Die Rolle des Vakuums bei Abscheidungsmethoden ist vielschichtig und entscheidend für den Erfolg von Dünnschichtabscheidungsprozessen. Eine Vakuumumgebung gewährleistet eine hohe mittlere freie Weglänge für aufgedampfte oder gesputterte Materialien und minimiert Kollisionen und Verunreinigungen. Das Vorhandensein von unerwünschten Gasen und Verunreinigungen wird reduziert, was die Abscheidung hochwertiger, fehlerfreier Schichten ermöglicht. Darüber hinaus ermöglichen die Vakuumbedingungen eine präzise Kontrolle der Gas- und Dampfzusammensetzung, erleichtern die Steuerung des Massenstroms und schaffen eine Niederdruck-Plasmaumgebung, die für Verfahren wie die physikalische Gasphasenabscheidung (PVD) und die Elektronenstrahlabscheidung (E-Beam) unerlässlich ist. Insgesamt sind Vakuumbedingungen unverzichtbar, um die gewünschten Schichteigenschaften, Reinheit und Gleichmäßigkeit bei Abscheidungsverfahren zu erreichen.
Die wichtigsten Punkte werden erklärt:
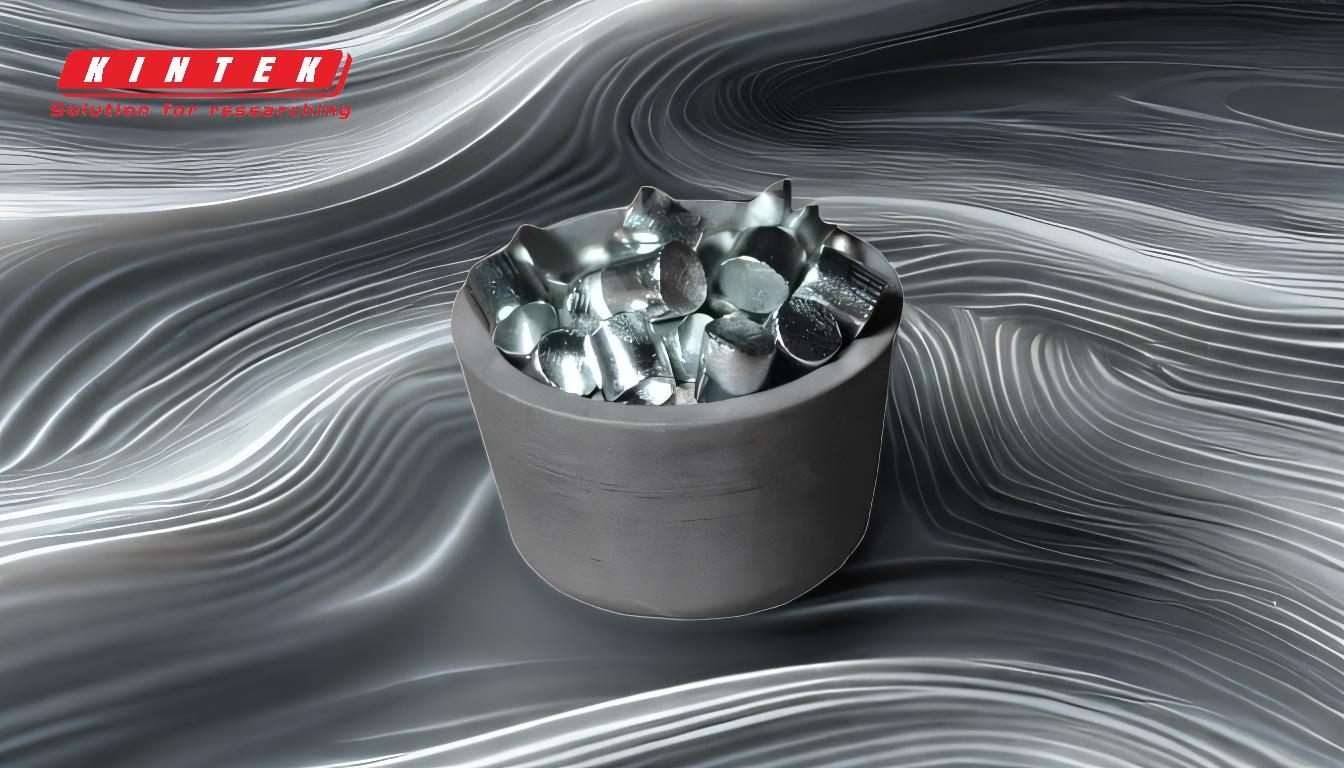
-
Hoher mittlerer freier Weg für verdampftes Material:
- Bei der Vakuumbeschichtung erhöht der reduzierte Gasdruck die mittlere freie Weglänge von Atomen und Molekülen erheblich. Das bedeutet, dass das verdampfte oder gesputterte Material längere Strecken zurücklegen kann, ohne mit anderen Partikeln zu kollidieren, so dass der größte Teil des Materials das Substrat erreicht. Dadurch werden Verluste und Verunreinigungen minimiert, was zu einer höheren Abscheidungseffizienz und einer besseren Schichtqualität führt.
-
Reduktion von Schadstoffen:
- In einer Vakuumumgebung wird das Vorhandensein von unerwünschten Gasen und Verunreinigungen, die Defekte in dünnen Schichten verursachen können, drastisch reduziert. Durch die Beseitigung oder Minimierung dieser Verunreinigungen erreichen die abgeschiedenen Schichten eine höhere Reinheit und bessere Leistungsmerkmale. Dies ist besonders wichtig bei Anwendungen, die hohe Präzision erfordern, wie z. B. bei der Halbleiterherstellung oder bei optischen Beschichtungen.
