Das Funkenplasmasintern (SPS) ist ein fortschrittliches Sinterverfahren, bei dem elektrischer Strom und schnelle Heizraten zur Verfestigung von Materialien mit hoher Dichte eingesetzt werden.Diese Methode ist besonders effektiv für das Sintern einer breiten Palette von Materialien, einschließlich Keramik, Metallen und Verbundwerkstoffen, bei niedrigeren Temperaturen und kürzeren Zeiten im Vergleich zu herkömmlichen Sinterverfahren.Das Verfahren beinhaltet die Anwendung eines gepulsten Gleichstroms, der durch das Material und die Form fließt und sowohl eine interne als auch eine externe Erwärmung ermöglicht.Dies führt zu verbesserten Verdichtungsmechanismen wie der Entfernung von Oberflächenoxid, Elektromigration und Elektroplastizität.SPS ist auch in der Lage, Materialien mit überlegenen mechanischen und optischen Eigenschaften herzustellen, was es zu einer wertvollen Technik für die Herstellung moderner Materialien macht.
Die wichtigsten Punkte werden erklärt:
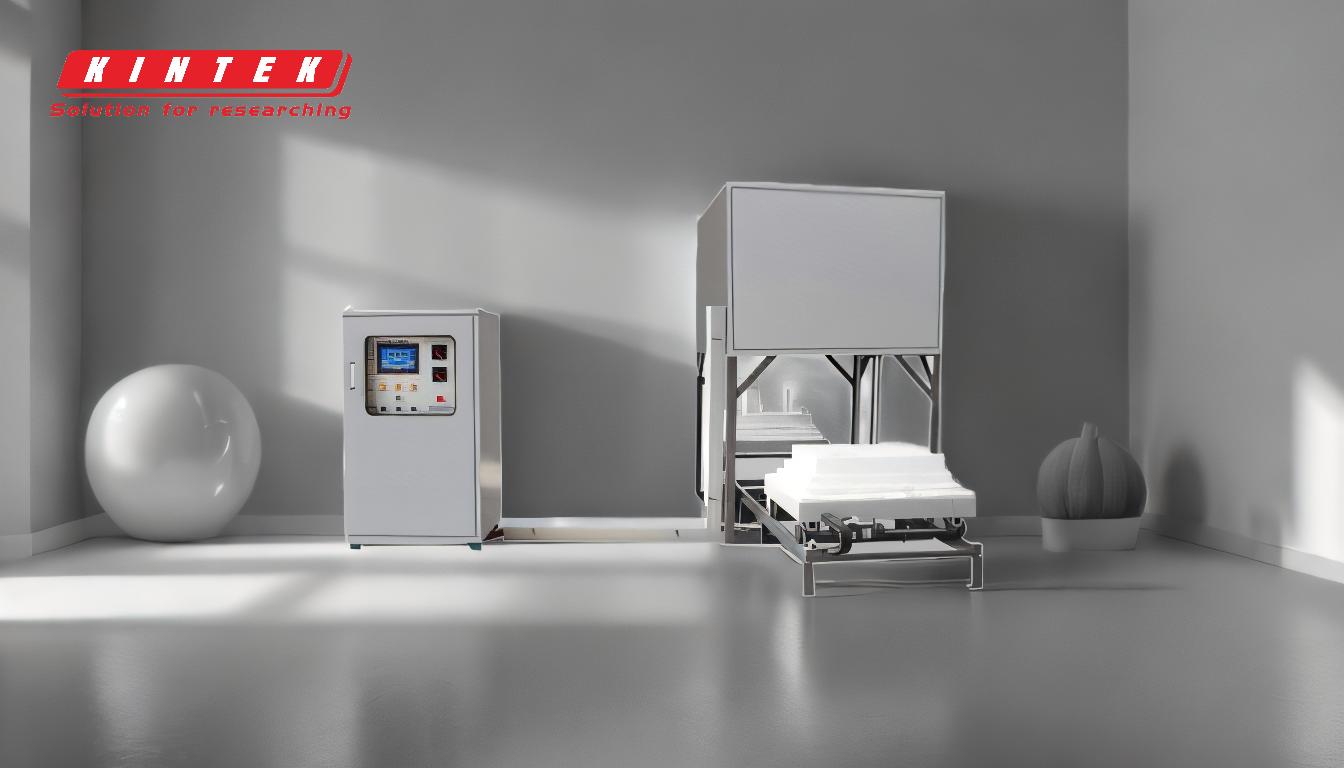
-
Anwendung von elektrischem Strom:
- Bei der SPS wird ein gepulster Gleichstrom angelegt, der durch die leitende Druckform (in der Regel aus Graphit) und, wenn das Material leitfähig ist, durch das Material selbst fließt.Dieser doppelte Erwärmungsmechanismus (intern und extern) verbessert den Sinterprozess erheblich, indem er verschiedene Mechanismen wie die Entfernung von Oberflächenoxiden, Elektromigration und Elektroplastizität aktiviert.Diese Mechanismen tragen zu einer schnellen Verdichtung des Materials bei.
