Das Induktionshärten ist ein Verfahren zum Härten der Oberfläche von Metallteilen durch Erhitzen mit einem magnetischen Wechselfeld und anschließendes schnelles Abkühlen.Die für das Induktionshärten erforderliche Temperatur liegt in der Regel über der kritischen Punkttemperatur des Stahls, d. h. der Temperatur, bei der der Stahl eine Phasenumwandlung von Ferrit in Austenit durchläuft.Diese kritische Temperatur variiert je nach Stahlsorte, liegt aber im Allgemeinen im Bereich von 700°C bis 900°C (1292°F bis 1652°F).Bei diesem Verfahren wird das Werkstück in eine Induktionsspule gelegt, wo ein Wechselstrom ein Magnetfeld erzeugt, das Wirbelströme induziert, die die Oberfläche des Werkstücks erwärmen.Die hohe Stromdichte an der Oberfläche bewirkt eine schnelle Erwärmung, und sobald die gewünschte Temperatur erreicht ist, wird das Werkstück schnell abgekühlt, um eine Oberflächenhärtung zu erreichen.
Die wichtigsten Punkte werden erklärt:
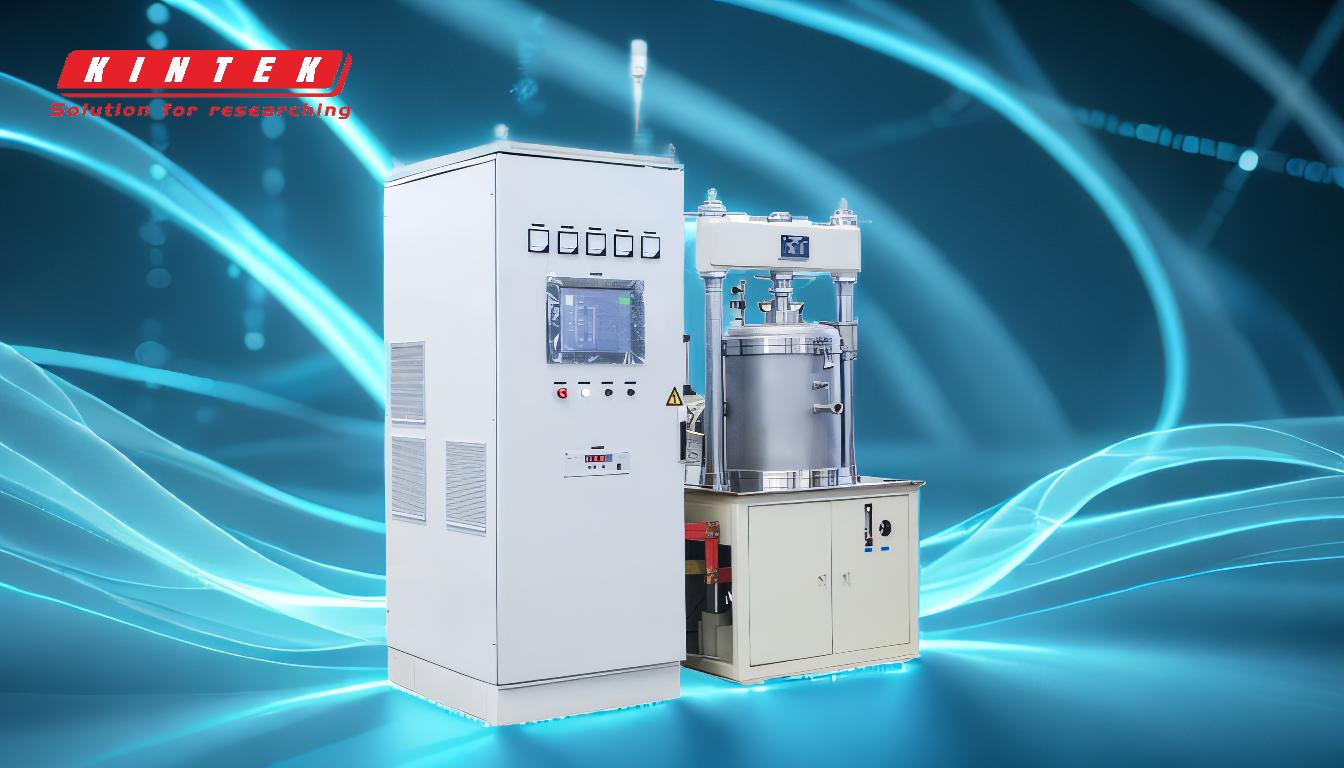
-
Induktionshärteverfahren:
- Beim Induktionshärten wird das Werkstück in eine Induktionsspule gelegt.