-
Kontrolle der Gas- und Dampfzusammensetzung:
- Unter Vakuumbedingungen lässt sich die Zusammensetzung der Gase und Dämpfe in der Beschichtungskammer genau steuern. Diese Kontrolle ist für Verfahren wie die chemische Gasphasenabscheidung (CVD) und die plasmaunterstützte chemische Gasphasenabscheidung (PECVD) unerlässlich, bei denen spezifische Gasmischungen erforderlich sind, um die gewünschten Schichteigenschaften zu erzielen. Sie ermöglicht auch die Zufuhr reaktiver Gase in kontrollierten Mengen, um die Schichteigenschaften zu verändern.
-
Niederdruck-Plasmaumgebung:
- Viele Abscheidungsmethoden, wie PVD und E-Beam Deposition, basieren auf einer Niederdruck-Plasmaumgebung. Das Vakuum erleichtert die Erzeugung und Aufrechterhaltung dieses Plasmas, das für Verfahren wie Sputtern und ionenunterstützte Abscheidung entscheidend ist. Die Plasmaumgebung erhöht die Energie der abgeschiedenen Partikel und verbessert so die Haftung und Dichte des Films.
-
Massendurchflussregelung:
- Vakuumsysteme ermöglichen eine präzise Steuerung des Massenstroms von Gasen und Dämpfen in die Beschichtungskammer. Dies ist entscheidend für die Aufrechterhaltung gleichmäßiger Abscheidungsraten und die Gewährleistung einer gleichmäßigen Schichtdicke. Massendurchflussregler (MFCs) werden häufig in Verbindung mit Vakuumsystemen eingesetzt, um dieses Maß an Kontrolle zu erreichen.
-
Thermische Verdampfungsrate:
- Bei thermischen Verdampfungsprozessen ermöglicht eine Vakuumumgebung höhere Verdampfungsraten, indem der Druck reduziert und das Vorhandensein von Restgasen minimiert wird. Dies ist besonders wichtig bei der E-Beam-Beschichtung, wo hohe Verdampfungsraten für einen effizienten Materialtransfer auf das Substrat erforderlich sind.
