Die Heizrate beim Spark-Plasma-Sintern (SPS) ist ein kritischer Parameter, der die Mikrostruktur und die Eigenschaften des gesinterten Endprodukts erheblich beeinflusst.SPS ist ein Schnellsinterverfahren, bei dem gepulster Gleichstrom (DC) zur internen Wärmeerzeugung im Material verwendet wird, was im Vergleich zu herkömmlichen Sinterverfahren wesentlich schnellere Aufheizraten ermöglicht.Die Erhitzungsrate bei SPS kann von wenigen Grad pro Minute bis zu mehreren hundert Grad pro Minute reichen, je nach dem zu sinternden Material und den gewünschten Eigenschaften.Diese schnelle Erwärmung wird durch die Kombination von Plasmaerwärmung und Joule-Erwärmungsstufen erreicht, bei denen die Partikeloberflächen lokal und kurzzeitig erwärmt werden, gefolgt von einer gleichmäßigen Erwärmung durch die vom gepulsten Gleichstrom erzeugte Joule-Wärme.Die Möglichkeit, die Heizrate präzise zu steuern, ist einer der Hauptvorteile von SPS, der die Herstellung von Materialien mit hoher Dichte und feinen Mikrostrukturen ermöglicht.
Die wichtigsten Punkte werden erklärt:
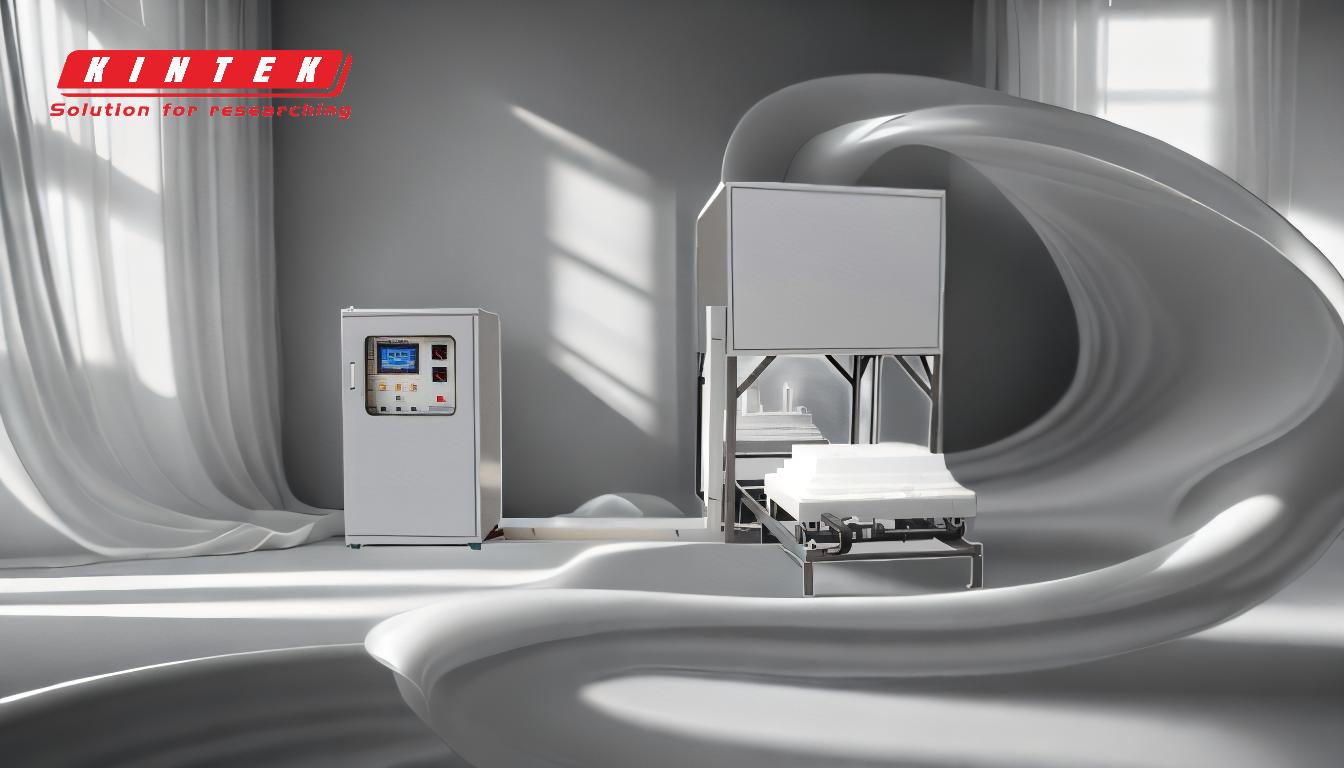
-
Heizrate bei SPS:
- Die Heizrate beim Spark-Plasma-Sintern (SPS) kann stark variieren und liegt typischerweise zwischen 50°C/min bis 500°C/min oder sogar höher, je nach Material und gewünschtem Ergebnis.Diese schnelle Erwärmung ist eines der Unterscheidungsmerkmale von SPS im Vergleich zu herkömmlichen Sinterverfahren, die oft viel langsamere Erwärmungsraten aufweisen.
