Die Temperatur des PVD-Plasmas (Physical Vapor Deposition, physikalische Gasphasenabscheidung) liegt in der Regel zwischen 70°C und 450°C, je nach dem spezifischen Verfahren, dem Substratmaterial und den Anwendungsanforderungen.Dieser relativ niedrige Temperaturbereich ist ein entscheidender Vorteil von PVD, da er das Risiko einer Veränderung der mechanischen Eigenschaften oder Abmessungen des Substrats minimiert.Die Temperatur kann genau gesteuert werden, um eine optimale Haftung und Schichtqualität zu gewährleisten und gleichzeitig die thermische Empfindlichkeit verschiedener Substrate, wie Kunststoffe oder Metalle wie Zink, Messing und Stahl, zu berücksichtigen.Aufgrund der im Vergleich zu CVD-Verfahren (Chemical Vapor Deposition) niedrigeren Betriebstemperatur eignet sich das PVD-Verfahren für eine Vielzahl von Anwendungen, bei denen die Unversehrtheit des Substrats entscheidend ist.
Die wichtigsten Punkte werden erklärt:
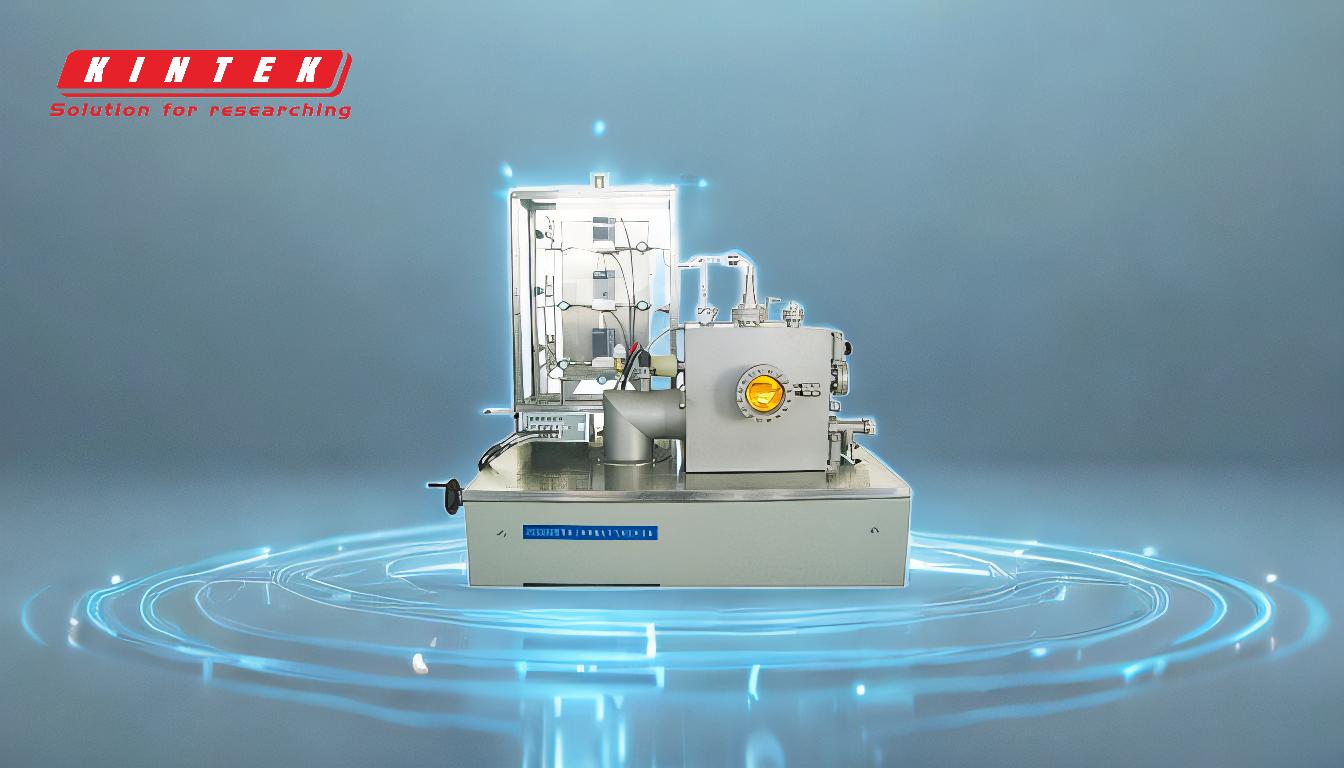
-
Typischer Temperaturbereich von PVD-Plasma:
- Die Temperatur des PVD-Plasmas reicht im Allgemeinen von 70°C bis 450°C (158°F bis 842°F) .Dieser Bereich gewährleistet, dass das Substrat stabil bleibt und sich während des Abscheidungsprozesses nicht wesentlich thermisch verformt oder verschlechtert.
