Die Kalzinierung ist ein thermischer Behandlungsprozess, der bei Erzen und anderen festen Materialien angewandt wird, um eine thermische Zersetzung, einen Phasenübergang oder die Entfernung eines flüchtigen Anteils zu erreichen. Der Prozess wird von mehreren Faktoren beeinflusst, darunter Temperatur, Zeit, Atmosphäre, Partikelgröße und die chemische Zusammensetzung des Materials. Das Verständnis dieser Faktoren ist entscheidend für die Optimierung der Kalzinierung, um die gewünschten Ergebnisse wie verbesserte Materialeigenschaften oder eine effiziente Entfernung von Verunreinigungen zu erzielen. Im Folgenden werden die wichtigsten Faktoren, die die Kalzinierung beeinflussen, und ihre Auswirkungen untersucht.
Die wichtigsten Punkte werden erklärt:
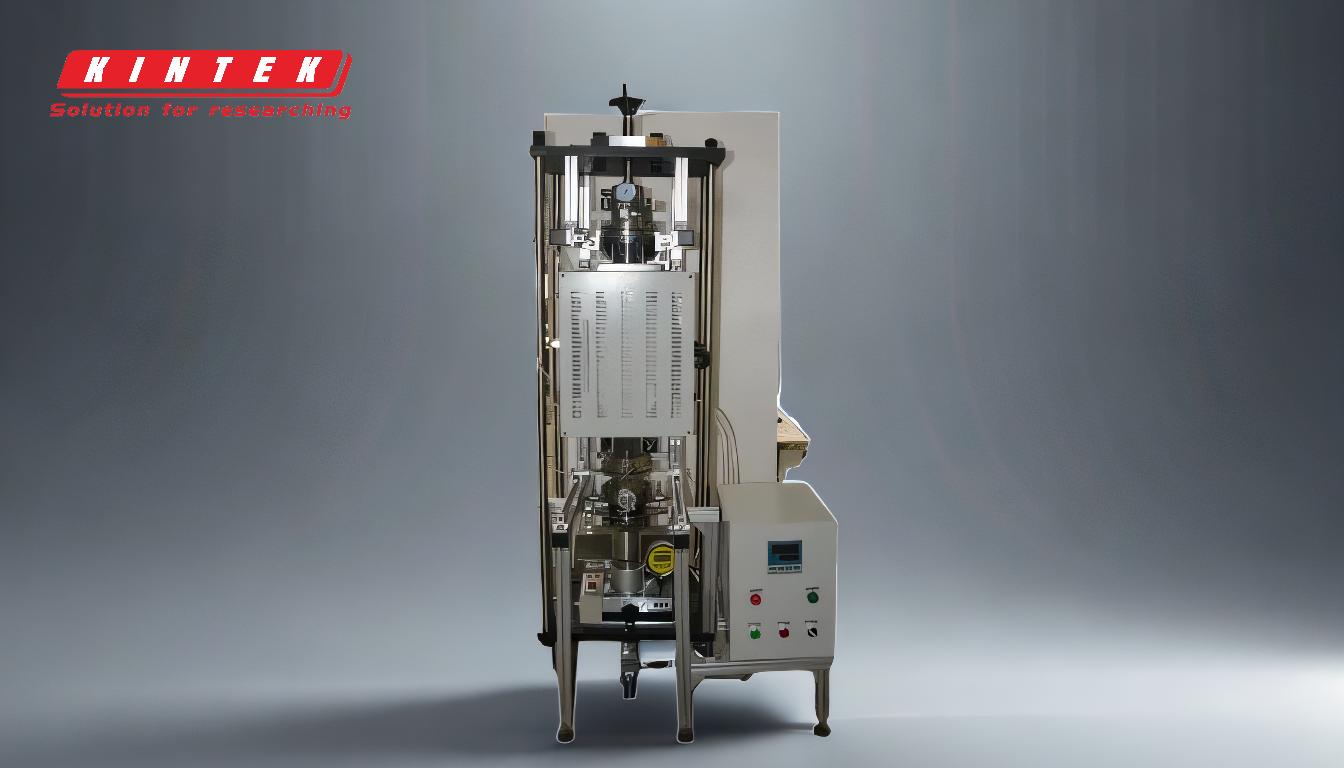
-
Temperatur
- Rolle: Die Temperatur ist der wichtigste Faktor bei der Kalzinierung, da sie die Geschwindigkeit und das Ausmaß der chemischen Reaktionen direkt beeinflusst.
-
Auswirkungen:
- Eine zu niedrige Temperatur kann zu einer unvollständigen Zersetzung oder einem Phasenübergang führen.
- Eine zu hohe Temperatur kann zu einer Überkalkung führen, die unerwünschte Veränderungen der Materialeigenschaften, wie z. B. Versinterung oder Verlust der Reaktivität, zur Folge hat.
