Der Wirkungsgrad eines Drehrohrofens ist ein entscheidender Faktor für seinen Betrieb, insbesondere in Industrien, in denen Energieverbrauch und thermische Leistung eine wichtige Rolle spielen.Drehrohröfen werden häufig für Prozesse wie Schmelzen, Pyrolyse und Materialbehandlung eingesetzt, aber ihr Wirkungsgrad ist im Allgemeinen niedrig und liegt zwischen 23 % und 27,5 %.Dieser niedrige Wirkungsgrad ist in erster Linie auf den erheblichen Wärmeverlust durch die Abgase zurückzuführen, die Temperaturen zwischen 1100°C und 1315°C erreichen können.Fortschritte in der Misch- und Fördertechnik, wie z. B. der Einsatz archimedischer Schnecken, haben jedoch die Volumennutzung und die Wärmeübertragung verbessert und damit die Gesamteffizienz erhöht.Darüber hinaus spielen Faktoren wie Ofentemperatur, Verweilzeit und Druckregelung eine entscheidende Rolle bei der Optimierung der Leistung.Die Kombination von Drehrohröfen mit Wärmetauscheranlagen ist ein neuer Trend, der die Effizienz weiter verbessert und die Betriebskosten senkt.
Die wichtigsten Punkte erklärt:
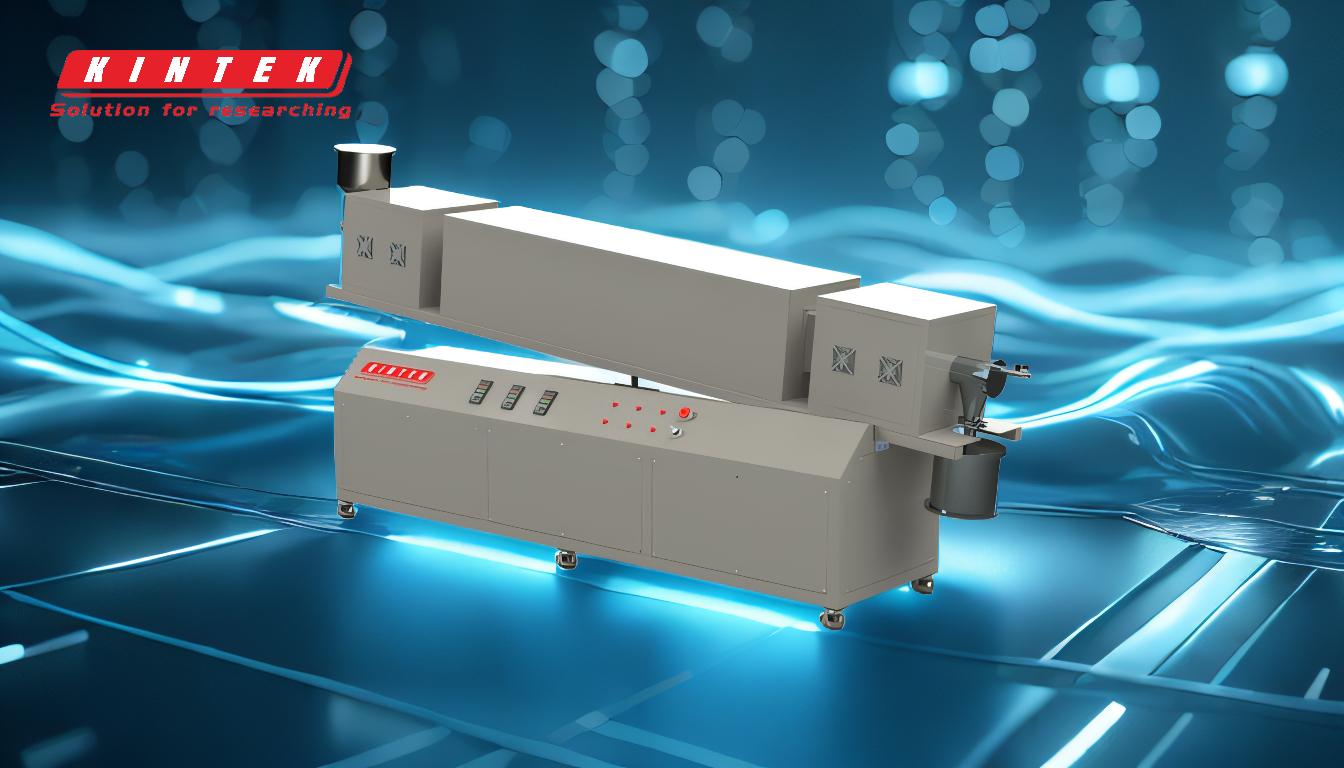
-
Thermischer Wirkungsgrad von Drehrohröfen:
- Drehrohröfen haben in der Regel einen thermischen Wirkungsgrad von 23 % bis 27,5 %, was im Vergleich zu anderen Industrieanlagen relativ niedrig ist.
