Ein Vakuumsystem beim Sputtern ist eine wichtige Komponente, die eine Niederdruckumgebung in einer Vakuumkammer schafft und aufrechterhält. Diese Umgebung ist für das Sputtering-Verfahren, ein PVD-Verfahren (Physical Vapor Deposition) zur Abscheidung dünner Schichten auf Substraten, unerlässlich. Das Vakuumsystem stellt sicher, dass der Abscheidungsprozess frei von Verunreinigungen ist, ermöglicht den gesputterten Atomen den ungehinderten Übergang vom Target zum Substrat und erleichtert die Bildung eines Plasmas. Durch die Steuerung des Drucks ermöglicht das Vakuumsystem eine präzise und wiederholbare Abscheidung und gewährleistet so hochwertige, gleichmäßige und kontaminationsfreie dünne Schichten.
Die wichtigsten Punkte erklärt:
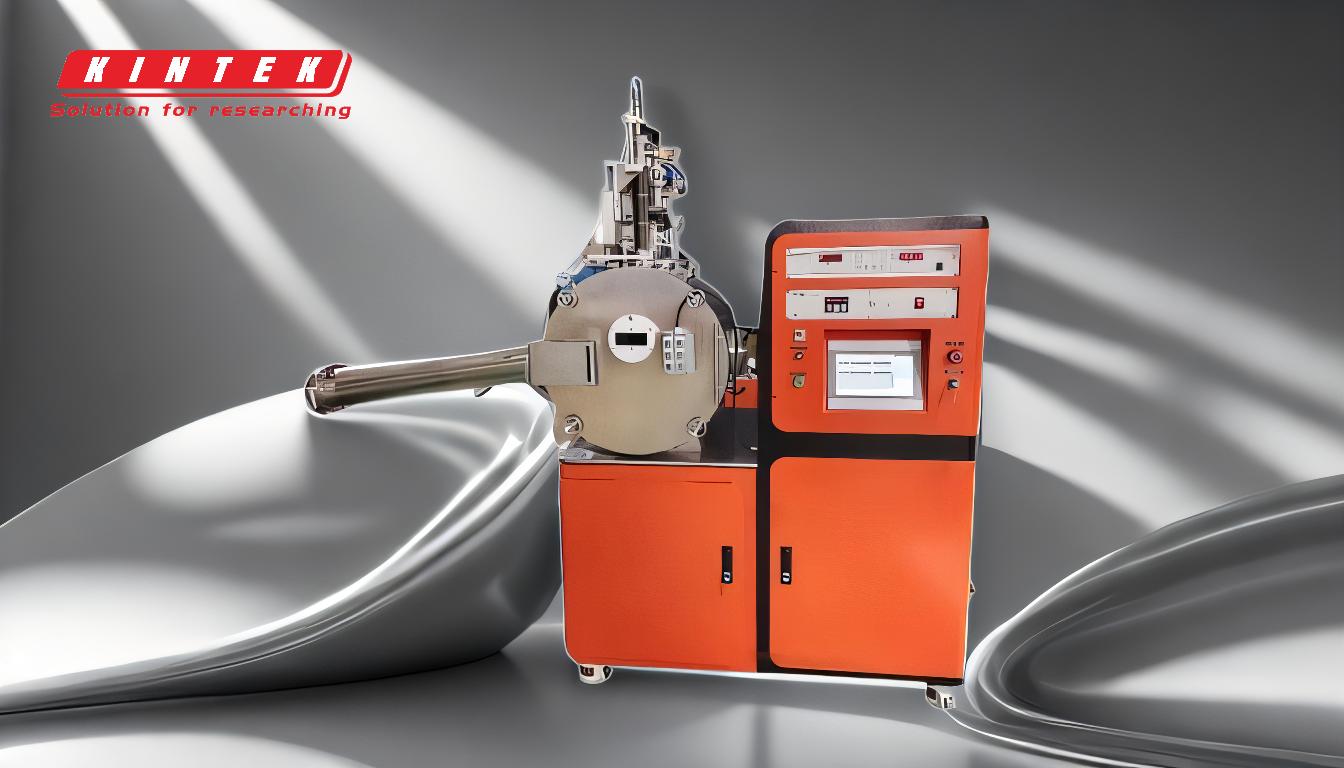
-
Zweck eines Vakuumsystems beim Sputtern:
- Das Vakuumsystem erzeugt in der Kammer eine Niederdruckumgebung, die für einen effektiven Sputterprozess erforderlich ist.
- Es sorgt dafür, dass das abzuscheidende Material nicht durch Luft oder andere Gase gebremst wird, so dass es das Substrat mit ausreichender Energie für eine starke Haftung erreichen kann.
- Das Vakuum minimiert die Verunreinigung durch externe Partikel und gewährleistet die Reinheit und Qualität der abgeschiedenen Schicht.
-
Die Rolle des Vakuums bei der Plasmabildung:
- Das Sputtern beruht auf der Bildung eines Plasmas, eines Gases aus ionisierten Atomen und Elektronen.
