Nitrieren und Aufkohlen sind beides Einsatzhärtungsverfahren, die zur Verbesserung der Oberflächeneigenschaften von Metallen eingesetzt werden, aber sie unterscheiden sich deutlich in ihren Anwendungen, Vor- und Nachteilen.Während das Nitrieren Vorteile wie verbesserte Härte, Verschleißfestigkeit und Ermüdungsfestigkeit bietet, hat es im Vergleich zum Aufkohlen auch einige Nachteile.Dazu gehören Einschränkungen bei der Einsatztiefe, der Materialverträglichkeit, der Prozesstemperatur und den Nachbehandlungsanforderungen.Im Folgenden werden die wichtigsten Nachteile des Nitrierens gegenüber dem Aufkohlen im Detail erläutert.
Die wichtigsten Punkte werden erklärt:
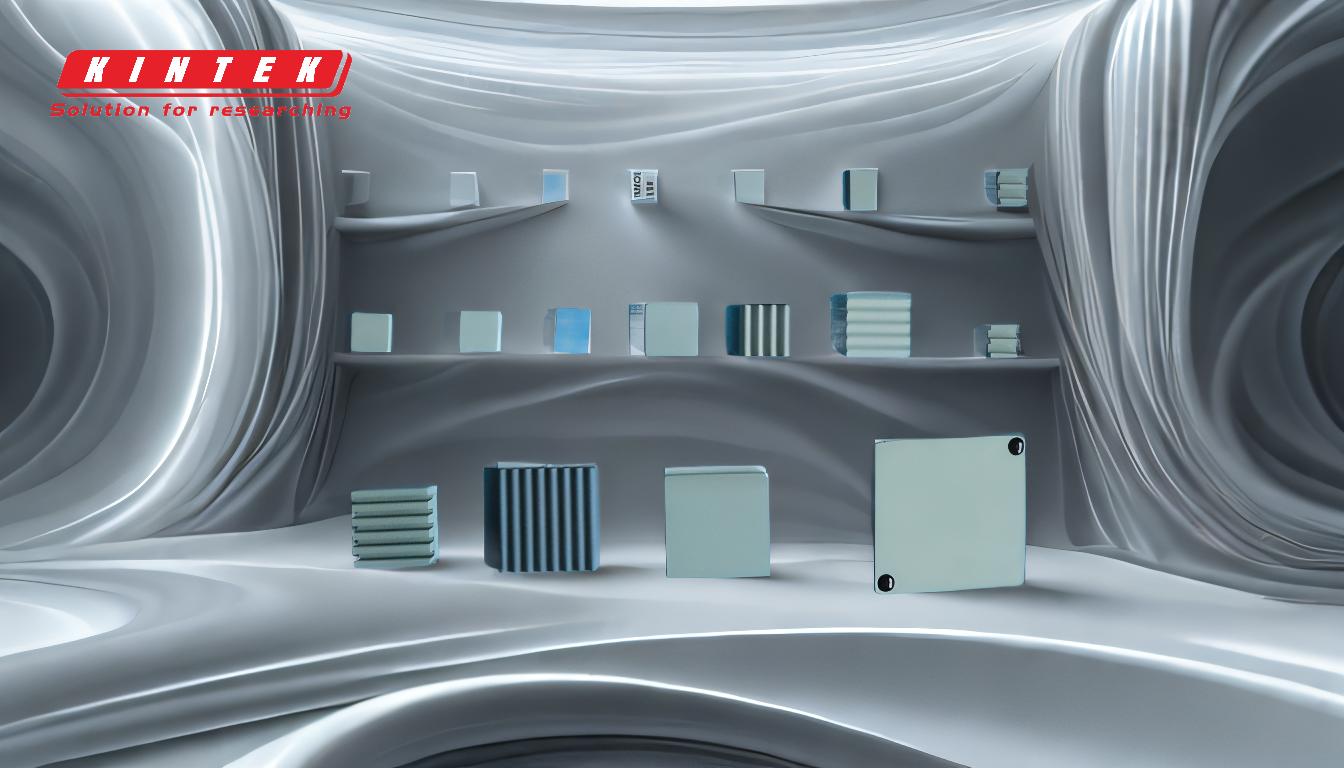
-
Begrenzte Einsatztiefe
- Beim Nitrieren wird in der Regel eine geringere Einsatztiefe als beim Aufkohlen erreicht.
- Beim Aufkohlen können Einsatztiefen von 0,5 mm bis 2 mm oder mehr erreicht werden, je nach Prozessdauer und Werkstoff.
- Beim Nitrieren hingegen werden in der Regel Einsatzhärtetiefen von 0,1 mm bis 0,6 mm erreicht, was für Anwendungen, die tiefere Härteschichten erfordern, unter Umständen nicht ausreichend ist.
- Diese Einschränkung macht das Nitrieren weniger geeignet für Teile, die hohem Verschleiß oder schweren Belastungen ausgesetzt sind und bei denen eine dickere Härteschicht erforderlich ist.
-
Materialverträglichkeit
- Das Nitrieren ist in erster Linie bei bestimmten legierten Stählen wirksam, z. B. bei chrom-, molybdän- und aluminiumhaltigen Stählen, die harte Nitride bilden.
- Das Aufkohlen hingegen kann auf eine breitere Palette von kohlenstoffarmen und legierten Stählen angewendet werden und ist daher vielseitiger.
