Die Dünnschichtabscheidung aus der Gasphase ist ein Verfahren zur Erzeugung dünner Materialschichten auf einem Substrat, in der Regel in einer Vakuumkammer.Diese Technik ist in verschiedenen Industriezweigen unverzichtbar, darunter Halbleiter, Optik, Luft- und Raumfahrt und biomedizinische Geräte.Bei diesem Verfahren werden chemische Ausgangsstoffe verdampft, die dann auf der Substratoberfläche reagieren und eine leistungsstarke Dünnschicht bilden.Das Aufdampfen von Dünnschichten wird für Anwendungen wie die Verbesserung optischer Eigenschaften, die Erhöhung der elektrischen Leitfähigkeit, die Herstellung von Korrosionsschutzschichten und die Entwicklung von Spitzentechnologien wie Solarzellen, Quantencomputern und biomedizinischen Geräten eingesetzt.Die Methode variiert je nach der verwendeten Technik, z. B. chemische Gasphasenabscheidung (CVD), thermische Verdampfung oder Sputtern.
Die wichtigsten Punkte erklärt:
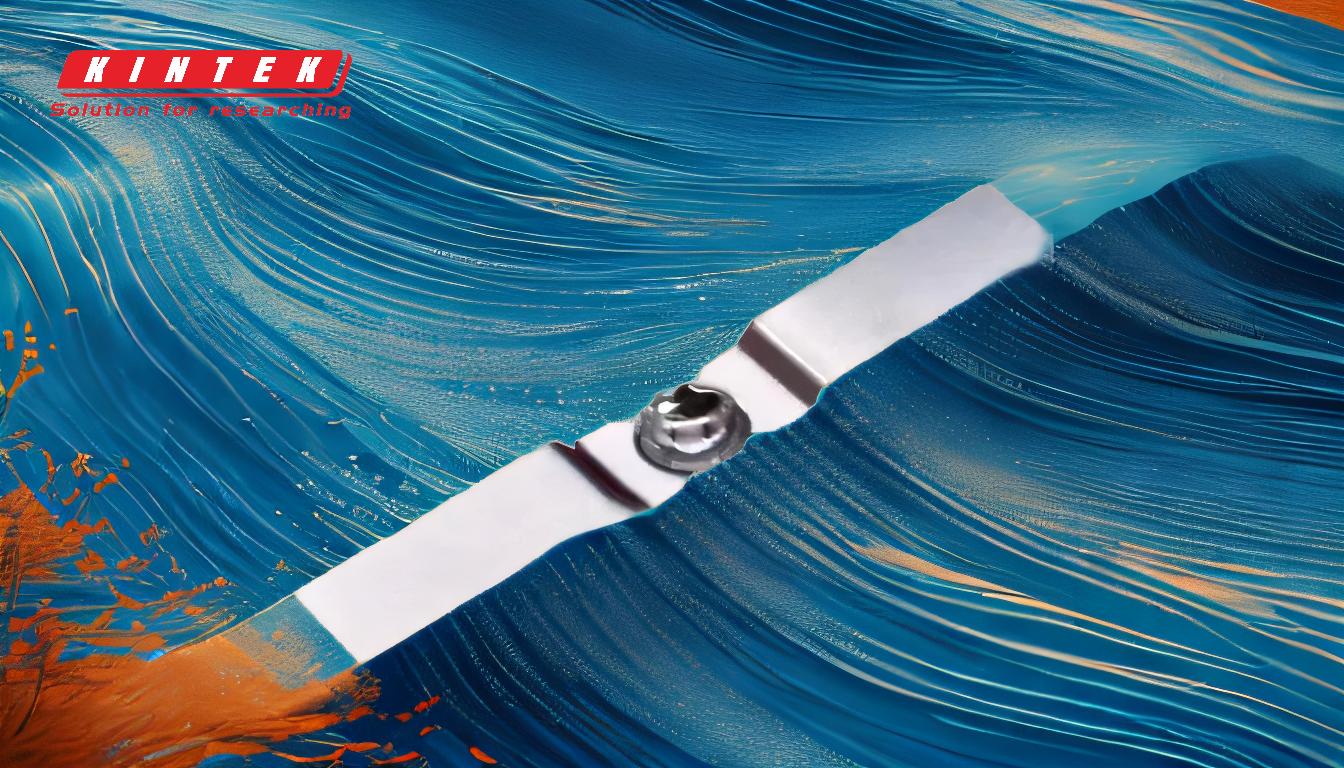
-
Definition der Dünnschichtaufdampfung:
- Bei der Dünnschichtabscheidung aus der Gasphase wird eine dünne Materialschicht in einer Vakuumkammer auf ein Substrat aufgebracht.
- Dabei werden chemische Ausgangsstoffe verdampft, die dann auf der Substratoberfläche reagieren und eine dünne Schicht bilden.
