Die Auswirkung des Drucks beim Sputtern ist ein entscheidender Faktor, der das Verhalten der gesputterten Ionen, die Energieverteilung der Quellatome und die Gesamtqualität der abgeschiedenen Schicht beeinflusst.Bei höherem Druck stoßen die Ionen mit den Gasatomen zusammen, was zu einer diffusiven Bewegung und einem "random walk" führt, was sich auf die Gleichmäßigkeit der Abscheidung und die Bedeckung auswirkt.Niedrigere Drücke hingegen ermöglichen hochenergetische ballistische Stöße, was zu einer direkteren und energiereicheren Abscheidung führt.Der Druck bestimmt auch die mittlere freie Weglänge der Ionen und wirkt sich auf ihre Energieverteilung und die Sputterausbeute aus, die je nach Zielmaterial und Sputterbedingungen variiert.Das Verständnis dieser Dynamik ist für die Optimierung von Sputterprozessen von entscheidender Bedeutung.
Die wichtigsten Punkte werden erklärt:
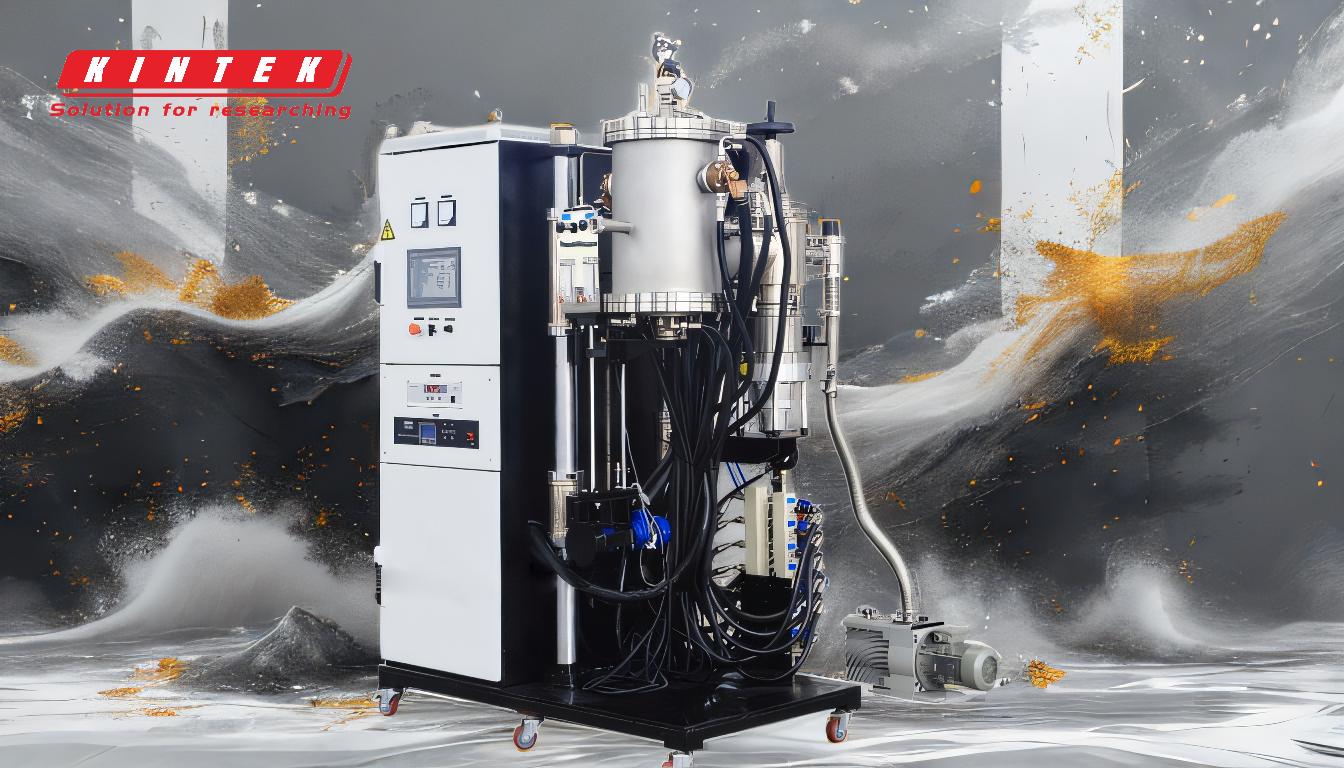
-
Einfluss des Drucks auf die Ionenbewegung:
- Höhere Drücke: Bei hohen Gasdrücken stoßen die gesputterten Ionen häufig mit Gasatomen zusammen.Diese Zusammenstöße wirken wie ein Moderator, der die Ionen dazu bringt, sich diffus zu bewegen.Dies führt zu einer Zufallsbewegung, bei der die Ionen einen längeren, weniger direkten Weg nehmen, um das Substrat oder die Kammerwände zu erreichen.Diese diffusive Bewegung kann die Gleichmäßigkeit der Bedeckung verbessern, kann aber die Energie der abgeschiedenen Partikel verringern.
- Niedrigere Drücke: Niedrigere Drücke hingegen reduzieren die Anzahl der Kollisionen zwischen Ionen und Gasatomen.Dadurch können sich die Ionen eher ballistisch fortbewegen, wobei sie höhere Energieniveaus beibehalten und direkter auf das Substrat auftreffen.Dies kann zu dichteren und besser haftenden Schichten führen, aber auch die Gleichmäßigkeit der Beschichtung beeinträchtigen.
