Die Betriebstemperatur eines Kalzinators liegt normalerweise zwischen 550°C bis 1300°C je nach der spezifischen Anwendung und dem zu verarbeitenden Material.Die Kalzinierung ist ein Hochtemperaturverfahren, das zur thermischen Zersetzung von Materialien, zur Entfernung flüchtiger Bestandteile oder zur Herbeiführung von Phasenübergängen eingesetzt wird.Der Temperaturbereich wird durch Faktoren wie die Art des Materials, die gewünschte chemische Reaktion und die Konstruktion der Anlage beeinflusst.So können einige Anwendungen niedrigere Temperaturen (550-1150°C) erfordern, während andere, wie z.B. die moderne Keramikverarbeitung, höhere Temperaturen bis zu 1300°C erfordern.Die Konstruktion des Kalzinators, einschließlich seiner Fähigkeit, eine kontrollierte Atmosphäre aufrechtzuerhalten, spielt ebenfalls eine entscheidende Rolle bei der Bestimmung der optimalen Betriebstemperatur.
Die wichtigsten Punkte werden erklärt:
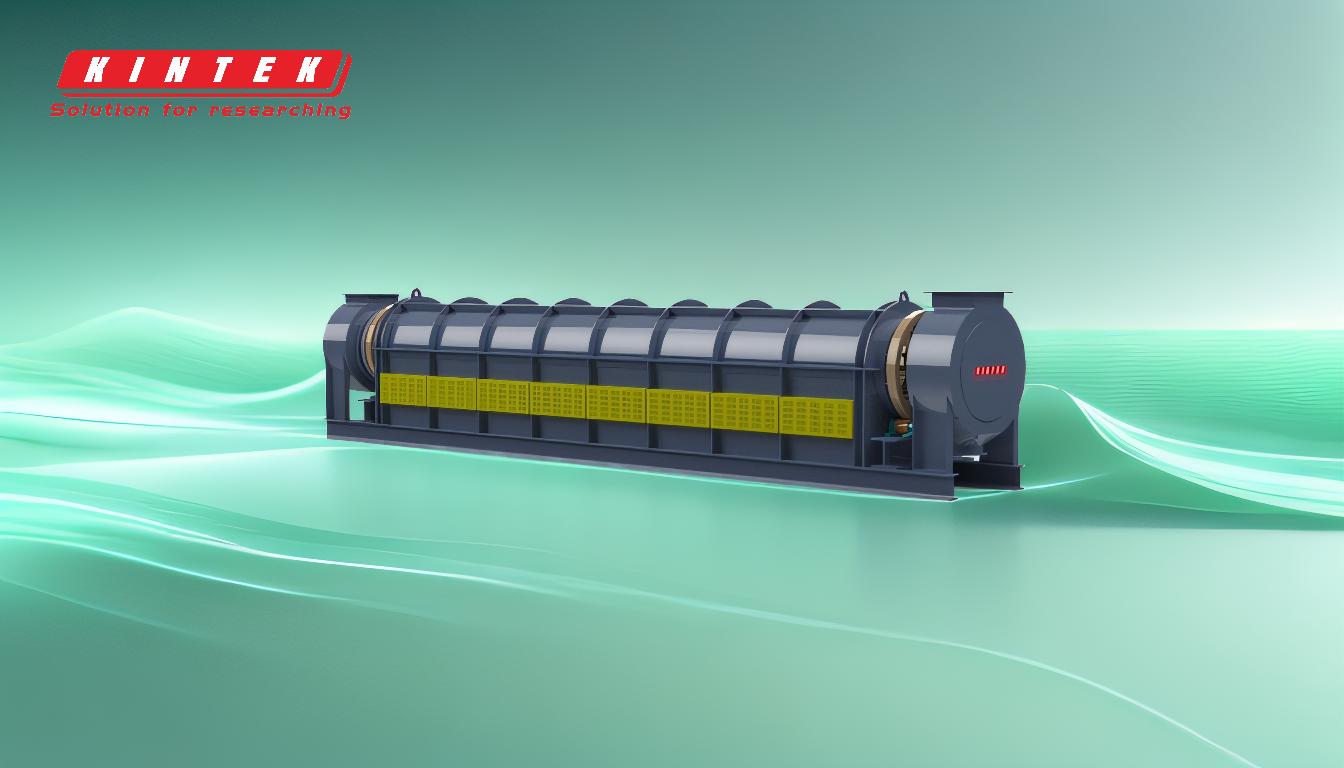
-
Typischer Betriebstemperaturbereich:
- Die Betriebstemperatur eines Kalzinators liegt im Allgemeinen zwischen 550°C und 1300°C .