-
Plasmaerwärmungsphase:
- Während der Plasmaerwärmungsphase, elektrische Entladung zwischen Pulverpartikeln führt zu einer lokalen und kurzzeitigen Erwärmung der Partikeloberflächen auf bis zu mehrere tausend Grad Celsius.Diese Erwärmung verteilt sich gleichmäßig über das gesamte Probenvolumen und reinigt und aktiviert die Partikeloberflächen durch Verdampfen von Verunreinigungen.Die gereinigten Oberflächenschichten schmelzen und verschmelzen und bilden "Hälse" zwischen den Partikeln.Diese Phase trägt zur ersten schnellen Erwärmung und Oberflächenaktivierung bei.
-
Phase der Joule-Erwärmung:
- In der Joule-Erwärmungsphase wird ein gepulster elektrischer Gleichstrom fließt durch die Verbindungsstellen zwischen den Partikeln und erzeugt Joule-Wärme.Diese Wärme erhöht die Diffusion der Atome/Moleküle in den Hälsen und fördert so ihr Wachstum.Die örtlich begrenzte und gleichmäßige Erwärmung ermöglicht einen schnellen Temperaturanstieg und -abfall, wodurch die Vergröberung der Materialkörner minimiert wird.Diese Phase ist entscheidend für das Erreichen hoher Heizraten und die Erhaltung feiner Mikrostrukturen.
-
Vorteile von hohen Heizraten:
- Minimiertes Kornwachstum: Die schnellen Erwärmungsraten bei SPS tragen dazu bei, das Kornwachstum zu minimieren, was für die Erhaltung feiner Mikrostrukturen und die Verbesserung mechanischer Eigenschaften wie Festigkeit und Zähigkeit von Vorteil ist.
- Reduzierte Verarbeitungszeit: Durch die Möglichkeit, hohe Heizraten zu erzielen, wird die Gesamtverarbeitungszeit erheblich verkürzt, was SPS im Vergleich zu herkömmlichen Verfahren zu einem effizienteren Sinterverfahren macht.
- Verbesserte Verdichtung: Die Kombination von Plasma- und Joule-Erwärmungsstufen fördert eine schnelle Verdichtung, was zu hochdichten Materialien mit minimaler Porosität führt.
-
Faktoren, die die Heizrate beeinflussen:
- Materialeigenschaften: Die Wärmeleitfähigkeit, die elektrische Leitfähigkeit und der Schmelzpunkt des zu sinternden Materials können die erreichbare Heizrate beeinflussen.
- Probengröße und -geometrie: Größere oder komplexere Proben erfordern möglicherweise eine Anpassung der Heizrate, um eine gleichmäßige Erwärmung zu gewährleisten und thermische Gradienten zu vermeiden.
- Fähigkeiten der Ausrüstung: Die Konstruktion und Leistung der SPS-Anlage, einschließlich der Fähigkeit, Hochstromimpulse zu liefern, spielen eine entscheidende Rolle bei der Bestimmung der maximalen Heizrate.
-
Anwendungen von SPS mit hohen Heizraten:
- Hochleistungskeramik: SPS wird häufig für das Sintern von Hochleistungskeramik verwendet, wo schnelle Aufheizraten dazu beitragen, feinkörnige Mikrostrukturen und hohe Dichten zu erzielen.
- Metallische Legierungen: Hohe Heizraten sind vorteilhaft für das Sintern von Metalllegierungen, insbesondere für solche, die feine Mikrostrukturen für verbesserte mechanische Eigenschaften erfordern.
- Verbundwerkstoffe: SPS wird auch zum Sintern von Verbundwerkstoffen verwendet, wobei die schnellen Heizraten dazu beitragen, die Integrität der verschiedenen Phasen im Verbundwerkstoff zu erhalten.
Zusammenfassend lässt sich sagen, dass die Heizrate beim Spark-Plasma-Sintern ein Schlüsselparameter ist, der präzise gesteuert werden kann, um eine schnelle Verdichtung und feine Mikrostrukturen zu erreichen.Die Kombination von Plasmaerwärmung und Joule-Heizstufen ermöglicht hohe Heizraten, die mehrere Vorteile bieten, darunter minimiertes Kornwachstum, reduzierte Verarbeitungszeit und verbesserte Verdichtung.Die Fähigkeit, hohe Heizraten zu erreichen, macht SPS zu einem leistungsstarken Werkzeug für das Sintern einer breiten Palette von Materialien, von Hochleistungskeramik bis hin zu Metalllegierungen und Verbundwerkstoffen.
Zusammenfassende Tabelle:
Aspekt | Einzelheiten |
---|---|
Bereich der Heizrate | 50°C/min bis 500°C/min oder höher, je nach Material und gewünschtem Ergebnis |
Plasma-Heizstufe | Örtliche Erwärmung bis zu Tausenden von °C, reinigt und aktiviert Oberflächen |
Joulesche Heizstufe | Gepulster Gleichstrom erzeugt gleichmäßige Wärme und minimiert das Kornwachstum |
Die wichtigsten Vorteile | Minimiertes Kornwachstum, reduzierte Verarbeitungszeit, verbesserte Verdichtung |
Anwendungen | Hochleistungskeramiken, metallische Legierungen, Verbundwerkstoffe |
Sind Sie bereit, Ihren Sinterprozess mit SPS zu optimieren? Kontaktieren Sie uns noch heute um mehr zu erfahren!