Spark-Plasma-Sintern (SPS) ist ein fortschrittliches Sinterverfahren, bei dem gepulster Gleichstrom (DC) zur schnellen Verdichtung von Pulverwerkstoffen eingesetzt wird.Im Gegensatz zu herkömmlichen Sinterverfahren werden bei SPS einachsiger mechanischer Druck und ein gepulster elektrischer Strom auf den Pulverpressling ausgeübt, wodurch lokal hohe Temperaturen (bis zu 10.000 °C) und ein Plasma zwischen den Partikeln erzeugt werden.Dieses Verfahren ermöglicht schnelle Heizraten (bis zu 1000°C/min), kurze Sinterzeiten und eine Verdichtung bei niedrigeren Temperaturen als beim herkömmlichen Sintern.Die Kombination aus mechanischem Druck, elektrischem Feld und thermischem Feld verbessert die Partikelbindung und führt zu Materialien mit hoher Dichte (in einigen Fällen über 99 %), wobei die inhärenten Eigenschaften von Nanopulvern erhalten bleiben.SPS ist energieeffizient, umweltfreundlich und für eine breite Palette von Materialien geeignet.
Die wichtigsten Punkte werden erklärt:
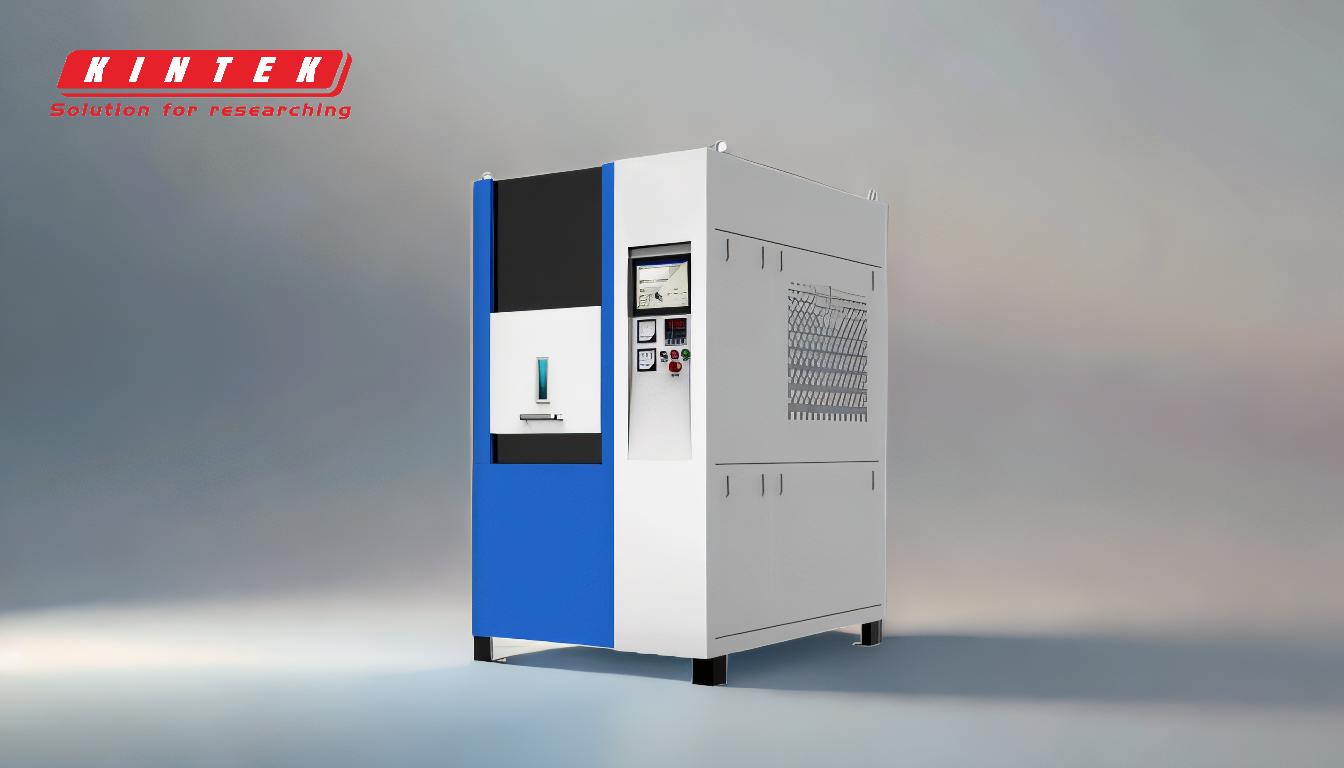
-
Prinzip der SPS:
- SPS beruht auf dem Prinzip der elektrischen Funkenentladung, bei der ein hochenergetischer gepulster Strom ein Funkenplasma zwischen den Pulverpartikeln erzeugt.