- Beispiel: Kalkstein (CaCO₃) wird normalerweise bei 800-900°C gebrannt, um Kalk (CaO) und CO₂ zu erzeugen. Eine Abweichung von diesem Bereich kann die Qualität des Kalkes beeinträchtigen.
-
Zeit
- Rolle: Die Dauer der Kalzinierung bestimmt, wie gründlich das Material die gewünschte Umwandlung durchläuft.
-
Auswirkungen:
- Bei unzureichender Zeit kann nicht oder nur teilweise reagiertes Material zurückbleiben.
- Ein zu langer Zeitraum kann zu einer Überkalkung führen, wodurch Energie verschwendet und das Material möglicherweise beschädigt wird.
- Optimierung: Zeit und Temperatur müssen aufeinander abgestimmt sein, um eine effiziente und vollständige Kalzinierung zu gewährleisten.
-
Atmosphäre
- Rolle: Die gasförmige Umgebung während der Kalzinierung kann den Prozess erheblich beeinflussen.
-
Auswirkungen:
- In einer oxidierenden Atmosphäre kann Sauerstoff mit bestimmten Materialien reagieren und deren Zusammensetzung verändern.
- In einer reduzierenden Atmosphäre ist der Sauerstoffgehalt begrenzt, was die Oxidation verhindern oder die Entfernung flüchtiger Bestandteile erleichtern kann.
- Inerte Atmosphären (z. B. Stickstoff oder Argon) werden verwendet, wenn die Reaktivität mit Gasen minimiert werden muss.
- Beispiel: Die Kalzinierung von Metallkarbonaten erfordert häufig eine kontrollierte Atmosphäre, um eine unerwünschte Oxidation der entstehenden Metalloxide zu verhindern.
-
Partikelgröße
- Rolle: Die Größe der zu kalzinierenden Partikel beeinflusst die Wärmeübertragung und die Reaktionskinetik.
-
Auswirkungen:
- Kleinere Partikel haben eine größere Oberfläche und ermöglichen eine schnellere und gleichmäßigere Erwärmung.
- Größere Partikel können ungleichmäßig erhitzt werden, was zu einer unvollständigen Kalzinierung im Kern führt.
- Optimierung: Das Zerkleinern von Materialien auf eine einheitliche und angemessene Partikelgröße kann die Effizienz der Kalzinierung erhöhen.
-
Chemische Zusammensetzung
- Rolle: Die inhärenten Eigenschaften des Materials, wie z. B. seine chemische Zusammensetzung und Struktur, beeinflussen, wie es auf die Kalzinierung reagiert.
-
Auswirkungen:
- Materialien mit einem höheren Gehalt an flüchtigen Bestandteilen (z. B. Hydrate oder Karbonate) erfordern eine sorgfältige Temperatur- und Zeitkontrolle, um eine vollständige Zersetzung zu gewährleisten.
- Verunreinigungen im Material können den Kalzinierungsprozess beeinflussen, indem sie entweder die erforderliche Temperatur senken oder unerwünschte Nebenprodukte bilden.
- Beispiel: Das Vorhandensein von Siliziumdioxid im Bauxit kann die Kalzinierung von Aluminiumoxid beeinträchtigen, was eine Anpassung der Prozessparameter erfordert.
-
Heizrate
- Rolle: Die Geschwindigkeit, mit der das Material erhitzt wird, kann die Gleichmäßigkeit und Qualität der Kalzinierung beeinflussen.
-
Auswirkungen:
- Schnelles Erhitzen kann einen thermischen Schock verursachen, der zu Rissen oder ungleichmäßiger Zersetzung führt.
- Langsames Erhitzen gewährleistet eine gleichmäßige Temperaturverteilung, kann aber den Prozess verlängern und den Energieverbrauch erhöhen.
- Optimierung: Für eine effiziente und qualitativ hochwertige Kalzinierung ist eine ausgewogene Heizrate unerlässlich.
-
Abkühlungsrate
- Rolle: Die Geschwindigkeit, mit der das Material nach dem Kalzinieren abgekühlt wird, kann seine endgültigen Eigenschaften beeinflussen.
-
Auswirkungen:
- Eine schnelle Abkühlung kann zu thermischen Spannungen führen, die Risse oder Phaseninstabilität verursachen.
- Die langsame Abkühlung ermöglicht eine kontrollierte Kristallisation und Stabilisierung des Materials.
- Beispiel: Bei der Herstellung von Zementklinker ist eine kontrollierte Abkühlung entscheidend, um die gewünschten kristallinen Phasen zu erhalten.
-
Ausrüstung Design
- Rolle: Die Art der Kalzinierungsanlagen (z. B. Drehrohröfen, Wirbelschichtreaktoren oder statische Öfen) wirkt sich auf die Wärmeübertragung, die Verweilzeit und die Gesamteffizienz aus.