- Ein erheblicher Teil der Wärme (50-70 %) geht durch die Abgase verloren, die den Ofen bei hohen Temperaturen (1100-1315 °C) verlassen.
- Dieser Wärmeverlust ist einer der Hauptgründe für den niedrigen Gesamtwirkungsgrad von Drehrohröfen.
-
Faktoren, die den Wirkungsgrad beeinflussen:
- Ofentemperatur:Die Betriebstemperatur des Ofens wirkt sich direkt auf die Effizienz aus.Höhere Temperaturen können die Reaktionsgeschwindigkeit verbessern, aber auch den Wärmeverlust erhöhen.
- Verweilzeit:Die Verweildauer der Materialien im Ofen wirkt sich auf die Vollständigkeit der Reaktionen aus.Eine ordnungsgemäße Steuerung der Verweilzeit gewährleistet eine optimale Wärmeübertragung und Reaktionseffizienz.
- Druck:Die internen Druckverhältnisse beeinflussen das Verhalten von Gasen und Materialien im Ofen und wirken sich auf die Wärmeverteilung und die Reaktionskinetik aus.
-
Technologischer Fortschritt:
- Mischen von Technologien:Innovationen wie die archimedischen Schnecken verbessern die Durchmischung und verkürzen die Zeit, die für Reaktionen mit begrenztem Wärme- und Stoffaustausch erforderlich ist.Dies verbessert die Volumennutzung und die Gesamteffizienz.
- Integration des Wärmeaustauschs:Die Kombination von Drehrohröfen mit Wärmetauschern ermöglicht die Rückgewinnung von Abwärme, was die Effizienz erhöht und den Energieverbrauch senkt.
-
Überlegungen zu Betrieb und Wartung:
- Ordnungsgemäßer Betrieb und Wartung sind für die Aufrechterhaltung der Effizienz unerlässlich.Durch regelmäßige Wartung wird sichergestellt, dass der Ofen unter optimalen Bedingungen arbeitet, wodurch die Energieverschwendung minimiert und die Lebensdauer der Anlage verlängert wird.
- Die Überwachung und Steuerung von Schlüsselparametern wie Temperatur, Verweilzeit und Druck sind entscheidend für eine hohe Effizienz.
-
Vorteile und Benachteiligungen:
- Vorteile:Drehrohröfen können minderwertigen Schrott und Krätze verarbeiten, die für andere Ofentypen schwierig sind.Dies macht sie vielseitig einsetzbar für verschiedene industrielle Anwendungen.
- Nachteile:Sie sind im Allgemeinen weniger effizient, erfordern einen höheren Wartungsaufwand und produzieren erhebliche Mengen an gefährlichen Abfällen (Salzkuchen), die ordnungsgemäß entsorgt werden müssen.
-
Aufkommende Trends:
- Es gibt einen wachsenden Trend zur Integration von Drehrohröfen mit fortschrittlichen Wärmeaustauschsystemen.Diese Kombination erhöht den Wirkungsgrad, senkt die Betriebskosten und ermöglicht kompaktere Ofenkonstruktionen.
Durch die Beschäftigung mit diesen Schlüsselpunkten können Betreiber die Faktoren, die die Effizienz von Drehrohröfen beeinflussen, besser verstehen und Strategien zur Optimierung ihrer Leistung umsetzen.
Zusammenfassende Tabelle:
Hauptaspekt | Einzelheiten |
---|---|
Thermischer Wirkungsgrad | 23% bis 27,5%, mit 50-70% Wärmeverlust durch Abgase (1100-1315°C). |
Faktoren, die den Wirkungsgrad beeinflussen | - Ofentemperatur |
- Verweilzeit
- Druckregelung | | Technologischer Fortschritt
- | Archimedische Schraubenspiralen Integration von Wärmetauschern zur Abwärmenutzung | | Vorteile | Verarbeitet minderwertigen Schrott und Krätze, vielseitig einsetzbar für industrielle Anwendungen.| | Benachteiligungen
| Geringere Effizienz, höherer Wartungsaufwand und Produktion von Sondermüll.| | Aufkommende Trends