-
Hohe Heizrate:
- Eines der herausragenden Merkmale von SPS ist die Fähigkeit, extrem hohe Heizraten von bis zu 1000°C/min zu erreichen.Diese schnelle Erwärmung ermöglicht die Verfestigung von Materialien bei niedrigeren Temperaturen und in kürzerer Zeit als bei herkömmlichen Sinterverfahren.Die hohe Erhitzungsrate ist besonders vorteilhaft für die Erhaltung der feinen Mikrostruktur von Werkstoffen, vor allem von solchen, die mit Techniken wie dem kryogenen Fräsen bearbeitet wurden.
-
Schritte im Sinterprozess:
- Zusammensetzung:Der Prozess beginnt mit der Zugabe und dem Mischen von Grundstoffen und Haftvermittlern.Dieser Schritt gewährleistet, dass das Pulver für die nachfolgenden Schritte gut vorbereitet ist.
- Komprimierung:Das gemischte Pulver wird anschließend mit einer Matrize in die gewünschte Form gepresst.Dieser Schritt ist entscheidend, um die gewünschte Geometrie und Ausgangsdichte des Materials zu erreichen.
- Wärme:Das geformte Pulver wird hohen Temperaturen ausgesetzt, die den Haftvermittler entfernen und das Ausgangsmaterial zu einem porenarmen Ganzen verschmelzen.Die schnelle Erhitzung bei der SPS stellt sicher, dass dieser Schritt effizient abgeschlossen wird, was zu einem dichten und gut verfestigten Material führt.
-
Matrize als Wärmequelle:
- Bei der SPS dient die Matrize nicht nur als Form für die Formgebung des Materials, sondern auch als Wärmequelle.Der elektrische Strom fließt durch die Graphitmatrize, und wenn das Material leitfähig ist, fließt er auch durch das Material selbst.Dies führt zu einer gleichmäßigen Erwärmung und einer schnellen Sinterung, was die wichtigsten Vorteile des SPS-Verfahrens sind.
-
Vorteile von SPS:
- Einfache Bedienung:SPS ist relativ einfach zu bedienen und erfordert im Vergleich zu herkömmlichen Sinterverfahren weniger komplexe Ausrüstung.
- Geringe technische Anforderungen:Das Verfahren erfordert keine hochspezialisierten Kenntnisse, so dass es für ein breites Spektrum von Anwendungen geeignet ist.
- Schnelle Sintergeschwindigkeit:Die schnellen Aufheiz- und Abkühlgeschwindigkeiten verkürzen die Gesamtsinterzeit erheblich und erhöhen die Produktivität und Effizienz.
-
Vorbereitung von amorphen Materialien:
- SPS eignet sich besonders gut für die Herstellung amorpher Materialien, wie z. B. Glas.Mit diesem Verfahren werden Übergänge zwischen Ordnung und Unordnung bei Temperaturen weit unterhalb des Schmelzpunkts von Glas erreicht, was zu Materialien mit höherer Härte, Bruchzähigkeit und besseren optischen Eigenschaften (Durchlässigkeit im nahen Infrarot und Ultraviolett) führt als bei herkömmlichen Schmelz-Kühl-Verfahren.
-
Gleichmäßige Erwärmung und hohe Sintertemperatur:
- Das SPS-Verfahren gewährleistet eine gleichmäßige Erwärmung des gesamten Materials, was für die Erzielung gleichmäßiger Materialeigenschaften entscheidend ist.Die hohen Sintertemperaturen des SPS-Verfahrens ermöglichen ein schnelles Sintern von dichten Sinterkörpern und eignen sich daher für eine breite Palette fortschrittlicher Materialanwendungen.
Zusammenfassend lässt sich sagen, dass das Spark-Plasma-Sintern ein vielseitiges und effizientes Verfahren ist, bei dem elektrischer Strom und schnelle Erwärmung zur Verfestigung von Materialien mit hoher Dichte genutzt werden.Die Fähigkeit, bei niedrigeren Temperaturen und kürzeren Zeiten zu arbeiten, sowie die Fähigkeit, Materialien mit hervorragenden Eigenschaften zu erzeugen, machen es zu einem unschätzbaren Werkzeug auf dem Gebiet der modernen Materialherstellung.
Zusammenfassende Tabelle:
Hauptaspekt | Beschreibung |
---|---|
Elektrischer Strom | Gepulster Gleichstrom fließt durch die Matrize und das Material, was eine doppelte Erwärmung ermöglicht. |
Hohe Heizrate | Bis zu 1000°C/min, was niedrigere Temperaturen und kürzere Sinterzeiten ermöglicht. |
Sinter-Schritte | Zusammensetzung, Verdichtung und Wärmezufuhr für eine schnelle Verdichtung. |
Matrize als Wärmequelle | Der Graphitstempel leitet den Strom und sorgt für eine gleichmäßige Erwärmung und schnelle Sinterung. |
Vorteile | Einfache Bedienung, geringe technische Anforderungen und hohe Sintergeschwindigkeit. |
Amorphe Werkstoffe | Erzeugt Materialien mit überlegener Härte, Zähigkeit und optischen Eigenschaften. |
Gleichmäßige Erwärmung | Sorgt für gleichbleibende Materialeigenschaften und hohe Sintertemperaturen. |
Erschließen Sie das Potenzial moderner Werkstoffe mit Spark-Plasma-Sintern. Kontaktieren Sie uns noch heute um mehr zu erfahren!