-
Techniken der Dünnschichtaufdampfung:
- Chemische Gasphasenabscheidung (CVD):Erhitzen von chemischen Grundstoffen, um sie zu verdampfen und eine chemische Reaktion auf der Substratoberfläche auszulösen, die einen dünnen Film bildet.
- Thermische Verdampfung:Das Material wird durch Hitze verdampft und kondensiert dann auf dem Substrat zu einem dünnen Film.
- Sputtern:Beschuss eines Zielmaterials mit Ionen, um Atome auszustoßen, die sich dann auf dem Substrat ablagern.
- Ionenstrahl-Beschichtung:Mit Hilfe eines Ionenstrahls wird Material von einem Target gesputtert, das sich dann auf dem Substrat ablagert.
-
Anwendungen der Dünnschichtaufdampfung:
- Optische Beschichtungen:Wird verwendet, um die Durchlässigkeit, Brechung und Reflexion von Linsen und Glasplatten zu verbessern.
- Halbleiterindustrie:Verbessert die Leitfähigkeit oder Isolierung in Halbleitergeräten und integrierten Schaltkreisen.
- Anti-Korrosions-Beschichtungen:Herstellung von keramischen Dünnschichten für Sensoren und andere Geräte zum Schutz vor Korrosion.
- Fortgeschrittene Technologien:Ermöglicht die Entwicklung ultrakleiner Strukturen wie Batterien, Solarzellen, Arzneimittelverabreichungssysteme und Quantencomputer.
- Dekorative und funktionelle Beschichtungen:Verwendet für dekorative Oberflächen, elektrische Beschichtungen und andere funktionelle Anwendungen.
-
Industrien, die die Dünnschichtaufdampfung nutzen:
- Halbleiter:Unverzichtbar für die Entwicklung elektronischer Materialien und die Verbesserung der Leistung von Geräten.
- Luft- und Raumfahrt:Bildet thermische und chemische Barriereschichten zum Schutz vor korrosiven Umgebungen.
- Optik:Verleiht Substraten die gewünschten reflektierenden und durchlässigen Eigenschaften.
- Biomedizinische Geräte:Einsatz in medizinischer Elektronik und Geräten zur Verbesserung der Leistung und Haltbarkeit.
- Unterhaltungselektronik:Verbessert die Funktionalität und Haltbarkeit einer breiten Palette von elektronischen Geräten.
-
Vorteile der Dünnschichtaufdampfung:
- Hochleistungs- beschichtungen:Erzeugt Beschichtungen mit hervorragenden Eigenschaften wie Härte, Korrosions- und Hitzebeständigkeit.
- Präzision und Kontrolle:Ermöglicht eine genaue Kontrolle über die Dicke und Zusammensetzung der abgeschiedenen Schichten.
- Vielseitigkeit:Anwendbar auf einer breiten Palette von Materialien und Substraten, wodurch es für verschiedene Anwendungen geeignet ist.
-
Zukünftige Trends und Innovationen:
- Nanotechnologie:Fortgesetzte Entwicklung von ultrakleinen Strukturen und Geräten.
- Nachhaltige Energie:Fortschritte bei Solarzellen und Energiespeichergeräten.
- Biomedizinische Anwendungen:Verbesserte Arzneimittelabgabesysteme und biokompatible Beschichtungen für medizinische Geräte.
Zusammenfassend lässt sich sagen, dass das Aufdampfen von Dünnschichten ein vielseitiges und unverzichtbares Verfahren ist, das in verschiedenen Branchen eingesetzt wird, um Hochleistungsbeschichtungen zu erzeugen und die Entwicklung fortschrittlicher Technologien zu ermöglichen.Die Anwendungen reichen von der Verbesserung der optischen Eigenschaften bis zur Steigerung der Funktionalität elektronischer und biomedizinischer Geräte.
Zusammenfassende Tabelle:
Aspekt | Einzelheiten |
---|---|
Definition | Verfahren zum Aufbringen dünner Materialschichten auf ein Substrat im Vakuum. |
Techniken | CVD, thermisches Aufdampfen, Sputtern, Ionenstrahlabscheidung. |
Anwendungen | Optische Beschichtungen, Halbleiter, Korrosionsschutz, Spitzentechnologien. |
Branchen | Halbleiter, Luft- und Raumfahrt, Optik, Biomedizin, Unterhaltungselektronik. |
Vorteile | Leistungsstarke Beschichtungen, Präzision, Vielseitigkeit. |
Zukünftige Trends | Nanotechnologie, nachhaltige Energie, Fortschritte in der Biomedizin. |
Entdecken Sie, wie die Dünnfilm-Bedampfung Ihre Branche verändern kann. Kontaktieren Sie uns noch heute für fachkundige Beratung!