Das Spark-Plasma-Sintern (SPS) ist ein modernes Sinterverfahren, das einachsigen Druck und gepulsten Gleichstrom kombiniert, um Pulver schnell zu dichten, homogenen Materialien zu verdichten.Das Verfahren zeichnet sich durch seine Schnelligkeit, Effizienz und die Fähigkeit aus, im Vergleich zu herkömmlichen Sinterverfahren eine hohe Verdichtung bei niedrigeren Temperaturen zu erreichen.Zu den wichtigsten Phasen des SPS-Verfahrens gehören Gasentfernung und Vakuumerzeugung, Anlegen von Druck, Widerstandserhitzung und Kühlung.Jede Stufe spielt eine entscheidende Rolle für die erfolgreiche Verdichtung und Bindung der Pulverpartikel.Das Verfahren nutzt Plasmaentladung, Joule-Erwärmung und plastische Verformung, um eine schnelle Erwärmung, Partikelbindung und Materialverfestigung zu erreichen.
Die wichtigsten Punkte werden erklärt:
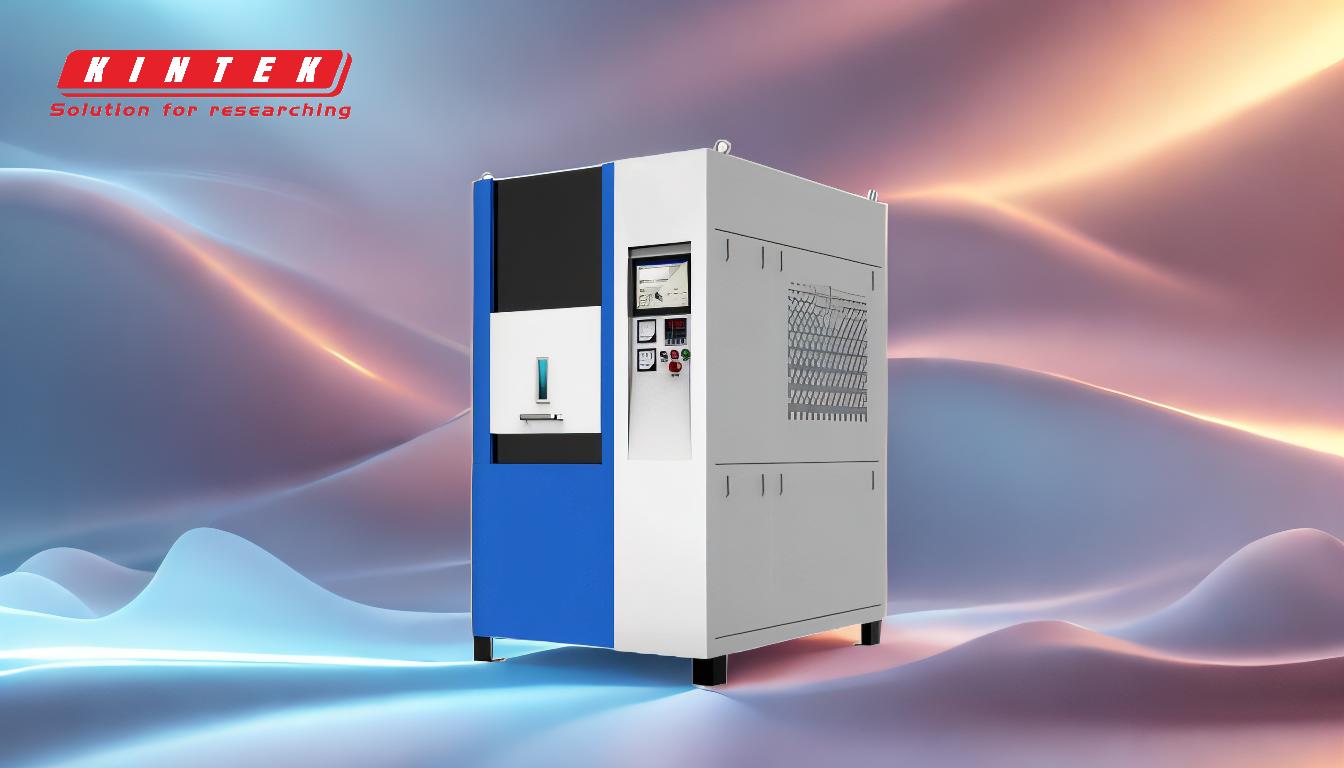
-
Gasentfernung und Vakuumerzeugung
- Der erste Schritt bei SPS besteht darin, die Gase aus der Sinterkammer zu entfernen und ein Vakuum oder eine kontrollierte Atmosphäre zu erzeugen.
