Depositionsprozessgase sind für verschiedene Dünnschichtabscheidungstechniken wie Sputtern und chemische Gasphasenabscheidung (CVD) unerlässlich.Diese Gase erleichtern die Übertragung des Materials von einer Quelle auf ein Substrat, wo es eine feste Schicht bildet.Inerte Gase wie Argon werden häufig wegen ihrer Stabilität und effizienten Impulsübertragung verwendet, während reaktive Gase wie Stickstoff, Sauerstoff und Acetylen eingesetzt werden, um Verbindungen wie Oxide, Nitride und Karbide zu erzeugen.Die Wahl des Gases hängt vom Zielmaterial und den gewünschten Filmeigenschaften ab, wobei das Atomgewicht und die chemische Reaktivität zu berücksichtigen sind.Die Prozessgase werden sorgfältig kontrolliert und geliefert, um eine präzise und hochwertige Abscheidung zu gewährleisten.
Die wichtigsten Punkte erklärt:
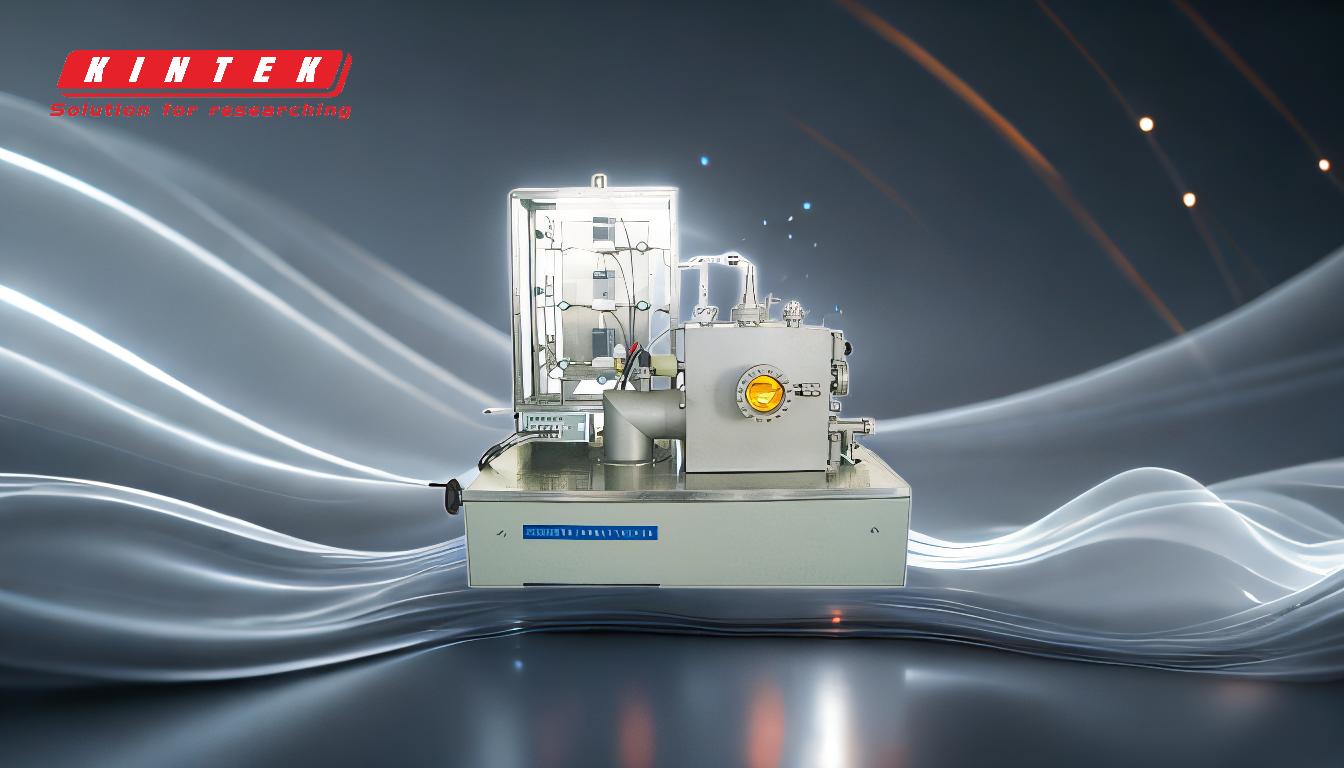
-
Definition von Depositionsprozessgasen:
- Abscheidungsprozessgase werden bei Techniken wie Sputtern und CVD verwendet, um Material von einer Quelle auf ein Substrat zu übertragen und eine feste Schicht zu bilden.
- Diese Gase können inert (z. B. Argon) oder reaktiv (z. B. Stickstoff, Sauerstoff) sein, je nach Anwendung.
-
Inerte Gase in der Abscheidung:
- Argon:Das am häufigsten verwendete Inertgas aufgrund seiner Stabilität und seiner effizienten Impulsübertragung.
- Neon, Krypton, Xenon:Die Verwendung richtet sich nach dem Atomgewicht des Zielmaterials.Neon wird für leichte Elemente bevorzugt, während Krypton und Xenon für schwere Elemente verwendet werden.
- Rolle:Inerte Gase wie Argon werden zum Sputtern von Zielmaterialien verwendet, indem sie einen Impuls übertragen, der sicherstellt, dass das Material herausgeschleudert wird und sich auf dem Substrat ablagert.
