Die Vakuumbeschichtung ist ein äußerst vielseitiges und präzises Verfahren zur Abscheidung dünner Materialschichten auf ein Substrat in einer Vakuum- oder Niederdruckumgebung.Diese Technik wird in vielen Branchen für Anwendungen wie Korrosionsschutz, optische Beschichtungen, Halbleiterbauelemente, Solarzellen und vieles mehr eingesetzt.Bei diesem Verfahren werden Atome oder Moleküle einzeln abgeschieden, wodurch extrem dünne und gleichmäßige Schichten, oft im Nanometerbereich, erzeugt werden können.Die Vakuumabscheidung bietet erhebliche Vorteile, darunter eine geringere Umweltbelastung, hohe Präzision und die Möglichkeit, mit Materialien zu arbeiten, die sonst unter atmosphärischen Bedingungen oxidieren oder zerfallen würden.Dies macht sie in der modernen Fertigung unverzichtbar, insbesondere für fortschrittliche Technologien wie Dünnschicht-Solarzellen, Mikroelektronik und flexible Displays.
Die wichtigsten Punkte werden erklärt:
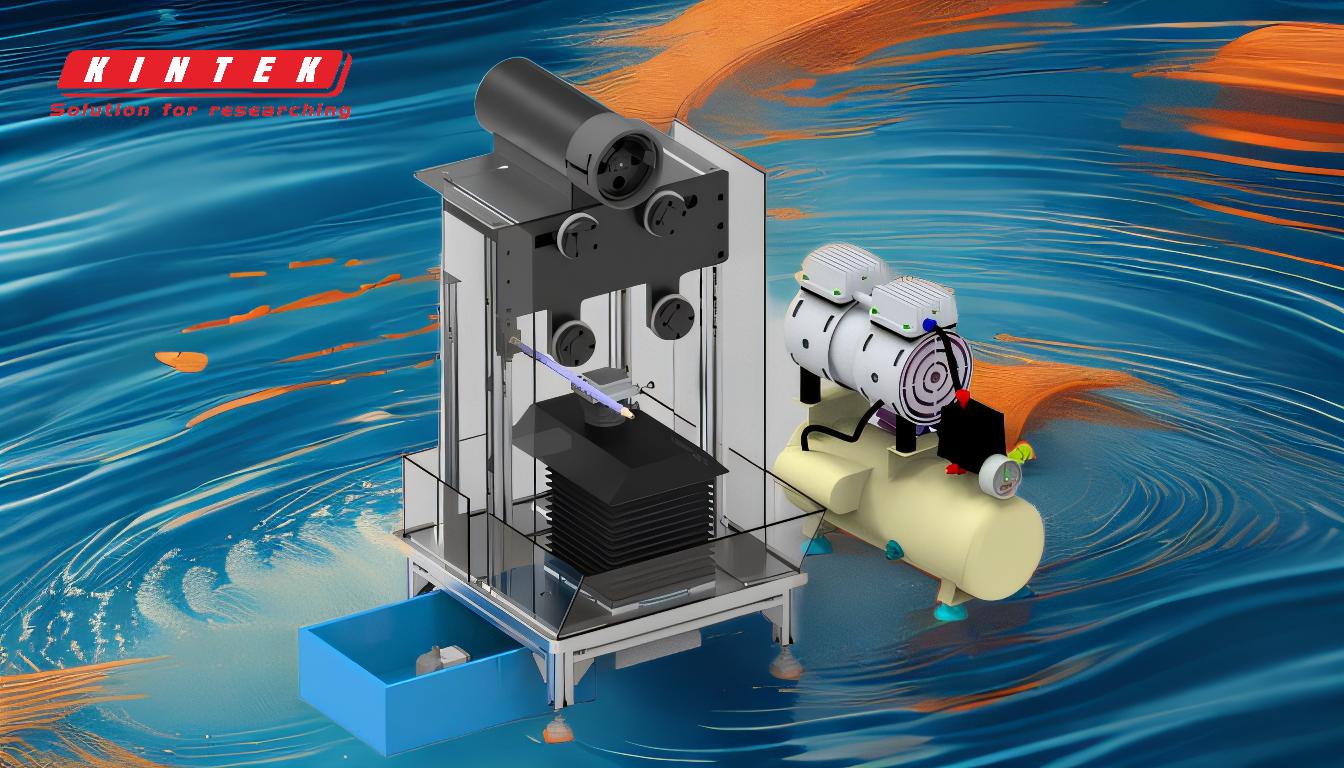
-
Definition und Verfahren der Vakuumbeschichtung
- Die Vakuumabscheidung ist ein Verfahren, bei dem dünne Materialschichten im Vakuum oder bei niedrigem Druck auf ein Substrat aufgebracht werden.
- Bei diesem Verfahren werden Atome oder Moleküle einzeln abgeschieden, so dass die Dicke und Gleichmäßigkeit der abgeschiedenen Schicht genau kontrolliert werden kann.