- Dieser Bereich wird durch das spezifische zu verarbeitende Material und die gewünschte chemische oder physikalische Umwandlung bestimmt.
- Beispielsweise werden niedrigere Temperaturen (550-1150 °C) häufig für Prozesse wie die thermische Zersetzung verwendet, während höhere Temperaturen (bis zu 1300 °C) für die moderne Materialsynthese erforderlich sind.
-
Faktoren, die die Temperatur beeinflussen:
- Materialeigenschaften:Verschiedene Materialien haben unterschiedliche thermische Zersetzungs- oder Reaktionstemperaturen.So erfolgt die Kalzinierung von Kalkstein in der Regel bei 900 °C, während für andere Materialien höhere Temperaturen erforderlich sein können.
- Anforderungen an den Prozess:Die Temperatur hängt von der jeweiligen Anwendung ab, z. B. von der Entfernung flüchtiger Bestandteile oder der Herbeiführung von Phasenänderungen.
- Konstruktion der Geräte:Die Konstruktion des Kalzinators, einschließlich seines Heizmechanismus und seiner Isolierung, beeinflusst seine Fähigkeit, hohe Temperaturen zu erreichen und zu halten.
-
Anwendungen und Temperaturschwankungen:
- Unterer Temperaturbereich (550-1150°C):Wird für Prozesse wie die thermische Zersetzung von Karbonaten, Hydroxiden oder organischen Materialien verwendet.
- Höherer Temperaturbereich (bis zu 1300°C):Erforderlich für fortgeschrittene Anwendungen wie das Sintern von Keramik oder die Synthese von hochreinen Materialien.
- Die Temperatur wird häufig angepasst, um eine optimale Reaktionskinetik und optimale Materialeigenschaften zu gewährleisten.
-
Kontrollierte Atmosphäre:
- Die Kalzinierung erfordert häufig eine kontrollierte Atmosphäre, um unerwünschte Reaktionen oder Verunreinigungen zu vermeiden.
- Die Fähigkeit des Kalzinators, eine bestimmte Atmosphäre (z. B. inert, oxidierend oder reduzierend) aufrechtzuerhalten, ist entscheidend für das Erreichen der gewünschten Ergebnisse.
-
Konstruktion und Effizienz der Anlage:
- Kalzinieröfen sind so konzipiert, dass sie hohe Temperaturen effizient handhaben können, wobei häufig indirekte Heizmethoden verwendet werden, um eine gleichmäßige Temperaturverteilung zu gewährleisten.
- Die Verwendung von rotierenden Stahlzylindern, wie in den Referenzen erwähnt, trägt zur Aufrechterhaltung gleichmäßiger Verarbeitungsbedingungen bei.
-
Praktische Überlegungen für Einkäufer:
- Berücksichtigen Sie bei der Auswahl eines Kalzinators den für Ihre spezielle Anwendung erforderlichen Temperaturbereich.
- Beurteilen Sie die Fähigkeit des Ofens, eine kontrollierte Atmosphäre aufrechtzuerhalten, und seine Energieeffizienz.
- Vergewissern Sie sich, dass die Anlage auf Langlebigkeit ausgelegt ist und einem längeren Hochtemperaturbetrieb standhält.
Durch die Kenntnis dieser wichtigen Punkte können Käufer fundierte Entscheidungen bei der Auswahl eines Kalzinators treffen, der ihren spezifischen Verarbeitungsanforderungen entspricht.
Zusammenfassende Tabelle:
Hauptaspekt | Einzelheiten |
---|---|
Typischer Temperaturbereich | 550°C bis 1300°C |
Unterer Bereich (550-1150°C) | Für die thermische Zersetzung von Karbonaten, Hydroxiden oder organischen Materialien. |
Höherer Bereich (bis zu 1300°C) | Erforderlich für das Sintern von Hochleistungskeramik oder die Synthese von hochreinen Materialien. |
Beeinflussende Faktoren | Materialeigenschaften, Prozessanforderungen und Gerätekonstruktion. |
Kontrollierte Atmosphäre | Unerlässlich, um unerwünschte Reaktionen oder Kontaminationen zu verhindern. |
Design der Ausrüstung | Gewährleistet gleichmäßige Temperaturverteilung und Langlebigkeit für den Einsatz bei hohen Temperaturen. |
Benötigen Sie einen Kalzinator, der auf Ihre spezifischen Temperaturanforderungen zugeschnitten ist? Kontaktieren Sie noch heute unsere Experten um die perfekte Lösung zu finden!