Abscheidungsbeschichtungen sind in verschiedenen Branchen von entscheidender Bedeutung, um die Oberflächeneigenschaften von Materialien zu verbessern, beispielsweise um die Verschleißfestigkeit, Korrosionsbeständigkeit und das ästhetische Erscheinungsbild zu verbessern. Diese Beschichtungen werden mit unterschiedlichen Techniken aufgetragen, die jeweils für spezifische Anwendungen und Materialanforderungen geeignet sind. Zu den wichtigsten Arten von Abscheidungsbeschichtungen gehören physikalische Gasphasenabscheidung (PVD), chemische Gasphasenabscheidung (CVD), Galvanisieren, thermische Sprühbeschichtung und Atomlagenabscheidung (ALD). Jede Methode weist einzigartige Eigenschaften, Vorteile und Einschränkungen auf, wodurch sie für verschiedene industrielle Anwendungen geeignet ist. Das Verständnis dieser Typen hilft bei der Auswahl der richtigen Beschichtungsmethode basierend auf den gewünschten Eigenschaften und Betriebsbedingungen.
Wichtige Punkte erklärt:
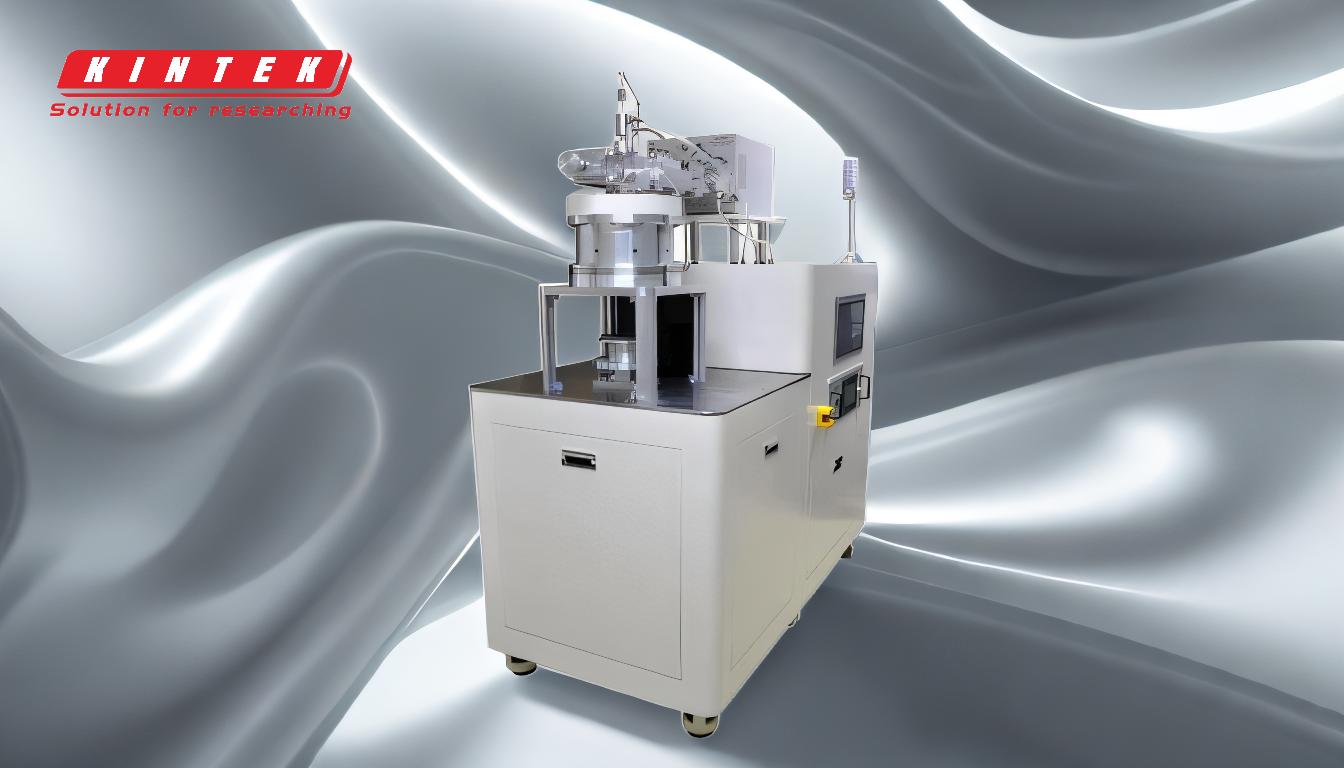
-
Physikalische Gasphasenabscheidung (PVD)
- Verfahren: PVD beinhaltet die Verdampfung eines festen Materials in einer Vakuumumgebung, das dann auf dem Substrat kondensiert und einen dünnen Film bildet.
- Typen: Zu den gängigen PVD-Techniken gehören Sputtern, Verdampfen und Ionenplattieren.
- Anwendungen: Wird häufig in der Luft- und Raumfahrt-, Automobil- und Werkzeugindustrie für Beschichtungen verwendet, die die Härte, Verschleißfestigkeit und thermische Stabilität verbessern.
- Vorteile: Erzeugt hochreine, dichte Beschichtungen mit hervorragender Haftung und minimaler Umweltbelastung.
- Einschränkungen: Erfordert Hochvakuumbedingungen, die kostspielig und komplex sein können.
-
Chemische Gasphasenabscheidung (CVD)
- Verfahren: CVD beinhaltet die chemische Reaktion gasförmiger Vorläufer auf der Substratoberfläche, um eine feste Beschichtung zu bilden.
