Eine Schutzgasatmosphäre beim Schweißen bezieht sich auf die Verwendung von nicht reaktiven Gasen, um eine schützende Umgebung um den Schweißbereich zu schaffen.Dies verhindert eine Verunreinigung durch reaktive Gase in der Luft, wie Sauerstoff und Stickstoff, die Defekte wie Porosität, Oxidation oder Entkohlung in der Schweißnaht verursachen können.Inerte Gase wie Argon und Helium werden üblicherweise bei Verfahren wie dem Wolfram-Lichtbogenschweißen (GTAW) und dem Vakuumlöten verwendet, um saubere, hochwertige Schweißnähte zu gewährleisten.Die inerte Atmosphäre schützt das geschmolzene Metall, die Wolframelektrode und die umgebenden Materialien vor chemischen Reaktionen und bewahrt so die Integrität und die gewünschten Eigenschaften der Schweißnaht.Diese kontrollierte Umgebung ist unerlässlich, um präzise, dauerhafte und fehlerfreie Schweißnähte in verschiedenen industriellen Anwendungen zu erzielen.
Die wichtigsten Punkte werden erklärt:
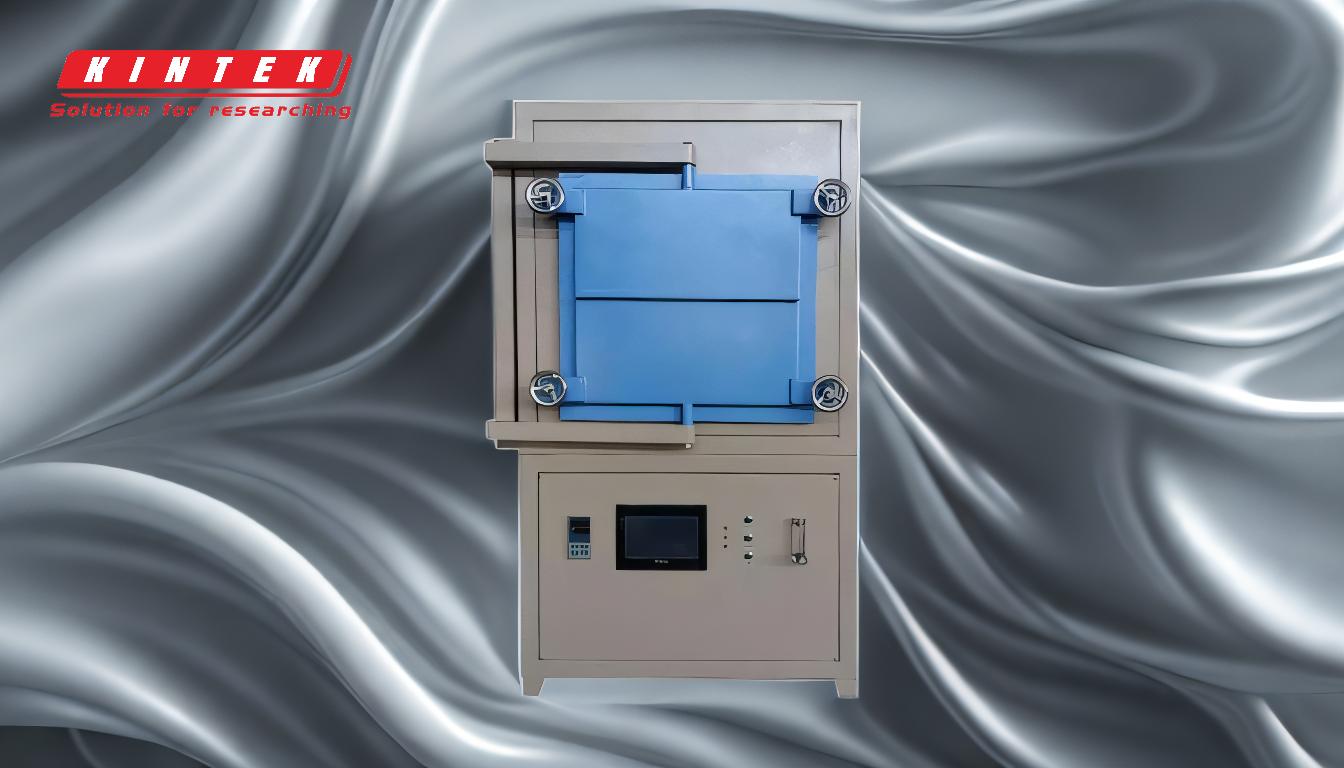
-
Definition der Schutzgasatmosphäre beim Schweißen:
- Eine inerte Atmosphäre ist eine kontrollierte Umgebung, die mit nicht reaktiven Gasen wie Argon oder Helium gefüllt ist, um den Schweißprozess vor Verunreinigungen zu schützen.
- Sie verhindert unerwünschte chemische Reaktionen, wie Oxidation oder Porosität, die die Qualität der Schweißnaht beeinträchtigen können.
-
Zweck der Verwendung von Schutzgasen:
- Abschirmung des Schweißbades:Inerte Gase schützen das geschmolzene Metall vor reaktiven Gasen wie Sauerstoff und Stickstoff in der Luft, die Fehler wie Porosität oder Sprödigkeit in der Schweißnaht verursachen können.
- Schutz der Wolframelektrode:Bei Verfahren wie dem Wolfram-Lichtbogenschweißen (WIG) schützen Schutzgase die Wolframelektrode vor Verunreinigungen und sorgen für einen stabilen Lichtbogen und eine gleichbleibende Schweißqualität.
- Aufrechterhaltung der Materialintegrität:Die Schutzgasatmosphäre sorgt dafür, dass die zu schweißenden Materialien ihre gewünschten Eigenschaften wie Festigkeit und Korrosionsbeständigkeit behalten, indem sie Oxidation oder Entkohlung verhindert.