-
Energieverteilung und mittlerer freier Weg:
- Mittlere freie Weglänge: Die mittlere freie Weglänge von Ionen ist die durchschnittliche Entfernung, die sie zwischen Kollisionen zurücklegen.Der Druck hat einen direkten Einfluss auf diesen Parameter; höhere Drücke verkürzen die mittlere freie Weglänge, während niedrigere Drücke sie verlängern.Eine kürzere mittlere freie Weglänge bei höherem Druck führt zu häufigeren Kollisionen und Energieverlusten, während eine längere mittlere freie Weglänge bei niedrigerem Druck es den Ionen ermöglicht, mehr Energie zu speichern, bis sie das Substrat erreichen.
- Energieverteilung: Die Energieverteilung der Quellatome wird durch den Druck bestimmt.Bei hyperthermischen Verfahren wie dem Sputtern spielt der Druck eine entscheidende Rolle bei der Bestimmung der Energieverteilung unter den gesputterten Atomen.Dies wirkt sich auf die Sputterausbeute und die Qualität der abgeschiedenen Schicht aus.
-
Sputtering-Ausbeute und Materialabhängigkeit:
- Sputtering-Ausbeute: Die Sputterausbeute, definiert als die Anzahl der pro einfallendem Ion ausgestoßenen Zielatome, wird durch den Druck beeinflusst.Höhere Drücke können die Sputterausbeute aufgrund von Energieverlusten durch Kollisionen verringern, während niedrigere Drücke die Ausbeute erhöhen können, da die Ionen mehr Energie speichern können.Die Ausbeute variiert auch je nach Targetmaterial und den spezifischen Sputterbedingungen.
- Materialkompatibilität: Verschiedene Materialien reagieren unterschiedlich auf Druckveränderungen.Einige Materialien benötigen beispielsweise höhere Drücke, um eine optimale Sputterausbeute zu erzielen, während andere bei niedrigeren Drücken besser abschneiden.Das Verständnis dieser materialspezifischen Verhaltensweisen ist entscheidend für die Optimierung des Sputterprozesses.
-
Abscheidequalität und Filmeigenschaften:
- Filmdichte und Adhäsion: Die kinetische Energie der emittierten Partikel, die durch den Druck beeinflusst wird, bestimmt deren Richtung und Ablagerung auf dem Substrat.Niedrige Drücke führen im Allgemeinen zu einer höheren kinetischen Energie, was zu dichteren und besser haftenden Schichten führt.Höhere Drücke können aufgrund von Energieverlusten durch Kollisionen zu weniger dichten Filmen führen.
- Oberflächenmobilität: Die überschüssige Energie der Metallionen kann die Oberflächenmobilität während des Abscheidungsprozesses erhöhen.Dies kann sich auf die Qualität der abgeschiedenen Schicht auswirken, da eine höhere Oberflächenmobilität zu glatteren und gleichmäßigeren Schichten führen kann.Der Druck spielt eine Rolle bei der Bestimmung des Ausmaßes dieser Oberflächenmobilität.
-
Prozessoptimierung und praktische Überlegungen:
- Druck und Temperatur: Bei der Optimierung des Sputterprozesses sollte neben der Abscheidetemperatur immer auch der Druck berücksichtigt werden.Die Wechselwirkung zwischen diesen beiden Parametern kann das Ergebnis der Abscheidung erheblich beeinflussen.
- Stromquelle: Die Art der beim Sputtern verwendeten Stromquelle (Gleichstrom oder Hochfrequenz) steht ebenfalls in Wechselwirkung mit dem Druck.So kann das HF-Sputtern bei niedrigerem Druck effektiver sein, während das DC-Sputtern bei höherem Druck besser funktioniert.Die Wahl der Stromquelle wirkt sich zusammen mit dem Druck auf die Abscheiderate, die Materialverträglichkeit und die Gesamtkosten des Verfahrens aus.
Zusammenfassend lässt sich sagen, dass der Druck ein grundlegender Parameter beim Sputtern ist, der die Ionenbewegung, die Energieverteilung, die Sputterausbeute und die Qualität der abgeschiedenen Schicht beeinflusst.Durch sorgfältige Steuerung des Drucks zusammen mit anderen Parametern wie Temperatur und Stromquelle kann der Sputterprozess optimiert werden, um die gewünschten Schichteigenschaften und Abscheideergebnisse zu erzielen.
Zusammenfassende Tabelle:
Aspekt | Höherer Druck | Niedrigerer Druck |
---|---|---|
Ionenbewegung | Diffusive Bewegung, random walk, verbesserte Gleichmäßigkeit der Abdeckung, geringere Energie | Ballistische Bewegung, direkte Stöße, höhere Energie, dichtere Filme |
Mittlerer freier Weg | Kürzer, häufige Kollisionen, Energieverlust | Länger, weniger Kollisionen, Energieerhalt |
Sputtering Ausbeute | Reduziert aufgrund von Energieverlusten | Verbessert durch erhaltene Energie |
Filmdichte und Haftung | Weniger dichte Filme aufgrund von Energieverlusten | Dichtere, stärker haftende Filme |
Oberflächenbeweglichkeit | Geringere Oberflächenbeweglichkeit, weniger gleichmäßige Filme | Höhere Oberflächenbeweglichkeit, glattere, gleichmäßigere Filme |
Prozess-Optimierung | Bessere Gleichmäßigkeit der Bedeckung, geringere Energie | Höhere Energie, dichtere Schichten, möglicherweise geringere Gleichmäßigkeit der Bedeckung |
Benötigen Sie Hilfe bei der Optimierung Ihres Sputtering-Prozesses? Kontaktieren Sie noch heute unsere Experten für maßgeschneiderte Lösungen!