Kalzinieren und Sintern sind beides thermische Verfahren, die in der Metallurgie und der Werkstoffkunde eingesetzt werden, aber sie dienen unterschiedlichen Zwecken und arbeiten unter verschiedenen Bedingungen.Beim Kalzinieren wird ein Material, in der Regel Metallerz, in Gegenwart von Luft oder Sauerstoff erhitzt, um Verunreinigungen wie Kohlenstoff, Wasser oder andere flüchtige Stoffe zu entfernen.Beim Sintern hingegen werden pulverförmige Metall- oder Keramikmaterialien unter ihren Schmelzpunkt erhitzt, um die Partikel miteinander zu verschmelzen und einen festen Gegenstand mit verbesserten mechanischen Eigenschaften zu schaffen.Obwohl beide Verfahren bei Temperaturen unterhalb des Schmelzpunkts des Materials ablaufen, unterscheiden sich ihre Ziele und Ergebnisse erheblich.Das Kalzinieren ist in erster Linie ein Reinigungsprozess, während das Sintern ein Verfestigungsprozess ist, der die Festigkeit und Integrität des Materials verbessern soll.
Die wichtigsten Punkte werden erklärt:
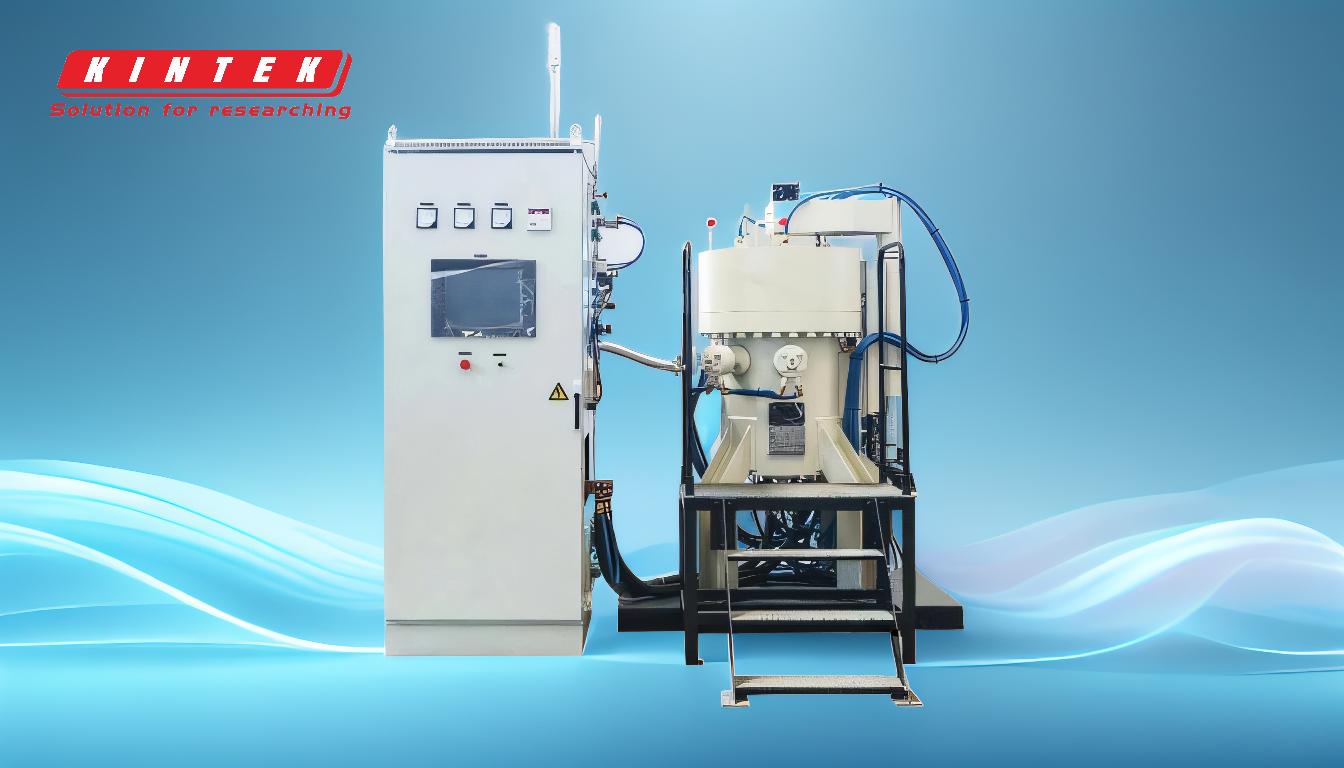
-
Definition und Zweck:
- Kalzinierung:Ein thermisches Verfahren, bei dem ein Material (in der Regel Metallerze) in Gegenwart von Luft oder Sauerstoff erhitzt wird, um Verunreinigungen wie Kohlenstoff, Wasser oder andere flüchtige Verbindungen zu entfernen.Das Ziel ist die Reinigung.
- Sintern:Ein thermisches Verfahren, bei dem pulverförmige Metall- oder Keramikmaterialien unter ihren Schmelzpunkt erhitzt werden, um die Partikel miteinander zu verschmelzen und einen festen Gegenstand zu bilden.Das Ziel ist die Verfestigung und Verbesserung der Materialeigenschaften.
-
Temperaturbereich:
- Beide Verfahren finden bei Temperaturen unterhalb des Schmelzpunkts des zu verarbeitenden Materials statt.
- Beim Kalzinieren herrschen in der Regel niedrigere Temperaturen als beim Sintern, da das primäre Ziel darin besteht, Verunreinigungen abzutreiben und nicht Partikel zu verschmelzen.
