Die Auskleidung eines Induktionsofens ist ein wichtiger Prozess, der die Effizienz, Sicherheit und Langlebigkeit des Ofens gewährleistet.Dabei werden hochwertige feuerfeste Materialien wie hochreine Aluminiumoxidfasern und vakuumgeformte Fasermaterialien verwendet, um eine Auskleidung zu schaffen, die hohen Temperaturen, schnellen Erwärmungs- und Abkühlungszyklen und den korrosiven Eigenschaften von geschmolzenen Metallen standhält.Das Auskleidungsverfahren umfasst mehrere Stufen: Materialauswahl, Vorbereitung und Sintern.Der Sinterprozess, bei dem die Auskleidung zu einer festen Struktur geformt wird, ist in drei Phasen unterteilt: Einbrennen, Halbsintern und vollständiges Sintern.Eine ordnungsgemäße Wartung und Überwachung der Auskleidung ist unerlässlich, um eine Verschlechterung zu verhindern und eine optimale Leistung über einen längeren Zeitraum zu gewährleisten.
Die wichtigsten Punkte erklärt:
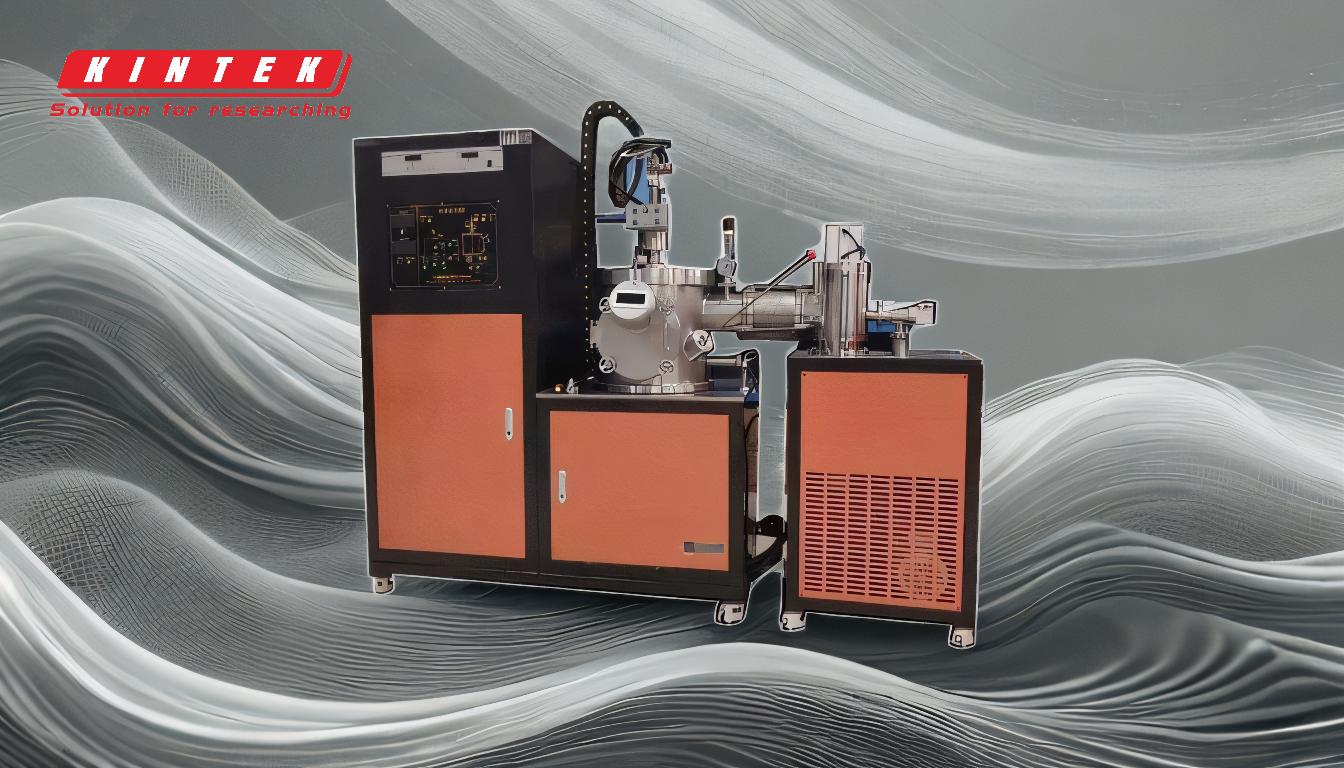
-
Zweck des Induktionsofens: Auskleidung:
- Die Auskleidung dient dazu, geschmolzenes Metall einzuschließen, es von der Außenstruktur des Ofens zu isolieren und den Ofenkörper während des Betriebs zu schützen.