- Dies ist entscheidend, um Oxidation und Verunreinigung des Pulvermaterials zu verhindern und die Reinheit und Qualität des Endprodukts zu gewährleisten.
- A Vakuumumgebung ermöglicht auch eine bessere Wärmeübertragung und Plasmaerzeugung in den nachfolgenden Phasen.
-
Anwendung von Druck
- Der einachsige Druck wird auf das Pulvermaterial in einer Matrize ausgeübt, die normalerweise aus Graphit .
- Der Druck trägt dazu bei, die Pulverteilchen zu verdichten, die Lücken zwischen ihnen zu verringern und einen besseren Kontakt für das Sintern zu fördern.
- Der ausgeübte Druck unterstützt auch die plastische Verformung der Partikel, die für eine hohe Verdichtung unerlässlich ist.
-
Widerstandsheizung
- Gepulster Gleichstrom wird durch die Graphitmatrize und, falls leitfähig, durch das Pulvermaterial selbst geleitet.
- Dadurch entstehen lokal hohe Temperaturen und Plasmaentladungen zwischen den Partikeln, die eine schnelle Erhitzung bewirken.
-
Der Prozess umfasst drei Heizmechanismen:
- Plasma-Erwärmung:Durch die Entladung zwischen den Partikeln entsteht ein Plasma, das die Oberflächendiffusion und die Bindung erleichtert.
- Joule-Erwärmung:Der elektrische Widerstand im Material erzeugt Wärme, die die Sinterung weiter unterstützt.
- Plastische Verformung:Durch die Kombination von Hitze und Druck verformen sich die Partikel und verbinden sich an ihren Grenzflächen.
- Diese Mechanismen ermöglichen eine Sinterung bei wesentlich niedrigeren Temperaturen und kürzeren Zeiten als bei herkömmlichen Verfahren.
-
Abkühlungsphase
- Nach dem Sinterprozess wird das Material schnell auf Raumtemperatur abgekühlt.
- Die rasche Abkühlung trägt dazu bei, dass die Mikrostruktur und die Eigenschaften des gesinterten Materials erhalten bleiben.
- Die Abkühlgeschwindigkeit wird kontrolliert, um thermische Spannungen oder Risse im Endprodukt zu vermeiden.
-
Vorteile von SPS
- Geschwindigkeit:SPS schließt den Sinterprozess in einem Bruchteil der Zeit ab, die bei herkömmlichen Verfahren benötigt wird.
- Niedrigere Temperaturen:SPS erreicht eine Verdichtung bei Temperaturen, die mehrere hundert Grad niedriger sind als beim herkömmlichen Sintern.
- Verbesserte Materialeigenschaften:Die schnellen Erwärmungs- und Abkühlungsraten führen zu feineren Mikrostrukturen und verbesserten mechanischen Eigenschaften.
- Vielseitigkeit:SPS kann für eine breite Palette von Materialien verwendet werden, darunter Keramik, Metalle und Verbundwerkstoffe.
-
Anwendungen von SPS
- SPS findet breite Anwendung bei der Herstellung von Hochleistungswerkstoffen wie nanostrukturierten Keramiken, funktional abgestuften Materialien und Verbundwerkstoffen.
- Sie ist besonders wertvoll in Branchen, die Hochleistungswerkstoffe mit präziser Kontrolle über Mikrostruktur und Eigenschaften benötigen, z. B. in der Luft- und Raumfahrt, der Automobilindustrie und der Elektronik.
Durch Befolgen dieser Schritte, Spark-Plasma-Sintern ermöglicht die Herstellung hochwertiger, dichter Werkstoffe mit überlegenen Eigenschaften, was es zu einem bevorzugten Verfahren für die Herstellung moderner Werkstoffe macht.
Zusammenfassende Tabelle:
Stufe | Wichtige Details |
---|---|
Gasentfernung & Vakuum | Entfernt Gase, verhindert Oxidation und sorgt für eine kontrollierte Atmosphäre. |
Anwendung von Druck | Verdichtet die Pulverpartikel, verringert die Lücken und unterstützt die plastische Verformung. |
Widerstandsheizung | Verwendet gepulsten Gleichstrom für Plasmaentladung, Joule-Erwärmung und schnelle Partikelbindung. |
Abkühlungsphase | Die schnelle Abkühlung erhält das Gefüge und verhindert thermische Spannungen. |
Vorteile | Geschwindigkeit, niedrigere Temperaturen, verbesserte Eigenschaften und Vielseitigkeit des Materials. |
Anwendungen | Luft- und Raumfahrt, Automobilbau, Elektronik und Herstellung moderner Werkstoffe. |
Erfahren Sie, wie das Spark-Plasma-Sintern Ihren Materialherstellungsprozess revolutionieren kann. Kontaktieren Sie uns noch heute !