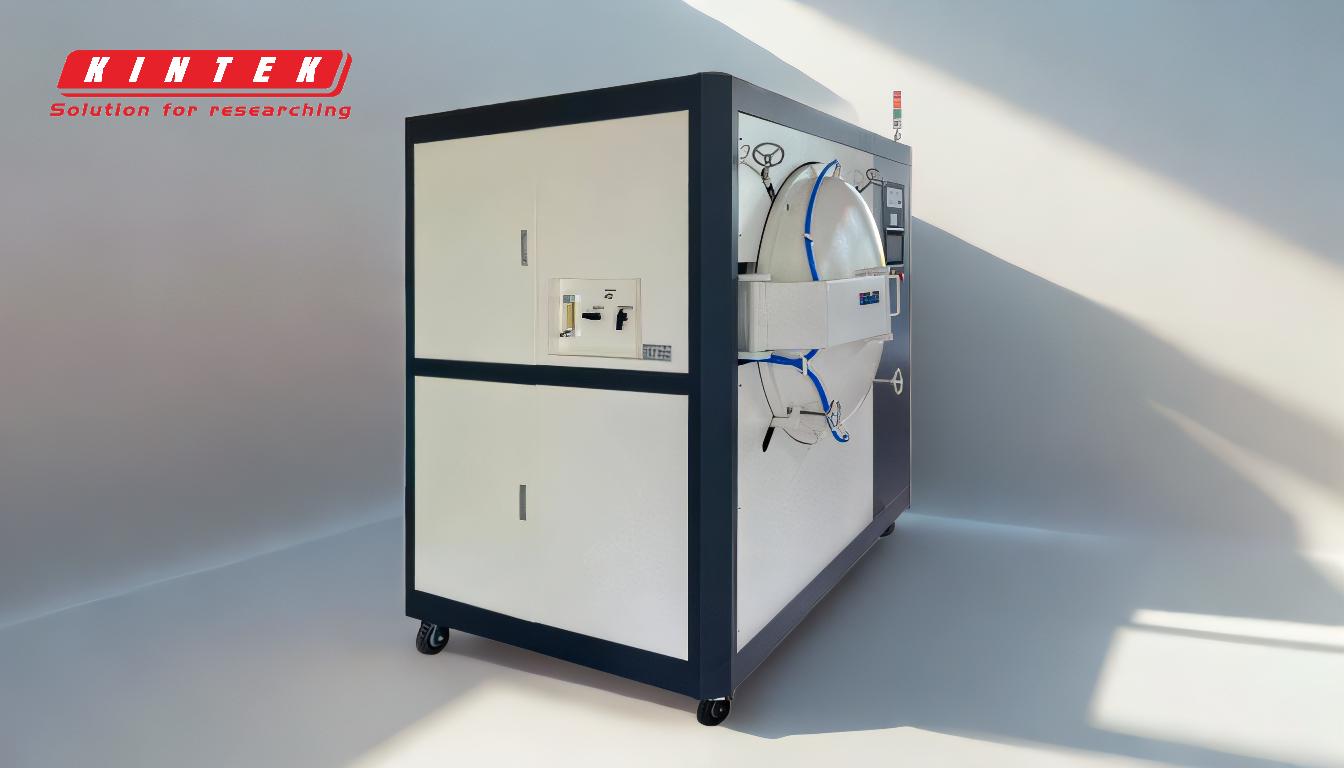
-
Bildung des Grünen Teils:
- Der Prozess beginnt mit einer Pulvermischung, oft gemischt mit einem Bindemittel (z. B. Wasser, Wachs oder Polymer), die in eine bestimmte Form verdichtet wird. Dieser „grüne“ Teil ist schwach und überdimensioniert, behält aber die gewünschte Form.
- Das Bindemittel sorgt in dieser Anfangsphase dafür, dass die Pulverpartikel aneinander haften.
-
Erhitzen und Entfernen von Bindemitteln:
- Der grüne Teil wird in a gelegt Sinterofen und erhitzt, um das Bindemittel zu entfernen. Dies geschieht in der Vorheizzone des Ofens, wo die Temperaturen hoch genug sind, um das Bindemittel zu verdampfen oder wegzubrennen.