- Typen: Umfasst Atmosphärendruck-CVD, Niederdruck-CVD und plasmaunterstütztes CVD.
- Anwendungen: Wird in der Halbleiterfertigung, Optik und Schutzbeschichtungen für Hochtemperaturanwendungen verwendet.
- Vorteile: Kann gleichmäßige Beschichtungen auf komplexen Geometrien und großen Flächen erzeugen.
- Einschränkungen: Erfordert häufig hohe Temperaturen und kann gefährliche Nebenprodukte erzeugen.
-
Galvanisieren
- Verfahren: Beim Galvanisieren wird ein elektrischer Strom verwendet, um gelöste Metallkationen zu reduzieren und eine zusammenhängende Metallbeschichtung auf dem Substrat zu bilden.
- Anwendungen: Wird häufig in der Automobil-, Elektronik- und Schmuckindustrie für dekorative Oberflächen und Korrosionsschutz verwendet.
- Vorteile: Relativ niedrige Kosten und Möglichkeit zur Beschichtung einer breiten Palette von Metallen.
- Einschränkungen: Umweltbedenken aufgrund der Verwendung giftiger Chemikalien und Probleme bei der Abfallentsorgung.
-
Thermische Spritzbeschichtung
- Verfahren: Hierbei wird Beschichtungsmaterial geschmolzen oder erhitzt und auf das Substrat aufgesprüht.
- Typen: Umfasst Flammspritzen, Lichtbogenspritzen, Plasmaspritzen und Hochgeschwindigkeits-Autogenspritzen (HVOF).
- Anwendungen: Wird in der Luft- und Raumfahrt, im Energiesektor und im Schwermaschinenbau für Beschichtungen verwendet, die Wärmeisolierung, Verschleißfestigkeit und Korrosionsschutz bieten.
- Vorteile: Kann dicke Schichten auftragen und verschlissene Teile reparieren.
- Einschränkungen: Die Haftung der Beschichtung kann unterschiedlich sein und der Prozess kann zu Porosität führen.
-
Atomlagenabscheidung (ALD)
- Verfahren: ALD ist eine Dampfphasentechnik, die dünne Filme erzeugt, indem das Substrat nacheinander verschiedenen Vorläufern ausgesetzt wird.
- Anwendungen: Wird hauptsächlich in der Mikroelektronik, Photovoltaik und Nanotechnologie für ultradünne, gleichmäßige Beschichtungen verwendet.
- Vorteile: Hervorragende Kontrolle über Filmdicke und Zusammensetzung auf atomarer Ebene.
- Einschränkungen: Langsame Abscheidungsraten und hohe Kosten, wodurch der Einsatz auf hochwertige Anwendungen beschränkt ist.
Das Verständnis dieser Abscheidungsbeschichtungsmethoden ermöglicht eine fundierte Entscheidungsfindung bei der Auswahl der geeigneten Technik auf der Grundlage der spezifischen Anforderungen der Anwendung, wie z. B. der Art des Substrats, der gewünschten Beschichtungseigenschaften und der Betriebsbedingungen. Jede Methode bietet unterschiedliche Vorteile und Herausforderungen und eignet sich daher für unterschiedliche industrielle Anforderungen.
Übersichtstabelle:
Typ | Verfahren | Anwendungen | Vorteile | Einschränkungen |
---|---|---|---|---|
Physikalische Gasphasenabscheidung (PVD) | Verdampfung von Feststoffen im Vakuum, Kondensierung auf dem Substrat. | Luft- und Raumfahrt, Automobilindustrie, Werkzeuge für Härte, Verschleißfestigkeit und thermische Stabilität. | Hochreine, dichte Beschichtungen; ausgezeichnete Haftung; minimale Umweltbelastung. | Hochvakuumbedingungen; kostspielige und komplexe Einrichtung. |
Chemische Gasphasenabscheidung (CVD) | Chemische Reaktion gasförmiger Vorläufer auf Substrat. | Halbleiter, Optik, Hochtemperatur-Schutzbeschichtungen. | Gleichmäßige Beschichtungen über komplexe Geometrien; großflächige Abdeckung. | Hohe Temperaturen; gefährliche Nebenprodukte. |
Galvanisieren | Elektrischer Strom reduziert Metallkationen und bildet eine Metallbeschichtung. | Automobil, Elektronik, Schmuck für dekorative Oberflächen, Korrosionsschutz. | Niedrige Kosten; große Auswahl an Metallen. | Giftige Chemikalien; Umweltbedenken. |
Thermische Spritzbeschichtung | Material schmelzen/erwärmen und auf den Untergrund sprühen. | Luft- und Raumfahrt, Energie, schwere Maschinen zur Wärmedämmung, Verschleiß, Korrosion. | Dicke Beschichtungen; Reparaturmöglichkeiten. | Variable Haftung; Porosität in Beschichtungen. |
Atomlagenabscheidung (ALD) | Sequentielle Belichtung mit Vorläufern für ultradünne Filme. | Mikroelektronik, Photovoltaik, Nanotechnologie. | Kontrolle der Dicke und Zusammensetzung auf atomarer Ebene. | Langsame Ablagerungsraten; hohe Kosten. |
Benötigen Sie Hilfe bei der Auswahl der richtigen Abscheidungsbeschichtung für Ihre Anwendung? Kontaktieren Sie noch heute unsere Experten!