Spark Plasma Sintering (SPS) ist ein modernes Sinterverfahren, das den Zeitaufwand für das Sintern im Vergleich zu konventionellen Methoden erheblich reduziert.Bei diesem Verfahren wird das Material in der Regel nur 5 bis 10 Minuten lang auf der Sintertemperatur gehalten, während das herkömmliche Sintern Stunden dauern kann.Diese Effizienz wird durch den Einsatz von gepulstem Gleichstrom (DC) erreicht, der hohe Temperaturen und ein Plasma zwischen den Partikeln erzeugt und so eine schnelle Verdichtung ermöglicht.Das Verfahren ermöglicht auch niedrigere Sintertemperaturen und führt zu Werkstoffen mit einer hohen Dichte, die oft über 99 % liegt.Das SPS-Verfahren ist vielseitig und kann eine Vielzahl von Werkstoffen, darunter Metalle, Keramiken und Verbundwerkstoffe, sintern und ist für seine Energieeffizienz und seine Umweltfreundlichkeit bekannt.
Die wichtigsten Punkte werden erklärt:
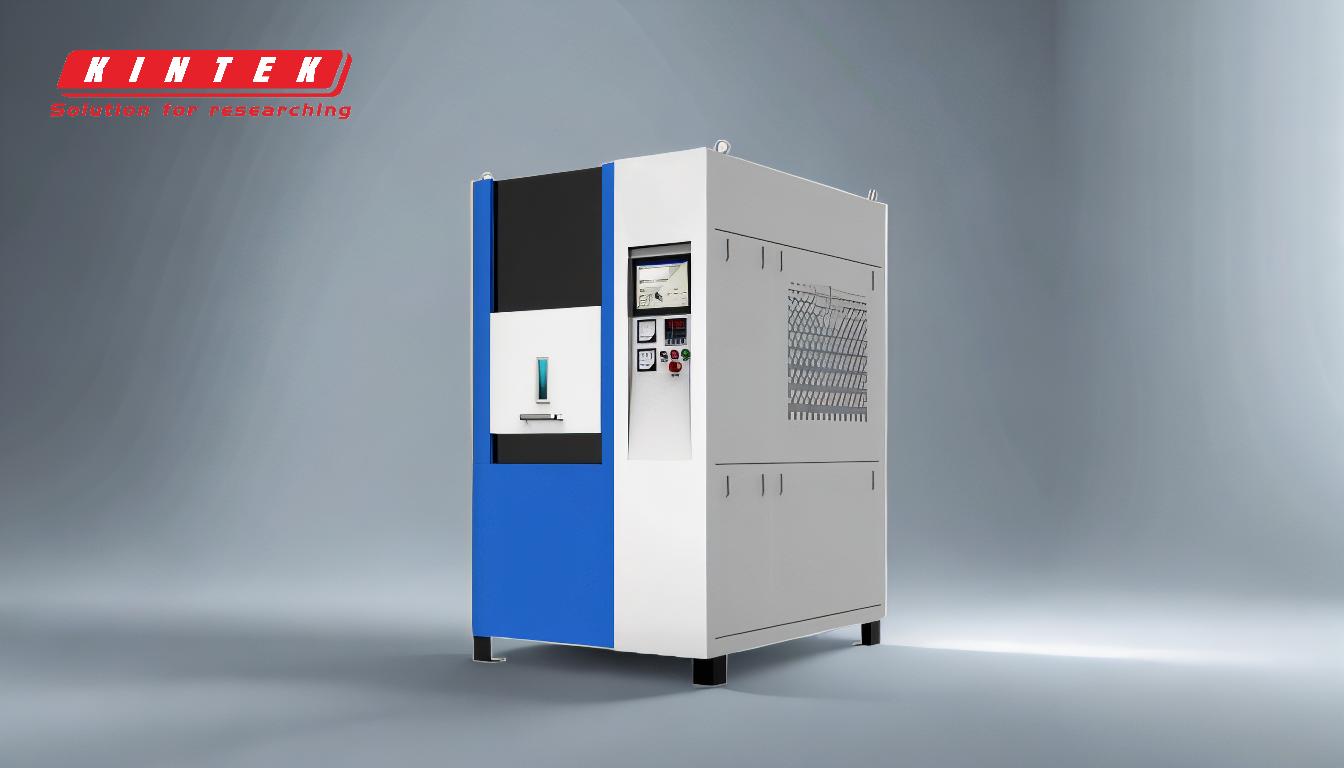
-
Verkürzte Sinterzeit:
- Erläuterung: SPS verkürzt die Sinterzeit drastisch auf nur 5 bis 10 Minuten bei der Sintertemperatur, im Vergleich zu mehreren Stunden bei herkömmlichen Sinterverfahren.Dies ist in erster Linie auf die schnellen Aufheiz- und Abkühlraten zurückzuführen, die durch den gepulsten Gleichstrom ermöglicht werden.
- Die Folgen: Diese Zeitersparnis beschleunigt nicht nur den Produktionsprozess, sondern minimiert auch das Risiko des Materialabbaus, der bei längerer Einwirkung hoher Temperaturen auftreten kann.