- Dieses Plasma erzeugt lokal hohe Temperaturen (bis zu 10.000 °C), die die Partikeloberflächen schmelzen und verschmelzen und "Nacken" bilden, die mit der Zeit wachsen und die Materialdichte erhöhen.
-
Komponenten und Aufbau:
- SPS verwendet ein Stempel-/Matrizensystem ähnlich dem Heißpressen, bei dem das Pulver in eine Matrize gegeben und unter einachsiger mechanischer Belastung komprimiert wird.
- Ein gepulster Gleichstrom wird direkt an den Pulverpressling angelegt, wodurch Joule-Erwärmung und Plasmaaktivierung erzeugt werden.
-
Schlüsselmechanismen:
- Plasma-Aktivierung:Der gepulste Strom erzeugt ein Plasma zwischen den Partikeln, wodurch die Partikelabstände verringert und die Oberflächendiffusion verbessert werden.
- Joule-Erwärmung:Der elektrische Strom erhitzt den Pulverpressling direkt und erreicht so schnelle Aufheizraten (bis zu 1000°C/min).
- Entladeschock-Druck:Die hochenergetischen Impulse erzeugen einen Schockdruck, der die Verdichtung weiter fördert.
-
Vorteile der SPS:
- Schnelle Verdichtung:SPS erreicht eine vollständige Verdichtung innerhalb von Minuten, deutlich schneller als das konventionelle Sintern.
- Niedrigere Sintertemperaturen:SPS kann Materialien bei Temperaturen verdichten, die 200-500°C niedriger sind als bei herkömmlichen Verfahren.
- Energie-Effizienz:Direkte Erhitzung und kurze Verarbeitungszeiten reduzieren den Energieverbrauch.
- Material Konservierung:Hohe Erhitzungs- und Abkühlungsraten tragen dazu bei, dass die Eigenschaften der Nanopulver im Endprodukt erhalten bleiben.
-
Anwendungen:
- SPS wird häufig zum Sintern von Hochleistungskeramik, Metallen, Verbundwerkstoffen und Nanomaterialien eingesetzt.
- Es ist besonders vorteilhaft für Materialien, die eine hohe Dichte und eine feine Mikrostrukturkontrolle erfordern.
-
Ökologische und wirtschaftliche Vorteile:
- Das Verfahren ist aufgrund des geringeren Energieverbrauchs und der kürzeren Verarbeitungszeiten umweltfreundlich.
- Niedrigere Sintertemperaturen und schnellere Verarbeitung senken die Gesamtproduktionskosten.
-
Vergleich mit konventionellem Sintern:
- Im Gegensatz zum Heißpressen, das auf Strahlungserwärmung beruht, nutzt SPS die direkte Joule-Erwärmung und Plasmaaktivierung.
- Mit SPS werden höhere Dichten und bessere Materialeigenschaften in einem Bruchteil der Zeit erreicht, die bei herkömmlichen Verfahren erforderlich ist.
-
Herausforderungen und Beschränkungen:
- Die hohen Kosten der SPS-Ausrüstung und die Notwendigkeit einer speziellen Ausbildung können die Einführung behindern.
- Das Verfahren ist möglicherweise nicht für alle Materialien geeignet, insbesondere für solche, die empfindlich auf schnelle Erhitzung oder hohe elektrische Felder reagieren.
Durch die Kombination von mechanischem Druck, elektrischen Feldern und thermischen Feldern bietet SPS einen einzigartigen und effizienten Ansatz für die Materialverdichtung, was es zu einer wertvollen Technik in der fortgeschrittenen Fertigung und Materialwissenschaft macht.
Zusammenfassende Tabelle:
Aspekt | Einzelheiten |
---|---|
Prinzip | Verwendet gepulsten Gleichstrom zur Erzeugung eines Funkenplasmas, das örtlich begrenzte hohe Temperaturen (bis zu 10.000 °C) erzeugt. |
Wichtigste Mechanismen | Plasmaaktivierung, Joule-Erwärmung und Entladungsstoßdruck. |
Vorteile | Schnelle Verdichtung, niedrigere Sintertemperaturen, Energieeffizienz und Materialschonung. |
Anwendungen | Hochleistungskeramik, Metalle, Verbundwerkstoffe und Nanomaterialien. |
Vorteile für die Umwelt | Geringerer Energieverbrauch und kürzere Bearbeitungszeiten. |
Herausforderungen | Hohe Ausrüstungskosten und spezielle Schulungsanforderungen. |
Möchten Sie erfahren, wie Spark Plasma Sintering Ihre Materialverarbeitung verändern kann? Kontaktieren Sie uns noch heute um mehr zu erfahren!