- Das Vakuumsystem hält den optimalen Druckbereich für die Plasmabildung aufrecht. Bei zu niedrigem Druck gibt es nicht genügend Kollisionen, um das Plasma aufrechtzuerhalten, während bei zu hohem Druck übermäßige Kollisionen verhindern, dass die Elektronen genug Energie erhalten, um die Atome effektiv zu ionisieren.
-
Verhinderung von Verunreinigungen:
- Eine Vakuumumgebung gewährleistet, dass der Sputterprozess steril und frei von Verunreinigungen bleibt.
- Verunreinigungen wie Staub, Feuchtigkeit oder Restgase können die Qualität der Dünnschicht beeinträchtigen und zu Defekten wie rauen Oberflächen, Ziellichtbögen oder Schichtversagen führen.
- Die Aufrechterhaltung einer sauberen Vakuumkammer und eines sauberen Sputtersystems ist entscheidend, um diese Probleme zu vermeiden.
-
Verlängern des mittleren freien Wegs:
- Die mittlere freie Weglänge ist die durchschnittliche Entfernung, die ein Teilchen zurücklegen kann, bevor es mit einem anderen Teilchen zusammenstößt.
- Im Vakuum verlängert sich die mittlere freie Weglänge der gesputterten Atome erheblich, so dass sie sich ohne Störungen vom Target zum Substrat bewegen können.
- Dies führt zu einer gleichmäßigeren und gleichmäßigeren Abscheidung der Dünnschicht.
-
Kontrollierte und wiederholbare Abscheidung:
- Das Vakuumsystem bietet eine kontrollierte Umgebung, die eine präzise Steuerung des Sputterprozesses ermöglicht.
- Durch die Aufrechterhaltung konstanter Druckniveaus gewährleistet das System wiederholbare Ergebnisse, was für industrielle Anwendungen, die hochwertige Dünnschichten erfordern, von entscheidender Bedeutung ist.
-
Komponenten eines Vakuumsystems:
- Vakuumpumpe: Entfernt Luft und andere Gase aus der Kammer, um die gewünschte Niederdruckumgebung zu erreichen.
- Vakuumkammer: Sie beherbergt den Sputterprozess und hält die Vakuumumgebung aufrecht.
- Druckmessgeräte und -steuerungen: Überwachen und regulieren den Druck in der Kammer, um optimale Bedingungen für das Sputtern zu gewährleisten.
- Inertgas-Versorgung: Führt Inertgase wie Argon in die Kammer ein, um die Plasmabildung und den Materialtransport zu erleichtern.
-
Wichtigkeit der Sauberkeit:
- Rückstände wie Schmieröl, Staub oder Vorbeschichtungsmaterialien können Feuchtigkeit und Verunreinigungen ansammeln und so das Risiko eines Filmausfalls erhöhen.
- Eine regelmäßige Reinigung der Vakuumkammer, der Sputterpistolen und der Targets ist unerlässlich, um Kurzschlüsse, Targetüberschläge und Oberflächenfehler zu vermeiden.
-
Anwendungen des Sputterns im Vakuum:
- Das Sputtern ist in Branchen wie der Halbleiterherstellung, der Optik und der dekorativen Beschichtung weit verbreitet.
- Das Vakuumsystem gewährleistet, dass die abgeschiedenen Schichten den strengen Reinheits- und Qualitätsanforderungen dieser Anwendungen entsprechen.
Zusammenfassend lässt sich sagen, dass ein Vakuumsystem beim Sputtern unverzichtbar ist, da es die kontrollierte Niederdruckumgebung schafft, die für einen effizienten Materialtransfer, die Plasmabildung und eine kontaminationsfreie Abscheidung erforderlich ist. Durch die Aufrechterhaltung des Vakuums auf einem bestimmten Niveau und die Sicherstellung der Sauberkeit des Systems können hochwertige dünne Schichten mit gleichmäßigen Eigenschaften zuverlässig hergestellt werden.
Zusammenfassende Tabelle:
Hauptaspekt | Beschreibung |
---|---|
Zweck | Schafft eine Niederdruckumgebung für effektives Sputtern und Materialtransfer. |
Plasma-Bildung | Hält den optimalen Druck für ein stabiles Plasma aufrecht, das für die Ionisierung von Atomen unerlässlich ist. |
Verhinderung von Verunreinigungen | Sorgt für eine sterile Umgebung und minimiert Verunreinigungen wie Staub und Feuchtigkeit. |
Mittlerer freier Weg | Verlängert die Bewegungsstrecke der Partikel und sorgt für eine gleichmäßige und glatte Schichtabscheidung. |
Kontrollierte Abscheidung | Ermöglicht präzise und wiederholbare Ergebnisse für hochwertige Dünnschichten. |
Bestandteile | Umfasst Vakuumpumpe, Kammer, Druckmessgeräte und Inertgasversorgung. |
Bedeutung der Sauberkeit | Regelmäßige Reinigung verhindert Defekte wie Target-Arcings und Filmversagen. |
Anwendungen | Einsatz in der Halbleiterfertigung, Optik und bei dekorativen Beschichtungen. |
Entdecken Sie, wie ein Vakuumsystem Ihren Sputtering-Prozess optimieren kann. Kontaktieren Sie unsere Experten noch heute !