- Zu den gängigen Verfahren gehören die physikalische Gasphasenabscheidung (PVD) und die chemische Gasphasenabscheidung bei niedrigem Druck (LPCVD).
-
Anwendungen der Vakuumbeschichtung
- Korrosionsschutz: Wird verwendet, um korrosionsbeständige Beschichtungen auf Substrate aufzutragen und so die Lebensdauer von Materialien in rauen Umgebungen zu verlängern.
- Optische Beschichtungen: Formt optische Interferenzbeschichtungen, Spiegelbeschichtungen und dekorative Beschichtungen für Linsen, Spiegel und andere optische Geräte.
- Halbleitergeräte: Unverzichtbar für die Herstellung von Mikrochips, LEDs und Solarzellen, wo präzise Metallbeschichtungen für die Funktionalität erforderlich sind.
- Solarzellen: Verbessert die Leitfähigkeit und die Lichtsammel-Eigenschaften von Dünnschicht-Solarzellen und erhöht so deren Effizienz und Haltbarkeit.
- Flexible Displays: Für die Herstellung von Dünnschichttransistoren für flexible Displays und Sensoren.
- Verschleißbeständige Beschichtungen: Dauerhafte Beschichtungen für Werkzeuge und Maschinen, die den Verschleiß reduzieren.
-
Vorteile der Vakuumbeschichtung
- Auswirkungen auf die Umwelt: Das Verfahren hat im Vergleich zu herkömmlichen Beschichtungsmethoden einen geringeren ökologischen Fußabdruck.
- Präzision und Kontrolle: Ermöglicht die Abscheidung extrem dünner Schichten, oft im Nanometerbereich, mit hoher Gleichmäßigkeit.
- Vielseitigkeit der Materialien: Ermöglicht die Verwendung von Materialien, die unter atmosphärischen Bedingungen oxidieren oder sich zersetzen würden.
- Saubere Umgebung: Die Vakuumumgebung minimiert Verunreinigungen und gewährleistet hochwertige Beschichtungen.
-
Industrielle Bedeutung
- Die Vakuumbeschichtung ist ein Eckpfeiler der modernen Fertigung, insbesondere in Branchen, die hohe Präzision und fortschrittliche Materialien benötigen.
- Sie spielt eine entscheidende Rolle bei der Herstellung von elektronischen Geräten, Technologien für erneuerbare Energien und modernen optischen Systemen.
- Die Möglichkeit, Materialien auf atomarer oder molekularer Ebene abzuscheiden, macht sie unverzichtbar für modernste Anwendungen wie flexible Elektronik und Nanotechnologie.
-
Herausforderungen und Überlegungen
- Kosten der Ausrüstung: Die Einrichtung und Wartung von Vakuumbeschichtungsanlagen kann teuer sein.
- Kompliziertheit: Der Prozess erfordert spezielles Wissen und Erfahrung, um effektiv zu arbeiten.
- Materialbeschränkungen: Obwohl sie vielseitig sind, eignen sich nicht alle Materialien für die Vakuumabscheidung, und einige erfordern besondere Bedingungen oder Modifikationen.
-
Zukünftige Trends
- Es wird erwartet, dass die Nachfrage nach der Vakuumbeschichtung mit den Fortschritten in den Bereichen erneuerbare Energien, Elektronik und Nanotechnologie steigen wird.
- Innovationen bei diesem Verfahren, wie verbesserte Vakuumsysteme und neue Abscheidetechniken, werden die Möglichkeiten und Anwendungen weiter verbessern.
- Die Nachhaltigkeit wird weiterhin im Mittelpunkt stehen, wobei Anstrengungen unternommen werden, den Energieverbrauch und die Umweltauswirkungen während des Abscheidungsprozesses zu verringern.
Wenn die Käufer von Anlagen und Verbrauchsmaterialien diese Schlüsselpunkte verstehen, können sie fundierte Entscheidungen über die Einführung und Umsetzung von Vakuumbeschichtungstechnologien in ihrem Betrieb treffen.
Zusammenfassende Tabelle:
Aspekt | Einzelheiten |
---|---|
Definition | Ablagerung dünner Materialschichten in einer Vakuum- oder Niederdruckumgebung. |
Wichtigste Methoden | Physikalische Gasphasenabscheidung (PVD), Chemische Niederdruck-Gasphasenabscheidung (LPCVD). |
Anwendungen | Korrosionsschutz, optische Beschichtungen, Halbleiter, Solarzellen, flexible Displays. |
Vorteile | Hohe Präzision, geringere Umweltbelastung, Vielseitigkeit der Materialien, saubere Umwelt. |
Herausforderungen | Hohe Ausrüstungskosten, komplexe Prozesse, Materialbeschränkungen. |
Zukünftige Trends | Wachstum in den Bereichen erneuerbare Energien, Elektronik und Nanotechnologie; Fokus auf Nachhaltigkeit. |
Sind Sie bereit, die Vakuumbeschichtung in Ihren Betrieb zu integrieren? Kontaktieren Sie noch heute unsere Experten für maßgeschneiderte Lösungen!