-
Auswirkungen:
- Drehrohröfen ermöglichen eine kontinuierliche Verarbeitung und eine gleichmäßige Erwärmung, können aber einen höheren Energieverbrauch haben.
- Wirbelschichtreaktoren bieten eine hervorragende Wärmeübertragung und kürzere Verarbeitungszeiten, sind jedoch nicht für alle Materialien geeignet.
- Optimierung: Die Auswahl der richtigen Ausrüstung auf der Grundlage der Materialeigenschaften und der Prozessanforderungen ist für eine effektive Kalzinierung unerlässlich.
-
Energieeinsatz
- Rolle: Die Menge und die Art der für die Kalzinierung verwendeten Energie beeinflussen die Kosten und die Umweltauswirkungen des Verfahrens.
-
Auswirkungen:
- Ein hoher Energieverbrauch erhöht die Betriebskosten und den ökologischen Fußabdruck.
- Erneuerbare oder Abwärmequellen können die Energiekosten senken und die Nachhaltigkeit verbessern.
- Optimierung: Energieeffiziente Konzepte und alternative Energiequellen können die wirtschaftliche und ökologische Tragfähigkeit der Kalzinierung verbessern.
-
Material-Vorschubgeschwindigkeit
- Rolle: Die Geschwindigkeit, mit der das Material dem Kalzinierungssystem zugeführt wird, beeinflusst die Verweilzeit und die Wärmeverteilung.
-
Auswirkungen:
- Eine hohe Vorschubgeschwindigkeit kann die Verweilzeit verkürzen und zu einer unvollständigen Kalzinierung führen.
- Eine niedrige Vorschubgeschwindigkeit gewährleistet eine gründliche Verarbeitung, kann aber den Durchsatz verringern.
- Optimierung: Die Abstimmung der Vorschubgeschwindigkeit mit anderen Parametern ist entscheidend für optimale Ergebnisse.
Durch sorgfältige Kontrolle dieser Faktoren kann die Kalzinierung optimiert werden, um die gewünschten Materialeigenschaften zu erzielen, den Energieverbrauch zu minimieren und die Umweltbelastung zu verringern. Jeder Faktor steht in Wechselwirkung mit den anderen und erfordert einen ganzheitlichen Ansatz für die Prozessgestaltung und den Betrieb.
Zusammenfassende Tabelle:
Faktor | Rolle | Auswirkungen |
---|---|---|
Temperatur | Beeinflusst die Geschwindigkeit und das Ausmaß von chemischen Reaktionen. | Zu niedrig: Unvollständige Zersetzung. Zu hoch: Überkalkung und Materialverschlechterung. |
Zeit | Bestimmt die Gründlichkeit der Transformation. | Unzureichend: Unreagiertes Material. Überschüssig: Energieverschwendung und Materialverschlechterung. |
Atmosphäre | Beeinflusst die chemischen Reaktionen während der Kalzinierung. | Oxidierende, reduzierende oder inerte Atmosphären verändern die Materialzusammensetzung und -zersetzung. |
Partikelgröße | Beeinflusst Wärmeübertragung und Reaktionskinetik. | Kleinere Partikel: Schnellere, gleichmäßige Erwärmung. Größere Partikel: Ungleichmäßige Erwärmung. |
Chemische Zusammensetzung | Bestimmt die Reaktion des Materials auf die Kalzinierung. | Der Gehalt an flüchtigen Bestandteilen und Verunreinigungen beeinflusst die Zersetzung und die Bildung von Nebenprodukten. |
Heizrate | Beeinflusst die Gleichmäßigkeit und Qualität der Kalzinierung. | Schnelle Erhitzung: Thermoschock. Langsame Erwärmung: Gleichmäßige Temperatur, aber höherer Energieverbrauch. |
Abkühlungsrate | Beeinflusst die endgültigen Materialeigenschaften. | Schnelle Abkühlung: Thermische Belastung. Langsame Abkühlung: Kontrollierte Kristallisation. |
Ausrüstung Design | Beeinflusst Wärmeübertragung, Verweilzeit und Effizienz. | Drehrohröfen, Wirbelschichtreaktoren oder statische Öfen beeinflussen das Prozessergebnis. |
Energieeinsatz | Ermittelt die Kosten und Umweltauswirkungen. | Ein hoher Energieverbrauch erhöht die Kosten. Erneuerbare Quellen verbessern die Nachhaltigkeit. |
Material-Vorschubgeschwindigkeit | Beeinflusst die Verweilzeit und die Wärmeverteilung. | Hohe Vorschubgeschwindigkeit: Unvollständige Kalzinierung. Niedrige Vorschubgeschwindigkeit: Gründliche Verarbeitung, aber geringerer Ausstoß. |
Optimieren Sie Ihren Kalzinierungsprozess mit fachkundiger Anleitung kontaktieren Sie uns noch heute !