-
Reaktive Gase bei der Abscheidung:
- Stickstoff (N₂):Zur Bildung von Nitriden, wie Titannitrid (TiN), die hart und verschleißfest sind.
- Sauerstoff (O₂):Wird zur Herstellung von Oxiden wie Aluminiumoxid (Al₂O₃) verwendet, die häufig wegen ihrer isolierenden Eigenschaften eingesetzt werden.
- Acetylen (C₂H₂) und Methan (CH₄):Zur Abscheidung von Karbidschichten, wie z. B. Siliziumkarbid (SiC), die für ihre Härte und thermische Stabilität bekannt sind.
- Wasserstoff (H₂):Wird häufig in CVD-Verfahren zur Reduktion von Oxiden oder als Trägergas verwendet.
- Rolle:Reaktive Gase gehen mit dem Zielmaterial oder den ausgestoßenen Partikeln eine chemische Wechselwirkung ein und bilden Verbindungen auf dem Substrat.
-
Kriterien für die Gasauswahl:
- Atomarer Gewichtsabgleich:Das Atomgewicht des Sputtergases sollte nahe an dem des Zielmaterials liegen, um einen effizienten Impulstransfer zu gewährleisten.So wird beispielsweise Neon für leichte Elemente verwendet, während Krypton oder Xenon für schwere Elemente eingesetzt werden.
- Chemische Reaktivität:Die reaktiven Gase werden je nach der gewünschten chemischen Zusammensetzung der abgeschiedenen Schicht ausgewählt.So wird beispielsweise Sauerstoff zur Bildung von Oxiden und Stickstoff zur Bildung von Nitriden verwendet.
- Anforderungen an den Prozess:Die Wahl des Gases hängt auch von der jeweiligen Abscheidungstechnik (z. B. Sputtern oder CVD) und den gewünschten Schichteigenschaften (z. B. Leitfähigkeit, Härte, optische Eigenschaften) ab.
-
Prozessgaszufuhr und -steuerung:
- Gasflaschen:Die Gase werden in der Regel aus Hochdruckflaschen zugeführt und vor dem Eintritt in die Beschichtungskammer geregelt.
- Ventile und Messgeräte:Der Gasfluss wird mit Hilfe von Ventilen und Durchflussmessern präzise gesteuert, um gleichbleibende und reproduzierbare Ablagerungsbedingungen zu gewährleisten.
- Vakuum-Umgebung:Abscheidungsprozesse finden häufig in einer Vakuumkammer statt, um die Kontamination zu minimieren und die Gasumgebung zu kontrollieren.
-
Anwendungen von Abscheidungsprozessgasen:
- Sputtern:Inerte Gase wie Argon werden zum Sputtern von Metallen und Legierungen verwendet, während reaktive Gase zur Abscheidung von Verbindungen wie Oxiden, Nitriden und Karbiden eingesetzt werden.
- Chemische Gasphasenabscheidung (CVD):Reaktive Gase wie Sauerstoff, Wasserstoff und Methan werden verwendet, um dünne Schichten aus verschiedenen Materialien abzuscheiden, darunter Siliziumdioxid (SiO₂) und Siliziumkarbid (SiC).
- Niederdruck-CVD (LPCVD):Gase wie Sauerstoff, Schwefel und Wasserstoff werden erhitzt und verdampft, um dünne Schichten auf Substraten abzuscheiden, die häufig bei der Halbleiterherstellung verwendet werden.
-
Die Bedeutung der Gasreinheit:
- Hochreine Gase sind entscheidend, um Verunreinigungen zu vermeiden und die Qualität der abgeschiedenen Schicht zu gewährleisten.Verunreinigungen können zu Defekten, verminderter Leistung oder zum Ausfall des Endprodukts führen.
- Die Reinheit der Gase ist besonders wichtig bei Halbleiter- und optischen Beschichtungsanwendungen, wo selbst Spuren von Verunreinigungen die Leistung der Geräte erheblich beeinträchtigen können.
Zusammenfassend lässt sich sagen, dass Prozessgase bei der Abscheidung von Dünnschichten eine entscheidende Rolle spielen. Inerte Gase wie Argon sorgen für einen effizienten Materialtransfer und reaktive Gase ermöglichen die Bildung komplexer Verbindungen.Die Auswahl und Steuerung dieser Gase ist entscheidend, um qualitativ hochwertige, funktionelle Schichten für ein breites Spektrum von Anwendungen zu erzielen.
Zusammenfassende Tabelle:
Kategorie | Einzelheiten |
---|---|
Inertgase | Argon, Neon, Krypton, Xenon - Für eine effiziente Impulsübertragung beim Sputtern. |
Reaktive Gase | Stickstoff (N₂), Sauerstoff (O₂), Acetylen (C₂H₂), Methan (CH₄) - Bilden Oxide, Nitride, Karbide. |
Kriterien für die Gasauswahl | Übereinstimmung mit dem Atomgewicht, chemische Reaktivität und Prozessanforderungen. |
Anwendungen | Sputtern, CVD, LPCVD - Einsatz in der Halbleiter- und optischen Beschichtungsindustrie. |
Die Bedeutung der Reinheit | Hochreine Gase gewährleisten kontaminationsfreie, leistungsstarke Dünnschichten. |
Optimieren Sie Ihren Dünnschichtabscheidungsprozess mit den richtigen Gasen - Kontaktieren Sie unsere Experten noch heute !