Das Flüssigphasensintern (LPS) ist ein in der Pulvermetallurgie und Keramik weit verbreitetes Verfahren, bei dem eine flüssige Phase die Verdichtung und Bindung von Feststoffpartikeln erleichtert.Es bietet zwar Vorteile wie eine verbesserte Verdichtung und die Möglichkeit, komplexe Formen herzustellen, hat aber auch einige Nachteile.Dazu gehören hohe Kosten aufgrund teurer Anlagen und des Energieverbrauchs, Probleme beim Erreichen gleichmäßiger Eigenschaften und potenzielle Defekte wie Verzug oder Durchbiegung.Darüber hinaus kann das Verfahren spezielle Materialien und eine genaue Kontrolle der Parameter erfordern, was es komplex und weniger geeignet für die Produktion in großem Maßstab oder für Anwendungen macht, die eine hohe mechanische Festigkeit erfordern.
Die wichtigsten Punkte werden erklärt:
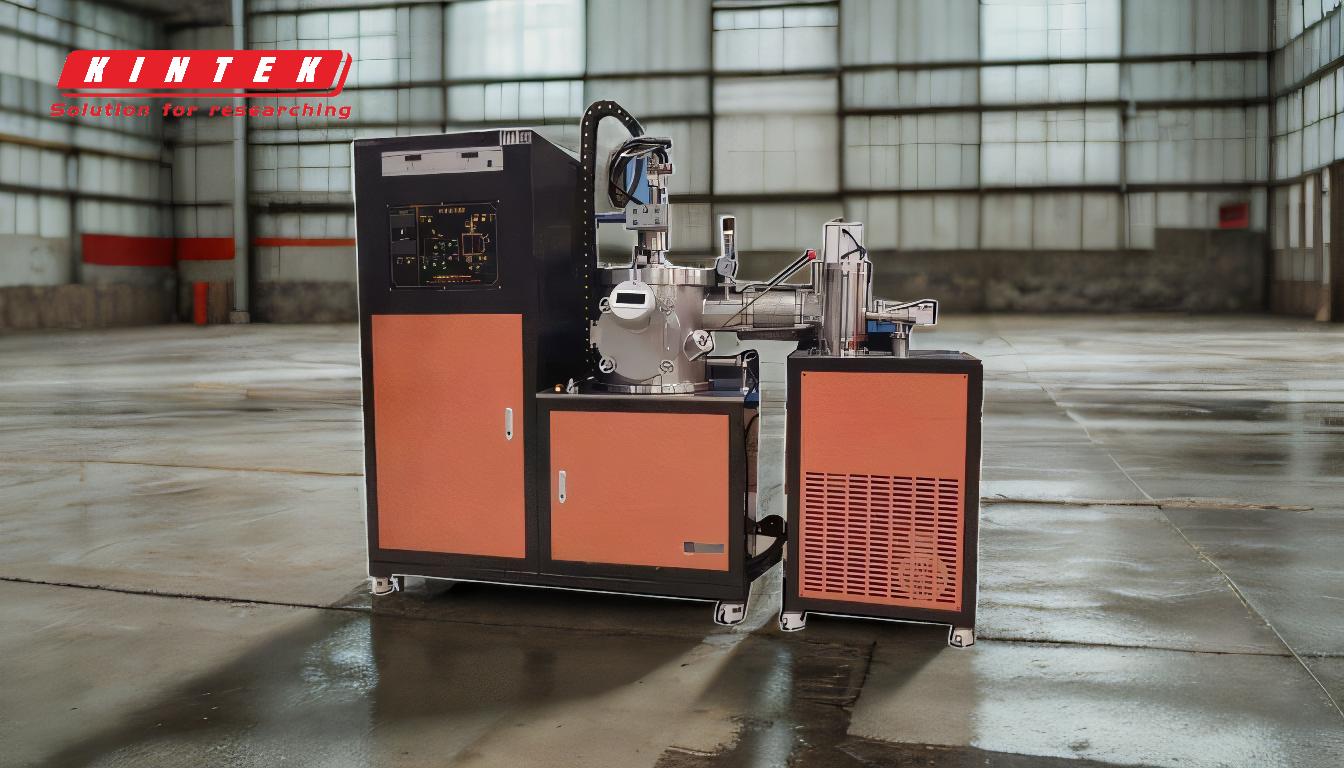
-
Hohe Ausrüstungs- und Betriebskosten
- Für die Flüssigphasensinterung sind häufig spezielle Öfen erforderlich, die präzise Temperaturen und Atmosphären aufrechterhalten können und die in der Anschaffung und Wartung teuer sind.