- Sie sorgt für Sicherheit, Effizienz und die Qualität des Endprodukts, indem sie Leckagen verhindert und die Wärmeisolierung aufrechterhält.
-
Verwendete Materialien für die Auskleidung:
- Hochreine Aluminiumoxidfasern, vakuumgeformte Fasermaterialien und leichte hohle Aluminiumoxidplatten werden üblicherweise verwendet.
- Diese Materialien bieten hohe Betriebstemperaturen, eine geringe Wärmespeicherkapazität, eine schnelle Hitze- und Kältebeständigkeit sowie hervorragende Wärmedämmeigenschaften.
-
Auskleidung Verfahren:
- Material Vorbereitung:Die feuerfesten Materialien werden so vorbereitet und geformt, dass sie in das Innere des Ofens passen.
- Anwendung:Die Materialien werden sorgfältig aufgetragen, um eine gleichmäßige Auskleidungsschicht zu bilden, die keine Lücken oder Schwachstellen aufweist.
-
Sinterprozess:
- Backen Bühne:Die Auskleidung wird auf 600 °C erhitzt, um die Feuchtigkeit zu entfernen, damit das Material trocken und stabil ist.
- Semi-Sintering Stadium:Die Temperatur wird auf 900°C und anschließend auf 1200°C erhöht, um die Auskleidung teilweise zu sintern und eine feste Struktur zu schaffen.
- Vollständige Sinterungsphase:Die endgültige Sintertemperatur wird erreicht, wodurch die Auskleidung vollständig verfestigt wird und ihre Haltbarkeit und Leistung gewährleistet ist.
-
Die Bedeutung des richtigen Sinterns:
- Ein gut ausgeführter Sinterprozess führt zu einer Auskleidung mit einem guten Gefüge, das die Beständigkeit gegen Temperaturschock, Rissbildung und Schlackenbildung erhöht.
- Die Sintertemperatur und die Sinterdauer haben einen erheblichen Einfluss auf die Lebensdauer der Auskleidung und die Gesamteffizienz des Ofens.
-
Wartung und Überwachung:
- Regelmäßige Inspektion und Wartung der Auskleidung sind von entscheidender Bedeutung, um Anzeichen von Verschleiß oder Verschlechterung zu erkennen und zu beheben.
- Die Lebensdauer der Auskleidung wird durch die Anzahl der Wärmezyklen bestimmt, die sie aushalten kann, bevor sie repariert oder ausgetauscht werden muss.
-
Herausforderungen und Überlegungen:
- Eine größere Auskleidungsdicke kann zu einem höheren Streufluss führen, der die Leistung, den Leistungsfaktor und den elektrischen Wirkungsgrad verringert.
- Die richtige Auswahl der feuerfesten Materialien und die Einhaltung des Sinterprozesses sind entscheidend, um diese Herausforderungen zu entschärfen und die Langlebigkeit der Auskleidung zu gewährleisten.
Wenn diese Schritte und Überlegungen befolgt werden, kann die Auskleidung des Induktionsofens effektiv installiert und gewartet werden, so dass eine optimale Leistung und Sicherheit im Metallschmelzbetrieb gewährleistet ist.
Zusammenfassende Tabelle:
Hauptaspekt | Einzelheiten |
---|---|
Zweck | Enthält geschmolzenes Metall, isoliert die Ofenstruktur, gewährleistet Sicherheit und Qualität |
Werkstoffe | Hochreine Aluminiumoxidfaser, vakuumgeformte Faser, leichtes hohles Aluminiumoxid |
Auskleidung Verfahren | Materialvorbereitung, Auftragen und Sintern |
Sinterstufen | Backen (600°C), Semi-Sintern (900°C-1200°C), vollständige Sinterung |
Wartung | Regelmäßige Inspektion, um Verschleiß zu erkennen und optimale Leistung zu gewährleisten |
Herausforderungen | Erhöhte Auskleidungsdicke reduziert Leistung und elektrischen Wirkungsgrad |
Optimieren Sie die Auskleidung Ihres Induktionsofens für Spitzenleistungen. Kontaktieren Sie unsere Experten noch heute !