Spark Plasma Sintering (SPS) ist ein modernes Sinterverfahren, das die Prinzipien des Heißpressens mit der Anwendung gepulster elektrischer Ströme kombiniert.Diese Methode ermöglicht eine schnelle Erwärmung und Verfestigung von Werkstoffen, was zu kürzeren Verarbeitungszeiten führt und die Möglichkeit bietet, Werkstoffe mit einzigartigen Mikrostrukturen und Eigenschaften zu schaffen.Der Schlüssel zur Effizienz liegt im direkten Stromfluss durch die Graphitmatrize und das zu verarbeitende Material, der eine lokale Erwärmung erzeugt und die Verdichtung erleichtert.Darüber hinaus spielt der "Funkenplasmaeffekt" eine entscheidende Rolle bei der Verhinderung des Partikelwachstums, was die Herstellung feinkörniger und leistungsstarker Materialien ermöglicht.
Die wichtigsten Punkte werden erklärt:
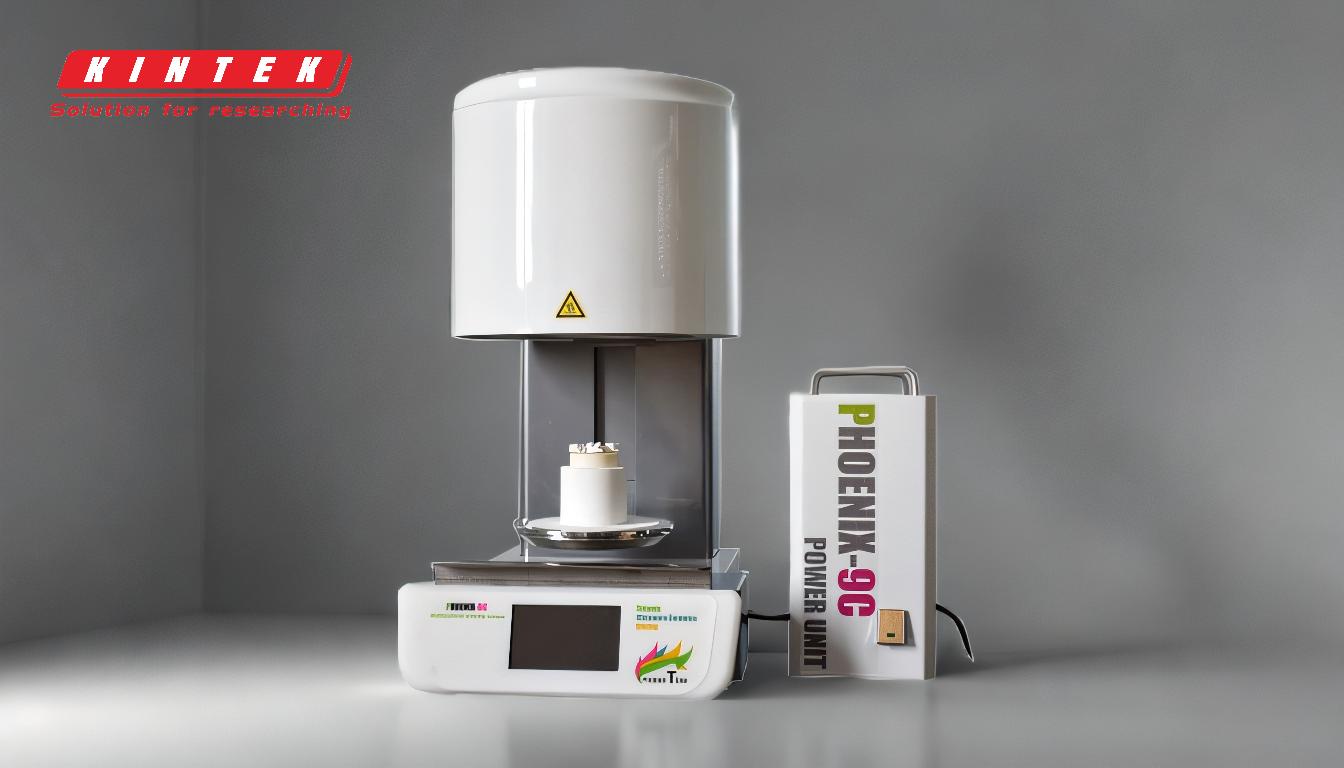
-
Modifizierter Heißpressenaufbau:
- Das SPS-Verfahren baut auf dem traditionellen Heißpressen auf, führt jedoch erhebliche Änderungen ein.Beim herkömmlichen Heißpressen wird die Wärme von außen auf die Matrize aufgebracht, die dann die Wärme auf das Material überträgt.Bei SPS fließt der elektrische Strom direkt durch die Graphitmatrize und das Material, was eine schnellere und effizientere Erwärmung ermöglicht.
- Dieser direkte Erhitzungsmechanismus verringert den Energieverlust und ermöglicht eine präzise Temperatursteuerung, was für das Erreichen der gewünschten Materialeigenschaften entscheidend ist.
-
Gepulste elektrische Ströme:
- Die Verwendung gepulster elektrischer Ströme ist ein charakteristisches Merkmal der SPS.Diese Ströme erzeugen eine schnelle und örtlich begrenzte Erwärmung, wodurch die für das Sintern erforderliche Zeit im Vergleich zu herkömmlichen Verfahren erheblich verkürzt wird.