-
Gängige Schutzgase beim Schweißen:
- Argon:Weit verbreitet aufgrund seiner hohen Dichte, die eine hervorragende Abdeckung und Schutz für das Schweißbad bietet.Außerdem ist es kostengünstig und leicht erhältlich.
- Helium:Wird häufig zum Schweißen dickerer Materialien oder bei Anwendungen, die eine höhere Wärmezufuhr erfordern, verwendet, da es im Vergleich zu Argon einen heißeren Lichtbogen erzeugt.
- Stickstoff:Gelegentlich in bestimmten Anwendungen eingesetzt, aber weniger verbreitet, da es bei hohen Temperaturen mit bestimmten Materialien reagieren kann.
-
Anwendungen der Schutzgasatmosphäre beim Schweißen:
- Gas-Wolfram-Lichtbogenschweißen (GTAW):Schutzgase sind für die Abschirmung der Wolframelektrode und des Schweißbades unerlässlich und gewährleisten eine saubere und präzise Schweißung.
- Vakuumlöten:Inerte Gase helfen, die Restluft aus den Kapillarwegen zu spülen und sorgen für eine feste Verbindung zwischen den gelöteten Materialien.
- Wärmebehandlung:Inerte Atmosphären werden bei der Wärmebehandlung eingesetzt, um Oxidation und Verunreinigung zu verhindern und die Materialeigenschaften bei Hochtemperaturprozessen zu erhalten.
-
Vorteile der Verwendung einer Schutzgasatmosphäre:
- Verbesserte Schweißnahtqualität:Verhindert Defekte wie Porosität, Oxidation und Verunreinigungen, was zu stärkeren und haltbareren Schweißnähten führt.
- Verbesserte Prozesskontrolle:Bietet eine stabile und vorhersehbare Umgebung für das Schweißen, verringert die Variabilität und verbessert die Konsistenz.
- Material-Konservierung:Schützt empfindliche Werkstoffe vor chemischen Reaktionen und sorgt dafür, dass sie ihre gewünschten mechanischen und chemischen Eigenschaften beibehalten.
-
Ausrüstung und Einrichtung für das Schweißen unter Schutzatmosphäre:
- Inertgasversorgung:Zur Aufrechterhaltung der Schutzatmosphäre ist eine zuverlässige Quelle für Inertgas wie Argon oder Helium erforderlich.
- Gaszufuhrsystem:Beinhaltet Schläuche, Regler und Düsen, um das Schutzgas präzise in den Schweißbereich zu leiten.
- Schweißbrenner:Entwickelt, um den Schutzgasstrom um das Schweißbad und die Elektrode herum zu leiten und so eine wirksame Abschirmung zu gewährleisten.
- Überwachungs- und Kontrollsysteme:Fortschrittliche Systeme wie mikroprozessorgestützte Steuerungen gewährleisten einen optimalen Gasfluss und eine optimale Temperatur für gleichbleibende Ergebnisse.
-
Herausforderungen und Überlegungen:
- Kosten für Inertgase:Hochreine Schutzgase können teuer sein, vor allem bei groß angelegten oder großvolumigen Schweißarbeiten.
- Gasfluss-Management:Die korrekte Steuerung des Gasflusses ist entscheidend, um Turbulenzen zu vermeiden, die Luft in den Schweißbereich einbringen und die Schutzgasatmosphäre beeinträchtigen können.
- Material-Kompatibilität:Nicht alle Materialien sind mit jedem Inertgas kompatibel.Stickstoff kann zum Beispiel bei hohen Temperaturen mit bestimmten Metallen reagieren und ist daher für manche Anwendungen ungeeignet.
-
Zukünftige Trends beim Schweißen unter Schutzatmosphäre:
- Fortgeschrittene Gasgemische:Die Entwicklung kundenspezifischer Gasgemische, die auf bestimmte Werkstoffe und Schweißverfahren zugeschnitten sind, wird immer häufiger eingesetzt.
- Automatisierung und Robotik:Zunehmender Einsatz von automatisierten Schweißsystemen mit integrierter Schutzgaszufuhr für mehr Präzision und Effizienz.
- Nachhaltigkeit:Bemühungen zur Reduzierung des Gasverbrauchs und der Abfälle durch bessere Prozesssteuerung und Recycling-Systeme.
Wenn Hersteller und Schweißer die Rolle von Schutzgasatmosphären beim Schweißen verstehen, können sie fundierte Entscheidungen treffen, um ihre Prozesse zu optimieren, die Schweißqualität zu verbessern und die Kosten zu senken.Die Verwendung von Schutzgasen ist ein entscheidender Faktor bei der Herstellung von Hochleistungsschweißnähten in Branchen von der Luft- und Raumfahrt bis zur Automobilindustrie und darüber hinaus.
Zusammenfassende Tabelle:
Aspekt | Einzelheiten |
---|---|
Definition | Eine kontrollierte Umgebung, in der nicht reaktive Gase verwendet werden, um eine Kontamination zu verhindern. |
Gängige Gase | Argon, Helium, Stickstoff (weniger häufig). |
Anwendungen | GTAW, Vakuumlöten, Wärmebehandlung. |
Vorteile | Verbesserte Schweißnahtqualität, verbesserte Prozesskontrolle, Materialerhaltung. |
Herausforderungen | Kosten für Inertgase, Gasflussmanagement, Materialverträglichkeit. |
Zukünftige Trends | Fortschrittliche Gasgemische, Automatisierung, Nachhaltigkeit. |
Optimieren Sie Ihren Schweißprozess mit Schutzgasen - Kontaktieren Sie noch heute unsere Experten für maßgeschneiderte Lösungen!