Entbindern und Sintern sind entscheidende Schritte in pulvermetallurgischen und keramischen Herstellungsverfahren.Beim Entbindern werden die Bindemittel von einem Formteil entfernt, was in der Regel durch thermischen Abbau, Verdampfung oder Lösungsmittelextraktion geschieht.Das Sintern folgt auf das Entbindern und beinhaltet das Erhitzen des Teils auf hohe Temperaturen, um die Metall- oder Keramikpartikel zu verschmelzen, was zu einem dichten und festen Endprodukt führt.Diese Prozesse werden sorgfältig gesteuert, mit spezifischen Temperaturprofilen, Heizraten und Haltezeiten, um die Integrität des Teils zu gewährleisten.Faktoren wie die Größe des Ofens, die Isolierung und die Vakuumumgebung sind ebenfalls entscheidend für die Optimierung des Prozesses.
Die wichtigsten Punkte erklärt:
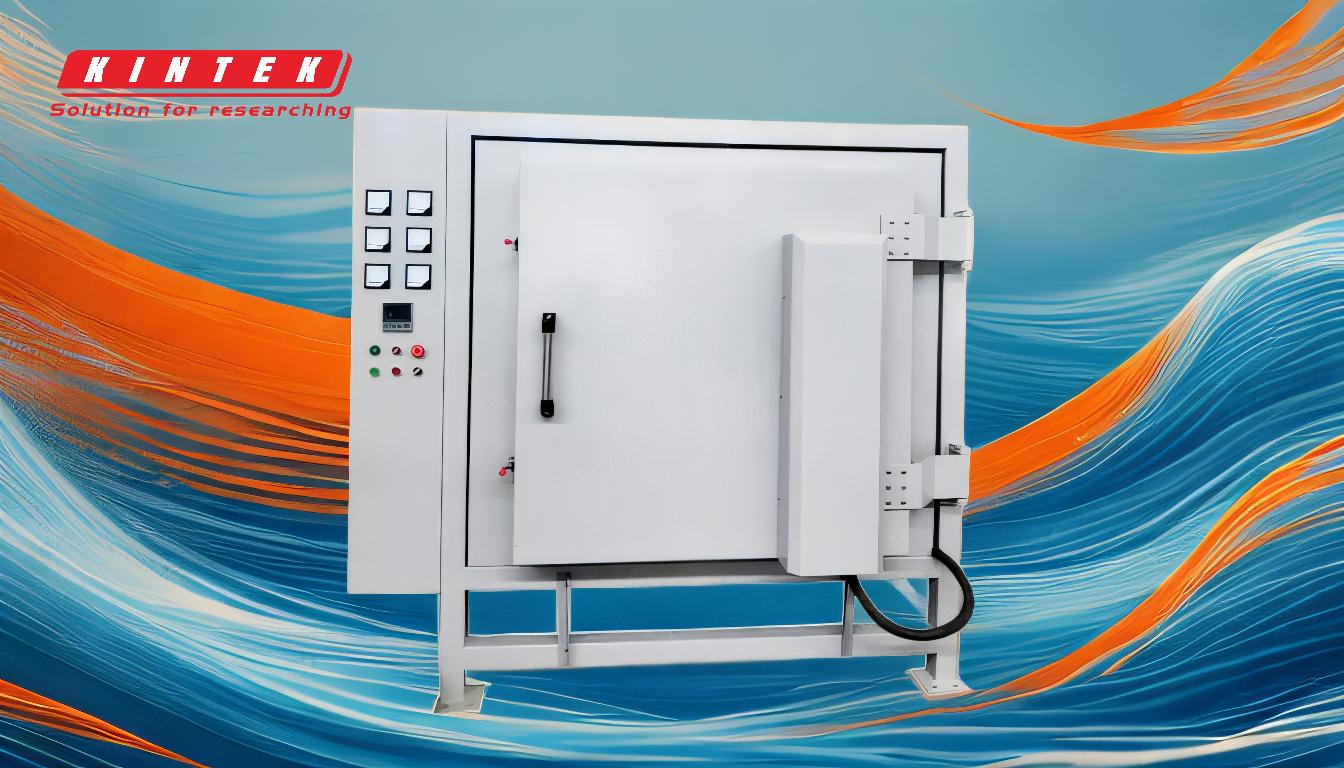
-
Entbindungsprozess:
- Zweck:Das Hauptziel des Entbinderns besteht darin, die Bindemittel (z. B. polymere Bindemittel wie Paraffin) zu entfernen, die verwendet werden, um das Metall- oder Keramikpulver in die gewünschte Form zu bringen.Diese Bindemittel sind während des Formgebungsprozesses notwendig, müssen aber vor dem Sintern entfernt werden, um Defekte zu vermeiden.
- Verfahren:Die Entbinderung kann je nach Art des verwendeten Bindemittels durch thermischen Abbau, Verdampfen oder Lösemittelextraktion erfolgen.
- Temperaturkontrolle:Der Prozess beginnt in der Regel bei Raumtemperatur und steigt allmählich auf etwa 600 °C an.Eine genaue Steuerung des Temperaturprofils ist unerlässlich, um Defekte wie Verformung oder Rissbildung zu vermeiden.