- Der gepulste Charakter des Stroms trägt auch dazu bei, eine gleichmäßige Temperaturverteilung im Material aufrechtzuerhalten, wodurch thermische Gradienten, die zu Defekten führen könnten, minimiert werden.
-
Funkenplasma-Effekt:
- Der "Funkenplasmaeffekt" ist ein einzigartiges Phänomen der SPS, bei dem der elektrische Strom die Bildung eines Plasmas zwischen den Partikeln induziert.Dieses Plasma erleichtert die Entfernung von Oberflächenoxiden und Verunreinigungen und fördert eine bessere Partikelbindung.
- Der Funkenplasmaeffekt hemmt auch das Partikelwachstum während des Sinterns, was für die Herstellung von Werkstoffen mit feinkörnigen Mikrostrukturen unerlässlich ist.Feinkörnige Werkstoffe weisen oft hervorragende mechanische, thermische und elektrische Eigenschaften auf.
-
Schnelle Erwärmung und kurze Prozesszyklen:
- Einer der wichtigsten Vorteile von SPS ist die Fähigkeit, sehr schnelle Aufheizraten zu erreichen, die oft in nur wenigen Minuten Temperaturen im Bereich von 1000-2000°C erreichen.Durch diese schnelle Erwärmung wird die Zeit, die das Material bei hohen Temperaturen verbringt, auf ein Minimum reduziert, wodurch das Risiko unerwünschter Phasenumwandlungen oder des Kornwachstums verringert wird.
- Kurze Prozesszyklen verbessern nicht nur die Effizienz, sondern machen das SPS-Verfahren auch für die Verarbeitung temperaturempfindlicher Materialien geeignet, die sich bei längerer Exposition gegenüber hohen Temperaturen zersetzen würden.
-
Schaffung einzigartiger Materialzusammensetzungen und -eigenschaften:
- SPS ermöglicht das Sintern von Materialien, die mit herkömmlichen Verfahren nur schwer oder gar nicht zu verarbeiten sind.Dazu gehören Materialien mit hohen Schmelzpunkten, Nanomaterialien und Verbundwerkstoffe.
- Der einzigartige Erhitzungsmechanismus und der Funkenplasmaeffekt ermöglichen die Herstellung von Werkstoffen mit maßgeschneiderten Mikrostrukturen, wie z. B. nanokristallinen oder Gradientenwerkstoffen, die verbesserte Eigenschaften wie erhöhte Festigkeit, Verschleißfestigkeit oder Wärmeleitfähigkeit aufweisen können.
-
Graphitstempel als Schlüsselkomponente:
- Die bei der SPS verwendete Graphitmatrize erfüllt mehrere Zwecke.Sie dient als Form für das zu sinternde Material, leitet den elektrischen Strom und sorgt für die Wärmeisolierung.Graphit wird wegen seiner hohen elektrischen Leitfähigkeit, thermischen Stabilität und Temperaturwechselbeständigkeit ausgewählt.
- Die Konstruktion der Matrize ist entscheidend für eine gleichmäßige Stromverteilung und Temperaturkontrolle, die für das Erreichen gleichmäßiger Materialeigenschaften unerlässlich sind.
-
Anwendungen und Vorteile:
- SPS findet breite Anwendung bei der Herstellung von Hochleistungskeramik, Metallen, Verbundwerkstoffen und funktional abgestuften Materialien.Seine Fähigkeit, dichte, feinkörnige Materialien mit minimalen Defekten herzustellen, macht es ideal für Anwendungen in der Luft- und Raumfahrt, der Automobilindustrie, der Elektronik und der biomedizinischen Industrie.
- Das Verfahren ist außerdem umweltfreundlich, da es im Vergleich zu herkömmlichen Sinterverfahren weniger Energie verbraucht und weniger Emissionen erzeugt.
Durch die Kombination der Grundsätze des Heißpressens mit innovativen elektrischen und Plasmaeffekten bietet SPS ein leistungsfähiges Werkzeug für Materialwissenschaftler und Ingenieure, um fortschrittliche Werkstoffe mit maßgeschneiderten Eigenschaften und verbesserter Leistung herzustellen.
Zusammenfassende Tabelle:
Hauptaspekt | Beschreibung |
---|---|
Modifiziertes Heißpressen | Direkter elektrischer Stromfluss ermöglicht eine schnellere und effizientere Erwärmung. |
Gepulste elektrische Ströme | Schnelle, örtlich begrenzte Erwärmung verkürzt die Sinterzeit und gewährleistet eine gleichmäßige Temperatur. |
Funkenplasma-Effekt | Verhindert das Partikelwachstum und erzeugt feinkörnige Hochleistungsmaterialien. |
Schnelle Erwärmung | Erreicht 1000-2000°C in Minuten, ideal für temperaturempfindliche Materialien. |
Einzigartige Materialerstellung | Ermöglicht das Sintern von Materialien mit hohem Schmelzpunkt, Verbundwerkstoffen und Nanomaterialien. |
Graphit-Matrize | Leitet den Strom, isoliert und gewährleistet eine gleichmäßige Temperaturkontrolle. |
Anwendungen | Die Luft- und Raumfahrt-, Automobil-, Elektronik- und biomedizinische Industrie profitieren von SPS. |
Vorteile | Energieeffizient, umweltfreundlich und mit minimalen Fehlern. |
Nutzen Sie das Potenzial des Spark-Plasma-Sinterns für Ihre Materialanforderungen. Kontaktieren Sie unsere Experten noch heute !