Spark Plasma Sintering (SPS) ist eine fortschrittliche Sintertechnik, die gepulsten elektrischen Gleichstrom und einachsigen Druck kombiniert, um dichte Materialien mit einzigartigen Eigenschaften herzustellen.Das Verfahren umfasst vier Hauptstufen: Vakuumerzeugung, Druckanwendung, Widerstandserhitzung und Abkühlung.Es wird in einem Vakuum oder einer kontrollierten Atmosphäre durchgeführt, um Oxidation zu verhindern und die Reinheit des Materials zu gewährleisten.SPS zeichnet sich durch hohe Heizraten, kurze Bearbeitungszeiten und eine präzise Steuerung von Temperatur, Druck und Heizrate aus und ermöglicht die Herstellung von Materialien mit maßgeschneiderten Mikrostrukturen und Eigenschaften.Das Verfahren wird durch eine Touchscreen-Schnittstelle für die Programmierung und Steuerung erleichtert.
Die wichtigsten Punkte werden erklärt:
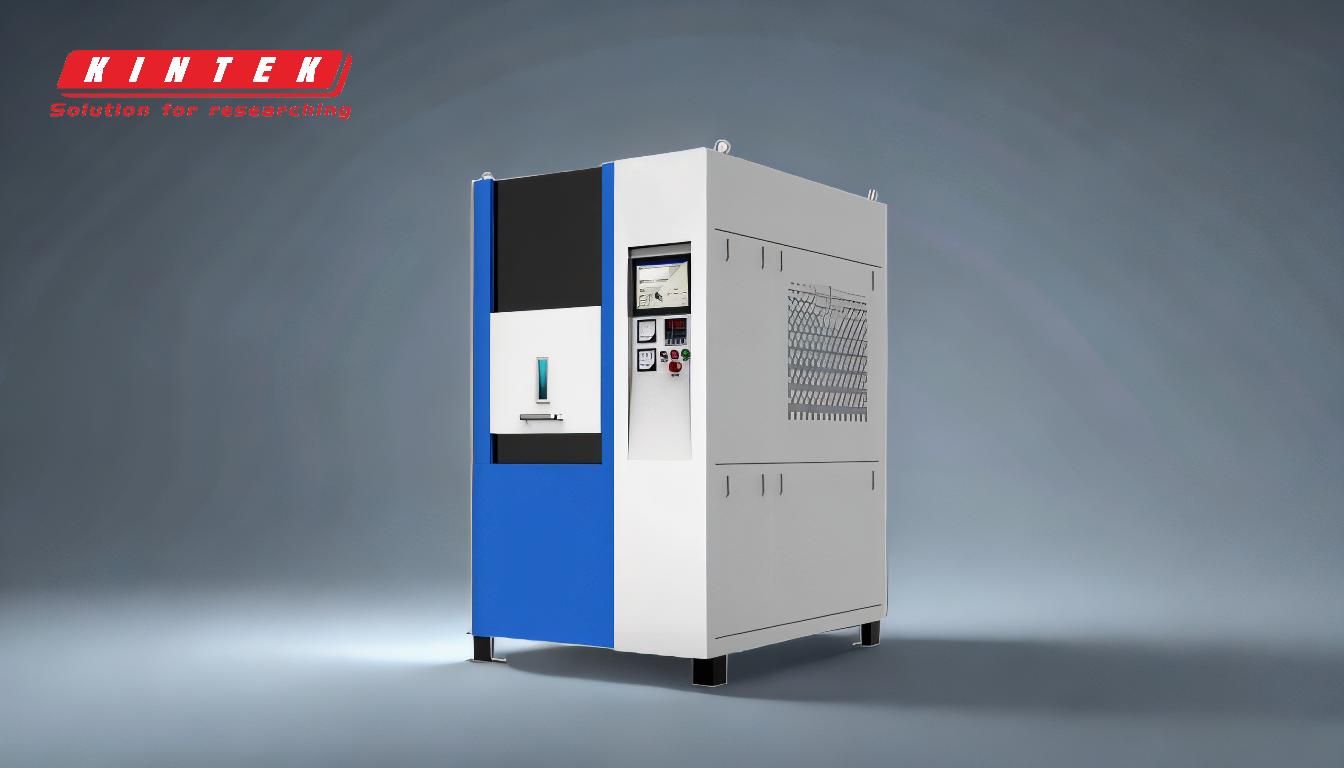
-
Überblick über SPS:
- SPS ist ein fortschrittliches Sinterverfahren, bei dem gepulster elektrischer Gleichstrom und einachsiger Druck verwendet werden.
- Es basiert auf einem modifizierten Heißpressverfahren, bei dem ein elektrischer Strom direkt durch die Graphitmatrize und das Bauteil fließt.
- Durch gepulste Ströme und den "Funkenplasmaeffekt" erreicht das Verfahren sehr schnelle Aufheizzeiten und kurze Prozesszyklen.