-
Chemische vs. physikalische Veränderungen:
- Kalzinierung:Es handelt sich in erster Linie um chemische Veränderungen, wie die Zersetzung von Karbonaten oder die Oxidation von Verunreinigungen.
- Sintern:Es handelt sich in erster Linie um physikalische Veränderungen, bei denen sich die Teilchen durch Diffusion und Kornwachstum ohne Schmelzen verbinden.
-
Anwendungen:
- Kalzinierung:Wird häufig bei der Herstellung von Zement, Kalk und Tonerde verwendet, wo Verunreinigungen entfernt werden müssen, um die gewünschte chemische Zusammensetzung zu erreichen.
- Sintern:Weit verbreitet in der Pulvermetallurgie und Keramik zur Herstellung von Bauteilen mit hoher Festigkeit, Dichte und Maßhaltigkeit.
-
Ausrüstung:
- Kalzinierofen:Konzipiert für die kontrollierte Erhitzung in einer oxidierenden Atmosphäre, oft mit Funktionen zur Kontrolle von Abgasen und Verunreinigungen.
- Sinterofen:Ausgelegt für gleichmäßige Erwärmung und kontrollierte Abkühlung, oft mit Funktionen zur Aufrechterhaltung einer bestimmten Atmosphäre (z. B. Inertgas), um Oxidation oder Kontamination zu verhindern.
-
Ergebnis:
- Kalzinierung:Das Ergebnis ist ein gereinigtes Material mit einem geringeren Gehalt an Verunreinigungen, oft in einem brüchigeren oder poröseren Zustand.
- Sintern:Das Ergebnis ist ein dichtes, festes Objekt mit verbesserten mechanischen Eigenschaften wie Festigkeit, Härte und Verschleißfestigkeit.
-
Zustand des Materials:
- Kalzinierung:Ausgangspunkt ist in der Regel ein Schüttgut oder Erz, das vor dem Erhitzen zerkleinert oder gemahlen werden kann.
- Sintern:Beginnt mit pulverförmigem Material, das vor dem Erhitzen in die gewünschte Form gepresst wird.
-
Atmosphärenkontrolle:
- Kalzinierung:Erfordert oft eine oxidierende Atmosphäre, um die Entfernung von Verunreinigungen zu erleichtern.
- Sintern:Erfordert möglicherweise eine kontrollierte Atmosphäre (z. B. Inertgas oder Vakuum), um Oxidation oder Verunreinigung während des Klebevorgangs zu verhindern.
-
Nachbearbeitung:
- Kalzinierung:Das entstandene Material muss je nach Anwendung zusätzlich bearbeitet werden, z. B. durch Mahlen oder weitere Veredelung.
- Sintern:Das gesinterte Produkt ist oft nahezu endkonturiert und erfordert nur eine minimale Nachbearbeitung, wie z. B. eine maschinelle Bearbeitung oder Oberflächenveredelung.
-
Relevanz für die Industrie:
- Kalzinierung:Entscheidend in Branchen wie der Zementherstellung, der Metallraffination und der chemischen Industrie.
- Sintern:Unverzichtbar in Branchen wie der Automobilindustrie, der Luft- und Raumfahrt und der Elektronik für die Herstellung von Hochleistungskomponenten.
Die Kenntnis dieser wichtigen Unterschiede hilft bei der Auswahl des geeigneten Verfahrens und der Ausrüstung für spezifische Materialverarbeitungsanforderungen und gewährleistet optimale Ergebnisse in Bezug auf Reinheit, Festigkeit und Funktionalität.
Zusammenfassende Tabelle:
Aspekt | Kalzinierung | Sintern |
---|---|---|
Zweck | Reinigung von Materialien durch Beseitigung von Verunreinigungen. | Verfestigung von pulverförmigen Materialien zur Verbesserung der Festigkeit und Integrität. |
Temperaturbereich | Niedrigere Temperaturen, unterhalb des Schmelzpunktes des Materials. | Höhere Temperaturen, immer noch unterhalb des Schmelzpunktes des Materials. |
Veränderungen | In erster Linie chemische Veränderungen (z. B. Zersetzung, Oxidation). | In erster Linie physikalische Veränderungen (z. B. Partikelbindung durch Diffusion). |
Anwendungen | Zement-, Kalk- und Tonerdeproduktion. | Pulvermetallurgie, Keramik, Automobilindustrie, Luft- und Raumfahrt und Elektronik. |
Ausrüstung | Kalzinierungsofen mit oxidierender Atmosphäre. | Sinterofen mit kontrollierter Atmosphäre (z. B. Inertgas oder Vakuum). |
Ergebnis | Gereinigtes Material mit weniger Verunreinigungen, oft porös. | Dichtes, festes Objekt mit verbesserten mechanischen Eigenschaften. |
Zustand des Materials | Beginnt mit Schüttgut oder Erz. | Beginnt mit pulverförmigem Material, das vor dem Erhitzen verdichtet wird. |
Atmosphärenkontrolle | Oxidierende Atmosphäre zur Entfernung von Verunreinigungen. | Kontrollierte Atmosphäre zur Vermeidung von Oxidation oder Verunreinigung. |
Nachbearbeitung | Kann Schleifen oder weitere Verfeinerung erfordern. | Oft nahezu endkonturiert, minimale Nachbearbeitung erforderlich. |
Relevanz für die Industrie | Zementherstellung, Metallveredelung, chemische Produktion. | Automobilindustrie, Luft- und Raumfahrt, Elektronik für Hochleistungskomponenten. |
Benötigen Sie Hilfe bei der Auswahl des richtigen Verfahrens oder der richtigen Ausrüstung für Ihre Materialverarbeitung? Kontaktieren Sie noch heute unsere Experten für eine persönliche Beratung!