-
Verringerung der gasförmigen Verunreinigung:
- Durch die Aufrechterhaltung eines Vakuums wird die Dichte unerwünschter Atome und Moleküle minimiert. Diese Verringerung der gasförmigen Verunreinigung ist entscheidend für die Erzielung hochwertiger Schichten mit minimalen Defekten. Sie verhindert auch die Bildung von Ruß oder anderen unerwünschten Nebenprodukten, die bei höherem Druck auftreten können.
-
Einfluss auf die Plasmaeigenschaften:
- Die Vakuumumgebung beeinflusst die Enthalpie, die Dichte der geladenen und ungeladenen Teilchen und die Energieverteilung im Plasma. Diese Faktoren sind entscheidend für die Steuerung des Abscheidungsprozesses und die Erzielung der gewünschten Schichteigenschaften, wie z. B. Haftung, Dichte und Gleichmäßigkeit.
-
Beseitigung von Restgasen:
- Durch das Erreichen von Ultrahochvakuumbedingungen (UHV) vor der Abscheidung werden Restgase eliminiert, die Defekte in dünnen Schichten verursachen können. Dies ist besonders wichtig bei Hochpräzisionsanwendungen, bei denen selbst Spuren von Verunreinigungen die Leistung der Schichten erheblich beeinträchtigen können.
-
Verbesserte Filmeigenschaften:
- Insgesamt verbessert die Vakuumumgebung die Eigenschaften der abgeschiedenen Schichten, einschließlich ihrer Reinheit, Gleichmäßigkeit, Haftung und Dichte. Diese Verbesserungen sind entscheidend für die Erfüllung der strengen Anforderungen fortschrittlicher technologischer Anwendungen wie Mikroelektronik, Optik und Nanotechnologie.
Zusammenfassend lässt sich sagen, dass die Vakuumumgebung bei Abscheidungsverfahren unverzichtbar ist, da sie die notwendigen Bedingungen für eine qualitativ hochwertige, fehlerfreie Schichtabscheidung schafft. Es gewährleistet eine kontrollierte, kontaminationsfreie Umgebung, erleichtert die präzise Prozesssteuerung und verbessert die Eigenschaften der abgeschiedenen Schichten.
Zusammenfassende Tabelle:
Die Schlüsselrolle des Vakuums bei der Abscheidung | Vorteile |
---|---|
Hoher mittlerer freier Weg | Minimiert Kollisionen, reduziert Verunreinigungen und verbessert die Abscheidungseffizienz. |
Reduktion von Schadstoffen | Sorgt für hochreine Filme, die für Präzisionsanwendungen entscheidend sind. |
Kontrolle der Gaszusammensetzung | Ermöglicht präzise Gas- und Dampfkontrolle für maßgeschneiderte Filmeigenschaften. |
Niederdruck-Plasmaumgebung | Erleichtert Verfahren wie PVD und E-Beam-Deposition für eine bessere Schichthaftung. |
Massendurchflussregelung | Sorgt für konstante Abscheideraten und gleichmäßige Schichtdicken. |
Thermische Verdampfungsrate | Erhöht die Verdunstungsrate und verbessert die Effizienz des Materialtransfers. |
Verringerung der gasförmigen Verunreinigung | Minimiert Fehler und unerwünschte Nebenprodukte. |
Einfluss auf die Plasmaeigenschaften | Steuert die Partikelenergie und -verteilung für optimale Filmeigenschaften. |
Beseitigung von Restgasen | Entfernt Spuren von Verunreinigungen und sorgt für fehlerfreie Filme. |
Verbesserte Filmeigenschaften | Verbessert die Reinheit, Gleichmäßigkeit, Haftung und Dichte der abgeschiedenen Schichten. |
Sind Sie bereit, Ihren Dünnschichtabscheidungsprozess zu optimieren? Kontaktieren Sie uns heute um mehr über Vakuumlösungen zu erfahren!