- Ein Wechselstrom in der Spule erzeugt ein Magnetfeld, das im Werkstück Wirbelströme induziert.
- Die Wirbelströme führen dazu, dass sich die Oberfläche des Werkstücks aufgrund des Skin-Effekts, bei dem die Stromdichte an der Oberfläche am höchsten ist, schnell erwärmt.
-
Temperaturbereich für die Induktionshärtung:
- Die für das Induktionshärten erforderliche Temperatur muss über der Temperatur des kritischen Punkts des Stahls liegen.
- Die Temperatur des kritischen Punktes ist die Temperatur, bei der sich der Stahl von Ferrit in Austenit umwandelt, in der Regel zwischen 700°C und 900°C (1292°F bis 1652°F).
- Die genaue Temperatur hängt von der jeweiligen Stahlsorte ab, die behandelt wird.
-
Auswirkung der Stromfrequenz:
- Die Frequenz des Wechselstroms beeinflusst die Tiefe der Heizschicht.
- Höhere Frequenzen führen zu einem größeren Stromdichteunterschied zwischen der Oberfläche und dem Inneren, was zu einer dünneren Heizschicht führt.
- Dadurch lässt sich die Tiefe der gehärteten Schicht genau steuern, so dass sich das Induktionshärten für Anwendungen eignet, die eine bestimmte Oberflächenhärte erfordern, ohne die Kerneigenschaften des Materials zu beeinträchtigen.
-
Schnelle Abkühlung:
- Sobald die Oberfläche des Werkstücks die kritische Temperatur erreicht hat, wird es schnell abgekühlt, in der Regel mit Wasser, Öl oder Abschreckmitteln auf Polymerbasis.
- Durch diese schnelle Abkühlung wird der Austenit in Martensit, eine harte und spröde Phase, umgewandelt, was zu einer gehärteten Oberflächenschicht führt.
-
Anwendungen und Vorteile:
- Das Induktionshärten ist in Branchen wie der Automobilindustrie, der Luft- und Raumfahrt und der verarbeitenden Industrie für Bauteile wie Zahnräder, Wellen und Lager weit verbreitet.
- Das Verfahren bietet mehrere Vorteile, darunter lokale Härtung, minimale Verformung und die Möglichkeit, bestimmte Bereiche eines Teils zu härten, ohne das gesamte Bauteil zu beeinträchtigen.
Zusammenfassend lässt sich sagen, dass die Temperatur für das Induktionshärten durch die Temperatur des kritischen Punkts des Stahls bestimmt wird, die in der Regel zwischen 700°C und 900°C liegt.Bei diesem Verfahren wird die Oberfläche des Werkstücks mit Hilfe eines magnetischen Wechselfeldes erwärmt und dann schnell abgekühlt, um eine gehärtete Oberflächenschicht zu erhalten.Die Frequenz des Wechselstroms beeinflusst die Tiefe der Erwärmungsschicht und ermöglicht eine präzise Steuerung des Härteprozesses.Das Induktionshärten ist eine vielseitige und effiziente Methode zur Verbesserung der Verschleißfestigkeit und Haltbarkeit von Metallteilen.
Zusammenfassende Tabelle:
Hauptaspekt | Einzelheiten |
---|---|
Temperaturbereich | 700°C bis 900°C (1292°F bis 1652°F) |
Kritischer Punkt Temperatur | Phasenumwandlung von Ferrit in Austenit |
Mechanismus der Erwärmung | Wechselndes Magnetfeld induziert Wirbelströme für eine schnelle Oberflächenerwärmung |
Abkühlungsmethode | Schnelles Abkühlen mit Wasser, Öl oder Abschreckmitteln auf Polymerbasis |
Anwendungen | Zahnräder, Wellen, Lager in der Automobilindustrie, Luft- und Raumfahrt und in der Fertigung |
Vorteile | Lokalisierte Härtung, minimaler Verzug, präzise Kontrolle |
Entdecken Sie, wie das Induktionshärten Ihre Metallkomponenten verbessern kann. Kontaktieren Sie unsere Experten noch heute !