-
Sinterprozess:
- Zweck:Unter Sintern versteht man das Erhitzen des abgetrennten Teils auf hohe Temperaturen (z. B. 1.300 °C), um die Metall- oder Keramikpartikel zu verschmelzen, was zu einem dichten und festen Endprodukt führt.
- Temperatur-Profil:Der Sinterprozess umfasst mehrere Hochtemperaturzyklen.Zum Beispiel werden die Teile mit einer Geschwindigkeit von 2°C/min auf 225°C erhitzt, dann mit 1°C/min auf 550°C und 2 Stunden lang gehalten, gefolgt von einer Erhitzung auf 1.300°C mit 6°C/min und unterschiedlichen Haltezeiten (40 bis 180 Minuten).Schließlich werden die Teile bei 6°C/min auf 600°C abgekühlt und dann im Ofen abgekühlt.
- Umgebung:Das Sintern erfolgt häufig unter Vakuum in einem Graphitofen, um Oxidation zu verhindern und eine gleichmäßige Erwärmung zu gewährleisten.
-
Kombinierte vs. getrennte Prozesse:
- Kombinierte Prozesse:In einigen Fällen können Entbindern und Sintern in einem einzigen kontinuierlichen Prozess kombiniert werden, was Zeit und Energie sparen kann.Dies erfordert jedoch eine sorgfältige Kontrolle des Temperaturprofils und der Atmosphäre, um sicherzustellen, dass beide Prozesse effektiv durchgeführt werden.
- Getrennte Prozesse:In anderen Fällen werden das Entbindern und das Sintern in getrennten Schritten durchgeführt, was eine genauere Steuerung der einzelnen Prozesse ermöglicht.Diese Vorgehensweise kann bei komplexen Teilen oder Materialien erforderlich sein, die spezielle Entbinderungsbedingungen erfordern.
-
Überlegungen zum Ofen:
- Größe und Konfiguration:Die Größe des Ofens und die Frage, ob eine Kasten- oder eine Nicht-Kasten-Konfiguration verwendet werden soll, sind wichtige Überlegungen.Diese Faktoren beeinflussen die Effizienz und Wirtschaftlichkeit des Sinterprozesses.
- Isolierung:Die Art der Isolierung in der Wärmekammer ist entscheidend für die Aufrechterhaltung der erforderlichen hohen Temperaturen und die Gewährleistung einer gleichmäßigen Erwärmung der Teile.
-
Defekt-Prävention:
- Kontrolle der Parameter:Eine sorgfältige Kontrolle des Temperaturprofils, des Drucks, der Gasatmosphäre und der Glühzeit ist unerlässlich, um Defekte wie Verwerfungen und Risse sowohl beim Entbindern als auch beim Sintern zu vermeiden.
- Überlegungen zum Material:Die spezifischen Eigenschaften des Metall- oder Keramikpulvers sowie die Art des verwendeten Bindemittels müssen bei der Planung des Entbinderungs- und Sinterungsprozesses berücksichtigt werden, um sicherzustellen, dass das Endprodukt den gewünschten Spezifikationen entspricht.
Zusammenfassend lässt sich sagen, dass Entbindern und Sintern komplexe Prozesse sind, die eine präzise Steuerung verschiedener Parameter erfordern, um hochwertige Metall- oder Keramikteile herzustellen.Das Verständnis der beteiligten Schlüsselfaktoren, wie Temperaturprofile, Ofenkonfiguration und Fehlervermeidung, ist für die Optimierung dieser Prozesse unerlässlich.
Zusammenfassende Tabelle:
Prozess | Zweck | Wichtige Details |
---|---|---|
Entbindern | Entfernen von Bindemitteln von Formteilen. | Methoden:Thermischer Abbau, Verdampfung, Lösungsmittelextraktion.Temperaturkontrolle bis zu 600°C. |
Sintern | Verschmelzen von Metall-/Keramikpartikeln für dichte, feste Produkte. | Temperaturzyklen bis zu 1.300°C.Durchgeführt in einer Vakuumumgebung für gleichmäßige Erwärmung. |
Kombiniert/getrennt | Optimieren Sie Zeit und Präzision. | Kombiniert:Ein einziges Verfahren für mehr Effizienz.Getrennt:Bessere Kontrolle für komplexe Teile. |
Einrichtung des Ofens | Sorgen Sie für Effizienz und Kosteneffizienz. | Größe, Konfiguration (mit oder ohne Gehäuse) und Isolierung sind entscheidend für die Aufrechterhaltung hoher Temperaturen. |
Vermeidung von Defekten | Vermeiden Sie Verformungen und Risse. | Kontrollieren Sie Temperatur, Druck, Gasatmosphäre und Glühzeit.Berücksichtigen Sie Material- und Bindemitteltypen. |
Benötigen Sie Hilfe bei der Optimierung Ihrer Entbinderungs- und Sinterprozesse? Kontaktieren Sie noch heute unsere Experten für maßgeschneiderte Lösungen!