-
Schlüsselphasen des SPS-Prozesses:
-
Stufe 1:Entfernen von Gas und Erzeugen eines Vakuums:
- Das Verfahren beginnt mit der Entfernung von Gas aus der Kammer, um ein Vakuum oder eine kontrollierte Atmosphäre zu schaffen.
- Dieser Schritt verhindert Oxidation und gewährleistet die Reinheit des Materials.
-
Stufe 2: Druck ausüben:
- Mit Hilfe von Ober- und Unterstempeln wird ein einachsiger Druck auf den Pulverpressling ausgeübt.
- Der Druck hilft bei der Verdichtung des Materials während des Sinterns.
-
Stufe 3: Widerstandsheizung:
- Gepulster elektrischer Gleichstrom wird durch die Graphitmatrize und den Pulverpressling geleitet.
- Die Funkenentladung erzeugt lokal hohe Temperaturen, die zu einer Oberflächenverdampfung und zum Schmelzen der Pulverpartikel führen.
- Dadurch bilden sich an den Kontaktstellen zwischen den Partikeln Verengungen, die zu einer Verdichtung führen.
-
Stufe 4: Abkühlung:
- Nach dem Sintern wird das Material unter kontrollierten Bedingungen abgekühlt, um das gewünschte Mikrogefüge und die gewünschten Eigenschaften zu erzielen.
-
Stufe 1:Entfernen von Gas und Erzeugen eines Vakuums:
-
Einzigartige Merkmale von SPS:
-
Hohe Heizraten:
- SPS erreicht schnelle Aufheizraten, wodurch sich die Verarbeitungszeiten im Vergleich zu herkömmlichen Sinterverfahren erheblich verkürzen.
-
Präzise Steuerung:
- Das Verfahren ermöglicht eine präzise Steuerung von Temperatur, Druck und Heizrate und damit die Herstellung von Materialien mit maßgeschneiderten Eigenschaften.
-
Niedrige Sintertemperaturen:
- SPS arbeitet im Vergleich zu herkömmlichen Verfahren mit niedrigeren Sintertemperaturen, wodurch das Kornwachstum minimiert und die Materialeigenschaften erhalten werden.
-
Hohe Heizraten:
-
Vorteile von SPS:
-
Kurze Bearbeitungszeiten:
- Die Kombination aus hohen Heizraten und gepulsten Strömen führt zu kürzeren Prozesszyklen.
-
Einzigartige Materialeigenschaften:
- Der \"Funkenplasmaeffekt\" hemmt das Partikelwachstum und ermöglicht die Herstellung von Materialien mit einzigartiger Zusammensetzung und Mikrostruktur.
-
Kontrollierte Atmosphäre:
- Der Betrieb im Vakuum oder in einer kontrollierten Atmosphäre gewährleistet die Reinheit des Materials und verhindert Oxidation.
-
Kurze Bearbeitungszeiten:
-
Anwendungen von SPS:
- SPS findet breite Anwendung bei der Herstellung von Hochleistungskeramik, Metallen, Verbundwerkstoffen und funktional abgestuften Materialien.
- Es ist besonders vorteilhaft für die Herstellung von Materialien mit verbesserten mechanischen, thermischen und elektrischen Eigenschaften.
-
Prozesskontrolle und Programmierung:
- Der SPS-Prozess wird über eine Touchscreen-Schnittstelle gesteuert und programmiert.
- Dies erleichtert die präzise Steuerung der Sinterparameter und gewährleistet die Reproduzierbarkeit des Prozesses.
Wenn man diese Schlüsselpunkte versteht, kann ein Käufer von Anlagen oder Verbrauchsmaterialien die einzigartigen Möglichkeiten der SPS und ihr Potenzial zur Herstellung von Hochleistungswerkstoffen mit maßgeschneiderten Eigenschaften schätzen.
Zusammenfassende Tabelle:
Hauptaspekt | Einzelheiten |
---|---|
Prozess-Übersicht | Kombiniert gepulsten elektrischen Strom und uniaxialen Druck zum Sintern. |
Wichtige Phasen | 1.Vakuumerzeugung 2.Druckanwendung 3.Widerstandsheizung 4.Kühlung. |
Einzigartige Merkmale | Hohe Heizraten, präzise Steuerung, niedrige Sintertemperaturen. |
Vorteile | Kurze Verarbeitungszeiten, einzigartige Materialeigenschaften, kontrollierte Atmosphäre. |
Anwendungen | Hochleistungskeramik, Metalle, Verbundwerkstoffe, funktional abgestufte Materialien. |
Prozesskontrolle | Touchscreen-Schnittstelle für präzise Programmierung und Reproduzierbarkeit. |
Möchten Sie erfahren, wie Spark Plasma Sintering Ihre Materialherstellung revolutionieren kann? Kontaktieren Sie uns noch heute für fachkundige Beratung!