- Das untere Ende des Bereichs (70°C bis 200°C) wird häufig für thermisch empfindliche Materialien wie Kunststoffe oder bestimmte Metalle verwendet, während das obere Ende (bis 450°C) für robustere Substrate wie Stahl geeignet ist.
-
Substrat-spezifische Temperaturkontrolle:
-
Die Temperatur während der PVD-Beschichtung kann je nach Substratmaterial angepasst werden.Zum Beispiel:
- Zink und Messing:Wird in der Regel bei niedrigeren Temperaturen (50°F bis 400°F oder 10°C bis 204°C) verarbeitet, um Schmelzen oder strukturelle Veränderungen zu vermeiden.
- Stahl:Kann höheren Temperaturen (bis zu 400°C oder 750°F) widerstehen, ohne seine mechanischen Eigenschaften zu beeinträchtigen.
- Kunststoffe:Noch niedrigere Temperaturen (unter 200°C oder 392°F) sind erforderlich, um Verformungen oder Beschädigungen zu vermeiden.
- Diese Anpassungsfähigkeit macht PVD für eine Vielzahl von Materialien und Anwendungen geeignet.
-
Die Temperatur während der PVD-Beschichtung kann je nach Substratmaterial angepasst werden.Zum Beispiel:
-
Einfluss der Temperatur auf die Filmqualität:
- Die Temperatur des Substrats während der PVD-Beschichtung beeinflusst maßgeblich den Haftungskoeffizient der bestimmt, wie gut das abgeschiedene Material auf dem Substrat haftet.
- Höhere Temperaturen (innerhalb des PVD-Bereichs) können die Schichthaftung und die Kristallinität verbessern, doch kann übermäßige Hitze die Eigenschaften des Substrats verändern oder thermische Spannungen verursachen.
- Thermisches Gleichgewicht auf der Substratoberfläche ist entscheidend für eine gleichmäßige Schichtqualität und eine gute Kristallstruktur.
-
Vergleich mit CVD:
- PVD arbeitet bei viel niedrigeren Temperaturen als die Chemischen Gasphasenabscheidung (CVD) die in der Regel Temperaturen über 900°C (1652°F) .
- Der niedrigere Temperaturbereich von PVD eignet sich besser für Anwendungen mit thermisch empfindlichen Substraten oder für Anwendungen, bei denen eine Verarbeitung bei hohen Temperaturen unpraktisch ist.
-
Kontrolle der Prozesstemperatur:
- PVD-Anlagen sind so konzipiert, dass sie eine präzise Temperatursteuerung gewährleisten, wobei häufig fortschrittliche Kühl- und Heizmechanismen zum Einsatz kommen, um gleichbleibende Abscheidungsbedingungen sicherzustellen.
- Die Möglichkeit, bei niedrigeren Temperaturen zu arbeiten, verringert den Bedarf an hoher Plasmaleistung, was den Energieverbrauch und die Betriebskosten weiter senken kann.
-
Anwendungen und Beschränkungen:
- Die relativ niedrige Betriebstemperatur von PVD macht es ideal für Anwendungen in Branchen wie Elektronik, Optik und medizinische Geräte wo die Integrität des Substrats entscheidend ist.
- Die Temperatur muss jedoch sorgfältig kontrolliert werden, um zu vermeiden, dass sich die Eigenschaften der Schicht verändern oder Defekte wie schlechte Haftung oder ungleichmäßige Dicke entstehen.
Durch die Beibehaltung eines kontrollierten Temperaturbereichs gewährleistet PVD hochwertige Beschichtungen bei gleichzeitiger Wahrung der strukturellen und mechanischen Integrität des Substrats.Diese Ausgewogenheit macht PVD zu einer vielseitigen und weit verbreiteten Beschichtungstechnik in verschiedenen Branchen.
Zusammenfassende Tabelle:
Aspekt | Details |
---|---|
Typischer Temperaturbereich | 70°C bis 450°C (158°F bis 842°F) |
Substratspezifische Steuerung |
- Zink/Messing: 10°C bis 204°C
- Stahl:Bis zu 400°C - Kunststoffe:Unter 200°C |
Auswirkungen auf die Filmqualität |
- Höhere Temperaturen verbessern die Adhäsion
- Thermisches Gleichgewicht gewährleistet Gleichmäßigkeit |
Vergleich mit CVD |
PVD:70°C bis 450°C
CVD:Über 900°C |
Anwendungen | Elektronik, Optik, medizinische Geräte und mehr |
Erfahren Sie, wie PVD-Plasma Ihre Substratbeschichtungen verbessern kann. Kontaktieren Sie unsere Experten noch heute !