- Diese Phase ist entscheidend für die Entfernung organischer Materialien und Schmierstoffe und stellt sicher, dass das Teil für die Partikelverschmelzung bereit ist.
-
Partikelfusion und -verdichtung:
- In der Sinterzone wird die Temperatur auf ein Niveau knapp unter dem Schmelzpunkt des Primärmaterials erhöht. Dadurch können sich Partikel durch Festkörperdiffusion verbinden und zwischen ihnen Hälse bilden.
- Die Partikel verschmelzen an ihren Oberflächen, wodurch die Porosität verringert und die Dichte erhöht wird. In einigen Fällen kann ein Zwischenbindemittel (z. B. Bronze) schmelzen und die Partikel verbinden, ohne das Primärmaterial zu verändern.
-
Kühlung und Endeigenschaften:
- Nach dem Sintern gelangt das Teil in die Kühlzone, wo eine kontrollierte Abkühlung die Struktur verfestigt und die mechanischen Eigenschaften verbessert.
- In dieser Phase kommt es zu einer Schrumpfung, die dem Teil seine endgültigen Abmessungen verleiht. Die Abkühlgeschwindigkeit kann angepasst werden, um Eigenschaften wie Härte und Festigkeit fein abzustimmen.
-
Arten von Sinteröfen:
- Periodische Öfen: Diese Öfen verarbeiten Teile in Chargen mit kontrollierten Heiz- und Kühlzyklen.
- Tunnelöfen: Teile bewegen sich kontinuierlich durch verschiedene Temperaturzonen (Vorwärmen, Sintern und Abkühlen), wodurch sie für die Massenproduktion geeignet sind.
-
Vorteile des Sinterns:
- Produziert komplexe, hochfeste Teile mit minimalem Materialabfall.
- Verbessert Materialeigenschaften wie Dichte, Festigkeit und Verschleißfestigkeit.
- Ermöglicht eine präzise Kontrolle der Abmessungen und mechanischen Eigenschaften.
-
Anwendungen des Sinterns:
- Wird häufig in der Metallurgie zur Herstellung von Metallkomponenten wie Zahnrädern, Lagern und Filtern verwendet.
- Unverzichtbar in der Keramikherstellung zur Herstellung langlebiger, hitzebeständiger Produkte.
- Wird in der Pulvermetallurgie zur Herstellung komplexer Teile mit maßgeschneiderten Eigenschaften eingesetzt.
Durch das Verständnis dieser Phasen und Mechanismen können Hersteller den Sinterprozess optimieren, um hochwertige, kostengünstige Komponenten für verschiedene industrielle Anwendungen herzustellen.
Übersichtstabelle:
Bühne | Beschreibung |
---|---|
Bildung des grünen Teils | Die Pulvermischung wird mit einem Bindemittel zu einer Form verdichtet. |
Erhitzen und Entfernen von Bindemitteln | Der grüne Teil wird erhitzt, um Bindemittel zu entfernen und ihn so für die Partikelverschmelzung vorzubereiten. |
Teilchenfusion | Partikel verbinden sich durch Diffusion, wodurch die Porosität verringert und die Dichte erhöht wird. |
Abkühlung und Finalisierung | Durch kontrollierte Abkühlung verfestigt sich die Struktur und erreicht ihre endgültigen Abmessungen. |
Arten von Öfen | Beschreibung |
Periodische Öfen | Chargenverarbeitung mit kontrollierten Heiz- und Kühlzyklen. |
Tunnelöfen | Kontinuierliche Verarbeitung durch Vorwärm-, Sinter- und Kühlzonen. |
Vorteile | Beschreibung |
Erweiterte Eigenschaften | Verbesserte Dichte, Festigkeit und Verschleißfestigkeit. |
Präzise Kontrolle | Maßgeschneiderte Abmessungen und mechanische Eigenschaften. |
Anwendungen | Beschreibung |
Metallurgie | Herstellung von Zahnrädern, Lagern und Filtern. |
Keramik | Schaffung langlebiger, hitzebeständiger Produkte. |
Pulvermetallurgie | Herstellung komplexer Teile mit maßgeschneiderten Eigenschaften. |
Optimieren Sie Ihren Sinterprozess mit fachkundiger Anleitung – Kontaktieren Sie uns noch heute !