- Der Prozess erfordert einen erheblichen Energieverbrauch, insbesondere beim Hochtemperatursintern, was zu höheren Betriebskosten führt.
- Für den Betrieb und die Wartung der Anlagen ist Fachwissen erforderlich, was die Arbeitskosten erhöht.
-
Material- und Prozessbeschränkungen
- Das Verfahren erfordert möglicherweise bestimmte Materialien oder Zusatzstoffe zur Bildung der flüssigen Phase, was die Materialkosten erhöhen kann.
- Es ist schwierig, eine gleichmäßige Verteilung der flüssigen Phase zu erreichen, was zu ungleichmäßigen Eigenschaften des Endprodukts führen kann.
- Das Verfahren eignet sich möglicherweise nicht für Materialien, die empfindlich auf hohe Temperaturen reagieren oder zu übermäßiger Schrumpfung neigen.
-
Mögliche Defekte
- Beim Sintern in der Flüssigphase kommt es aufgrund von Schwerkraft oder Reibung häufig zu Verformungen und Durchhängen, was zu Maßungenauigkeiten oder Defekten im fertigen Teil führen kann.
- Eine übermäßige Schrumpfung während des Sinterns kann den Entwurfs- und Produktionsprozess erschweren und erfordert eine sorgfältige Kompensation in der Anfangsphase.
-
Beschränkungen hinsichtlich Größe und Komplexität
- Ähnlich wie bei anderen pulvermetallurgischen Verfahren kann das Flüssigphasensintern bei der Herstellung großer oder komplex geformter Teile an Grenzen stoßen.
- Das Verfahren erreicht möglicherweise nicht die gleiche mechanische Festigkeit oder Duktilität wie herkömmliche Guss- oder Schmiedeverfahren, was seinen Einsatz bei Hochleistungsanwendungen einschränkt.
-
Geringe Produktivität und Ausstoß
- Der Sinterprozess ist oft zeitaufwändig, mit langen Zykluszeiten, die die Gesamtproduktivität verringern.
- Der Ausstoß pro Ofen ist in der Regel gering, so dass es im Vergleich zu anderen Herstellungsverfahren weniger effizient für die Großproduktion ist.
-
Technische Komplexität
- Das Verfahren erfordert eine präzise Steuerung von Parametern wie Temperatur, Druck und Atmosphäre, was es technisch anspruchsvoll macht.
- Für unterschiedliche Materialien können Anpassungen erforderlich sein, was den Vorgang komplexer macht und das Fehlerrisiko erhöht.
Zusammenfassend lässt sich sagen, dass das Flüssigphasensintern zwar einzigartige Vorteile bietet, aber aufgrund seiner Nachteile - wie hohe Kosten, technische Komplexität und mögliche Fehler - für bestimmte Anwendungen weniger geeignet ist.Eine sorgfältige Abwägung dieser Faktoren ist bei der Wahl dieses Verfahrens für die Herstellung unerlässlich.
Zusammenfassende Tabelle:
Nachteil | Zentrale Herausforderungen |
---|---|
Hohe Ausrüstungskosten | Teure Spezialöfen, hoher Energieverbrauch und hohe Arbeitskosten. |
Materialbedingte Einschränkungen | Erfordert spezifische Zusatzstoffe, ungleichmäßige Verteilung der flüssigen Phase und Materialprobleme. |
Mögliche Defekte | Verformung, Durchbiegung und übermäßige Schrumpfung während des Sinterns. |
Begrenzte Größe und Komplexität | Begrenzte Fähigkeit zur Herstellung großer oder komplexer Teile mit hoher mechanischer Festigkeit. |
Geringe Produktivität | Zeitaufwändiger Prozess mit geringem Ausstoß pro Ofen. |
Technische Komplexität | Präzise Steuerung von Temperatur, Druck und Atmosphäre erforderlich. |
Benötigen Sie Hilfe bei der Bewältigung der Herausforderungen des Flüssigphasensinterns? Kontaktieren Sie noch heute unsere Experten für maßgeschneiderte Lösungen!