-
Mechanismus der Wirkung:
- Erläuterung: Beim SPS-Verfahren wird ein gepulster Gleichstrom verwendet, der zwischen den Partikeln ein Funkenplasma erzeugt, das Temperaturen von bis zu 10.000 °C erreicht.Diese hohe Temperatur führt dazu, dass die Oberfläche der Partikel schmilzt und miteinander verschmilzt und dichte Strukturen bildet, die als "Hälse" bekannt sind.
- Die Folgen: Die Bildung dieser Hälse ist entscheidend für die Erzielung von Materialien mit hoher Dichte, die oft über 99 % liegt, was für Anwendungen, die starke und dauerhafte Materialien erfordern, von wesentlicher Bedeutung ist.
-
Niedrigere Sintertemperaturen:
- Erläuterung: SPS ermöglicht das Sintern bei Temperaturen, die mehrere hundert Grad niedriger sind als bei herkömmlichen Verfahren.Dies wird durch die kombinierte Wirkung des elektrischen Feldes und des Heißpressens erreicht.
- Die Auswirkungen: Niedrigere Sintertemperaturen verringern den Energieverbrauch und minimieren die thermische Belastung der Materialien, was zu einer besseren Qualität und gleichmäßigeren Produkten führt.
-
Vielseitigkeit bei der Materialverarbeitung:
- Erläuterung: SPS kann zum Sintern einer Vielzahl von Werkstoffen verwendet werden, darunter Metalle, Keramiken, Verbundwerkstoffe, Nanomaterialien, amorphe Schüttgüter und Gradientenwerkstoffe.
- Auswirkungen: Diese Vielseitigkeit macht SPS zu einem wertvollen Verfahren in verschiedenen Branchen, von der Luft- und Raumfahrt bis zur Biomedizintechnik, in denen unterschiedliche Materialeigenschaften erforderlich sind.
-
Energieeffizienz und Umweltvorteile:
- Erläuterung: Die schnellen Aufheiz- und Abkühlraten sowie die niedrigen Sintertemperaturen tragen zur Energieeffizienz des SPS-Verfahrens bei.Darüber hinaus ist das Verfahren umweltfreundlich, da es den Gesamtenergieverbrauch senkt und die Abfallmenge minimiert.
- Die Folgen: Diese Vorteile machen SPS zu einer attraktiven Option für Industrien, die ihren ökologischen Fußabdruck verringern und gleichzeitig hohe Produktionsstandards aufrechterhalten wollen.
-
Kontrolliertes Mikrogefüge:
- Erläuterung: SPS ermöglicht eine genaue Kontrolle über die Mikrostruktur des gesinterten Materials, was für die Erzielung der gewünschten mechanischen und physikalischen Eigenschaften entscheidend ist.
- Die Auswirkungen: Diese Kontrolle ist besonders wichtig für fortschrittliche Anwendungen, bei denen spezifische Materialeigenschaften erforderlich sind, wie z. B. bei der Entwicklung von Hochleistungskeramiken oder modernen Verbundwerkstoffen.
Zusammenfassend lässt sich sagen, dass das Spark-Plasma-Sintern ein schnelles, effizientes und vielseitiges Verfahren zum Sintern einer Vielzahl von Werkstoffen darstellt.Seine Fähigkeit, Werkstoffe mit hoher Dichte und kontrollierter Mikrostruktur zu erzeugen und dabei mit niedrigeren Temperaturen und geringerem Energieverbrauch zu arbeiten, macht es zu einem äußerst vorteilhaften Verfahren in der modernen Materialwissenschaft und -technik.
Zusammenfassende Tabelle:
Hauptmerkmal | Beschreibung | Implikationen |
---|---|---|
Verkürzte Sinterzeit | Sinterung in 5-10 Minuten im Vergleich zu Stunden bei herkömmlichen Verfahren. | Schnellere Produktion, geringerer Materialabbau. |
Wirkmechanismus | Gepulster Gleichstrom erzeugt ein Plasma, das die Partikeloberflächen schmilzt und dichte Hälse bildet. | Erzielt eine Dichte von >99% für starke, haltbare Materialien. |
Niedrigere Sintertemperaturen | Arbeitet bei Hunderten von Grad niedrigeren Temperaturen als herkömmliche Verfahren. | Reduziert den Energieverbrauch, minimiert die thermische Belastung und verbessert die Produktkonsistenz. |
Vielseitigkeit | Sintert Metalle, Keramiken, Verbundwerkstoffe und mehr. | Ideal für Anwendungen in der Luft- und Raumfahrt, in der Biomedizin und bei modernen Materialien. |
Energie-Effizienz | Schnelles Aufheizen/Abkühlen und niedrigere Temperaturen reduzieren den Energieverbrauch. | Umweltfreundlich mit minimalem Abfall. |
Kontrollierte Mikrostruktur | Präzise Kontrolle über die Materialmikrostruktur. | Ermöglicht maßgeschneiderte mechanische und physikalische Eigenschaften für fortschrittliche Anwendungen. |
Sind Sie bereit, Ihre Materialverarbeitung zu verändern? Kontaktieren Sie uns noch heute um zu erfahren, wie Ihre Projekte von SPS profitieren können!