- Diese eingeschränkte Materialkompatibilität des Nitrierens schränkt seine Verwendung in Industrien ein, in denen eine Vielzahl von Stahlsorten verwendet wird.
-
Niedrigere Prozesstemperatur
- Das Nitrieren wird bei relativ niedrigen Temperaturen (typischerweise 500°C bis 570°C) durchgeführt, verglichen mit dem Aufkohlen (typischerweise 850°C bis 950°C).
- Die niedrigere Temperatur verringert zwar den Verzug und den Energieverbrauch, begrenzt aber auch die Diffusion von Stickstoff in das Metall, was zu einer geringeren Einsatztiefe führt.
- Die höhere Temperatur des Aufkohlens ermöglicht eine tiefere Kohlenstoffdiffusion und ist daher effektiver für Anwendungen, die eine starke Einsatzhärtung erfordern.
-
Anforderungen an die Nachbehandlung
- Beim Nitrieren ist kein Abschrecken nach dem Prozess erforderlich, was die Gefahr des Verzugs verringert.
- Das Fehlen des Abschreckens bedeutet jedoch, dass nitrierte Teile eine geringere Kernhärte aufweisen können als aufgekohlte Teile, die durch Abschrecken und Anlassen eine harte Oberfläche und einen zähen Kern erhalten.
- Diese Einschränkung kann die mechanische Gesamtleistung von nitrierten Bauteilen beeinträchtigen, insbesondere bei Anwendungen mit hoher Beanspruchung.
-
Oberflächenbeschaffenheit und Ästhetik
- Das Nitrieren kann manchmal zu einer Oberflächenbeschaffenheit führen, die aufgrund der Bildung einer spröden "weißen Schicht" (einer Verbundschicht aus Eisennitriden) weniger ästhetisch ist.
- Diese Schicht erfordert unter Umständen eine zusätzliche Nachbearbeitung, wie Schleifen oder Polieren, um die gewünschte Oberflächenqualität zu erreichen.
- Das Aufkohlen mit anschließendem Vergüten führt im Allgemeinen zu einer glatteren und gleichmäßigeren Oberfläche, so dass weniger zusätzliche Bearbeitungsschritte erforderlich sind.
-
Kosten und Komplexität
- Nitrierverfahren, wie das Gas- oder Plasmanitrieren, können im Vergleich zum Aufkohlen komplexer und kostspieliger sein.
- Die Notwendigkeit, stickstoffhaltige Atmosphären oder Plasmaumgebungen genau zu steuern, erhöht die Anlagen- und Betriebskosten.
- Das Aufkohlen ist ein etablierteres und weit verbreitetes Verfahren, das oft kostengünstiger ist und sich leichter in großen Produktionsumgebungen einsetzen lässt.
-
Anwendungsspezifische Beschränkungen
- Das Nitrieren ist für Teile, die durchgehärtet werden müssen oder die hohen Stoßbelastungen ausgesetzt sind, weniger effektiv, da es in erster Linie die Oberfläche härtet.
- Das Aufkohlen mit seiner größeren Einsatztiefe und der Fähigkeit, sowohl die Oberfläche als auch den Kern zu härten, ist für solche Anwendungen besser geeignet.
- Außerdem können nitrierte Teile eine geringere Zähigkeit aufweisen, wodurch sie für dynamische oder stoßbelastete Umgebungen weniger geeignet sind.
Zusammenfassend lässt sich sagen, dass das Nitrieren zwar Vorteile wie geringeren Verzug und verbesserte Verschleißfestigkeit bietet, seine Nachteile - wie begrenzte Einsatztiefe, eingeschränkte Materialkompatibilität und höhere Kosten - das Aufkohlen jedoch zu einer vielseitigeren und effektiveren Wahl für viele industrielle Anwendungen machen.Die Entscheidung zwischen Nitrieren und Aufkohlen hängt letztendlich von den spezifischen Anforderungen an das Teil ab, einschließlich der beabsichtigten Verwendung, der Materialzusammensetzung und der gewünschten mechanischen Eigenschaften.
Zusammenfassende Tabelle:
Aspekt | Nitrieren | Aufkohlen |
---|---|---|
Einsatztiefe | 0,1 mm bis 0,6 mm (dünner) | 0,5 mm bis 2 mm oder mehr (tiefer) |
Material-Kompatibilität | Begrenzt auf bestimmte legierte Stähle (z. B. Cr, Mo, Al) | Kompatibel mit einer breiten Palette von kohlenstoffarmen und legierten Stählen |
Prozess-Temperatur | 500°C bis 570°C (niedriger) | 850°C bis 950°C (höher) |
Nachbehandlung | Kein Abschrecken erforderlich (geringere Kernhärte) | Abschrecken und Anlassen (höhere Kernhärte) |
Oberflächengüte | Kann aufgrund der spröden "weißen Schicht" zusätzliche Nachbearbeitung erfordern. | Glattere und gleichmäßigere Oberfläche |
Kosten und Komplexität | Höhere Kosten und Komplexität (z. B. Gas-/Plasma-Nitrieren) | Kostengünstiger und einfacher zu implementieren |
Anwendungen | Weniger effektiv für Anwendungen mit hoher Schlagbeanspruchung oder Durchhärtung | Besser geeignet für Anwendungen mit hoher Schlagbeanspruchung und Durchhärtung |
Benötigen Sie Hilfe bei der Auswahl des richtigen Einsatzhärtungsverfahrens für Ihre Anwendung? Kontaktieren Sie unsere Experten noch heute!